Introduction to PCB Milling
PCB milling is a process of creating custom printed circuit boards (PCBs) using a computer-controlled milling machine. This method allows for rapid prototyping and small-scale production of PCBs without the need for expensive and time-consuming traditional PCB fabrication methods. In this article, we will guide you through the step-by-step process of creating your own PCB milling boards.
Advantages of PCB Milling
- Quick turnaround time for prototyping
- Cost-effective for small-scale production
- Allows for customization and flexibility in design
- Suitable for both single-sided and double-sided PCBs
Equipment and Materials Required
To get started with PCB milling, you will need the following equipment and materials:
- A computer-controlled milling machine (e.g., CNC mill)
- PCB design software (e.g., Eagle, KiCad, or Altium)
- Copper-clad PCB material (either single-sided or double-sided)
- Milling bits (usually carbide or diamond-coated)
- Drill bits for through-hole components
- Safety equipment (safety glasses, dust mask, and ear protection)
Step 1: Designing Your PCB
Choosing PCB Design Software
The first step in creating a PCB milling board is to design your circuit using PCB design software. There are several popular options available, such as:
- Eagle (https://www.autodesk.com/products/eagle/overview)
- KiCad (https://www.kicad.org/)
- Altium Designer (https://www.altium.com/altium-designer/)
Choose the software that best suits your needs and level of expertise.
Creating Your PCB Design
- Create a new project in your chosen PCB design software.
- Design your schematic diagram, including all the necessary components and connections.
- Convert the schematic into a PCB layout.
- Place and route the components on the PCB, ensuring that the traces are of appropriate width and spacing.
- Add any necessary text, labels, or logos to your PCB design.
- Generate the Gerber files, which will be used to control the milling machine.
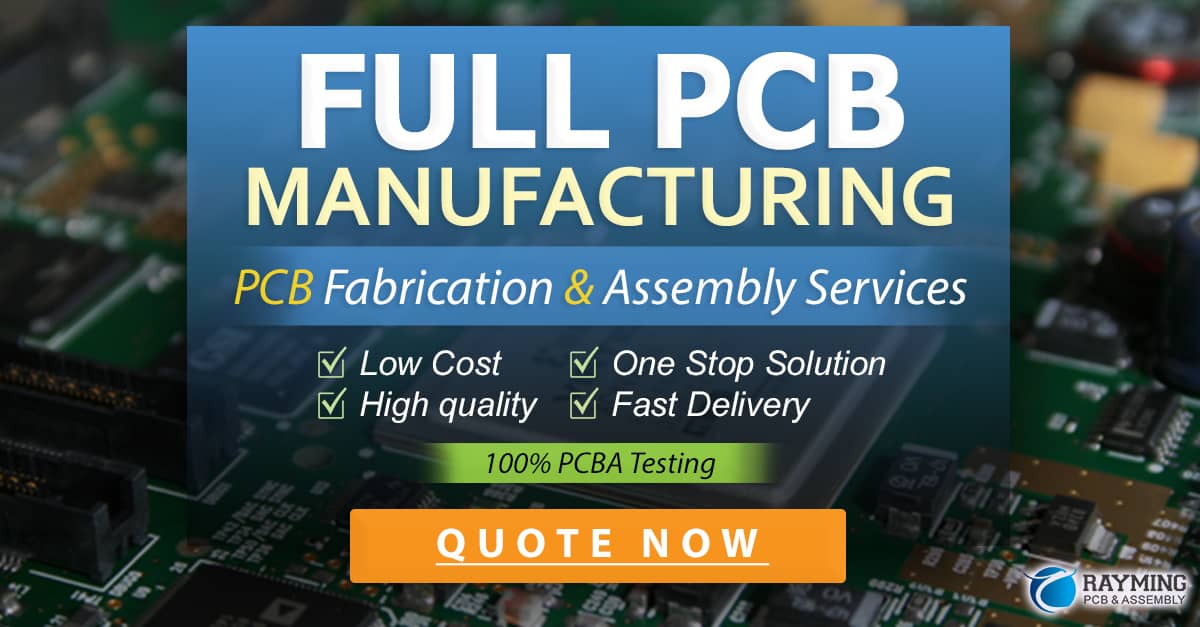
Step 2: Preparing the Milling Machine
Setting Up the Milling Machine
- Ensure that your milling machine is properly calibrated and the axes are moving smoothly.
- Install the appropriate milling bit for your PCB material and design requirements.
- Secure the copper-clad PCB material to the milling machine bed using double-sided tape or a vacuum table.
