Introduction to PCB Assembly and Reflow Soldering
Printed Circuit Board (PCB) assembly is a crucial process in the manufacturing of electronic devices. It involves the placement and soldering of electronic components onto a PCB to create a functional circuit. One of the most common methods used in PCB assembly is reflow soldering.
Reflow soldering is a process where a solder paste, containing tiny solder particles, is applied to the PCB’s pads. The components are then placed on the board, and the entire assembly is heated in a reflow oven. The solder paste melts and forms a strong bond between the components and the PCB pads as it cools down.
Advantages of Reflow Soldering in PCB Assembly
- Efficiency: Reflow soldering allows for the simultaneous soldering of multiple components, making the process faster and more efficient compared to manual soldering.
- Consistency: The automated nature of reflow soldering ensures consistent solder joint quality across the entire PCB.
- Precision: Reflow soldering enables the use of smaller components and finer pitch sizes, resulting in more compact and high-density PCB designs.
- Reliability: The controlled heating and cooling process in reflow soldering minimizes thermal stress on components, leading to more reliable solder joints.
Choosing the Right PCB Assembly Service Provider
When it comes to PCB assembly, selecting the right service provider is crucial for the success of your project. Here are some key factors to consider when choosing a PCB assembly service provider:
1. Experience and Expertise
Look for a service provider with a proven track record in PCB assembly and reflow soldering. They should have experience working with a wide range of PCB designs, components, and materials. Additionally, they should be well-versed in industry standards and best practices to ensure the highest quality of work.
2. Technology and Equipment
A reliable PCB assembly service provider should invest in state-of-the-art technology and equipment. This includes:
- Surface Mount Technology (SMT) assembly lines
- Automated Optical Inspection (AOI) systems
- X-ray inspection machines
- Reflow ovens with precise temperature control
- Electrostatic Discharge (ESD) protection measures
Having access to advanced technology and well-maintained equipment ensures that your PCBs are assembled with the utmost precision and reliability.
3. Quality Control and Testing
Quality control and testing are critical aspects of PCB assembly. Your chosen service provider should have a robust quality management system in place, which may include:
- Incoming material inspection
- In-process quality checks
- Final functional testing
- Burn-in testing
- Environmental stress screening
These measures help identify and rectify any issues early in the assembly process, reducing the risk of defects and failures in the final product.
4. Certifications and Standards Compliance
Ensure that your PCB assembly service provider holds relevant certifications and complies with industry standards. Some common certifications and standards in the PCB assembly industry include:
- ISO 9001 (Quality Management Systems)
- IPC-A-610 (Acceptability of Electronic Assemblies)
- IPC-J-STD-001 (Requirements for Soldered Electrical and Electronic Assemblies)
- RoHS (Restriction of Hazardous Substances)
- REACH (Registration, Evaluation, Authorization, and Restriction of Chemicals)
Compliance with these standards demonstrates the service provider’s commitment to quality, reliability, and environmental responsibility.
5. Flexibility and Scalability
Your PCB assembly service provider should be able to accommodate your specific requirements and adapt to changes in your project. They should offer flexibility in terms of:
- PCB design support
- Component sourcing
- Production volume (prototypes to mass production)
- Lead times
- Customization options
As your business grows and your needs evolve, your service provider should be able to scale their services accordingly, ensuring a long-term partnership.
The Reflow Soldering Process in PCB Assembly
Reflow soldering is a multi-step process that involves careful planning, precise execution, and thorough inspection. Here’s a closer look at the key stages of the reflow soldering process in PCB assembly:
1. Solder Paste Application
The first step in reflow soldering is applying solder paste to the PCB’s pads. Solder paste is a mixture of tiny solder particles suspended in a flux medium. The most common methods for applying solder paste are:
- Stencil printing: A stainless steel or polyimide stencil with apertures corresponding to the PCB pads is placed over the board. Solder paste is then spread across the stencil using a squeegee, depositing the paste onto the pads.
- Jet printing: An inkjet-like printer dispenses solder paste directly onto the PCB pads. This method is suitable for low-volume production or prototypes.
The solder paste application process must be carefully controlled to ensure the correct amount of paste is deposited on each pad. Insufficient or excessive solder paste can lead to defects such as open circuits, shorts, or poor solder joint formation.
