What are PCB Stencils?
PCB stencils, also known as solder paste stencils, are thin metal sheets with laser-cut openings that correspond to the pads on a printed circuit board (PCB). These stencils are used to apply solder paste onto the pads of a PCB before components are placed and soldered. The use of PCB stencils ensures precise and consistent solder paste application, which is crucial for achieving reliable and high-quality solder joints.
Types of PCB Stencils
There are several types of PCB stencils available, each with its own advantages and disadvantages:
Stencil Type | Material | Thickness | Advantages | Disadvantages |
---|---|---|---|---|
Laser-cut | Stainless steel, nickel, or mylar | 0.1-0.2mm | High precision, durability | Higher cost, longer lead time |
Chemical-etched | Stainless steel or brass | 0.1-0.2mm | Lower cost, faster lead time | Lower precision compared to laser-cut |
Electroformed | Nickel | 0.05-0.15mm | Extremely fine pitch capabilities | Higher cost, fragile |
3D-printed | Resin | 0.1-0.2mm | Rapid prototyping, low cost | Limited durability, lower precision |
How to Make PCB Stencils
Step 1: Prepare the PCB Design
To create a PCB stencil, you first need to have a completed PCB design. Ensure that your design includes all the necessary pads and that the pad sizes are appropriate for the components you plan to use. Most PCB design software, such as Altium Designer or KiCad, can generate stencil files (usually in Gerber format) based on your PCB layout.
Step 2: Choose a Stencil Fabrication Method
As mentioned earlier, there are several methods for fabricating PCB stencils. Choose the method that best suits your needs based on the required precision, durability, and budget. For most applications, laser-cut stainless steel stencils offer the best combination of precision and durability.
Step 3: Select a Stencil Thickness
The thickness of your PCB stencil will depend on the size of the pads and the amount of solder paste required. A general rule of thumb is to use a stencil thickness that is approximately 60-80% of the pad width. For example, if your pads are 0.5mm wide, a stencil thickness of 0.3-0.4mm would be appropriate.
Step 4: Generate Stencil Files
Using your PCB design software, generate the necessary stencil files. These files should include the aperture locations and sizes corresponding to the pads on your PCB. Ensure that the files are in a format compatible with your chosen stencil fabrication method (e.g., Gerber files for Laser-Cut Stencils).
Step 5: Submit Files to a Stencil Manufacturer
Send your stencil files to a reputable stencil manufacturer. Provide them with any additional specifications, such as the desired stencil material, thickness, and any special instructions. The manufacturer will then fabricate your stencil according to your specifications.
Step 6: Inspect and Clean the Stencil
Upon receiving your PCB stencil, carefully inspect it for any defects or inconsistencies. Check that the apertures align correctly with your PCB Pads and that there are no signs of damage or contamination. Before using the stencil, clean it thoroughly with isopropyl alcohol to remove any residues or oils that may affect solder paste application.
Using PCB Stencils
Step 1: Secure the PCB
Place your PCB on a flat, stable surface. If your PCB has any components already soldered, ensure that they are protected or masked off to prevent solder paste from accidentally contacting them.
Step 2: Align the Stencil
Carefully align your PCB stencil with the pads on the PCB. Use alignment pins or fiducials to ensure accurate positioning. If your stencil has a frame, secure it to the PCB using tape or clamps.
Step 3: Apply Solder Paste
Place a small amount of solder paste on one end of the stencil. Using a squeegee or metal blade, spread the solder paste across the stencil, filling the apertures. Maintain a consistent pressure and angle (typically 45-60 degrees) while moving the squeegee across the stencil. Ensure that all apertures are filled with solder paste and that there is no excess paste on the stencil surface.
Step 4: Remove the Stencil
Carefully lift the stencil away from the PCB, ensuring that the solder paste remains on the pads. Inspect the pads to verify that the solder paste has been applied evenly and consistently.
Step 5: Clean the Stencil
After each use, clean your PCB stencil thoroughly with isopropyl alcohol. This will prevent the buildup of solder paste residue, which can affect the quality of future solder paste applications. Store your stencil in a clean, dry place to protect it from damage and contamination.
