What is Solder Mask and Why Does Color Matter?
Solder mask, also known as solder resist or solder stop mask, is a thin lacquer-like layer of polymer applied to the copper traces of a printed circuit board (PCB). Its primary purpose is to prevent solder bridges from forming between closely spaced solder pads during assembly. Solder mask also provides protection against oxidation and contamination of the copper traces, improving the durability and longevity of the PCB.
While the functional aspects of solder mask remain the same regardless of color, the choice of solder mask color can have a significant impact on the aesthetics, usability, and even the performance of a PCB. Different colors offer varying levels of contrast, visibility, and heat absorption, which can influence the manufacturing process and the end-user experience.
Common Solder Mask Colors
Color | Pantone Code | RGB Code | Hex Code |
---|---|---|---|
Green | 356 C | 0, 111, 70 | #006F46 |
Blue | 2935 C | 0, 87, 184 | #0057B8 |
Red | 185 C | 228, 0, 43 | #E4002B |
Yellow | 123 C | 255, 199, 44 | #FFC72C |
Black | Black C | 0, 0, 0 | #000000 |
White | White | 255, 255, 255 | #FFFFFF |
Factors to Consider When Choosing Solder Mask Color
Contrast and Visibility
One of the primary considerations when selecting a solder mask color is the contrast it provides against the PCB’s silkscreen labels and component markings. High contrast makes it easier for technicians to read and identify components during assembly and debugging, reducing the likelihood of errors and improving overall efficiency.
Best Solder Mask Colors for Contrast
- Black: Offers the highest contrast against white silkscreen labels and markings.
- Blue: Provides good contrast against white silkscreen while being easier on the eyes than black.
- Red: Offers high contrast against white silkscreen but may cause eye strain during extended use.
Heat Absorption and Thermal Management
Different colors absorb and reflect light and heat differently, which can impact the thermal management of a PCB. In applications where heat dissipation is crucial, such as high-power electronics or devices operating in warm environments, choosing a solder mask color that minimizes heat absorption can help maintain optimal performance.
Solder Mask Colors and Heat Absorption
Color | Heat Absorption |
---|---|
Black | High |
Blue | Medium |
Red | Medium-High |
Yellow | Low-Medium |
Green | Low-Medium |
White | Low |
Aesthetics and Branding
In consumer electronics and other products where visual appeal is important, the choice of solder mask color can play a significant role in the overall aesthetics and branding of the device. Many companies opt for custom solder mask colors that match their brand identity or complement the product’s enclosure.
Popular Custom Solder Mask Colors
- Pantone Colors: Many PCB Manufacturers offer custom solder mask colors based on the Pantone Matching System (PMS), allowing for a wide range of color options.
- Metallic Finishes: Some manufacturers provide metallic solder mask options, such as gold or silver, for a premium look and feel.
- Clear/Translucent: Clear or translucent solder masks can showcase the intricate copper traces of a PCB, creating a unique aesthetic for certain applications.
Cost and Availability
The cost and availability of different solder mask colors can vary depending on the PCB manufacturer and the specific color chosen. Standard colors like green, blue, red, and black are generally more readily available and cost-effective, while custom colors and specialized finishes may incur additional costs and longer lead times.
Typical Cost and Availability of Solder Mask Colors
Color | Cost | Availability |
---|---|---|
Standard | Low | High |
Custom | Medium | Medium |
Metallic | High | Low |
Clear | Medium | Medium-Low |
Selecting the Right Solder Mask Color for Your Application
Industrial and Automotive Electronics
For industrial and automotive electronics, reliability and durability are paramount. In these applications, choose solder mask colors that provide good contrast for easy assembly and debugging while considering the thermal management requirements of the environment.
Recommended colors:
– Blue
– Black
– Green
Consumer Electronics and IoT Devices
In consumer electronics and IoT devices, aesthetics and branding often play a significant role in the choice of solder mask color. Opt for colors that complement the product’s enclosure and align with the brand identity while ensuring adequate contrast for assembly and maintenance.
Recommended colors:
– Custom Pantone colors
– Black
– White
Medical Devices and Equipment
Medical devices and equipment require high levels of reliability, cleanliness, and visibility. Choose solder mask colors that provide excellent contrast against silkscreen markings and minimize the visibility of any potential contaminants.
Recommended colors:
– Blue
– Green
– White
Aerospace and Defense Applications
Aerospace and defense applications demand the utmost reliability and durability in harsh environments. Select solder mask colors that offer good contrast, thermal management, and resistance to environmental factors such as UV radiation and extreme temperatures.