2. Component Placement
Once the solder paste is applied, the electronic components are placed onto the PCB. This process is typically performed using automated pick-and-place machines, which use vacuum nozzles or grippers to pick up components from feeders and place them onto the PCB with high precision.
The placement process is guided by computer-aided design (CAD) data, which contains information about the component locations, orientations, and polarities. The pick-and-place machine uses this data to accurately position the components on the solder paste-covered pads.
For smaller batches or prototypes, manual placement using tweezers may be employed. However, this method is more time-consuming and prone to human error compared to automated placement.
3. Reflow Soldering
After the components are placed, the PCB assembly is ready for reflow soldering. The assembly is loaded onto a conveyor belt that passes through a reflow oven. The reflow oven has multiple temperature zones, each with precise temperature control to ensure the solder paste melts and forms reliable solder joints.
A typical reflow soldering temperature profile consists of four stages:
- Preheat: The assembly is gradually heated to activate the flux and remove any moisture from the PCB and components.
- Thermal soak: The temperature is maintained just below the solder paste’s melting point to ensure even heat distribution across the assembly.
- Reflow: The temperature is rapidly increased above the solder paste’s melting point, causing the solder particles to melt and form solder joints between the components and PCB pads.
- Cooling: The assembly is cooled down gradually to allow the solder joints to solidify without causing thermal stress or defects.
The reflow soldering process is critical to the quality and reliability of the final PCB assembly. Improper temperature profiles or inadequate process control can lead to defects such as:
- Tombstoning: When a component stands up on one end due to uneven heating or surface tension imbalance.
- Bridging: When solder inadvertently connects adjacent pads or component leads.
- Insufficient wetting: When the solder fails to adhere properly to the PCB pads or component leads.
- Voids: When air bubbles or gas pockets form within the solder joints, weakening the connection.
4. Inspection and Testing
After the reflow soldering process, the PCB assembly undergoes thorough inspection and testing to ensure its quality and functionality. Common inspection methods include:
- Visual inspection: A trained operator visually examines the solder joints and components for any visible defects or abnormalities.
- Automated Optical Inspection (AOI): An automated system uses high-resolution cameras and image processing algorithms to detect surface-level defects such as missing components, shifted components, or solder bridging.
- X-ray inspection: For defects that are not visible on the surface, such as voids or hidden solder joints, X-ray inspection is used to create a detailed image of the internal structure of the assembly.
In addition to inspection, functional testing is performed to verify that the PCB assembly operates as intended. This may include:
- In-circuit testing (ICT): A bed-of-nails fixture makes contact with specific test points on the PCB, allowing for the testing of individual components and circuits.
- Flying probe testing: Movable probes are used to test various points on the PCB without the need for a dedicated test fixture.
- Boundary scan testing: A built-in test architecture, such as JTAG, is used to test the interconnections and functionality of the components on the PCB.
Thorough inspection and testing help identify any defects or performance issues early in the production process, allowing for necessary rework or corrective actions to be taken before the PCB assembly is shipped to the customer.
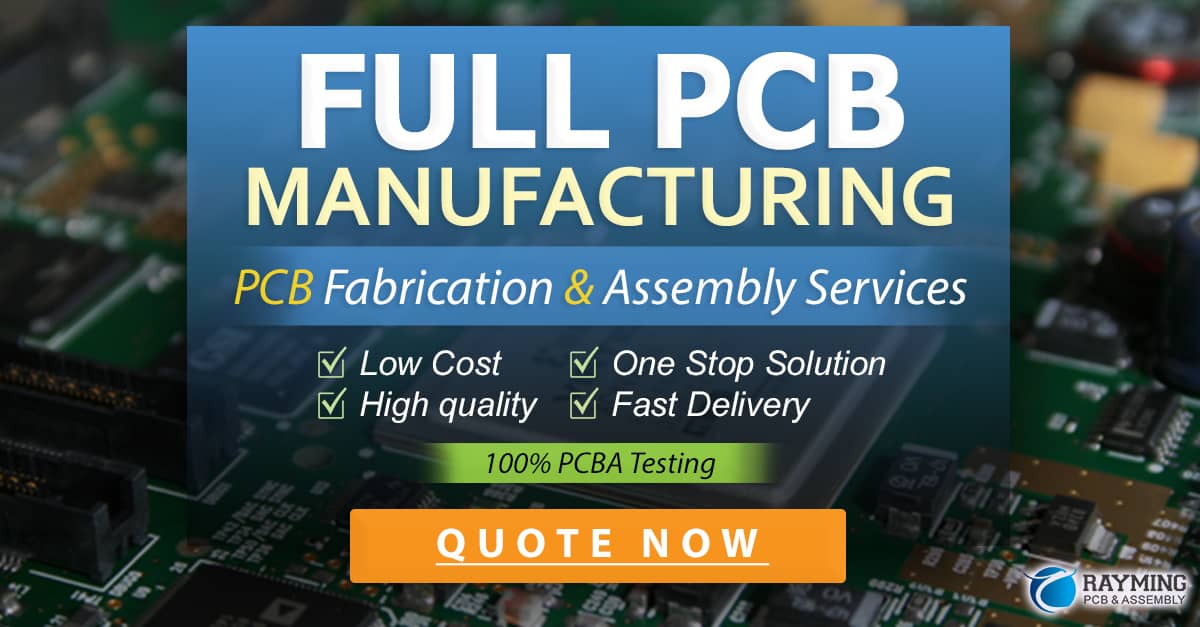
Challenges and Considerations in Reflow Soldering PCB Assembly
