Introduction
Printed Circuit Boards (PCBs) are essential components in modern electronic devices, ranging from smartphones and computers to industrial equipment and medical devices. However, the cost of PCB manufacturing and assembly can significantly impact the overall budget of a project. In this article, we will discuss the top 7 tips to help save cost during PCB manufacturing and assembly, focusing on key areas such as design optimization, material selection, and process efficiency.
Tip 1: Optimize Your PCB Design
Minimize Board Size
One of the most effective ways to reduce PCB cost is to minimize the board size. Smaller boards require less material, which translates to lower manufacturing costs. Consider the following strategies to minimize your PCB size:
- Use smaller components, such as chip-scale packages (CSPs) or ball grid arrays (BGAs)
- Optimize component placement to minimize the overall board dimensions
- Utilize multi-layer PCBs to increase component density and reduce board size
Reduce Layer Count
Another way to optimize your PCB design is to reduce the number of layers. Each additional layer increases the manufacturing cost, as it requires more material and processing steps. Consider the following tips to reduce layer count:
- Use fewer power and ground planes
- Combine signal layers when possible
- Utilize blind and buried vias to minimize layer count while maintaining connectivity
Simplify Your Design
A simpler PCB design can lead to lower manufacturing costs. Here are some ways to simplify your design:
- Avoid using complex shapes or curves in your board outline
- Minimize the number of unique components
- Use standard component packages and footprints
- Avoid using non-standard drill sizes or spacings
Tip 2: Choose the Right Materials
Select Cost-Effective Substrates
The choice of substrate material can significantly impact the cost of your PCB. Some common substrate materials include:
Material | Cost | Characteristics |
---|---|---|
FR-4 | Low | Good electrical and mechanical properties, suitable for most applications |
CEM-1 | Low | Similar to FR-4, but with lower quality and lower cost |
Polyimide | High | Excellent thermal and chemical resistance, suitable for high-temperature applications |
PTFE | High | Low dielectric constant and dissipation factor, suitable for high-frequency applications |
When selecting a substrate material, consider the specific requirements of your application and choose the most cost-effective option that meets those requirements.
Optimize Copper Weight
The copper weight, or thickness, of your PCB can also affect the manufacturing cost. Thicker copper layers are more expensive, as they require more material and processing time. Consider the following tips to optimize copper weight:
- Use the minimum copper weight that meets your electrical and thermal requirements
- Consider using different copper weights for different layers, such as thinner copper for signal layers and thicker copper for power and ground planes
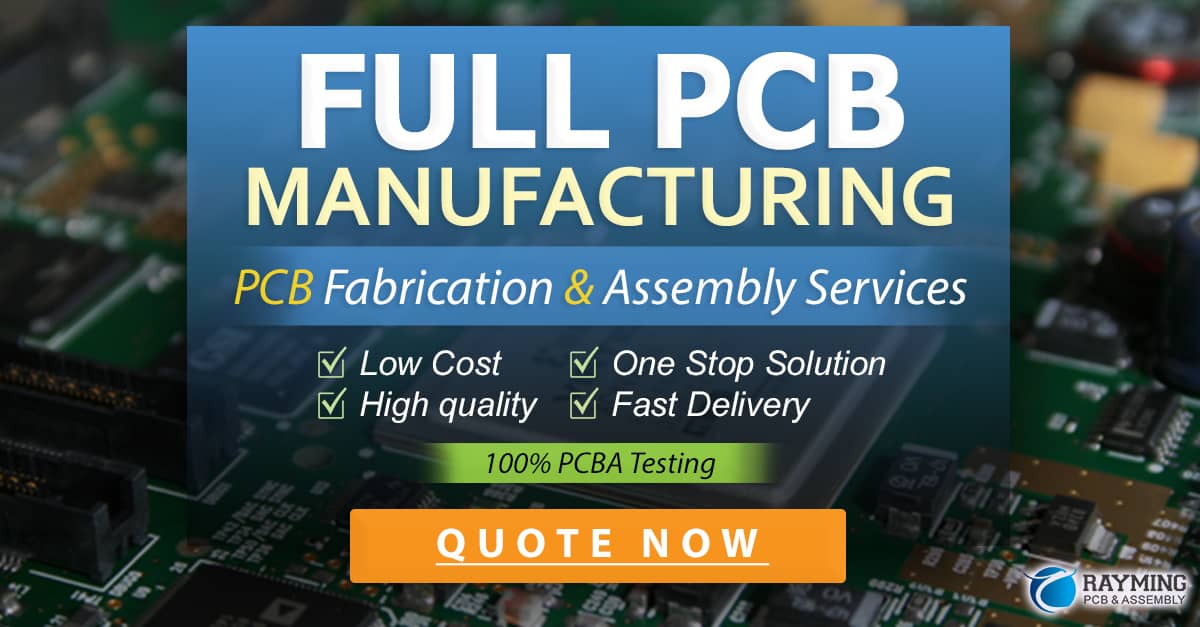
Tip 3: Leverage Standardization
Use Standard Component Packages
Using standard component packages can help reduce the cost of PCB manufacturing and assembly. Standard packages, such as SOICs, QFPs, and TQFPs, are widely available and typically less expensive than custom or non-standard packages. Additionally, standard packages are easier to source and have better availability, which can help avoid supply chain disruptions and delays.
Implement a Common Parts Library
Implementing a common parts library can help streamline your PCB design process and reduce costs. A common parts library is a centralized database of pre-approved components that have been vetted for cost, availability, and performance. By using components from the common parts library, you can:
