What is a Single-Sided PCB?
A Single-Sided PCB, also known as a one-sided PCB or single-layer PCB, is a printed circuit board that has conductive copper traces on only one side of the board. The other side of the board is typically left bare or covered with a solder mask for protection. Single-sided PCBs are the simplest and most cost-effective type of PCB, making them a popular choice for many electronic projects.
Advantages of Single-Sided PCBs
- Cost-effective: Single-sided PCBs are the least expensive type of PCB to manufacture due to their simple design and fewer materials required.
- Easy to design: With only one conductive layer, single-sided PCBs are easier to design compared to multi-layer PCBs.
- Quick turnaround: The manufacturing process for single-sided PCBs is faster, allowing for shorter lead times and quicker project completion.
- Suitable for simple circuits: Single-sided PCBs are ideal for simple electronic circuits with fewer components and connections.
Disadvantages of Single-Sided PCBs
- Limited routing options: With only one conductive layer, single-sided PCBs have limited space for routing traces, which can make designing complex circuits challenging.
- Larger board size: To accommodate all the necessary components and traces, single-sided PCBs may require a larger board size compared to multi-layer PCBs.
- Lower power handling: Single-sided PCBs have a limited ability to dissipate heat, which can restrict their power handling capabilities.
- Electromagnetic interference: Single-sided PCBs are more susceptible to electromagnetic interference (EMI) due to the exposed traces on the board’s surface.
How to Design a Single-Sided PCB
Step 1: Create a Schematic
The first step in designing a single-sided PCB is to create a schematic of your electronic circuit. A schematic is a visual representation of the components and their connections. Use electronic design automation (EDA) software to create your schematic, ensuring that all components and connections are accurately represented.
Step 2: Convert Schematic to PCB Layout
Once your schematic is complete, convert it into a PCB layout using your EDA software. The PCB layout shows the physical arrangement of components and traces on the board. When designing a single-sided PCB, keep in mind the following considerations:
- Component placement: Arrange components in a logical manner, minimizing the distance between connected components to reduce the length of traces.
- Trace width: Ensure that traces are wide enough to handle the required current and minimize resistance.
- Clearance: Maintain appropriate clearance between traces and components to avoid short circuits and interference.
- Drilling holes: Include drilling holes for through-hole components and mounting the PCB.
Step 3: Add Silkscreen and Solder Mask
Add silkscreen and solder mask layers to your PCB design. The silkscreen layer contains text and symbols that help identify components and their orientation. The solder mask layer protects the PCB from oxidation and prevents solder bridges during the soldering process.
Step 4: Generate Gerber Files
Once your PCB layout is complete, generate Gerber files, which are the industry-standard format for PCB manufacturing. Gerber files contain all the necessary information for the PCB manufacturer to fabricate your board, including the copper traces, solder mask, silkscreen, and drilling data.
How to Manufacture a Single-Sided PCB
Step 1: Choose a PCB Manufacturer
Select a reputable PCB manufacturer that specializes in producing single-sided PCBs. Consider factors such as cost, lead time, quality, and customer support when making your choice.
Step 2: Submit Gerber Files
Submit your Gerber files to the chosen PCB manufacturer. Most manufacturers accept Gerber files via their website or email. Ensure that you provide all the necessary files and specify any special requirements, such as material type, thickness, or surface finish.
Step 3: PCB Fabrication
The PCB manufacturer will fabricate your single-sided PCB using the following process:
- Copper cladding: A thin layer of copper is laminated onto the base material, typically FR-4.
- Photoresist application: A photoresist layer is applied to the copper surface.
- Exposure and development: The photoresist is exposed to UV light through a photomask containing your PCB layout. The exposed areas are then removed during the development process.
- Etching: The exposed copper is etched away using a chemical solution, leaving only the desired traces.
- Solder mask application: A solder mask layer is applied to protect the PCB and prevent solder bridges.
- Silkscreen printing: The silkscreen layer is printed onto the PCB for component identification and orientation.
- Drilling: Holes are drilled for through-hole components and mounting.
- Surface finish: A surface finish, such as HASL or ENIG, is applied to protect the exposed copper and improve solderability.
Step 4: PCB Assembly
Once your single-sided PCB is fabricated, you can proceed with the assembly process. This involves soldering components onto the board according to your schematic and PCB layout. You can choose to assemble the PCB yourself or outsource the assembly to a professional PCB assembly service.
