What is Teflon PCB?
Teflon PCB, also known as PTFE (polytetrafluoroethylene) PCB, is a type of printed circuit board that uses Teflon as the base material instead of the more commonly used FR-4. Teflon is a synthetic fluoropolymer known for its excellent dielectric properties, high heat resistance, and low friction coefficient. When used in PCB manufacturing, Teflon imparts these properties to the circuit board, making it suitable for high-frequency and high-temperature applications.
Key Properties of Teflon PCB
- High dielectric constant and low dissipation factor
- Excellent thermal stability and heat resistance
- Low moisture absorption
- High chemical resistance
- Low coefficient of friction
Advantages of Teflon PCB
Superior Dielectric Properties
One of the primary advantages of Teflon PCB is its exceptional dielectric properties. Teflon has a dielectric constant of 2.1, which is significantly lower than that of FR-4 (4.5). This low dielectric constant minimizes signal loss and allows for faster signal transmission, making Teflon PCBs ideal for high-frequency applications such as radar, satellite communication, and RF systems.
High Heat Resistance
Teflon PCBs can withstand temperatures up to 260°C (500°F) without deteriorating or losing their mechanical and electrical properties. This high heat resistance makes them suitable for applications that involve extreme temperatures, such as aerospace, military, and industrial equipment.
Low Moisture Absorption
Teflon has a very low moisture absorption rate (less than 0.01%), which helps maintain the PCB’s dimensional stability and prevents warping or delamination. This property is particularly important in humid environments or applications where moisture can cause issues with the circuit board’s performance.
Excellent Chemical Resistance
Teflon PCBs are highly resistant to most chemicals, including acids, bases, and solvents. This chemical resistance makes them suitable for use in harsh industrial environments or in applications where the PCB may be exposed to corrosive substances.
Teflon PCB Manufacturing Process
The manufacturing process for Teflon PCBs is similar to that of standard FR-4 PCBs, with a few key differences:
-
Material Selection: Teflon laminates are used instead of FR-4. The most common Teflon laminates are PTFE-based, such as Rogers RT/duroid and Taconic TLY.
-
Drilling: Due to Teflon’s softness, special drill bits and lower feed rates are used to prevent tearing or deformation of the material.
-
Plating: Electroless copper plating is used to metallize the drilled holes, followed by electroplating to build up the required copper thickness.
-
Etching: Standard photolithography and etching processes are used to create the circuit patterns on the Teflon PCB.
-
Solder Mask and Silkscreen: Teflon-compatible solder mask and silkscreen inks are applied to protect the circuitry and provide component designations.
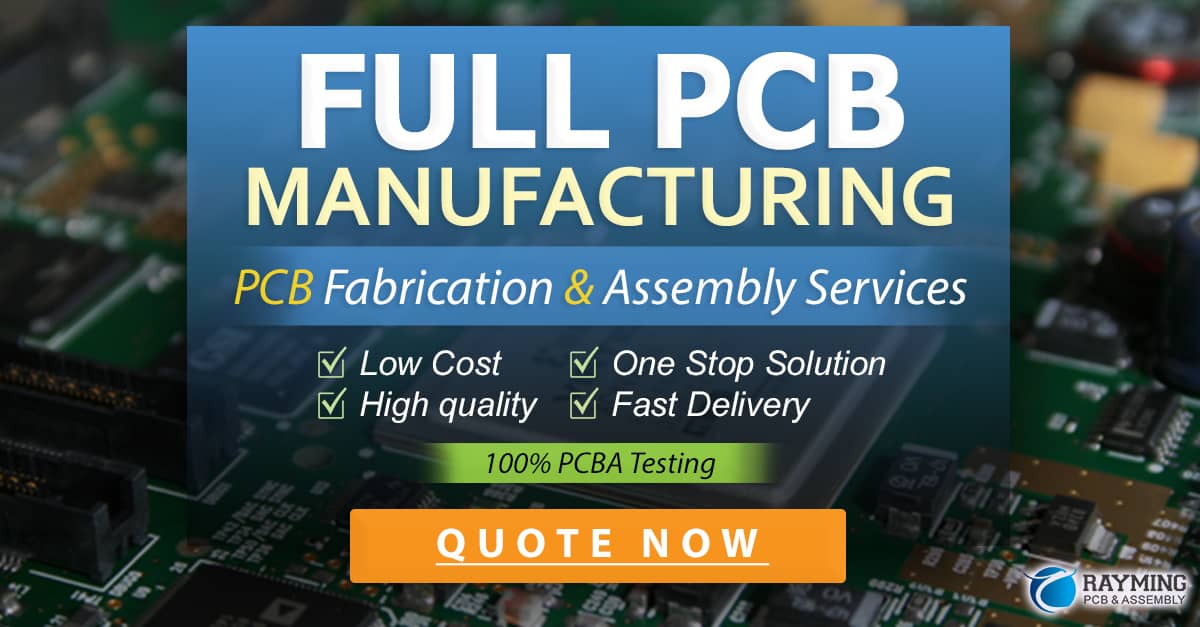
Applications of Teflon PCB
Teflon PCBs find applications in various industries where high-frequency performance, heat resistance, and chemical stability are critical:
- Aerospace and Defense
- Radar systems
- Satellite communication
-
Avionics
-
Telecommunications
- 5G networks
- Microwave devices
-
RF power amplifiers
-
Industrial
- Oil and gas exploration
- Chemical processing
-
High-temperature sensors
-
Medical
- MRI machines
- High-frequency surgical equipment
- Implantable devices
Comparison of Teflon PCB with Other PCB Materials
Property | Teflon PCB | FR-4 PCB | Ceramic PCB |
---|---|---|---|
