Introduction to Prepreg and PCB Core
In the world of printed circuit board (PCB) manufacturing, two essential materials play a crucial role in the construction and performance of the final product: prepreg and PCB core. Both materials serve as the foundation for the PCB, providing structural support and insulation between the conductive layers. However, despite their similar functions, prepreg and PCB core have distinct characteristics and properties that set them apart. In this comprehensive guide, we will delve into the intricacies of prepreg and PCB core, comparing their composition, manufacturing processes, and applications to help you make informed decisions when designing and fabricating PCBs.
What is Prepreg?
Prepreg, short for pre-impregnated, is a composite material consisting of a reinforcement fabric, such as fiberglass, that is pre-impregnated with a partially cured resin system. The resin is typically an epoxy-based material that has been partially polymerized, allowing it to maintain a semi-solid state at room temperature. This unique composition enables prepreg to be easily handled and stored until it is ready to be used in the PCB manufacturing process.
Composition of Prepreg
The two main components of prepreg are the reinforcement fabric and the resin system. The most common reinforcement fabric used in prepreg is fiberglass, which provides excellent mechanical strength and dimensional stability. Other reinforcement materials, such as aramid or carbon fiber, may be used for specialized applications that require higher strength or thermal conductivity.
The resin system in prepreg is usually an epoxy-based material that has been partially cured. The partial curing process, also known as B-staging, allows the resin to maintain a semi-solid state at room temperature, making it easy to handle and store. The resin system also contains various additives, such as curing agents, flame retardants, and fillers, which enhance the properties of the prepreg and the resulting PCB.
Manufacturing Process of Prepreg
The manufacturing process of prepreg involves several steps:
-
Impregnation: The reinforcement fabric is impregnated with the resin system using a process called dip-coating or roll-to-roll coating. The fabric is passed through a bath containing the liquid resin, ensuring uniform distribution of the resin throughout the fabric.
-
Partial Curing: After impregnation, the prepreg undergoes a partial curing process, also known as B-staging. This process involves exposing the prepreg to heat and pressure, causing the resin to partially polymerize and solidify. The B-staging process is carefully controlled to ensure that the resin reaches the desired level of polymerization while maintaining its ability to flow and bond during the final PCB lamination process.
-
Cutting and Packaging: Once the prepreg has been partially cured, it is cut to the desired size and shape using precision cutting equipment. The prepreg sheets are then packaged in moisture-resistant materials to prevent contamination and maintain their quality until they are ready to be used in the PCB manufacturing process.
What is PCB Core?
PCB core, also known as the substrate or base material, is the foundation upon which the conductive layers and components of a PCB are built. It is a rigid, insulating material that provides structural support and electrical insulation between the conductive layers of the PCB.
Composition of PCB Core
PCB core is typically made from a composite material consisting of a reinforcement fabric, such as fiberglass, impregnated with a fully cured resin system. The most common type of PCB core is FR-4, which is made from a woven fiberglass fabric impregnated with an epoxy resin. Other types of PCB core materials include:
- FR-2: A paper-based phenolic resin laminate used for low-cost, low-performance applications.
- CEM-1: A composite material consisting of a non-woven fiberglass mat and a paper core, impregnated with an epoxy resin.
- Polyimide: A high-performance, heat-resistant material used for applications that require excellent thermal stability and mechanical strength.
- PTFE: A low-dielectric-constant material used for high-frequency applications, such as RF and microwave circuits.
Manufacturing Process of PCB Core
The manufacturing process of PCB core involves several steps:
-
Impregnation: The reinforcement fabric is impregnated with the resin system using a process similar to that used for prepreg. However, in the case of PCB core, the resin is fully cured during the impregnation process.
-
Curing: After impregnation, the PCB core undergoes a complete curing process, where it is exposed to heat and pressure to fully polymerize the resin. This process results in a rigid, stable material that can withstand the subsequent processing steps.
-
Cutting and Drilling: Once the PCB core has been fully cured, it is cut to the desired size and shape using precision cutting equipment. Holes are then drilled through the core to accommodate vias and other interconnects that will be used to connect the conductive layers of the PCB.
-
Surface Finishing: The surface of the PCB core is then prepared for the application of the conductive layers. This may involve a process called desmearing, which removes any resin smear from the drilled holes, ensuring a clean surface for the copper plating process.
