What is RoHS?
RoHS stands for “Restriction of Hazardous Substances”. It is a directive that originated in the European Union and restricts the use of specific hazardous materials found in electrical and electronic products (EEE). The directive came into force on 1 July 2006 and is required to be enforced and became a law in each member state.
The original RoHS, often referred to as RoHS 1, restricted the use of six hazardous materials:
- Lead (Pb)
- Mercury (Hg)
- Cadmium (Cd)
- Hexavalent chromium (Cr6+)
- Polybrominated biphenyls (PBB)
- Polybrominated diphenyl ether (PBDE)
RoHS 2, an evolution of the original directive, went into effect in July 2011. It deals with the same six hazardous substances as RoHS 1 and requires periodic re-evaluations that facilitate gradual broadening of its requirements to cover additional electronic and electrical equipment, cables, and spare parts.
Any EEE products put on the market in the EU must meet RoHS compliance. Non-compliant products are not allowed on the market.
Purpose of RoHS
The purpose of the RoHS directive is to restrict certain dangerous substances commonly used in electronic and electronic equipment. Any RoHS compliant component is tested for the presence of Lead (Pb), Cadmium (Cd), Mercury (Hg), Hexavalent chromium (Hex-Cr), Polybrominated biphenyls (PBB), and Polybrominated diphenyl ethers (PBDE). For Cadmium and Hexavalent chromium, there must be less than 0.01% of the substance by weight at raw homogeneous materials level. For Lead, PBB, and PBDE, there must be no more than 0.1% of the material, when calculated by weight at raw homogeneous materials. Any RoHS compliant component must have 100 ppm or less of mercury and the mercury must not have been intentionally added to the component.[1]
The maximum permitted concentrations in non-exempt products are 0.1% or 1000 ppm (except for cadmium, which is limited to 0.01% or 100 ppm) by weight. The restrictions are on each homogeneous material in the product, which means that the limits do not apply to the weight of the finished product, or even to a component, but to any single substance that could (theoretically) be separated mechanically—for example, the sheath on a cable or the tinning on a component lead.
RoHS Compliance Summary Table
Restricted Substance | Maximum Concentration Limit |
---|---|
Lead (Pb) | 0.1% |
Mercury (Hg) | 0.1% |
Cadmium (Cd) | 0.01% |
Hexavalent Chromium (Cr6+) | 0.1% |
Polybrominated Biphenyls (PBB) | 0.1% |
Polybrominated Diphenyl Ethers (PBDE) | 0.1% |
RoHS Compliance Requirements
To be RoHS compliant, products must meet the material restrictions as stated by the RoHS directive. A company must take several steps to ensure that its products are RoHS compliant:
-
Determine if the product is in scope for RoHS. If it is, identify the specific restricted substances present in the product.
-
Evaluate the supply chain to determine where compliance data will be available and where more work and information may be needed. Compliance data should be collected for each part or material in the product that is procured.
-
Determine the compliance status of the product based on supplier material declarations or engineering analysis. Compliance status may be reported as RoHS compliant, non-compliant (and why), or unknown where data are incomplete.
-
Prepare compliance documentation for customers and regulatory bodies. Compile compliance data into a technical file or other reporting formats.
-
Have a process in place to monitor product compliance status over time as the product, part designs, suppliers, or regulations change.
More details on each of these steps are provided in the sections that follow.
Determining if a Product is in Scope
The first step in ensuring RoHS compliance is determining if the RoHS Directive applies to the product. In general, all electronic and electrical equipment (EEE) is considered in scope for RoHS unless it is specifically excluded.
Some key product categories that are in scope for RoHS include:
- Large and small household appliances
- IT and telecommunications equipment
- Consumer equipment
- Lighting equipment
- Electrical and electronic tools
- Toys, leisure, and sports equipment
- Medical devices
- Monitoring and control instruments
- Automatic dispensers
Some notable exclusions from RoHS are:
- Military and national security equipment
- Equipment designed to be sent into space
- Large-scale stationary industrial tools
- Means of transport (excluding electric two-wheel vehicles)
- Non-road mobile machinery for professional use
- Active implantable medical devices
- Photovoltaic panels
- Equipment specifically designed solely for R&D
If any uncertainty exists about whether a product is in scope, it is best to consult with a regulatory expert or legal counsel for guidance.