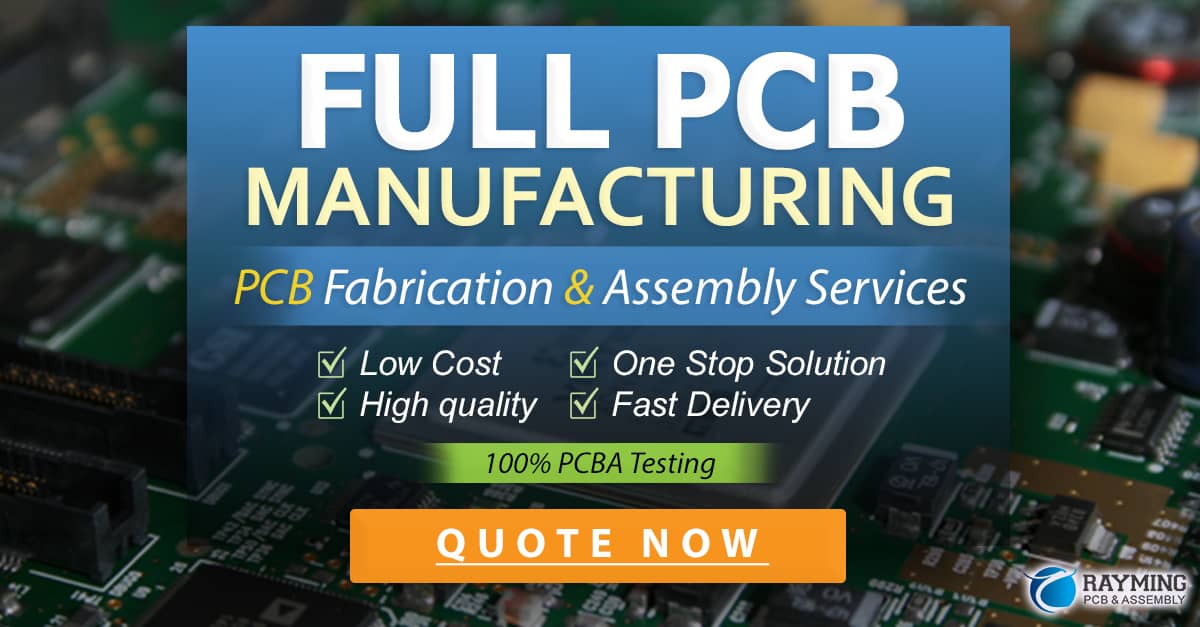
Frequently Asked Questions (FAQ)
-
Can I reuse my PCB stencil?
Yes, PCB stencils can be reused multiple times if they are properly cleaned and stored after each use. However, over time, the apertures may become worn or damaged, affecting the quality of solder paste application. If you notice any inconsistencies or defects, it may be time to replace your stencil. -
How do I choose the right solder paste for my PCB?
When selecting a solder paste, consider factors such as the alloy composition, particle size, and flux type. The alloy composition should match the requirements of your components and PCB materials. Particle size affects the printing process and the final Solder Joint Quality. Flux type (e.g., rosin, no-clean, water-soluble) depends on your cleaning process and environmental considerations. -
What is the shelf life of solder paste?
The shelf life of solder paste varies depending on the manufacturer and storage conditions. Generally, solder paste has a shelf life of 6-12 months when stored at a temperature of 0-10°C (32-50°F). Always check the manufacturer’s guidelines and expiration date before using solder paste. -
How do I store my PCB stencil when not in use?
Store your PCB stencil in a clean, dry place, away from direct sunlight and extreme temperatures. Keep the stencil flat to prevent warping or damage to the apertures. Consider storing your stencil in a protective case or envelope to minimize the risk of contamination or damage. -
Can I make my own PCB stencil at home?
While it is possible to make a basic PCB stencil at home using materials like mylar or kapton film, the precision and durability of these homemade stencils will be limited. For best results, it is recommended to use professionally manufactured stencils, especially for high-density PCB designs or production-level work.
Conclusion
PCB stencils are an essential tool for achieving precise and consistent solder paste application in surface mount assembly. By following the steps outlined in this guide, you can create high-quality PCB stencils that will help you produce reliable and professional-looking PCBs. Remember to choose the appropriate stencil fabrication method, material, and thickness based on your specific requirements, and always handle and store your stencils with care to ensure optimal performance and longevity.
0 Comments