Introduction to PCB Stack-up
Printed Circuit Boards (PCBs) are the backbone of modern electronics. They provide a platform for mounting and interconnecting electronic components, enabling the creation of complex electronic systems. One crucial aspect of PCB design is the stack-up, which refers to the arrangement of conductive layers and insulating materials that make up the PCB. In this article, we will dive into the details of a standard 4-layer PCB stack-up, exploring its design, fabrication process, and the associated manufacturing costs.
What is a 4-Layer PCB Stack-up?
A 4-layer PCB stack-up consists of four conductive layers separated by insulating materials. The four layers are typically arranged as follows:
- Top Layer (Layer 1): This is the uppermost conductive layer where components are mounted and signals are routed.
- Ground Layer (Layer 2): This layer serves as a reference plane for the top layer, providing a low-impedance return path for signals.
- Power Layer (Layer 3): This layer is used to distribute power to the components on the PCB.
- Bottom Layer (Layer 4): This is the lowermost conductive layer, often used for additional signal routing and component placement.
Between each conductive layer, there are insulating materials, typically made of FR-4 (Flame Retardant 4), which is a composite material composed of woven fiberglass cloth with an epoxy resin binder.
Advantages of a 4-Layer PCB Stack-up
Using a 4-layer PCB stack-up offers several advantages over simpler 2-layer designs:
- Improved Signal Integrity: The dedicated ground and power layers help reduce electromagnetic interference (EMI) and crosstalk between signals, resulting in better signal integrity.
- Increased Routing Density: With four layers available for routing, designers have more flexibility in component placement and signal routing, allowing for denser and more complex designs.
- Enhanced Power Distribution: The dedicated power layer ensures a stable and uniform power distribution to all components on the PCB.
- Better Thermal Management: The additional layers help dissipate heat more efficiently, reducing thermal stress on components.
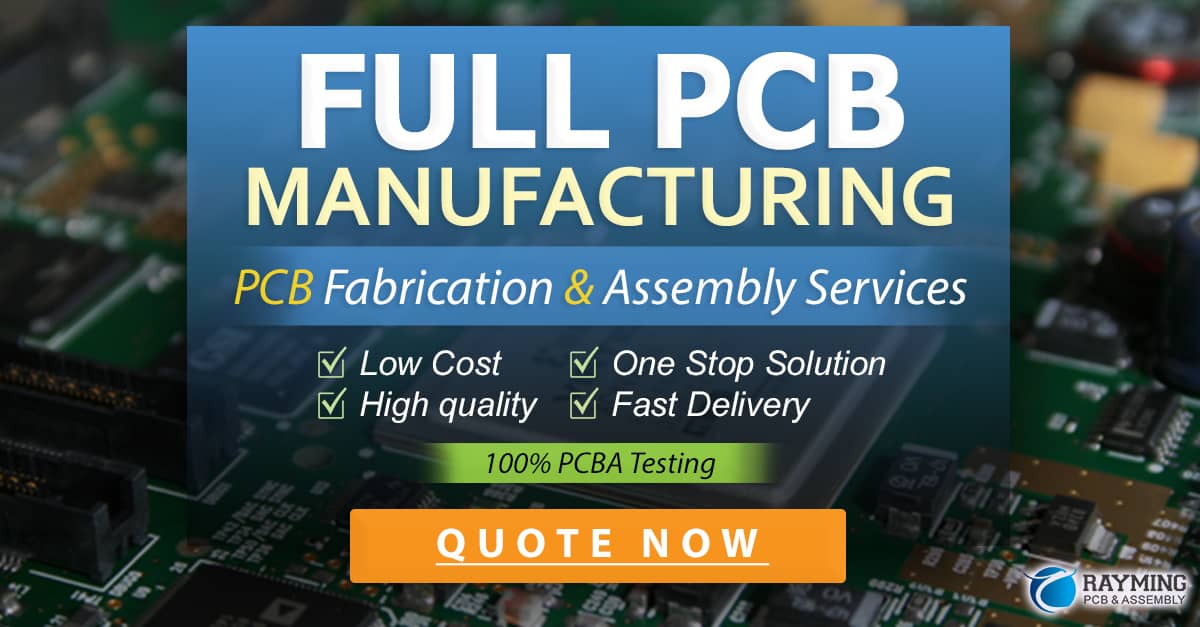
Designing a 4-Layer PCB Stack-up
Designing a 4-layer PCB stack-up involves several key considerations:
1. Layer Thickness
The thickness of each layer in the stack-up is an important factor in determining the PCB’s overall thickness and its electrical and mechanical properties. A typical 4-layer PCB stack-up might have the following layer thicknesses:
Layer | Thickness (mm) |
---|---|
Top Layer (Layer 1) | 0.036 |
Ground Layer (Layer 2) | 0.035 |
Power Layer (Layer 3) | 0.035 |
Bottom Layer (Layer 4) | 0.036 |
The thickness of the insulating materials between layers is typically around 0.2 mm to 0.3 mm.
2. Material Selection
Choosing the right materials for the PCB stack-up is crucial for ensuring the desired electrical and mechanical properties. The most common material used for the insulating layers is FR-4, which offers good dielectric properties, mechanical strength, and thermal stability. For high-frequency or high-speed applications, specialized materials like Rogers or Isola may be used to achieve better performance.
