Introduction to PCB-SMD
Printed Circuit Boards (PCBs) are the backbone of modern electronics. They provide a way to mechanically support and electrically connect electronic components using conductive pathways, tracks or signal traces etched from copper sheets laminated onto a non-conductive substrate. One of the most important advancements in PCB technology has been the development of Surface Mount Devices (SMDs) and Surface Mount Technology (SMT).
SMDs are electronic components that are designed to be soldered directly onto the surface of a PCB, rather than being inserted through holes drilled in the board. This has revolutionized the electronics industry, allowing for smaller, more compact devices with increased functionality and reliability.
In this article, we will explore the world of PCB-SMD prototyping, including the benefits of using SMDs, the different types of SMDs available, and the tools and techniques used for PCB-SMD assembly. We will also provide tips and best practices for designing and manufacturing PCB-SMDs, as well as troubleshooting common issues that may arise during the prototyping process.
Benefits of Using SMDs in PCB Prototyping
There are several key benefits to using SMDs in PCB prototyping:
Smaller Size and Higher Density
One of the main advantages of SMDs is their small size compared to through-hole components. This allows for much higher component density on a PCB, which in turn enables the design of smaller, more compact devices. SMDs can be as small as 0.4mm x 0.2mm, making them ideal for applications where space is at a premium, such as smartphones, wearables, and medical devices.
Increased Reliability
SMDs are generally more reliable than through-hole components because they have shorter lead lengths and are less susceptible to mechanical stress and vibration. This is because SMDs are soldered directly onto the surface of the PCB, rather than being inserted through holes and soldered on the opposite side. This also reduces the risk of solder joint failures and improves the overall reliability of the device.
Faster Assembly and Lower Costs
SMDs are designed for automated assembly using pick-and-place machines and reflow soldering techniques. This allows for much faster assembly times compared to manual through-hole soldering, which can significantly reduce labor costs and increase production throughput. Additionally, the smaller size of SMDs means that less PCB material is required, which can further reduce costs.
Improved High-Frequency Performance
SMDs have shorter lead lengths and smaller parasitic capacitance and inductance compared to through-hole components. This makes them ideal for high-frequency applications such as RF and microwave circuits, where signal integrity is critical. SMDs also enable the design of controlled impedance transmission lines on the PCB, which can further improve high-frequency performance.
Types of SMDs Used in PCB Prototyping
There are several different types of SMDs used in PCB prototyping, each with their own unique characteristics and applications. Some of the most common types of SMDs include:
Resistors
SMD resistors are available in a wide range of values and sizes, from 0.1 ohms to several megohms, and from 0201 (0.6mm x 0.3mm) to 2512 (6.3mm x 3.2mm). They are used for current limiting, voltage division, and impedance matching applications.
Capacitors
SMD capacitors are available in various dielectric materials, such as ceramic, tantalum, and polymer, and in capacitance values ranging from a few picofarads to several microfarads. They are used for decoupling, filtering, and energy storage applications.
Inductors
SMD inductors are available in various core materials, such as ferrite, iron powder, and air core, and in inductance values ranging from a few nanohenries to several millihenries. They are used for power supply filtering, impedance matching, and RF tuning applications.
Diodes
SMD diodes are available in various types, such as rectifier, Zener, Schottky, and LED, and in various package sizes, such as SOD-123 and SOT-23. They are used for rectification, voltage regulation, and electrostatic discharge (ESD) protection applications.
Transistors
SMD transistors are available in various types, such as bipolar junction transistors (BJTs), metal-oxide-semiconductor field-effect transistors (MOSFETs), and insulated-gate bipolar transistors (IGBTs), and in various package sizes, such as SOT-23 and SOT-223. They are used for amplification, switching, and voltage regulation applications.
Integrated Circuits (ICs)
SMD ICs are available in a wide range of functions, such as microcontrollers, amplifiers, sensors, and power management ICs, and in various package sizes, such as QFN, SOIC, and BGA. They are used for signal processing, control, and communication applications.