Collecting Compliance Data
Once it is determined that a product is subject to RoHS restrictions, the next step is collecting compliance data from the supply chain. This involves requesting material composition data or RoHS compliance declarations from suppliers for any parts or materials procured to manufacture the product.
When requesting data from suppliers, provide them with a list of the restricted substances, their Chemical Abstracts Service (CAS) numbers, and the maximum concentration limits. Many suppliers have this data readily available, but others may need time and support to generate this information.
Some tips for collecting compliance data from suppliers:
- Use industry-standard data formats like IPC-1752 material declarations where possible to make it easier for suppliers to report data in a consistent way
- Be as specific as possible in requests—specify required data formats, units of measure, submission methods, and due dates
- Follow up with suppliers to ensure they understand the request and expectations
- Track supplier responses and follow up with suppliers that are unresponsive or provide incomplete data
- Validate the data received from suppliers—cross-check it against other sources like engineering documentation or test reports
If compliance data cannot be obtained for a supplied part or material, it may be possible to assess its compliance through an engineering analysis based on the part’s composition and manufacturing process. Failing that, the part may need to be treated as non-compliant if its status cannot be definitively determined.
Determining Compliance Status
The compliance status of the product can be determined once material composition data has been collected for all parts and materials. To calculate the worst-case concentration of a restricted substance in the product, use this formula:
Worst-case concentration (ppm) =
Part substance concentration (ppm) * Part weight (g) / Product weight (g) * 1,000,000
Sum the worst-case concentrations for each part to get the total concentration in the overall product. Compare this value to the maximum concentration limit to determine if it exceeds the threshold. If the concentration is below the limit, the product can be considered RoHS compliant (assuming this calculation has been done for all restricted substances).
An example RoHS compliance calculation for lead (Pb) is shown in the table below:
Part | Material | Pb Conc (ppm) | Weight (g) | Worst-case Pb (ppm) |
---|---|---|---|---|
A | Copper alloy | 300 | 25 | 37.5 |
B | Steel | 1000 | 50 | 250 |
C | Plastic | 0 | 40 | 0 |
D | Solder | 800 | 5 | 20 |
Product-level worst-case Pb concentration: 307.5 ppm (compliant)
In this simplified example, although some of the parts/materials contain lead in concentrations exceeding the 1000 ppm limit, when factored into the total mass of the product, the overall worst-case lead concentration is still within the RoHS limit. The product would be deemed RoHS compliant for lead based on this analysis.
Documentation and Reporting
Manufacturers must compile compliance documentation into a technical file or other reporting format to demonstrate the due diligence performed in assessing RoHS compliance. The RoHS Directive does not prescribe a required format for technical documentation, but best practices include:
- Listing the product’s identity (e.g. name, model/part number)
- Providing a technical description and images/diagrams of the product
- Stating the compliance status (e.g. “RoHS Compliant to Directive 2011/65/EU”)
- Listing the assessment methodology used (e.g. material declarations, engineering analysis, testing)
- Including a signed Declaration of Conformity (DoC)
- Making the technical file available to authorities upon request
Examples of supporting documentation to include in the technical file are:
- Bill of Materials (BOM) listing all parts/materials
- Supplier material declarations
- Engineering analysis reports
- Material safety data sheets (MSDS)
- Test reports
- Compliance assurance process documentation
Proper documentation helps demonstrate compliance to customers and regulatory bodies. It also provides a record of compliance efforts in case issues arise in the future.
Ongoing Compliance Assurance
RoHS compliance requires ongoing monitoring and assurance efforts. Product compliance status may change over time due to factors such as:
- Changes in suppliers or outsourced manufacturing locations
- Part design changes or material substitutions
- Regulatory changes (e.g. additional substance restrictions)
- Availability of new compliance data
Manufacturers should have a process in place to assess the impact of such changes on compliance status. This may involve:
- Flagging any engineering change orders (ECOs) that affect BoM for compliance review
- Regularly surveying suppliers about changes in compliance status of provided parts/materials
- Monitoring relevant regulatory developments
- Conducting periodic compliance assessments or testing on higher-risk items
An annual internal audit of the RoHS compliance process is also recommended to ensure procedures are being properly followed and documented. Automating data collection and analysis can help reduce the burden of continuous compliance assurance.