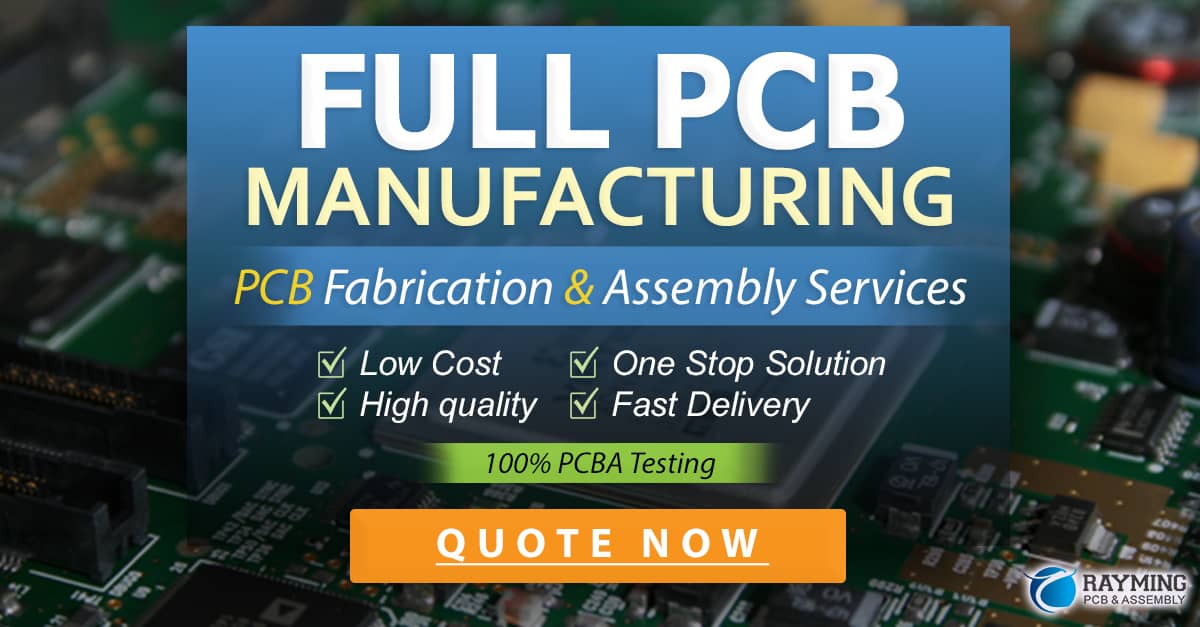
Cost-Saving Tips for Single-Sided PCBs
- Optimize your PCB design: Minimize the board size and number of components to reduce material costs.
- Choose a standard board thickness: Stick to standard board thicknesses, such as 1.6mm, to avoid additional costs associated with custom thicknesses.
- Select a cost-effective surface finish: HASL (Hot Air Solder Leveling) is a cost-effective surface finish compared to more expensive options like ENIG (Electroless Nickel Immersion Gold).
- Order in bulk: Many PCB Manufacturers offer discounts for larger order quantities. Consider ordering more boards than you need to take advantage of these savings.
- Opt for a longer lead time: Choosing a longer lead time can often result in lower costs, as the manufacturer has more flexibility in scheduling your order.
Cost-Saving Tip | Description |
---|---|
Optimize PCB design | Minimize board size and number of components to reduce material costs |
Standard board thickness | Choose standard thicknesses (e.g., 1.6mm) to avoid custom thickness costs |
Cost-effective finish | Select a cost-effective surface finish, such as HASL, over more expensive options like ENIG |
Order in bulk | Many PCB manufacturers offer discounts for larger order quantities, so consider ordering more boards |
Longer lead time | Opting for a longer lead time can often result in lower costs due to manufacturer scheduling flexibility |
Frequently Asked Questions (FAQ)
1. What is the minimum trace width for a single-sided PCB?
The minimum trace width for a single-sided PCB depends on the PCB manufacturer’s capabilities and the required current carrying capacity. Generally, a minimum trace width of 0.2mm (8mil) is achievable for most manufacturers. However, it’s always best to consult with your chosen manufacturer for their specific guidelines.
2. Can single-sided PCBs be used for high-frequency applications?
Single-sided PCBs are not ideal for high-frequency applications due to their limited ability to control impedance and increased susceptibility to electromagnetic interference (EMI). For high-frequency applications, it’s recommended to use multi-layer PCBs with proper grounding and shielding techniques.
3. What is the maximum number of components that can be placed on a single-sided PCB?
The maximum number of components that can be placed on a single-sided PCB depends on several factors, including the board size, component sizes, and routing complexity. There is no strict limit, but as the number of components increases, it becomes more challenging to route traces efficiently on a single layer. In general, single-sided PCBs are best suited for designs with fewer than 50 components.
4. Can single-sided PCBs be used for surface-mount components?
Yes, single-sided PCBs can be used for surface-mount components. However, the placement of surface-mount components on a single-sided PCB requires careful planning to ensure that all the necessary connections can be made without crossing traces. In some cases, it may be necessary to use jumper wires to make connections that cannot be routed on the single layer.
5. Are single-sided PCBs suitable for prototyping?
Single-sided PCBs are an excellent choice for prototyping due to their low cost and quick turnaround times. They allow designers to test and validate their designs before investing in more complex and expensive multi-layer PCBs. However, it’s important to keep in mind the limitations of single-sided PCBs, such as limited routing options and potential EMI issues, when deciding if they are suitable for your specific prototype.
Conclusion
Single-sided PCBs offer a cost-effective and efficient solution for simple electronic projects. By understanding the advantages, disadvantages, and design considerations of single-sided PCBs, you can make informed decisions when planning your next project. Following the steps outlined in this guide, from designing your PCB to manufacturing and assembly, will help ensure the success of your single-sided PCB project while saving costs along the way.
0 Comments