- Reduce the time and effort required for component selection and approval
- Minimize the risk of using obsolete or hard-to-source components
- Leverage volume pricing discounts by using the same components across multiple designs
Tip 4: Optimize Your Manufacturing Process
Choose the Right PCB Manufacturer
Selecting the right PCB manufacturer is crucial for reducing costs and ensuring quality. When evaluating potential manufacturers, consider the following factors:
- Experience and expertise in manufacturing PCBs similar to your design
- Quality control processes and certifications (e.g., ISO 9001, IPC-A-610)
- Turnaround time and delivery options
- Pricing and volume discounts
- Customer support and communication
Consider Panelization
Panelization is the process of grouping multiple PCBs onto a single panel for manufacturing. By panelizing your PCBs, you can:
- Reduce the overall manufacturing cost per board
- Minimize handling and processing time
- Improve production efficiency and yield
When designing your PCBs for panelization, consider the following factors:
- Panel size and material
- Spacing between individual boards
- Placement of fiducials and tooling holes
- Depaneling method (e.g., routing, scoring, or perforating)
Tip 5: Opt for Surface Mount Technology (SMT)
Surface Mount Technology (SMT) is a method of assembling electronic components directly onto the surface of a PCB. Compared to through-hole technology (THT), SMT offers several advantages that can help reduce costs:
- Smaller component sizes, allowing for higher component density and smaller board sizes
- Faster assembly speeds, as components can be placed and soldered in a single pass
- Lower labor costs, as the process is highly automated
- Improved reliability, as SMT components have shorter leads and are less susceptible to mechanical stress
When designing your PCB for SMT Assembly, consider the following tips:
- Use standard component packages and footprints
- Ensure adequate spacing between components for automated placement
- Follow design guidelines for solder pad sizes and shapes
- Consider using no-clean solder paste to minimize cleaning requirements
Tip 6: Implement Design for Manufacturing (DFM)
Design for Manufacturing (DFM) is a set of principles and guidelines that aim to optimize your PCB design for the manufacturing process. By implementing DFM, you can:
- Reduce manufacturing costs by minimizing the risk of defects and rework
- Improve production efficiency by ensuring your design is compatible with manufacturing processes and equipment
- Enhance product quality and reliability by following best practices for PCB design
Some key DFM guidelines include:
- Adhering to minimum trace width and spacing requirements
- Avoiding acute angles in traces and using curved or 45-degree angles instead
- Ensuring adequate clearance between components and board edges
- Using standard drill sizes and avoiding small or closely spaced holes
- Providing clear and accurate documentation, including assembly drawings and bill of materials (BOM)
Tip 7: Consider Outsourcing
Outsourcing your PCB manufacturing and assembly to a specialized provider can help reduce costs and improve efficiency. By outsourcing, you can:
- Access state-of-the-art equipment and processes without investing in capital equipment
- Leverage the expertise and experience of specialized professionals
- Benefit from volume pricing discounts and economies of scale
- Focus on your core competencies, such as product design and marketing
When selecting an outsourcing partner, consider the following factors:
- Technical capabilities and experience in manufacturing PCBs similar to your design
- Quality control processes and certifications
- Intellectual property (IP) protection and non-disclosure agreements (NDAs)
