Understanding the Characteristics of Flex PCBs
Before diving into the soldering process, it’s essential to understand the unique characteristics of flex PCBs that set them apart from rigid PCBs. Flex PCBs are made from thin, flexible substrates such as polyimide or polyester, which allow them to bend and twist without breaking. However, this flexibility also makes them more susceptible to damage during handling and soldering.
Property | Rigid PCB | Flex PCB |
---|---|---|
Substrate Material | FR-4, Ceramic, Aluminum | Polyimide, Polyester |
Thickness | 0.8mm – 3.2mm | 0.05mm – 0.3mm |
Flexibility | Rigid | Flexible |
Thermal Expansion | Low | High |
Durability | High | Moderate |
As shown in the table above, flex PCBs have a much thinner substrate compared to rigid PCBs, which contributes to their flexibility but also makes them more delicate. Additionally, the thermal expansion of flex PCBs is higher than that of rigid PCBs, which can lead to stress on the solder joints during temperature changes.
Choosing the Right Solder and Flux
When soldering SMDs onto flex PCBs, selecting the appropriate solder and flux is crucial for achieving a strong and reliable connection. Lead-free solder alloys, such as Sn96.5Ag3.0Cu0.5 (SAC305), are commonly used due to their excellent mechanical strength and resistance to fatigue. However, these alloys typically require higher soldering temperatures compared to leaded solders, which can be challenging when working with heat-sensitive flex PCBs.
To mitigate the risk of thermal damage, using a low-temperature solder alloy, such as Sn42Bi58 or Sn42Bi57Ag1, can be beneficial. These alloys have melting points around 140°C, which is significantly lower than the 217°C melting point of SAC305. However, it’s important to note that low-temperature solders may have reduced mechanical strength and may not be suitable for all applications.
Solder Alloy | Melting Point (°C) | Tensile Strength (MPa) | Elongation (%) |
---|---|---|---|
Sn96.5Ag3.0Cu0.5 (SAC305) | 217 | 45 | 35 |
Sn42Bi58 | 138 | 55 | 50 |
Sn42Bi57Ag1 | 140 | 63 | 44 |
In addition to selecting the right solder alloy, using a compatible flux is essential for promoting wetting and preventing oxidation during the soldering process. For flex PCBs, a no-clean, low-residue flux is recommended to minimize the risk of contamination and to facilitate cleaning after soldering.
Controlling the Soldering Temperature and Time
Controlling the soldering temperature and time is critical when working with flex PCBs to prevent thermal damage and ensure proper solder joint formation. As mentioned earlier, flex PCBs are more susceptible to heat damage due to their thin substrate and high thermal expansion. Overexposure to high temperatures can cause delamination, warping, or even burning of the flexible substrate.
To minimize the risk of thermal damage, it’s essential to use a soldering iron with precise temperature control and a fine tip to focus the heat on the solder joint. A soldering iron temperature between 300°C and 350°C is generally recommended for lead-free solders, while a lower temperature range of 250°C to 300°C is suitable for low-temperature solders.
In addition to controlling the soldering iron temperature, it’s crucial to limit the soldering time to prevent excessive heat buildup. A soldering time of 2 to 5 seconds is typically sufficient for SMD components on flex PCBs. Prolonged exposure to heat can cause the flexible substrate to deform or the solder joint to become brittle.
Component Size | Soldering Temperature (°C) | Soldering Time (s) |
---|---|---|
0201 | 300 – 350 | 2 – 3 |
0402 | 300 – 350 | 3 – 4 |
0603 | 300 – 350 | 3 – 5 |
0805 | 300 – 350 | 4 – 5 |
1206 | 300 – 350 | 4 – 5 |
The table above provides general guidelines for soldering temperatures and times based on common SMD component sizes. However, it’s essential to consult the manufacturer’s recommendations and adapt the soldering parameters according to the specific components and flex PCB material being used.
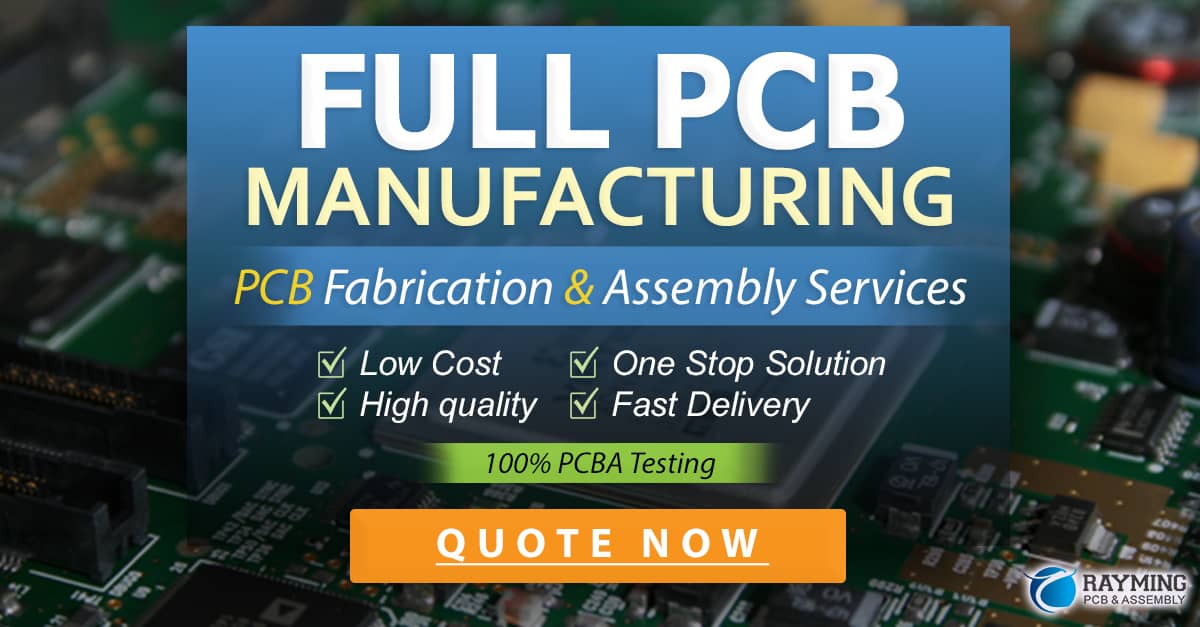
Proper Handling and Support of Flex PCBs
Proper handling and support of flex PCBs during the soldering process are essential to prevent damage and ensure consistent results. Unlike rigid PCBs, flex PCBs can easily bend and deform under pressure, which can lead to misalignment or poor solder joint formation.
