Introduction
Developing new electronic products requires building multiple iterations of prototype printed circuit boards (PCBs) to test designs and features before finalizing them for production. Prototyping is an indispensable phase of product development, validation, and refinement.
To accelerate prototyping and avoid delays, partnering with an experienced prototype PCB manufacturer is essential. However, not all PCB vendors provide specialized support for fast-turnaround, flexible, small-batch prototyping.
This guide covers how to identify and select the right PCB supplier for prototype services by exploring:
- The prototyping process and its benefits
- Capabilities to look for in a prototyping partner
- Key factors to consider when selecting a vendor
- How prototype and production PCB manufacturing differ
- Strategies for reducing prototype expenses
- Ensuring quality despite compressed timelines
- Questions to ask potential suppliers
- Pitfalls to avoid when prototyping boards
Understanding prototype PCB manufacturing will enable smart outsourcing of this critical activity to focus internal resources on design and engineering.
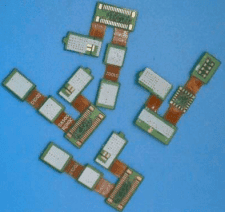
The PCB Prototyping Process and Its Benefits
PCB prototyping involves producing multiple iterations of a printed circuit board design in small quantities to validate functionality and performance before large scale production.
Typical prototyping steps include:
- Producing initial concept PCBs focused purely on functionality even with crude aesthetics
- Building more refined versions to test form, fit, and subtleties like EMI/RFI
- Environmental stress testing with vibration, temperature cycling, etc.
- Pilot testing of PCBs in the final product and environment
- Producing final pre-production prototypes prior to mass manufacturing
Each phase provides valuable data to improve the design and identify issues early before large financial and time investments in tooling and volume production.
Benefits of thorough prototyping include:
Risk mitigation – Finding and resolving problems early prevents costly production delays and fixes.
Faster time-to-market – Learning, feedback and refinement accelerates development.
Design validation – Testing proves the design works as intended before launch.
Cost reduction – Errors found during prototyping prevent waste in mass production.
Improved quality – More robust performance and reliability by discovering corner cases.
Responsive changes – Tweaks and optimizations are simple with an agile supplier.
Prototyping is essential, but choosing the right PCB provider enables maximizing these benefits.
Capabilities to Look for in a Prototyping Partner
To fully leverage prototyping PCBs and avoid limitations that lead to delays, look for these key capabilities in a potential supplier:
Rapid fabrication turnaround – Look for 1-3 day turnarounds to prevent waiting weeks between iterations.
Flexible small quantities – Produce 5-10 boards of a design without high costs or minimums.
Design-for-manufacturability reviews – Engineer feedback during layout ensures producibility.
Manual assembly – Hand-soldering of SMT components quickly without costly setup charges.
Multiple revision support – Reuse gerbers across iterations without full data resubmission each time.
One-stop-shop – End-to-end services like design, fabrication, assembly, and testing avoids coordinating multiple vendors.
Supply chain services – Assistance procuring components, inventory management, and shipments.
Local facilities – Geographic proximity speeds logistics and communication.
Exceptional support – Direct engineering access and transparent order tracking prevents delays.
Established quality processes – Consistent results despite condensed timelines.
The best prototyping partners offer much more than just bare PCB fabrication. Seek comprehensive capabilities.
Key Selection Factors for Prototype PCB Suppliers
Consider these important criteria when evaluating and selecting among prototype circuit board manufacturers:
Technical expertise – Look for in-depth electronic and PCB design knowledge to provide expert guidance.
Prototype focus – Avoid general PCB vendors optimized for mid/high-volume production.
Capability range – Supports various board complexities – layers, materials, features, etc.
Order flexibility – Comfortable with shifting priorities and changes vs optimizing rigid production pipelines.
Quality pedigree – Known for consistently delivering high-quality boards with low defects.
Customer reviews – Ask peers about firsthand vendor experience and reputation.
Security – Protects customers’ sensitive designs and IP. Ask about practices.
Business stability – Check for 7+ years in business with steady growth and customers.
Fair pricing – Reasonable costs for small quantities and services. Avoid very low (risky) and very high bids.
Communication skills – Responsive account management and sales staff.
Evaluating suppliers on these factors will help identify the right PCB prototyping partner for your needs.
How Prototype PCB Manufacturing Differs from Production
Prototype PCB fabrication has much different goals, processes, and priorities compared to full-scale printed circuit board production. Some key differences include:
Volumes – Prototyping requires much smaller quantities, often just a few boards. Production involves large lot sizes.
Turnaround time – Prototypes favor ultra-fast turnarounds, sometimes 1-3 days. Mass production has longer ~8-12 week timeframes.
Yields – Getting functional boards is prioritized over efficiency and waste for prototypes. Production maximizes yield.
Quality – Some defects and variances are acceptable for prototypes. Production demands near-perfect results.
Testing – Limited testing often manual visual inspection for prototypes. High-volume needs extensive automated testing.
Processes – Specialized techniques used for fast prototyping that differ from mass production methods.
Costs – Unit price is higher for prototypes but total spend is contained. Production focuses on high-volume cost savings.