Lead-Free Compliance
While lead is one of the six substances restricted by RoHS, the wider transition to lead-free products has been driven by other factors as well. Lead-free initiatives actually preceded RoHS—the European End-of-Life Vehicles (ELV) Directive mandated the removal of lead from automobiles starting in 2003.
In the electronics industry, the move to lead-free was spurred by several Japanese electronics companies in the late 1990s. They were motivated by environmental and health concerns associated with lead, as well as the business benefits of staying ahead of anticipated regulations.
The transition gained momentum in the early 2000s, with major industry groups advocating for the adoption of Lead-free Solder and components. This culminated in the IPC-1752 materials declaration standard being updated in 2005 to collect lead-free data from suppliers.
Today, the electronics industry has largely transitioned to lead-free solder and finishes, with some notable exceptions for high-reliability applications. The most common lead-free solder alloy is tin-silver-copper (SAC), typically in a 3-4% Ag, 0.5-0.7% Cu composition.
Lead-Free Solder Comparison
Solder Alloy | Composition | Melting Point | Relative Cost |
---|---|---|---|
Tin-lead | Sn63Pb37 | 183°C | $ |
SAC305 | Sn96.5Ag3.0Cu0.5 | 217°C | $$$ |
SAC405 | Sn95.5Ag4.0Cu0.5 | 217°C | $$$$ |
Tin-silver | Sn96.5Ag3.5 | 221°C | $$$ |
*Relative cost scale: $ (lowest) to $$$$ (highest)
As shown in the table above, lead-free solders have higher melting points than traditional tin-lead solder. This has implications for printed circuit board (PCB) assembly, as it requires higher reflow temperatures and updated processes.
Some key considerations for lead-free PCB Assembly are:
- Use of lead-free compatible components (e.g. with lead-free finishes)
- Higher melting point of solder requires tighter process control
- Potential for increased warpage of PCBs due to higher reflow temperatures
- Compatibility of PCB materials and coatings with lead-free processes
- Differences in joint formation, wetting, and reliability compared to tin-lead solder
Despite these challenges, the transition to lead-free electronics has been largely successful. Advances in materials, processes, and equipment have helped enable the shift. However, the use of lead is still permitted in some exempted applications where viable lead-free alternatives do not yet exist.
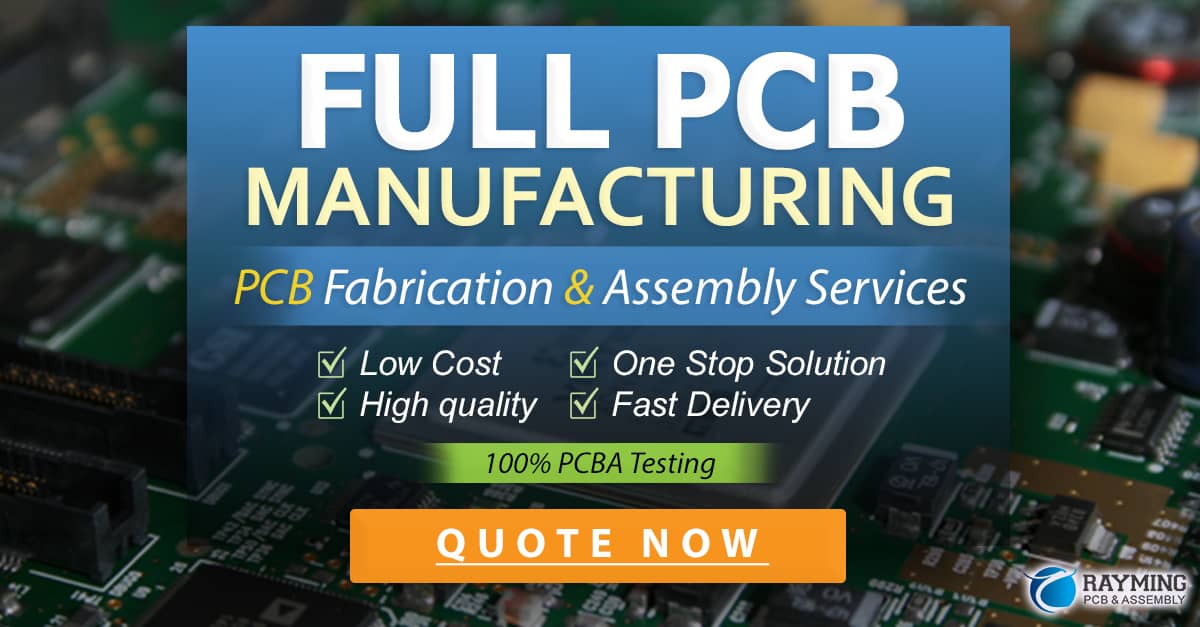
Frequently Asked Questions
What is the difference between RoHS and REACH?
