Introduction to Flex PCB Soldering
Flexible printed circuit boards (Flex PCBs) have gained significant popularity in recent years due to their versatility and ability to fit in compact, complex electronic devices. Unlike rigid PCBs, Flex PCBs can bend and twist, making them ideal for applications that require flexibility and durability. However, soldering components onto Flex PCBs requires specialized techniques and considerations to ensure a reliable and robust connection.
In this article, we will explore five common Flex PCB soldering technologies, their advantages, disadvantages, and best practices for achieving optimal results.
1. Hand Soldering
Hand soldering is a manual process that involves using a soldering iron to melt solder and join components to the Flex PCB. This method is often used for low-volume production, prototyping, or rework.
Advantages of Hand Soldering
- Low initial investment
- Flexibility in component placement and soldering
- Suitable for small-scale production and repairs
Disadvantages of Hand Soldering
- Time-consuming and labor-intensive
- Inconsistent results due to human error
- Limited to relatively large components
Best Practices for Hand Soldering Flex PCBs
- Use a temperature-controlled soldering iron with a fine tip
- Apply flux to improve solder flow and prevent oxidation
- Preheat the Flex PCB to minimize thermal stress
- Use the appropriate solder wire gauge and composition
- Maintain a steady hand and avoid excessive pressure on the Flex PCB
2. Reflow Soldering
Reflow soldering is an automated process that involves applying solder paste to the Flex PCB, placing components, and heating the entire assembly in a reflow oven. The solder paste melts and forms a connection between the components and the Flex PCB.
Advantages of Reflow Soldering
- High-speed and efficient for large-scale production
- Consistent and reliable solder joints
- Suitable for small, surface-mount components
Disadvantages of Reflow Soldering
- Higher initial investment in equipment
- Limited flexibility in component placement and soldering
- Requires careful control of reflow oven temperature profile
Best Practices for Reflow Soldering Flex PCBs
- Use a stencil to apply solder paste accurately
- Ensure proper component placement and alignment
- Optimize the reflow oven temperature profile for the specific Flex PCB and components
- Use nitrogen in the reflow oven to reduce oxidation and improve solder joint quality
- Perform post-reflow inspection to identify any defects or issues
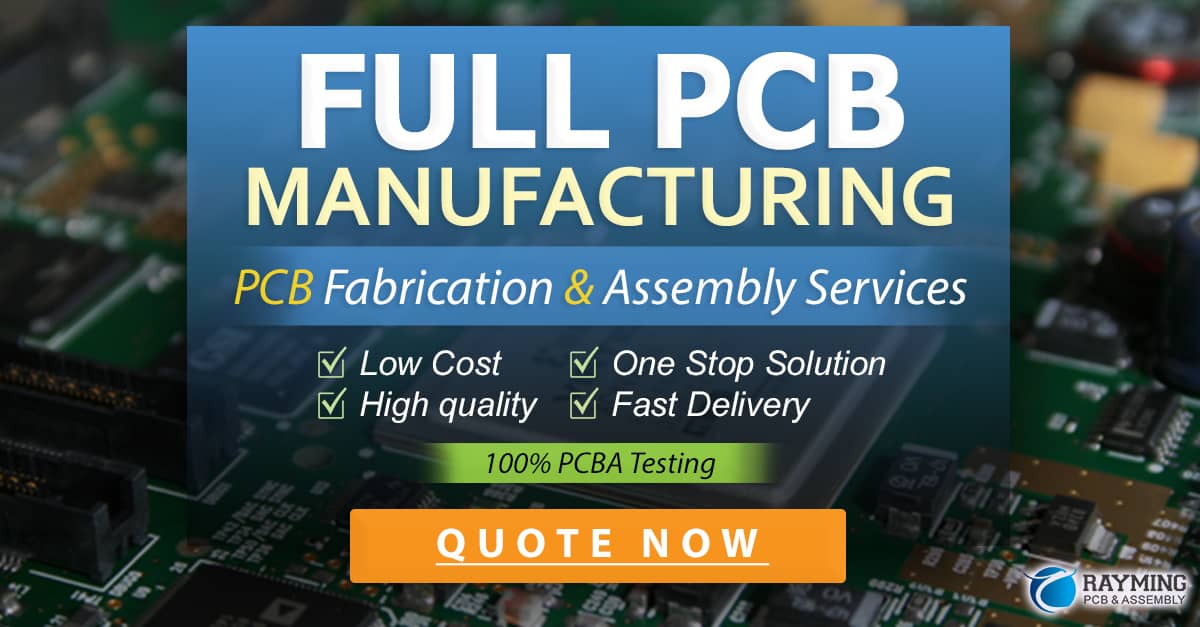
3. Wave Soldering
Wave soldering is an automated process that involves passing the Flex PCB over a molten solder wave, which selectively solders the components to the board. This method is commonly used for through-hole components.