Dielectric Constant | 2.1 | 4.5 | 9.5 |
Dissipation Factor | 0.0002 | 0.02 | 0.001 |
Thermal Conductivity | 0.25 W/mK | 0.3 W/mK | 20-30 W/mK |
Maximum Operating Temp. | 260°C | 130°C | 1000°C |
Moisture Absorption | < 0.01% | 0.1-0.2% | 0% |
Cost | High | Low | High |
Challenges in Teflon PCB Design and Manufacturing
Design Considerations
- Teflon’s softness and flexibility can make it challenging to maintain tight tolerances during the manufacturing process.
- The low surface energy of Teflon can make it difficult to achieve strong adhesion between the copper traces and the Teflon substrate.
- Teflon’s high thermal expansion coefficient must be considered when designing the PCB layout to avoid stress on components and connections.
Manufacturing Challenges
- Special equipment and processes are required to handle Teflon’s unique properties during drilling, plating, and etching.
- Teflon’s low surface energy can make it difficult to apply solder mask and silkscreen inks evenly.
- The higher cost of Teflon laminates compared to FR-4 can make Teflon PCBs more expensive to manufacture.
FAQ
-
Q: Are Teflon PCBs suitable for all applications?
A: No, Teflon PCBs are primarily used in high-frequency, high-temperature, and chemically harsh environments. For most standard applications, FR-4 PCBs are sufficient and more cost-effective. -
Q: Can Teflon PCBs be assembled using standard soldering techniques?
A: Yes, Teflon PCBs can be assembled using standard soldering techniques, such as reflow soldering and wave soldering. However, the solder mask and pad finishes must be compatible with Teflon. -
Q: How does the cost of Teflon PCBs compare to other PCB materials?
A: Teflon PCBs are generally more expensive than FR-4 PCBs due to the higher cost of Teflon laminates and the specialized manufacturing processes required. However, they are often comparable in price to other high-performance PCB materials, such as ceramic or polyimide. -
Q: Can Teflon PCBs be manufactured with multiple layers?
A: Yes, Teflon PCBs can be manufactured with multiple layers, just like FR-4 PCBs. However, the layer count is typically limited to 8-12 layers due to the challenges in bonding Teflon laminates. -
Q: Are there any environmental concerns associated with Teflon PCBs?
A: Teflon itself is a stable and inert material that does not pose significant environmental concerns. However, the manufacturing process for Teflon PCBs may involve the use of chemicals that require proper handling and disposal to minimize environmental impact.
Conclusion
Teflon PCBs offer unique properties that make them ideal for high-frequency, high-temperature, and chemically demanding applications. Their superior dielectric properties, thermal stability, and chemical resistance set them apart from standard FR-4 PCBs. However, designing and manufacturing Teflon PCBs comes with its own set of challenges, and they are generally more expensive than FR-4 PCBs.
When considering Teflon PCBs for your application, it’s essential to weigh the benefits against the costs and challenges. In many cases, the enhanced performance and reliability offered by Teflon PCBs can justify the additional investment, particularly in mission-critical applications where failure is not an option.
As technology continues to advance, the demand for high-performance PCBs like Teflon is expected to grow. By understanding the properties, advantages, and applications of Teflon PCBs, engineers and designers can make informed decisions when selecting the best material for their projects.
0 Comments