Introduction to PCB Warpage Measurement
Printed Circuit Board (PCB) warpage is a critical issue in the electronics manufacturing industry. It can lead to various problems during the assembly process, such as component misalignment, poor solder joint formation, and even device failure. To address this issue, the IPC (Association Connecting Electronics Industries) has released a new standard, IPC-9641, which provides guidelines for measuring PCB warpage during the reflow process.
In this article, we will discuss the importance of measuring PCB warpage, the key features of the IPC-9641 standard, and how to implement it in your manufacturing process.
Why Measure PCB Warpage?
The Impact of PCB Warpage on Assembly Quality
PCB warpage can have a significant impact on the quality of the final assembled product. When a PCB warps during the reflow process, it can cause several issues:
- Component misalignment
- Poor solder joint formation
- Uneven heat distribution
- Increased risk of bridging and tombstoning
These issues can lead to reduced reliability, increased rework costs, and even complete device failure. By measuring PCB warpage, manufacturers can identify potential problems early in the process and take corrective actions to improve assembly quality.
The Benefits of Early Detection
Detecting PCB warpage early in the manufacturing process can help:
- Reduce rework and scrap costs
- Improve overall product quality and reliability
- Increase production efficiency
- Minimize the risk of field failures
By implementing a standardized method for measuring PCB warpage, manufacturers can establish a baseline for acceptable warpage levels and quickly identify boards that exceed these limits.
The IPC-9641 Standard
Key Features of IPC-9641
The IPC-9641 standard, titled “Measurement and Inspection of End-Item Printed Boards for Bow and Twist,” provides a comprehensive set of guidelines for measuring PCB warpage during the reflow process. Some of the key features of the standard include:
- Definition of terms and concepts related to PCB warpage
- Specification of measurement equipment and setup requirements
- Description of measurement procedures for both bow and twist
- Guidance on data analysis and reporting
- Recommendations for establishing acceptable warpage limits
By following the IPC-9641 standard, manufacturers can ensure consistent and accurate measurement of PCB warpage across different facilities and equipment.
Measurement Equipment and Setup
The IPC-9641 standard specifies the use of non-contact measurement methods, such as shadow moiré or fringe projection, for measuring PCB warpage. These methods provide high-resolution, full-field measurements of the board’s surface topography without physically contacting the board.
The standard also provides guidelines for setting up the measurement equipment, including:
- Calibration requirements
- Lighting and environment control
- Sample preparation and handling
- Data acquisition and processing
Proper setup and calibration of the measurement equipment are critical for obtaining accurate and repeatable results.
Measurement Procedures and Data Analysis
The IPC-9641 standard describes detailed procedures for measuring both bow and twist of PCBs. Bow refers to the curvature of the board along its length or width, while twist refers to the board’s rotation about its diagonal axis.
The measurement procedures involve:
- Capturing the board’s surface topography at specified intervals during the reflow process
- Analyzing the captured data to calculate bow and twist values
- Comparing the measured values to established acceptance criteria
- Reporting the results in a standardized format
The standard also provides guidance on data analysis, including methods for calculating statistical parameters such as mean, standard deviation, and cpk values.
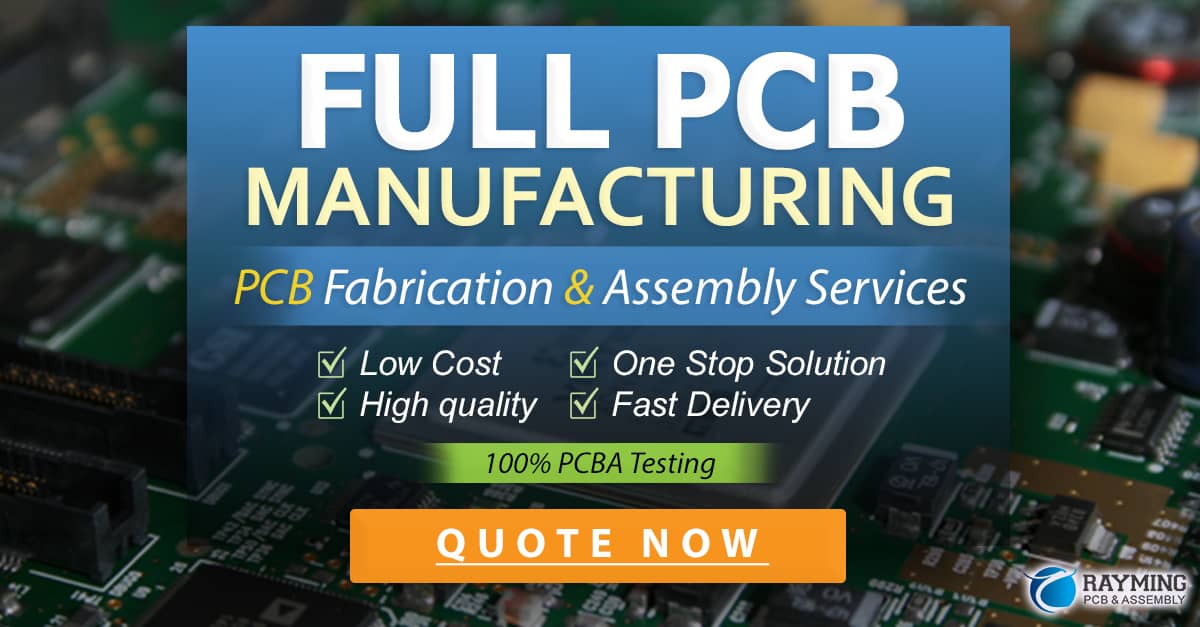
Implementing IPC-9641 in Your Manufacturing Process
Establishing Acceptable Warpage Limits
One of the key steps in implementing the IPC-9641 standard is establishing acceptable warpage limits for your specific products and processes. These limits should take into account factors such as:
- Component type and size
- Board thickness and material
- Reflow profile and peak temperature
- Assembly process requirements
Acceptable warpage limits may vary depending on the application and the specific requirements of your customers. It is important to work closely with your design and engineering teams to establish appropriate limits based on a thorough understanding of your products and processes.
