Introduction
Surface mount technology (SMT) assembly refers to the process of mounting and soldering electronic components onto the surface of printed circuit boards (PCBs). SMT assembly enables higher component density and improved automation compared to through-hole assembly. However, the complexity of SMT manufacturing presents challenges in achieving high efficiency and quality. This article examines strategies and solutions for optimizing rapid SMT assembly.
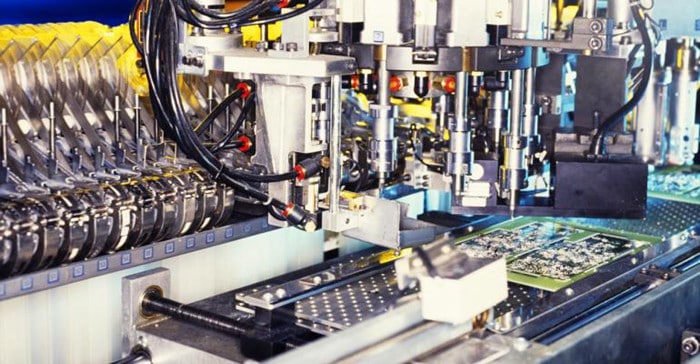
Benefits of Rapid SMT Assembly
Rapid SMT assembly provides a number of benefits:
- Faster time-to-market: Reduced manufacturing lead times allow products to reach the market quicker. This improves competitiveness.
- Increased production capacity: Higher throughput means more products can be assembled with existing equipment and labor.
- Lower costs: Greater efficiency reduces operating costs per unit. This leads to higher profit margins.
- Improved quality: Automated processes are more consistent than manual work, leading to lower defect rates.
- Better responsiveness: Quicker turnaround times can accommodate last-minute design changes and urgent orders.
Challenges in SMT Assembly
However, there are a number of challenges inherent to SMT manufacturing:
- Complex processes: SMT production involves many different steps – printing solder paste, pick-and-place, reflow soldering, cleaning, inspection, etc.
- Small components: Chips, resistors, capacitors and other parts are tiny, making handling difficult.
- High-mix production: Frequent product changeovers are needed for low-volume or high-mix output.
- Quality control: Miniature parts and solder joints are hard to inspect. Defect detection requires automation.
- Precision assembly: Components must be accurately placed to avoid shorts, open circuits, skewed parts and other defects.
Overcoming these challenges is key to rapid SMT assembly. Solutions involve both process innovations and equipment advances.
Process Innovations for Rapid SMT Assembly
Several process strategies can help accelerate SMT production and raise quality levels:
- Simplified product design: Design for manufacturing (DFM) techniques optimize PCB layouts and component choices to streamline assembly. Common tactics include component standardization, elimination of placements on both sides, liberal spacing rules and avoidance of tiny chip resistors and capacitors when possible.
- Lean manufacturing: Apply lean principles to identify and eliminate waste from processes. Common techniques include 5S workplace organization, line balancing, work standardization and Mistake Proofing (Poka-Yoke).
- Set-up reduction: Use changeover methods like SMED (single minute exchange of dies) to slash equipment set-up times during product changeovers. Perform external set-ups and standardize adjustment procedures.
- Concurrent operations: Overlap processes to reduce total cycle time. For example, upload programs while the line operates, reflow one board while another is being solder printed, etc.
- Automated inspection: Replace manual inspection with automated optical inspection (AOI) and X-ray to detect defects rapidly and consistently. Apply automated testing for functionality.
- Process data analytics: Collect and analyze process data to identify bottlenecks, quality issues, line stoppages and other actionable improvement opportunities.
Process Innovation | Description |
---|---|
Simplified Product Design | Design for Manufacturing techniques to optimize PCB layouts and component choices |
Lean Manufacturing | Eliminate waste through 5S, line balancing, standard work, poka-yoke, etc. |
Set-up Reduction | Use SMED and standardization to slash changeover times |
Concurrent Operations | Overlap processes to reduce total cycle time |
Automated Inspection | Employ AOI, X-ray and testing instead of manual inspection |
Process Data Analytics | Collect and analyze process data to drive improvements |
Equipment Advances for Rapid SMT Assembly
New SMT assembly equipment provides capabilities that enable faster, higher quality production:
- High-speed chip shooters: Advanced pick-and-place machines offer faster component mounting with greater accuracy. For example, multi-head and multi-gantry pickers reduce cycle times by working concurrently.
- Intelligent feeders: Features like tape feeder carts with RFID tracking and inventory management automate and streamline feeder set-up for faster changeovers.
- High-precision screen printers: Tight process controls for pressure, squeegee speed and separation provide consistent, high-quality solder paste printing at rapid rates.
- Specialty feeding systems: For small parts like 01005 chips, vibration bowl feeders and linear stick feeders improve feeding reliability.
- Next-generation soldering: Techniques like multi-wave soldering, pin transfer and multi-zone profiling ensure excellent joint quality at faster conveyor speeds.
- Advanced dispensers: High-speed automated dispensing systems accurately apply epoxies, adhesives, silicones and other materials with less waste and superior precision.
- Smart storage solutions: Intelligent warehouses, storage and material handling systems streamline material logistics. Automated planning and replenishment save time.