Here is a table summarizing the different types of SMDs and their typical applications:
SMD Type | Typical Applications |
---|---|
Resistors | Current limiting, voltage division, impedance matching |
Capacitors | Decoupling, filtering, energy storage |
Inductors | Power supply filtering, impedance matching, RF tuning |
Diodes | Rectification, voltage regulation, ESD protection |
Transistors | Amplification, switching, voltage regulation |
ICs | Signal processing, control, communication |
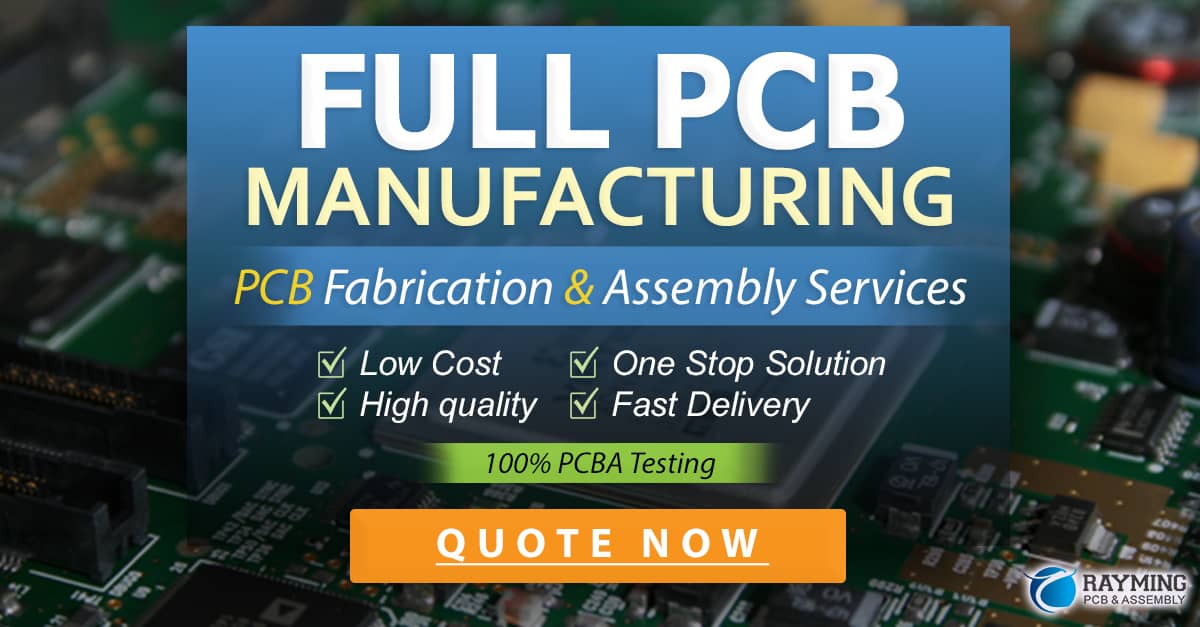
PCB-SMD Assembly Tools and Techniques
Assembling PCB-SMDs requires specialized tools and techniques to ensure proper placement and soldering of the components. Some of the most common tools and techniques used for PCB-SMD assembly include:
Pick-and-Place Machines
Pick-and-place machines are automated systems that use a robotic arm to pick up SMDs from a feeder and place them onto the PCB with high precision and speed. They are typically used for high-volume production runs and can place thousands of components per hour.
Solder Paste Stencils
Solder paste stencils are thin metal sheets with openings that correspond to the pads on the PCB. They are used to apply solder paste to the pads before placing the SMDs. The stencil is aligned with the PCB and solder paste is squeegeed across the surface, filling the openings and leaving a precise amount of solder on each pad.
Reflow Soldering
Reflow soldering is a process where the PCB with SMDs and solder paste is heated in an oven to melt the solder and form a permanent bond between the components and the pads. The temperature profile of the reflow process is carefully controlled to ensure proper melting and solidification of the solder without damaging the components.
Inspection and Testing
After assembly, PCB-SMDs are inspected and tested to ensure proper functionality and reliability. Visual inspection using microscopes or automated optical inspection (AOI) systems can detect solder defects, component misalignment, and other issues. Electrical testing using in-circuit testers (ICT) or flying probe testers can verify the continuity and functionality of the circuits.