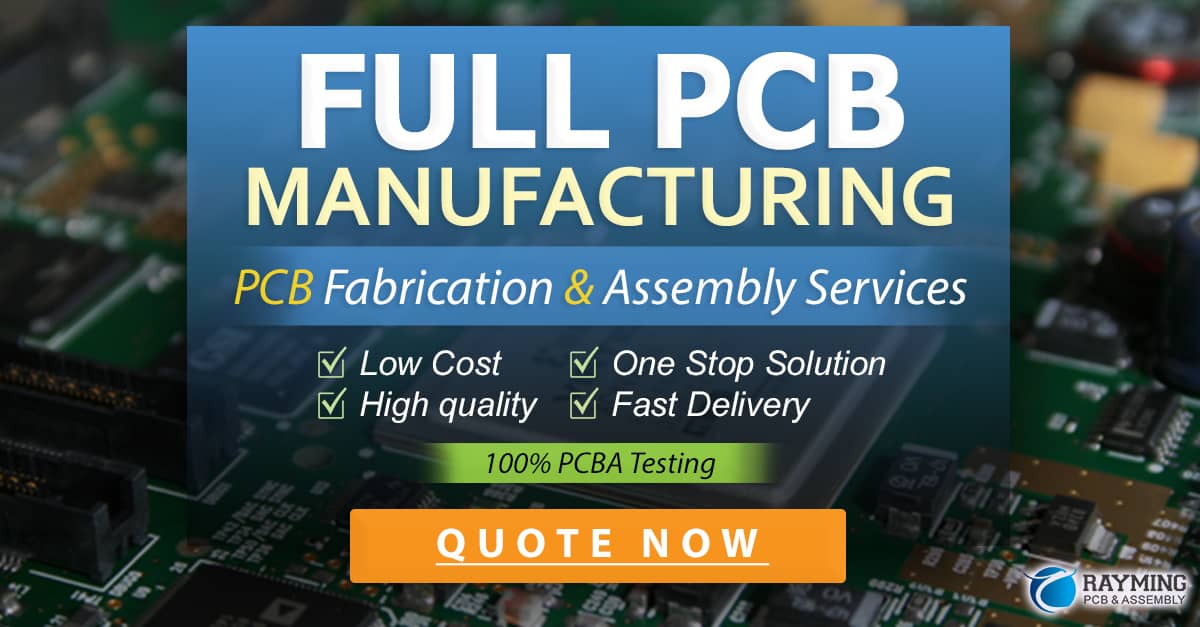
Comparing Prepreg and PCB Core
While both prepreg and PCB core serve as the foundation for PCBs, they have distinct differences in their composition, manufacturing processes, and applications. Let’s compare these two materials across various aspects:
Composition
Aspect | Prepreg | PCB Core |
---|---|---|
Reinforcement Fabric | Fiberglass, aramid, or carbon fiber | Fiberglass, paper, or non-woven mat |
Resin System | Partially cured epoxy | Fully cured epoxy, phenolic, or other resins |
Additives | Curing agents, flame retardants, fillers | Similar additives, depending on the specific material |
Manufacturing Process
Aspect | Prepreg | PCB Core |
---|---|---|
Impregnation | Dip-coating or roll-to-roll coating | Similar to prepreg |
Curing | Partial curing (B-staging) | Full curing |
Cutting and Packaging | Cut to size and packaged in moisture-resistant materials | Cut to size and drilled for vias and interconnects |
Surface Finishing | Not applicable | Desmearing and surface preparation for copper plating |
Applications
Aspect | Prepreg | PCB Core |
---|---|---|
Primary Use | Bonding layers in multi-layer PCBs | Foundation for single-layer and multi-layer PCBs |
Flexibility | Can be used for flexible and Rigid-Flex PCBs | Primarily used for rigid PCBs |
High-frequency Applications | Suitable for high-frequency applications when using low-dielectric-constant materials | Suitable for high-frequency applications when using materials like PTFE |
Thermal Management | Can be used with thermally conductive materials for better heat dissipation | Limited thermal management capabilities |
Advantages and Disadvantages of Prepreg and PCB Core
Prepreg
Advantages:
– Enables the creation of multi-layer PCBs with strong, reliable bonds between layers
– Provides excellent insulation and dielectric properties
– Can be used for flexible and rigid-Flex PCBs
– Allows for the use of specialized materials for high-frequency and thermal management applications
Disadvantages:
– Requires careful storage and handling to maintain quality
– More expensive than PCB core materials
– Requires additional processing steps during PCB manufacturing
PCB Core
Advantages:
– Provides a strong, stable foundation for PCBs
– Less expensive than prepreg materials
– Simpler manufacturing process compared to prepreg
– Suitable for a wide range of applications, from low-cost to high-performance
Disadvantages:
– Limited flexibility compared to prepreg
– Limited thermal management capabilities
– May require additional surface preparation steps before applying conductive layers
Applications of Prepreg and PCB Core in PCB Manufacturing
Prepreg and PCB core are essential materials in the PCB manufacturing process, each serving specific purposes and enabling the creation of a wide range of PCB Types.