Advantages of Wave Soldering
- High-speed and efficient for large-scale production
- Suitable for through-hole components
- Provides a strong mechanical connection
Disadvantages of Wave Soldering
- Limited flexibility in component placement and soldering
- Requires careful control of solder wave parameters
- May cause thermal stress on the Flex PCB
Best Practices for Wave Soldering Flex PCBs
- Use a pallet or carrier to support the Flex PCB during soldering
- Apply a solder mask to protect the Flex PCB from excessive solder
- Optimize the solder wave parameters (height, speed, and temperature) for the specific Flex PCB and components
- Use a nitrogen atmosphere to reduce oxidation and improve solder joint quality
- Perform post-soldering cleaning to remove flux residue
4. Selective Soldering
Selective soldering is an automated process that combines the advantages of hand soldering and wave soldering. It uses a focused solder nozzle to selectively solder specific components or areas on the Flex PCB.
Advantages of Selective Soldering
- Flexibility in component placement and soldering
- Suitable for both surface-mount and through-hole components
- Reduces thermal stress on the Flex PCB
Disadvantages of Selective Soldering
- Higher initial investment in equipment
- Slower than wave soldering for high-volume production
- Requires programming for each specific component and location
Best Practices for Selective Soldering Flex PCBs
- Use a fixtureto secure the Flex PCB during soldering
- Optimize the solder nozzle parameters (size, shape, and temperature) for the specific components
- Apply flux to improve solder flow and prevent oxidation
- Use nitrogen to reduce oxidation and improve solder joint quality
- Perform post-soldering inspection to identify any defects or issues
5. Laser Soldering
Laser soldering is an advanced process that uses a focused laser beam to heat and melt solder, joining components to the Flex PCB. This method offers high precision and minimal thermal stress.
Advantages of Laser Soldering
- High precision and accuracy
- Minimal thermal stress on the Flex PCB
- Suitable for small, delicate components
Disadvantages of Laser Soldering
- High initial investment in equipment
- Slower than other automated soldering methods
- Requires specialized training and expertise
Best Practices for Laser Soldering Flex PCBs
- Use a laser with the appropriate wavelength and power for the specific solder and components
- Optimize the laser parameters (spot size, pulse duration, and power) for the specific application
- Use a coaxial nozzle to deliver solder wire or paste to the soldering site
- Implement a vision system for precise component alignment and process monitoring
- Perform post-soldering inspection to identify any defects or issues
Comparison of Flex PCB Soldering Technologies
Soldering Technology | Suitable for | Advantages | Disadvantages |
---|---|---|---|
Hand Soldering | Low-volume production, prototyping, rework | Low initial investment, flexibility | Time-consuming, inconsistent results |
Reflow Soldering | Large-scale production, surface-mount components | High-speed, consistent results | Higher initial investment, limited flexibility |
Wave Soldering | Large-scale production, through-hole components | High-speed, strong mechanical connection | Limited flexibility, thermal stress on Flex PCB |
Selective Soldering | Surface-mount and through-hole components | Flexibility, reduced thermal stress | Higher initial investment, slower than wave soldering |
Laser Soldering | Small, delicate components | High precision, minimal thermal stress | High initial investment, slower than other automated methods |
FAQ
-
Q: What is the most suitable soldering technology for prototyping Flex PCBs?
A: Hand soldering is the most suitable soldering technology for prototyping Flex PCBs, as it offers flexibility in component placement and soldering and requires a low initial investment. -
Q: Which soldering technology is best for large-scale production of Flex PCBs with surface-mount components?
A: Reflow soldering is the best soldering technology for large-scale production of Flex PCBs with surface-mount components, as it provides high-speed, consistent, and reliable solder joints. -
Q: How can I minimize thermal stress on Flex PCBs during soldering?
A: To minimize thermal stress on Flex PCBs during soldering, you can use selective soldering or laser soldering, which offer more focused heat application. Additionally, preheating the Flex PCB and using nitrogen atmosphere can help reduce thermal stress. -
Q: What are the advantages of using nitrogen atmosphere in soldering processes?
A: Using nitrogen atmosphere in soldering processes helps reduce oxidation and improve solder joint quality by preventing the formation of oxides on the solder surface. -
Q: How important is post-soldering inspection for Flex PCBs?
A: Post-soldering inspection is crucial for Flex PCBs, as it helps identify any defects or issues that may affect the reliability and performance of the electronic device. Regular inspection and quality control measures ensure the production of high-quality Flex PCBs.
Conclusion
Flex PCB soldering technology has advanced significantly in recent years, offering a range of options for manufacturers to choose from based on their specific requirements. From hand soldering for prototyping and small-scale production to automated methods like reflow soldering and laser soldering for large-scale production, each technology has its own advantages and disadvantages. By understanding the best practices and considerations for each soldering method, manufacturers can optimize their processes and ensure the production of reliable, high-quality Flex PCBs.
As the demand for flexible and compact electronic devices continues to grow, the importance of selecting the appropriate Flex PCB soldering technology cannot be overstated. By staying up-to-date with the latest advancements and techniques in Flex PCB soldering, manufacturers can remain competitive and meet the ever-evolving needs of the electronics industry.
0 Comments