3. Trace Width and Spacing
The width and spacing of the traces on each layer must be carefully designed to ensure proper signal integrity and manufacturability. The trace width is determined by the required current carrying capacity and the desired impedance, while the spacing between traces is governed by the PCB fabrication capabilities and the need to minimize crosstalk.
4. Via Design
Vias are conductive pathways that connect different layers of the PCB. In a 4-layer PCB stack-up, vias are used to route signals between layers and to connect components to the power and ground planes. The size and placement of vias must be carefully considered to ensure reliable connections and to minimize their impact on signal integrity.
Fabrication of a 4-Layer PCB
The fabrication process for a 4-layer PCB involves several steps:
-
Inner Layer Fabrication: The inner layers (layers 2 and 3) are fabricated first. The copper foil is laminated onto the insulating material, and then the desired patterns are etched using photolithography and chemical etching processes.
-
Lamination: The inner layers are then sandwiched between the top and bottom layers, with insulating material (prepreg) placed between each layer. This stack-up is then subjected to high pressure and temperature in a lamination press, bonding the layers together.
-
Drilling: After lamination, holes are drilled through the PCB to accommodate through-hole components and vias.
-
Plating: The drilled holes are then plated with copper to create conductive pathways between layers.
-
Outer Layer Fabrication: The outer layers (layers 1 and 4) are fabricated using a similar process to the inner layers, with the desired patterns etched onto the copper foil.
-
Solder Mask Application: A solder mask is applied to the outer layers to protect the copper traces from oxidation and to prevent solder bridges during the assembly process.
-
Silkscreen Printing: Finally, a silkscreen layer is printed onto the PCB to add component labels, logos, and other identifying marks.
Cost of Manufacturing a 4-Layer PCB
The cost of manufacturing a 4-layer PCB depends on several factors, including:
- PCB Size: Larger PCBs require more material and processing time, resulting in higher costs.
- Quantity: Higher quantities of PCBs often result in lower per-unit costs due to economies of scale.
- Material Selection: Specialized materials like Rogers or Isola may increase the overall cost compared to standard FR-4.
- Complexity: PCBs with high component density, fine pitch traces, or complex via arrangements may require more advanced fabrication techniques, increasing the cost.
- Turnaround Time: Faster turnaround times often come with a premium cost.
As a rough estimate, a 4-layer PCB with dimensions of 100 mm x 100 mm, manufactured in a quantity of 100 pieces, using standard FR-4 material, and with a lead time of 2-3 weeks, might cost around $10-$20 per board. However, this is just a ballpark figure, and actual costs can vary significantly based on the specific requirements of the project.
FAQ
-
Q: Can I use different thicknesses for the layers in a 4-layer PCB stack-up?
A: Yes, it is possible to use different thicknesses for each layer, depending on the specific requirements of the design. However, it is essential to consider the impact on the overall PCB thickness and the compatibility with the chosen fabrication process. -
Q: What are the limitations of a 4-layer PCB compared to designs with more layers?
A: While a 4-layer PCB offers significant advantages over 2-layer designs, it may not be sufficient for very complex or high-speed designs. In such cases, PCBs with 6, 8, or even more layers may be necessary to accommodate the required routing density and to ensure proper signal integrity. -
Q: Can I mix different materials in a 4-layer PCB stack-up?
A: Yes, it is possible to use different materials for different layers in a 4-layer PCB stack-up. For example, you might use standard FR-4 for the inner layers and a high-frequency material like Rogers for the outer layers in a high-speed design. However, mixing materials can increase the complexity and cost of the fabrication process. -
Q: What are the typical lead times for manufacturing a 4-layer PCB?
A: Lead times for 4-layer PCBs can vary depending on the manufacturer and the specific requirements of the project. Typical lead times range from 1-2 weeks for standard designs to 3-4 weeks for more complex or specialized requirements. Expedited manufacturing options may be available at an additional cost. -
Q: How can I reduce the cost of manufacturing a 4-layer PCB?
A: There are several ways to potentially reduce the cost of manufacturing a 4-layer PCB: - Optimize the PCB size to minimize material usage
- Use standard materials like FR-4 instead of specialized high-frequency materials
- Increase the order quantity to take advantage of economies of scale
- Choose a longer lead time to avoid expedited manufacturing fees
- Work with the manufacturer to identify design optimizations that can reduce complexity and cost
By carefully considering these factors and working closely with the PCB manufacturer, it is possible to design and fabricate high-quality 4-layer PCBs while managing costs effectively.
Conclusion
The standard 4-layer PCB stack-up is a versatile and widely-used configuration that offers a balance of performance, manufacturability, and cost. By understanding the design considerations, fabrication process, and cost factors associated with 4-layer PCBs, engineers and designers can make informed decisions when developing their electronic products.
While a 4-layer PCB may not be suitable for every application, it provides a solid foundation for many common electronic designs. As with any engineering project, careful planning, attention to detail, and close collaboration with manufacturing partners are essential for achieving the best possible results.
0 Comments