Integrating Warpage Measurement into Quality Control
Once you have established acceptable warpage limits, the next step is to integrate warpage measurement into your quality control processes. This may involve:
- Purchasing or upgrading measurement equipment to meet IPC-9641 requirements
- Training personnel on the proper use of the equipment and interpretation of results
- Developing standard operating procedures (SOPs) for warpage measurement
- Establishing a system for tracking and analyzing warpage data over time
- Implementing corrective actions when warpage limits are exceeded
By making warpage measurement a regular part of your quality control process, you can identify potential issues early and take proactive steps to improve assembly quality and reliability.
Continuous Improvement and Process Optimization
Measuring PCB warpage is not a one-time event, but rather an ongoing process of continuous improvement. By regularly collecting and analyzing warpage data, you can identify trends and patterns that may indicate opportunities for process optimization.
Some potential areas for improvement may include:
- Adjusting reflow profiles to minimize warpage
- Modifying board design or material selection to improve stability
- Implementing better process controls for handling and storage of boards
- Investigating alternative assembly methods or equipment to reduce warpage
By continuously monitoring and optimizing your processes based on warpage data, you can drive ongoing improvements in assembly quality and efficiency.
Frequently Asked Questions (FAQ)
-
Q: What is PCB warpage, and why is it important to measure?
A: PCB warpage refers to the distortion or curvature of a printed circuit board during the reflow process. It is important to measure because excessive warpage can lead to component misalignment, poor solder joint formation, and other assembly defects that can impact product quality and reliability. -
Q: What are the key features of the IPC-9641 standard?
A: The IPC-9641 standard provides guidelines for measuring PCB warpage during reflow, including specification of measurement equipment and setup, description of measurement procedures for bow and twist, guidance on data analysis and reporting, and recommendations for establishing acceptable warpage limits. -
Q: What type of equipment is used for measuring PCB warpage?
A: The IPC-9641 standard specifies the use of non-contact measurement methods, such as shadow moiré or fringe projection, which provide high-resolution, full-field measurements of the board’s surface topography without physically contacting the board. -
Q: How do I establish acceptable warpage limits for my products?
A: Acceptable warpage limits should be based on factors such as component type and size, board thickness and material, reflow profile and peak temperature, and assembly process requirements. It is important to work closely with your design and engineering teams to establish appropriate limits based on a thorough understanding of your products and processes. -
Q: How can I use warpage measurement data to optimize my assembly processes?
A: By regularly collecting and analyzing warpage data, you can identify trends and patterns that may indicate opportunities for process optimization. This may involve adjusting reflow profiles, modifying board design or material selection, implementing better process controls, or investigating alternative assembly methods or equipment to reduce warpage and improve assembly quality.
Conclusion
Measuring PCB warpage during reflow is a critical step in ensuring the quality and reliability of electronic assemblies. The new IPC-9641 standard provides a comprehensive set of guidelines for implementing warpage measurement in your manufacturing process, from equipment setup and measurement procedures to data analysis and reporting.
By following the IPC-9641 standard and integrating warpage measurement into your quality control processes, you can identify potential issues early, establish acceptable warpage limits, and drive continuous improvement in your assembly processes. This, in turn, can help you reduce rework and scrap costs, improve product quality and reliability, and increase overall production efficiency.
As the electronics industry continues to evolve, with ever-increasing demands for smaller, faster, and more complex devices, the importance of measuring and controlling PCB warpage will only continue to grow. By staying up-to-date with the latest standards and best practices, such as IPC-9641, manufacturers can position themselves to meet these challenges and deliver the high-quality, reliable products that their customers demand.
0 Comments