Recommended colors:
– Black
– Green
– Red
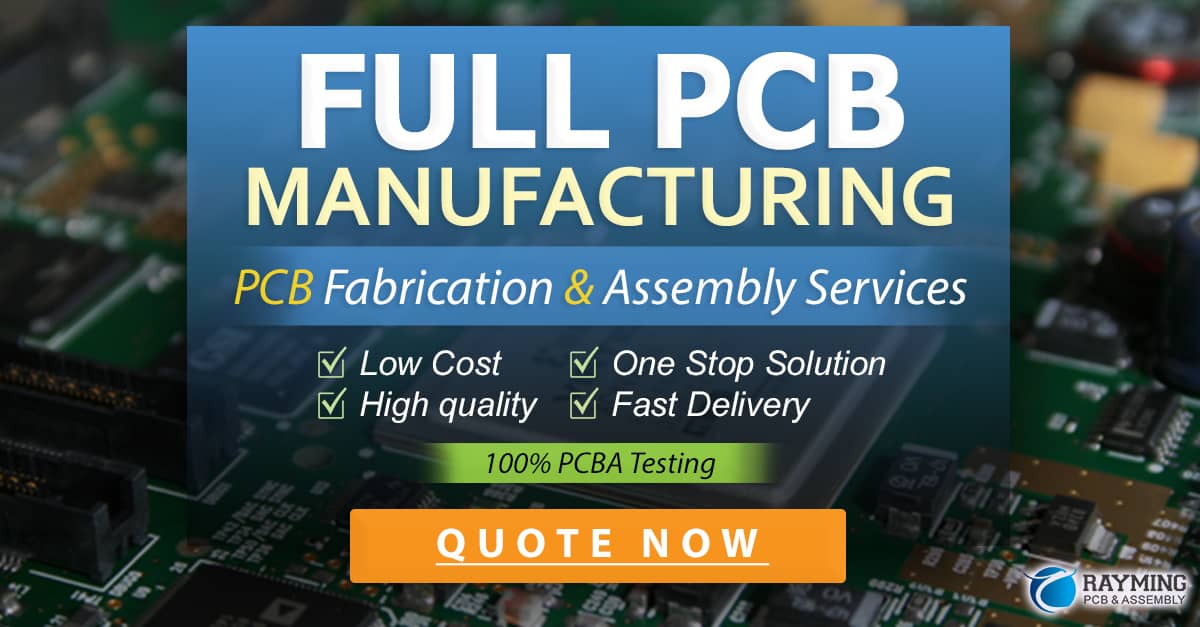
FAQ
1. What is the most common solder mask color?
Green is the most common solder mask color, as it provides a good balance of contrast, heat absorption, and cost-effectiveness. Green has become the default choice for many PCB manufacturers and is widely used across various industries.
2. Can I mix different solder mask colors on the same PCB?
While it is technically possible to use different solder mask colors on the same PCB, it is generally not recommended. Using multiple colors can increase the complexity and cost of the manufacturing process and may lead to issues with color consistency and alignment.
3. How does solder mask color affect PCB performance?
Solder mask color can indirectly affect PCB performance through its impact on thermal management. Darker colors like black and red absorb more heat, which may be beneficial in applications where heat dissipation is crucial. Lighter colors, such as white and yellow, reflect more heat and may be preferred in environments where minimizing heat absorption is important.
4. Are there any industry standards for solder mask colors?
There are no strict industry standards for solder mask colors, as the choice often depends on the specific application, aesthetics, and performance requirements. However, IPC (Association Connecting Electronics Industries) provides guidelines for solder mask materials and application processes in its IPC-SM-840 and IPC-A-600 standards.
5. How long does it typically take to obtain custom solder mask colors?
The lead time for custom solder mask colors can vary depending on the PCB manufacturer and the specific color requested. Custom colors may require additional setup time and material procurement, which can extend the overall manufacturing timeline. It is best to consult with your PCB manufacturer for specific lead times, as they can range from a few days to several weeks.
Conclusion
Choosing the right solder mask color for your PCB project involves considering various factors, including contrast, visibility, thermal management, aesthetics, branding, cost, and availability. By understanding the properties and implications of different solder mask colors, you can make an informed decision that balances the functional and visual requirements of your application.
When in doubt, consult with your PCB manufacturer for guidance and recommendations based on your specific needs. They can provide valuable insights into the available color options, custom color matching, and any potential impact on the manufacturing process and timeline.
Ultimately, the right solder mask color will contribute to the overall success of your PCB Assembly, ensuring that your device performs reliably, looks great, and meets the expectations of your end-users.
0 Comments