RoHS and REACH are both European Union regulations that restrict the use of certain hazardous substances, but they have some key differences:
- RoHS specifically applies to electrical and electronic equipment, while REACH applies to all chemicals and products.
- RoHS restricts the use of six substances (lead, mercury, cadmium, hexavalent chromium, PBB, and PBDE), while REACH restricts a much larger list of Substances of Very High Concern (SVHCs).
- RoHS sets maximum concentration limits for restricted substances, while REACH requires reporting and authorization for SVHCs above certain thresholds.
So while there is some overlap between the two regulations, they have different scopes and requirements. Products may need to comply with both depending on their composition and intended use.
Are RoHS and lead-free the same thing?
Not exactly. RoHS restricts the use of lead and five other hazardous substances in electrical and electronic products. The transition to lead-free electronics was driven by RoHS and other factors, but it specifically refers to the elimination of lead in solder and component finishes.
So while all RoHS-compliant products are lead-free (at least for the restricted applications), not all lead-free products are necessarily RoHS compliant. They could still contain other RoHS-restricted substances above the allowable limits.
In practice, though, the terms are often used interchangeably since lead was the most common of the substances restricted by RoHS and its elimination was a major focus of compliance efforts.
How do I know if my product is RoHS compliant?
There are a few ways to determine if a product is RoHS compliant:
-
Check the manufacturer’s website or product documentation for a RoHS compliance statement or certification.
-
Look for the CE marking on the product or packaging, which indicates compliance with applicable EU directives including RoHS.
-
Contact the manufacturer directly to request a Declaration of Conformity or other compliance documentation.
-
Have the product tested by an accredited lab to verify its composition and compare it to RoHS substance restrictions.
It’s important to properly document the compliance status and supporting evidence for your own products and those you incorporate from suppliers. Failing to comply with RoHS can result in fines and the inability to sell products in certain markets.
Is RoHS compliance mandatory?
Yes, RoHS compliance is mandatory for all products within its scope that are sold in the European Union. Member states are required to adopt the RoHS Directive into their national laws and enforce its requirements.
Many other countries have also adopted RoHS-like regulations, so even products sold outside the EU may need to comply with similar restrictions. Some common examples are:
- China RoHS
- Korea RoHS
- California RoHS
- UAE RoHS
While the specifics may vary, these regulations generally mirror the EU RoHS Directive in terms of restricted substances and concentration limits. So aiming for EU RoHS compliance can help ensure compliance with other RoHS-like requirements around the world.
How do I stay up to date on RoHS requirements?
The RoHS Directive is periodically reviewed and updated to account for new scientific evidence and technological developments. The most recent update, known as RoHS 3 or Directive (EU) 2015/863, added four new substances to the list of restrictions (DEHP, BBP, DBP, and DIBP) and updated some of the exemptions.
To stay current on RoHS requirements, some strategies include:
- Monitoring the European Commission’s RoHS website for news and updates
- Subscribing to newsletters or alerts from industry associations or compliance service providers
- Attending webinars, conferences, or training sessions on RoHS and other product compliance topics
- Consulting with a regulatory expert or legal counsel for guidance on how changes may impact your products
It’s also important to have a system in place to track and manage compliance data for your products and supply chain. This can help you more easily assess the impact of regulatory changes and update your compliance status as needed.
Staying proactive and informed about RoHS requirements is critical to
0 Comments