Here is a table summarizing the common tools and techniques used for PCB-SMD assembly:
Tool/Technique | Description |
---|---|
Pick-and-Place | Automated system for placing SMDs onto PCB |
Solder Paste Stencil | Metal sheet with openings for applying solder paste to pads |
Reflow Soldering | Heating process for melting solder and bonding SMDs to pads |
Visual Inspection | Using microscopes or AOI systems to detect assembly defects |
Electrical Testing | Using ICT or flying probe testers to verify circuit function |
PCB-SMD Design Tips and Best Practices
Designing PCB-SMDs requires careful consideration of several factors to ensure proper functionality, reliability, and manufacturability. Here are some tips and best practices for PCB-SMD design:
Choose the Right SMD Package
Selecting the appropriate SMD package for each component is critical for ensuring proper fit, performance, and reliability. Consider factors such as the component’s power dissipation, pin count, and footprint size when choosing a package. Use standardized packages whenever possible to simplify procurement and assembly.
Optimize Component Placement
Proper component placement is essential for minimizing signal interference, reducing circuit board size, and improving manufacturing efficiency. Place components in a logical sequence based on their function and connectivity. Keep high-speed components close together to minimize trace lengths and parasitic effects. Avoid placing components too close to the edge of the board or in hard-to-reach areas.
Use Copper Pour and Ground Planes
Using copper pour and ground planes on the PCB can help improve signal integrity, reduce EMI, and dissipate heat. Pour copper on unused areas of the board and connect it to ground to create a low-impedance return path for signals. Use ground planes on dedicated layers to provide a stable reference voltage and shield sensitive signals.
Follow Manufacturer’s Recommended Land Patterns
Each SMD component has a recommended land pattern that specifies the size, shape, and spacing of the pads on the PCB. Following these recommendations ensures proper solderability and reliability of the component. Consult the component’s datasheet or use CAD libraries provided by the manufacturer to create the correct land patterns.
Use Solder Mask and Silkscreen
Solder mask and silkscreen are important features of PCB-SMDs that help improve manufacturability and usability. Solder mask is a thin polymer coating that covers the copper traces on the PCB, leaving only the pads exposed for soldering. This helps prevent solder bridges and short circuits during assembly. Silkscreen is a printed layer of text and symbols that identifies the components and their polarity, making it easier to assemble and troubleshoot the board.
Perform Design Rule Checks (DRC)
Design Rule Checks (DRC) are automated checks performed by PCB design software to verify that the board meets manufacturing and assembly requirements. DRC checks for issues such as minimum trace width and spacing, hole size and spacing, and solder mask clearance. Performing DRC early and often in the design process can help catch errors and avoid costly rework later on.
Here is a table summarizing the key tips and best practices for PCB-SMD design:
Tip/Best Practice | Description |
---|---|
Choose the Right SMD Package | Select package based on power, pin count, and footprint size |
Optimize Component Placement | Place components logically and minimize trace lengths |
Use Copper Pour and Ground Planes | Pour copper and use ground planes for signal integrity and EMI |
Follow Land Pattern Recommendations | Use manufacturer’s recommended land patterns for solderability |
Use Solder Mask and Silkscreen | Apply solder mask and silkscreen for manufacturability and usability |
Perform Design Rule Checks (DRC) | Use DRC to verify manufacturing and assembly requirements |
Common PCB-SMD Prototyping Issues and Troubleshooting
Despite careful design and assembly, PCB-SMDs can still encounter issues during prototyping. Here are some common issues and troubleshooting tips:
Solder Bridges and Short Circuits
Solder bridges and short circuits occur when solder inadvertently connects two or more pads or traces that should be separated. This can happen due to excessive solder paste, improper stencil alignment, or component misplacement. To troubleshoot, visually inspect the board under magnification and use a multimeter to check for continuity between suspect pads. Use solder wick or a desoldering tool to remove the excess solder.
Component Misalignment or Tombstoning
Component misalignment or tombstoning occurs when an SMD is not properly seated on its pads during reflow soldering. This can happen due to uneven solder paste application, incorrect placement, or variations in component size or shape. To troubleshoot, visually inspect the component and its pads for proper alignment and solder joint formation. If necessary, rework the component by removing it, cleaning the pads, and resoldering it with fresh solder paste.