Multi-layer PCBs
Prepreg is the primary material used for bonding the layers of a multi-layer PCB. In this application, alternating layers of prepreg and copper-clad PCB core are stacked and then subjected to heat and pressure in a lamination press. During this process, the partially cured resin in the prepreg flows and bonds the layers together, creating a strong, reliable connection between the conductive layers.
Flexible and Rigid-Flex PCBs
Prepreg is also used in the manufacturing of flexible and rigid-flex PCBs. In these applications, a flexible prepreg material, such as a polyimide-based prepreg, is used to bond the flexible layers of the PCB. The rigid sections of the PCB are constructed using standard PCB core materials, such as FR-4.
High-Frequency PCBs
Both prepreg and PCB core can be used in the manufacturing of high-frequency PCBs, such as those used in RF and microwave applications. For these applications, specialized materials with low dielectric constants, such as PTFE-based prepregs or PCB cores, are used to minimize signal loss and maintain signal integrity at high frequencies.
Thermally Conductive PCBs
Prepreg can be used in the manufacturing of thermally conductive PCBs, which are designed to efficiently dissipate heat generated by the components on the board. In these applications, thermally conductive prepregs, such as those containing ceramic fillers or metal particles, are used to enhance the thermal conductivity of the PCB.
Frequently Asked Questions (FAQ)
-
What is the main difference between prepreg and PCB core?
The main difference between prepreg and PCB core is their composition and curing state. Prepreg is a composite material consisting of a reinforcement fabric pre-impregnated with a partially cured resin system, while PCB core is a fully cured, rigid material that serves as the foundation for the PCB. -
Can prepreg be used as a standalone PCB material?
No, prepreg is not used as a standalone PCB material. It is primarily used for bonding layers in multi-layer PCBs and requires additional processing steps, such as lamination, to create a functional PCB. -
What is the most common type of PCB core material?
The most common type of PCB core material is FR-4, which is made from a woven fiberglass fabric impregnated with an epoxy resin. -
Can PCB core be used for flexible PCBs?
Standard PCB core materials, such as FR-4, are not suitable for flexible PCBs due to their rigidity. Flexible PCBs typically use flexible substrates, such as polyimide films, along with flexible prepreg materials for bonding the layers. -
How do I choose between prepreg and PCB core for my PCB design?
The choice between prepreg and PCB core depends on the specific requirements of your PCB design. Factors to consider include the number of layers, flexibility requirements, thermal management needs, and the intended application (e.g., high-frequency or standard). Consult with your PCB manufacturer or a PCB design expert to determine the most suitable materials for your project.
Conclusion
Prepreg and PCB core are two fundamental materials in the world of PCB manufacturing, each serving a unique purpose in the construction of printed circuit boards. While prepreg is primarily used for bonding layers in multi-layer PCBs and providing insulation between conductive layers, PCB core serves as the rigid foundation upon which the PCB is built.
Understanding the differences between these two materials, including their composition, manufacturing processes, and applications, is crucial for designing and fabricating high-quality, reliable PCBs. By carefully selecting the appropriate prepreg and PCB core materials based on the specific requirements of your project, you can ensure optimal performance, durability, and cost-effectiveness in your PCB designs.
As PCB technology continues to advance, it is essential for designers and manufacturers to stay informed about the latest developments in prepreg and PCB core materials. By leveraging the unique properties and capabilities of these materials, the electronics industry can push the boundaries of innovation and create increasingly sophisticated and efficient electronic devices.
0 Comments