Equipment Advance | Description |
---|---|
High-Speed Chip Shooters | Advanced pick-and-place machines mount faster with accuracy |
Intelligent Feeders | Automated tape feeder set-up slashes changeover times |
High-Precision Screen Printers | Excellent solder paste printing quality at rapid rates |
Specialty Feeding Systems | Reliable handling of tiny components like 01005 chips |
Next-Generation Soldering | Superior joint quality at fast conveyor speeds |
Advanced Dispensers | High-speed precision application of adhesives and silicones |
Smart Storage Solutions | Streamlined material logistics and planning |
Optimizing the SMT Assembly Line
Equipment Advance | Description |
---|---|
High-Speed Chip Shooters | Advanced pick-and-place machines mount faster with accuracy |
Intelligent Feeders | Automated tape feeder set-up slashes changeover times |
High-Precision Screen Printers | Excellent solder paste printing quality at rapid rates |
Specialty Feeding Systems | Reliable handling of tiny components like 01005 chips |
Next-Generation Soldering | Superior joint quality at fast conveyor speeds |
Advanced Dispensers | High-speed precision application of adhesives and silicones |
Smart Storage Solutions | Streamlined material logistics and planning |
Optimizing the SMT Assembly Line
To maximize the benefits from process improvements and equipment advances, manufacturers should take a holistic approach to optimizing rapid SMT assembly:
- Line balancing: Make sure conveyor lengths and process times are balanced to avoid bottlenecks. Collect and analyze line data.
- Standardized work: Develop precise standard operating procedures for each process to drive consistency.
- Total productive maintenance: Use TPM to improve uptime and performance of equipment. Focus on cleaning, PMs, streamlined changeovers and staff skills.
- Error proofing: Incorporate poka-yoke devices, automation and mistake-proof process designs to prevent defects from occurring.
- Continuous improvement culture: Empower staff at all levels to contribute ideas for improving processes. Provide training in problem-solving tools.
- Lean material flow: Redesign kitting processes, storage locations and material replenishment to streamline material logistics. Utilize Kanban and visual controls.
- Automated guidance: Augmented reality systems can provide pick-by-light instructions and process documentation to workers on the line. This improves quality and productivity.
Careful orchestration of optimized processes, cutting-edge equipment and motivated personnel enables electronics manufacturers to achieve rapid SMT assembly with outstanding quality levels. Maintaining an infrastructure for continuous improvement is critical for sustaining a competitive advantage.
FAQ
What are some quick wins for accelerating SMT assembly?
Some relatively easy tactics for faster SMT assembly include simplifying products designs, minor line balancing adjustments, implementing 5S visual controls, adjusting board flow angles, and optimizing oven zone temperatures.
How can manufacturers handle frequent product changeovers?
Reducing changeover times through SMED, modular jigs, and streamlined changeover procedures allows quick switch overs between products. Versatile lines with flexible equipment also help.
What are key considerations in high-mix low-volume SMT?
Changeover optimization is crucial. Lean material flow and kanban systems keep inventory under control. Modular product designs use standard components as much as possible. Auto-programming helps reduce changeover.
How does automated inspection compare with manual inspection?
Automated optical and X-ray inspection offer superior speed, repeatability, precision, and data capture compared to manual inspection. However, manual inspection still excels at finding hidden or complex defects. A combination is ideal.
Why are tiny components like 01005 chips challenging in SMT assembly?
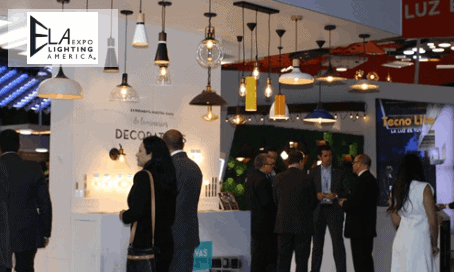
To maximize the benefits from process improvements and equipment advances, manufacturers should take a holistic approach to optimizing rapid SMT assembly:
- Line balancing: Make sure conveyor lengths and process times are balanced to avoid bottlenecks. Collect and analyze line data.
- Standardized work: Develop precise standard operating procedures for each process to drive consistency.
- Total productive maintenance: Use TPM to improve uptime and performance of equipment. Focus on cleaning, PMs, streamlined changeovers and staff skills.
- Error proofing: Incorporate poka-yoke devices, automation and mistake-proof process designs to prevent defects from occurring.
- Continuous improvement culture: Empower staff at all levels to contribute ideas for improving processes. Provide training in problem-solving tools.
- Lean material flow: Redesign kitting processes, storage locations and material replenishment to streamline material logistics. Utilize Kanban and visual controls.
- Automated guidance: Augmented reality systems can provide pick-by-light instructions and process documentation to workers on the line. This improves quality and productivity.
Careful orchestration of optimized processes, cutting-edge equipment and motivated personnel enables electronics manufacturers to achieve rapid SMT assembly with outstanding quality levels. Maintaining an infrastructure for continuous improvement is critical for sustaining a competitive advantage.
FAQ
What are some quick wins for accelerating SMT assembly?
Some relatively easy tactics for faster SMT assembly include simplifying products designs, minor line balancing adjustments, implementing 5S visual controls, adjusting board flow angles, and optimizing oven zone temperatures.
How can manufacturers handle frequent product changeovers?
Reducing changeover times through SMED, modular jigs, and streamlined changeover procedures allows quick switch overs between products. Versatile lines with flexible equipment also help.
What are key considerations in high-mix low-volume SMT?
Changeover optimization is crucial. Lean material flow and kanban systems keep inventory under control. Modular product designs use standard components as much as possible. Auto-programming helps reduce changeover.
How does automated inspection compare with manual inspection?
Automated optical and X-ray inspection offer superior speed, repeatability, precision, and data capture compared to manual inspection. However, manual inspection still excels at finding hidden or complex defects. A combination is ideal.
Why are tiny components like 01005 chips challenging in SMT assembly?
The small size makes handling difficult – they are hard to pick up consistently and susceptible to static. Specialized feeders, tape materials, pick-up tools, lighting and magnification help enable reliable 01005 assembly.
0 Comments