To maintain the stability of the flex PCB during soldering, it’s recommended to use a fixture or a support plate that matches the contour of the board. This support helps to distribute the pressure evenly and prevents the PCB from flexing excessively. A rigid backing material, such as aluminum or FR-4, can be used to provide additional support and heat dissipation.
When handling flex PCBs, it’s crucial to avoid excessive bending or creasing, as this can cause damage to the copper traces and the substrate. Use tweezers or vacuum pickup tools to handle the components and the PCB, and avoid touching the surface of the board with bare hands to prevent contamination.
Handling Tip | Benefit |
---|---|
Use a support plate or fixture | Prevents excessive flexing and maintains stability |
Use a rigid backing material | Provides additional support and heat dissipation |
Handle components and PCB with tweezers or vacuum pickup tools | Minimizes the risk of damage and contamination |
Avoid excessive bending or creasing | Prevents damage to copper traces and substrate |
By following these handling and support guidelines, you can minimize the risk of damage to the flex PCB during the soldering process and ensure consistent and reliable solder joint formation.
Inspection and Quality Control
After soldering SMD components onto a flex PCB, it’s essential to perform thorough inspection and quality control to ensure the reliability and functionality of the assembly. Visual inspection is the first step in identifying any soldering defects or issues, such as bridging, insufficient solder, or poor wetting.
A microscope or a high-resolution camera can be used to examine the solder joints closely and check for any irregularities. Common solder joint defects to look out for include:
- Bridging: Solder connecting adjacent pads or components
- Insufficient solder: Solder joint lacking the necessary amount of solder for a reliable connection
- Poor wetting: Solder not adhering properly to the pad or component lead
- Tombstoning: One end of a component lifting off the pad due to uneven heating or poor pad design
In addition to visual inspection, electrical testing should be performed to verify the functionality of the assembly. This can include continuity testing, resistance measurements, and functional testing of the circuit.
Inspection Method | Purpose |
---|---|
Visual Inspection | Identify soldering defects and issues |
Microscope or High-Resolution Camera | Examine solder joints closely for irregularities |
Electrical Testing | Verify the functionality of the assembly |
Continuity Testing | Check for proper connections between components |
Resistance Measurements | Ensure solder joints have the expected resistance |
Functional Testing | Confirm the circuit performs as intended |
By implementing thorough inspection and quality control measures, you can identify and address any soldering issues early in the process, ensuring the reliability and performance of the flex PCB Assembly.
Frequently Asked Questions (FAQ)
- What is the main difference between soldering SMDs on flex PCBs compared to rigid PCBs?
-
The main difference is that flex PCBs are more sensitive to heat and require lower soldering temperatures and shorter soldering times to prevent thermal damage. Additionally, flex PCBs require proper support and handling to maintain their stability during the soldering process.
-
Can I use the same soldering iron for flex PCBs as I do for rigid PCBs?
-
While you can use the same soldering iron, it’s essential to ensure that it has precise temperature control and a fine tip to focus the heat on the solder joint. A lower temperature range may be necessary when working with flex PCBs to minimize the risk of thermal damage.
-
Is it necessary to use low-temperature solder alloys for flex PCBs?
-
Using low-temperature solder alloys is not always necessary, but it can be beneficial when working with heat-sensitive flex PCBs. Low-temperature solders have lower melting points, which reduces the risk of thermal damage. However, they may have reduced mechanical strength compared to standard lead-free solders.
-
How can I prevent my flex PCB from bending or deforming during the soldering process?
-
To prevent bending or deforming, use a fixture or support plate that matches the contour of the flex PCB. This helps to distribute pressure evenly and maintains the stability of the board. Additionally, using a rigid backing material, such as aluminum or FR-4, can provide extra support and heat dissipation.
-
What should I do if I notice soldering defects during the inspection process?
- If soldering defects are identified during inspection, the first step is to determine the cause of the defect. This may involve reviewing the soldering process, checking the solder and flux materials, or examining the PCB design. Once the cause is identified, appropriate corrective actions should be taken, such as adjusting the soldering parameters, replacing materials, or modifying the PCB design. Rework may be necessary to repair or replace the affected solder joints.
In conclusion, soldering SMD components onto flex PCBs requires careful attention to several key factors, including understanding the characteristics of flex PCBs, choosing the right solder and flux, controlling the soldering temperature and time, proper handling and support, and thorough inspection and quality control. By considering these factors and following best practices, you can achieve reliable and durable solder joints on flex PCBs, ensuring the performance and longevity of your electronic devices.
0 Comments