- Communication and customer support
- Pricing and delivery options
FAQ
1. How can I estimate the cost of my PCB design?
To estimate the cost of your PCB design, consider factors such as board size, layer count, material selection, component types, and quantity. Many PCB Manufacturers offer online quote tools that can provide a rough estimate based on your design specifications. Additionally, you can request quotes from multiple manufacturers to compare pricing and lead times.
2. What are the most common PCB substrate materials?
The most common PCB substrate materials include:
- FR-4: A glass-reinforced epoxy laminate, widely used for general-purpose PCBs
- CEM-1: A composite epoxy material, similar to FR-4 but with lower quality and cost
- Polyimide: A high-temperature, chemically resistant material, used for demanding applications
- PTFE: A low-loss, high-frequency material, used for RF and microwave applications
3. What is the difference between through-hole and surface mount technology?
Through-hole technology (THT) involves mounting components with leads that are inserted into drilled holes in the PCB and soldered on the opposite side. Surface mount technology (SMT) involves mounting components directly onto the surface of the PCB, with solder pads instead of drilled holes. SMT offers smaller component sizes, faster assembly, and lower costs compared to THT.
4. How can I ensure my PCB design is manufacturable?
To ensure your PCB design is manufacturable, follow Design for Manufacturing (DFM) guidelines, such as:
- Adhering to minimum trace width and spacing requirements
- Avoiding acute angles in traces and using curved or 45-degree angles instead
- Ensuring adequate clearance between components and board edges
- Using standard drill sizes and avoiding small or closely spaced holes
- Providing clear and accurate documentation, including assembly drawings and bill of materials (BOM)
Additionally, consult with your PCB manufacturer early in the design process to identify any potential manufacturability issues and ensure your design is compatible with their processes and equipment.
5. What are the benefits of outsourcing PCB manufacturing and assembly?
Outsourcing PCB manufacturing and assembly can offer several benefits, including:
- Access to state-of-the-art equipment and processes without investing in capital equipment
- Leveraging the expertise and experience of specialized professionals
- Benefiting from volume pricing discounts and economies of scale
- Focusing on your core competencies, such as product design and marketing
When selecting an outsourcing partner, consider factors such as technical capabilities, quality control processes, intellectual property protection, communication, and pricing.
Conclusion
Reducing PCB cost is a critical factor in the success of any electronic product development project. By following the top 7 tips outlined in this article, you can optimize your PCB design, select cost-effective materials, leverage standardization, optimize your manufacturing process, implement Design for Manufacturing (DFM) principles, and consider outsourcing to specialized providers.
Remember to focus on key areas such as minimizing board size, reducing layer count, simplifying your design, choosing the right substrate materials, using standard component packages, implementing a common parts library, panelizing your PCBs, opting for surface mount technology (SMT), and adhering to DFM guidelines.
By implementing these cost-saving strategies and working closely with your PCB manufacturer, you can reduce costs, improve efficiency, and ensure the success of your electronic product development project.
0 Comments