While reflow soldering is a highly automated and efficient process, there are several challenges and considerations that PCB assembly service providers must address to ensure the best possible results:
1. Component Compatibility
Not all electronic components are suitable for reflow soldering. Some components, such as certain types of connectors, batteries, or heat-sensitive devices, may require alternative soldering methods or special handling during the assembly process.
PCB assembly service providers must carefully review the bill of materials (BOM) and component datasheets to identify any components that may pose challenges during reflow soldering. They should work closely with their clients to find appropriate solutions, such as using alternative components, modifying the PCB design, or employing selective soldering techniques for specific components.
2. Thermal Profile Optimization
Developing and optimizing the reflow soldering thermal profile is crucial for achieving high-quality solder joints and minimizing the risk of defects. The thermal profile must be tailored to the specific requirements of the PCB design, components, and solder paste used.
Factors that influence the thermal profile include:
- PCB thickness and layer count
- Component thermal mass and heat sensitivity
- Solder paste composition and melting point
- Reflow oven capabilities and conveyor speed
PCB assembly service providers use specialized software and monitoring equipment to develop and fine-tune the thermal profile. They may also conduct trial runs and analyze the results to ensure that the profile meets the desired quality standards.
3. Moisture Sensitivity Management
Many electronic components, particularly those with plastic packages, are susceptible to moisture absorption. If these components are exposed to high temperatures during reflow soldering without proper moisture control, they can suffer from delamination, cracking, or “popcorning” defects.
To mitigate moisture-related issues, PCB assembly service providers must implement moisture sensitivity level (MSL) classification and handling procedures in accordance with industry standards such as IPC/JEDEC J-STD-020. This involves:
- Storing moisture-sensitive components in moisture-barrier bags with desiccants
- Monitoring the exposure time of components to ambient conditions
- Baking components to remove excess moisture before assembly, if necessary
- Ensuring that the reflow soldering process is completed within the allowable exposure time for the given MSL
Proper moisture sensitivity management helps to minimize the risk of moisture-related defects and ensures the long-term reliability of the PCB assembly.
4. Cleanliness and Contamination Control
Cleanliness and contamination control are essential for achieving high-quality reflow soldering results. Contaminants such as dust, dirt, oils, or residues can interfere with the solder paste application, component placement, and solder joint formation, leading to defects and reliability issues.
PCB assembly service providers must maintain a clean and controlled environment throughout the assembly process. This includes:
- Using clean room facilities with air filtration and particle control
- Implementing regular cleaning and maintenance procedures for equipment and tools
- Ensuring that operators follow proper handling and hygiene practices
- Using high-quality, contaminant-free materials and consumables
In addition to general cleanliness, PCB assembly service providers must also control the ioniccontamination levels on the PCB surface. Ionic contamination, such as flux residues or other process chemicals, can lead to corrosion, electromigration, or other long-term reliability issues.
To mitigate ionic contamination, service providers may use no-clean or low-residue solder pastes, implement post-reflow cleaning processes, or conduct ionic contamination testing to ensure that the assembly meets the required cleanliness standards.