- Set the zero position for the X, Y, and Z axes.
Importing Gerber Files
- Transfer the generated Gerber files from your PCB design software to the milling machine’s control software.
- Import the Gerber files into the control software, ensuring that the layers are correctly assigned.
- Set the appropriate milling parameters, such as feed rate, spindle speed, and depth of cut, based on your PCB material and milling bit specifications.
Step 3: Milling the PCB
Milling the Traces
- Begin the milling process by starting the spindle and moving the milling bit to the starting position.
- The milling machine will follow the paths defined by the Gerber files, removing the unwanted copper from the PCB material to create the traces.
- Monitor the milling process closely to ensure that the machine is operating correctly and the traces are being milled accurately.
Drilling Through-Holes
- Once the traces have been milled, switch to the appropriate drill bit for creating through-holes for components.
- The milling machine will drill the holes at the specified locations based on the Gerber files.
- Ensure that the drill bits are sharp and the holes are clean and free of debris.
Step 4: Cleaning and Finishing the PCB
Removing Burrs and Cleaning the PCB
- After milling and drilling, remove the PCB from the milling machine bed.
- Use a small brush or compressed air to remove any burrs or debris from the PCB surface and through-holes.
- Clean the PCB with isopropyl alcohol to remove any remaining dirt or grease.
Applying Solder Mask and Silkscreen (Optional)
- If desired, apply a solder mask to protect the PCB traces and prevent accidental short circuits.
- Apply silkscreen to add text, labels, or logos to the PCB surface.
- Allow the solder mask and silkscreen to dry completely before proceeding.
Step 5: Assembling and Testing the PCB
Soldering Components
- Place the components on the PCB, ensuring that they are correctly oriented and seated in the through-holes or on the pads.
- Solder the components to the PCB using a soldering iron and solder wire.
- Inspect the solder joints to ensure that they are clean, shiny, and free of any bridges or cold joints.
Testing and Troubleshooting
- Connect the assembled PCB to a power source and test its functionality using appropriate test equipment (e.g., multimeter or oscilloscope).
- If any issues are detected, troubleshoot the PCB by checking for incorrect component placement, solder bridges, or damaged traces.
- Make any necessary repairs or adjustments to ensure that the PCB functions as intended.
Frequently Asked Questions (FAQ)
-
What is the difference between PCB milling and traditional PCB fabrication methods?
PCB milling is a rapid prototyping and small-scale production method that uses a computer-controlled milling machine to remove unwanted copper from a PCB material. Traditional PCB fabrication methods, such as etching, involve using chemicals to remove the unwanted copper. PCB milling is faster and more cost-effective for small quantities, while traditional methods are better suited for large-scale production. -
Can I create double-sided PCBs using a milling machine?
Yes, you can create double-sided PCBs using a milling machine. However, you will need to design your PCB layout accordingly and ensure that your milling machine is capable of handling double-sided PCB material. You will also need to accurately align the two sides of the PCB when milling and drilling. -
What is the minimum trace width and spacing that can be achieved with PCB milling?
The minimum trace width and spacing achievable with PCB milling depends on the capabilities of your milling machine and the size of the milling bit. Generally, trace widths and spacing of around 0.2 mm (8 mil) can be achieved with a high-quality milling machine and a small-diameter milling bit. However, for more complex designs or finer traces, you may need to use traditional PCB fabrication methods. -
How do I choose the appropriate milling bit for my PCB material and design?
When selecting a milling bit, consider the following factors: - PCB material: Use carbide or diamond-coated bits for harder materials like FR-4, and use high-speed steel (HSS) bits for softer materials like PTFE.
- Trace width and spacing: Use smaller-diameter bits for finer traces and larger-diameter bits for wider traces.
-
Milling depth: Ensure that the bit is long enough to cut through the copper layer without damaging the PCB substrate.
-
Can I reuse the same PCB material for multiple milling jobs?
It is not recommended to reuse PCB material for multiple milling jobs, as the milling process removes a significant amount of copper from the surface. Reusing the material may result in inconsistent trace thickness and potentially damage the PCB substrate. It is best to use a new piece of PCB material for each milling job to ensure the best possible results.
Conclusion
PCB milling is an excellent method for creating custom PCBs quickly and cost-effectively, particularly for prototyping and small-scale production. By following the step-by-step guide provided in this article, you can design, mill, and assemble your own PCB milling boards with confidence. Remember to prioritize safety, use the appropriate equipment and materials, and take your time to ensure the best possible results. With practice and experience, you will be able to create increasingly complex and sophisticated PCB designs using the milling process.
0 Comments