Interactions – Prototyping requires considerable hands-on engineering collaboration. Production relationships are more transactional.
Priorities – Prototyping emphasizes responsiveness, flexibility, and problem-solving. Production values consistency, schedules, and precision.
Recognizing these priorities when assessing suppliers is crucial to match needs to capabilities.
Strategies for Reducing Prototype PCB Expenses
By nature, small-batch printed circuit boards cost more per unit than high-volume production. However, smart prototyping can help minimize expenses:
- Use budget materials – Save cost using FR-4 vs advanced substrates for early iterations only testing functionality.
- Avoid advanced finishes – Apply surface finishes like ENIG, Immersion Silver or Gold only when needed. Use HASL or bare copper initially.
- Skip soldermask – Leave soldermask off non-critical areas when aesthetics are not important.
- Relax tolerances – Loosen tolerances wherever functionality allows more process leeway.
- Simplify testing – Only perform key parameter or functional tests to confirm operation rather than comprehensive evaluation.
- Reuse panels – Order prototypes on same panel sizes as previous versions to save setup costs.
- Panelize efficiently – Carefully nest multiple boards on each panel to maximize material utilization.
- Adjust quantities – Increase per-revision quantities to benefit from volume discounts while minimizing unused boards.
Work closely with your supplier to identify the most impactful areas to reduce prototyping costs.
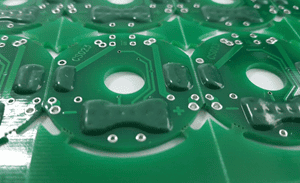
Ensuring Quality With Accelerated Prototype Lead Times
Maintaining consistent quality with extremely condensed PCB fabrication lead times requires specialized processes:
Tighter process controls – Precisely monitor chemistry concentrations, exposures, temperatures, and other parameters.
More frequent machine calibration – Increase maintenance and calibration intervals compared to production lines for stability.
Enhanced inspection – Thoroughly inspect every board under magnification given limited testing time.
Lean production – Eliminate waste and non-value steps from the process flow.
Qualified materials – Use proven suppliers and lots to minimize variability.
Skilled teams – Dedicate the most experienced staff to time-critical prototyping orders.
Prioritization – Prototype orders take priority over standard production when scheduling.
Test coupons – Include dedicated test points and structures on panels for rapid quality checks.
Real-time monitoring – Track WIP on the shop floor to catch any process excursions immediately.
With rigorous quality practices tailored for prototyping, reliability need not suffer even with accelerated fabrication schedules.
Questions to Ask Potential Prototype PCB Suppliers
Evaluating vendors goes beyond just technical capabilities and order details. Here are insightful questions to probe a supplier’s prototyping competency:
- How long have you offered prototyping services? What % of orders are prototypes vs production?
- What are your fastest and average turnaround times for prototype orders?
- What prototyping-specific processes, tools, and expertise do you leverage?
- How do you ensure quality for prototypes with shortened fabrication times?
- How many prototype iterations do customers typically require before finalizing a design?
- Can you provide referrals from customers with complex prototypes you’ve manufactured?
- How do you protect customers’ intellectual property and confidential designs?
- How much engineering support, DFM analysis, and recommendations do you provide during prototyping?
- What challenges do new customers commonly face with their initial prototypes? How do you help them resolve those issues?
- Why should we select your company over another prototyping provider?
The supplier’s responses will provide insight into their suitability beyond just their website list of services.
Pitfalls to Avoid When Prototyping Boards
While prototyping printed circuit boards is indispensable, avoid these common missteps:
- Attempting to finalize designs without building physical prototype boards first.
- Underestimating the number of design iterations and prototype boards needing testing.
- Skipping prototyping altogether to save time or money.
- Using a vendor unfamiliar with prototyping needs.
- Selecting a supplier based on lowest cost rather than capabilities and expertise.
- Failing to budget for multiple boards needed across prototyping phases.
- Neglecting to order spare PCBs to protect schedules from potential issues or damage.
- Holding suppliers to mass production quality levels rather than assessing functional viability.
- Not prioritizing manufacturability reviews during layout to avoid fabrication issues.
Avoiding these pitfalls helps ensure prototyping proceeds smoothly and provides maximum benefits.
Frequently Asked Questions
What are the typical quantities for prototype PCB orders?
Prototype quantities are usually between 5 and 10 boards on the low end, and up to about 25 boards on the high side. Some complex designs may warrant 50-100 boards to allow extensive testing.
How many different revisions are typical during prototyping?
Most products require at least 2-3 significant design revisions that necessitate building new prototype boards. More complex products often undergo 5+ iterations before being finalized.
What fabrication lead times are common for prototype PCB orders?
Leading prototype PCB suppliers offer lead times between 1 and 5 days for simple boards. Typical lead times range from 5-10 days for more complex designs requiring more processing steps.
Should every design iteration use the same manufacturer?
Consistency is preferable when prototyping multiple revisions, as the supplier gains familiarity with the design and can better optimize their processes. But changing is acceptable if quality or pricing issues emerge.
How much more expensive is prototyping PCB compared to mass production?
As a rough estimate, prototype boards tend to cost anywhere from 10X to 100X more than large volume production of the same design, depending on quantity differences and complexity.
0 Comments