Poor Solder Joint Formation
Poor solder joint formation can occur due to insufficient or excessive solder paste, incorrect reflow temperature profile, or contamination of the pads or component leads. Symptoms include dull, grainy, or incomplete solder joints that may not provide reliable electrical or mechanical connection. To troubleshoot, visually inspect the solder joints under magnification and use X-ray inspection for hidden joints. Rework the joints by removing the old solder, cleaning the pads and leads, and resoldering with fresh solder paste and the correct reflow profile.
Thermal Damage to Components
Thermal damage to components can occur during reflow soldering if the temperature or duration of the heating process exceeds the component’s specifications. Symptoms include discoloration, deformation, or loss of functionality of the component. To troubleshoot, check the reflow temperature profile and compare it to the component’s datasheet. If the component is damaged, remove it and replace it with a new one, making sure to use the correct reflow profile.
Signal Integrity Issues
Signal integrity issues can occur due to improper PCB layout, component selection, or grounding practices. Symptoms include distortion, ringing, or loss of signal quality, especially at high frequencies. To troubleshoot, review the PCB layout for proper trace routing, impedance control, and grounding. Check the component selection for proper frequency response and power handling. Use signal analysis tools such as oscilloscopes or network analyzers to measure and optimize the signal performance.
Here is a table summarizing the common PCB-SMD prototyping issues and troubleshooting tips:
Issue | Troubleshooting Tips |
---|---|
Solder Bridges/Short Circuits | Visually inspect, check continuity, remove excess solder |
Component Misalignment | Inspect alignment and solder joints, rework component |
Poor Solder Joint Formation | Inspect joints, rework with fresh solder paste and correct profile |
Thermal Damage to Components | Check reflow profile, replace damaged component |
Signal Integrity Issues | Review layout, component selection, and grounding, use signal analysis |
FAQ
What is the difference between SMD and through-hole components?
SMD components are designed to be soldered directly onto the surface of a PCB, while through-hole components have leads that are inserted through holes drilled in the board and soldered on the opposite side. SMDs are smaller, faster to assemble, and have better high-frequency performance compared to through-hole components.
Can I mix SMD and through-hole components on the same PCB?
Yes, it is possible to mix SMD and through-hole components on the same PCB, but it requires special design considerations and assembly techniques. The PCB will need to have both surface mount pads and through-holes, and the assembly process will involve both pick-and-place and manual soldering steps. Mixing component types can increase the complexity and cost of the PCB, so it should only be done when necessary.
What is the smallest SMD component size available?
The smallest SMD component size commonly available is 0201, which measures 0.6mm x 0.3mm. Even smaller sizes, such as 01005 (0.4mm x 0.2mm) and 0603 (1.6mm x 0.8mm), are available for specialized applications, but they require advanced assembly equipment and techniques.
How do I choose the right solder paste for PCB-SMD assembly?
Choosing the right solder paste involves considering factors such as the alloy composition, particle size, flux type, and viscosity. The most common solder paste alloy for PCB-SMD assembly is SAC305, which contains 96.5% tin, 3% silver, and 0.5% copper. The particle size should be matched to the stencil aperture size and the pad geometry, with smaller particles used for finer pitch components. The flux type and viscosity should be selected based on the reflow profile and the cleaning requirements of the PCB.
What is the typical reflow temperature profile for PCB-SMD assembly?
The typical reflow temperature profile for PCB-SMD assembly involves four stages: preheat, soak, reflow, and cooling. The preheat stage gradually raises the temperature of the PCB and components to activate the flux and evaporate any solvents. The soak stage maintains a stable temperature to allow the flux to remove any oxides and prepare the surfaces for soldering. The reflow stage raises the temperature above the melting point of the solder alloy, typically around 220-250°C for SAC305, to form the solder joints. The cooling stage gradually lowers the temperature to solidify the solder joints without introducing thermal stress. The exact temperature and duration of each stage depends on the specific solder paste and PCB design, and should be optimized through experimentation and profiling.
Conclusion
PCB-SMD prototyping is a critical process in the development of modern electronic devices. By using surface mount components and assembly techniques, designers can create smaller, faster, and more reliable PCBs with improved functionality and performance. However, PCB-SMD prototyping also requires careful design considerations, specialized tools and techniques, and attention to detail to ensure proper manufacturability an
0 Comments