Selecting the Right Components for Reflow Soldering PCB Assembly
The success of a reflow soldering PCB assembly project depends not only on the skills and capabilities of the service provider but also on the selection of appropriate components. Here are some key considerations when choosing components for reflow soldering:
1. Package Type and Size
Component package type and size play a significant role in their compatibility with the reflow soldering process. Surface mount device (SMD) packages, such as chip resistors, chip capacitors, and small outline integrated circuits (SOICs), are well-suited for reflow soldering due to their flat, leadless design and small footprint.
However, some package types may pose challenges during reflow soldering. For example:
- Ball Grid Array (BGA) packages have an array of solder balls underneath the component, making it difficult to inspect the solder joints visually.
- Quad Flat Packages (QFPs) have closely spaced leads on all four sides, requiring precise solder paste application and component placement to avoid bridging or open circuits.
- Power packages, such as TO-220 or D-PAK, have a large thermal mass and may require additional heat sinking or special reflow profiles to ensure proper solder joint formation.
When selecting components, it is essential to consider their package type, size, and pitch (the distance between leads or pads) to ensure compatibility with the reflow soldering process and the PCB design.
2. Temperature Ratings and Sensitivity
Electronic components have specific temperature ratings that indicate their maximum allowable exposure to heat during the soldering process. Exceeding these temperature limits can cause damage to the component, such as internal delamination, cracking, or parametric shifts.
When selecting components for reflow soldering, it is crucial to review their datasheets and ensure that their temperature ratings are compatible with the reflow soldering profile. Some components, such as certain electrolytic capacitors or batteries, may be particularly sensitive to high temperatures and require special handling or alternative soldering methods.
PCB assembly service providers should work closely with their clients to select components that can withstand the reflow soldering process without compromising their performance or reliability.
3. Moisture Sensitivity Level (MSL)
As mentioned earlier, moisture sensitivity is a critical consideration for components undergoing reflow soldering. The Moisture Sensitivity Level (MSL) classification, as defined by IPC/JEDEC J-STD-020, indicates a component’s susceptibility to moisture-induced damage during reflow soldering.
Components with higher MSL ratings (e.g., MSL 3 or above) require more stringent moisture control measures, such as dry storage, limited exposure time, and pre-bake procedures. Failure to properly manage moisture-sensitive components can lead to defects such as popcorning, delamination, or cracking during the reflow soldering process.
When selecting components, it is essential to consider their MSL rating and ensure that the PCB assembly service provider has the necessary capabilities and processes in place to handle moisture-sensitive components effectively.
4. Availability and Lead Time
Component availability and lead time are critical factors in the overall success and timely completion of a PCB assembly project. Long lead times or unexpected supply chain disruptions can cause delays in production and increase costs.
When selecting components, it is essential to consider their availability from multiple sources and to review their lead times carefully. PCB assembly service providers should work closely with their clients and component suppliers to ensure that all necessary components are procured in a timely manner and that any potential supply chain risks are identified and mitigated.
In some cases, it may be necessary to consider alternative components or redesign the PCB to accommodate more readily available components. PCB assembly service providers should be proactive in communicating any supply chain concerns to their clients and collaborating to find suitable solutions.
Conclusion
Reflow soldering is a critical process in PCB assembly that enables the efficient, reliable, and high-quality production of electronic devices. By understanding the key considerations and challenges associated with reflow soldering, PCB assembly service providers can optimize their processes, select the right components, and deliver exceptional results to their clients.
When choosing a PCB assembly service provider for your project, it is essential to consider factors such as their experience, technology, quality control measures, certifications, and flexibility. By partnering with a reputable and capable service provider, you can ensure that your PCB assembly project is completed successfully, on time, and to the highest quality standards.
As the electronics industry continues to evolve and demand for high-density, high-performance PCB assemblies grows, reflow soldering will remain a vital technology in the PCB assembly process. By staying informed about the latest advancements and best practices in reflow soldering, PCB assembly service providers and their clients can collaborate effectively to bring innovative and reliable electronic products to market.
Frequently Asked Questions (FAQ)
1. What is the difference between reflow soldering and wave soldering in PCB assembly?
Reflow soldering and wave soldering are two common methods used in PCB assembly, but they differ in their approach and suitability for different types of components.
Reflow soldering is typically used for surface mount devices (SMDs) and involves applying solder paste to the PCB pads, placing the components, and then heating the entire assembly in a reflow oven to melt the solder and form the solder joints.
Wave soldering, on the other hand, is primarily used for through-hole components. In this process, the PCB
0 Comments