Developing the first working versions of a new printed circuit board (PCB) design requires an experienced prototype partner. The right PCB prototyping service provides a blend of rapid fabrication, robust assembly capabilities, and engineering support to transform your design from concept to physical reality.
Choosing the optimal prototype service accelerates your development timeline and avoids costly delays at this critical phase. This guide covers key factors to evaluate when selecting a PCB prototyping partner:
Capabilities Summary
Start by verifying the service provider offers the full range of prototyping capabilities you will likely utilize:
- PCB fabrication from simple 2-layer to complex multilayer boards
- SMT assembly with automated pick-and-place and soldering
- Hand soldering services for large components
- Component procurement including hard-to-find and long lead-time parts
- Design for Manufacturing (DFM) reviews and layout optimization
- Fast turnaround options from 24 hours to 1 week delivery
Ideally, the partner should handle PCB production, assembly, and procurement to simplify logistics.
Facilities and Equipment
Look for state-of-the-art facilities outfitted with leading-edge equipment:
- Fabrication – newer photolithography, etching, drilling, and lamination equipment
- Clean rooms – ISO Class 8 or better for assembly and sensitive processes
- SMT Lines – high-precision pick-and-place and soldering equipment
- Test and inspection – x-ray, AOI, flying probe, and functional test systems
- Prototyping – dedicated lines for low-medium volume batches
Modernized equipment and separated low/high volume areas prevent prototyping disruptions.
Engineering Expertise
Knowledgeable engineering staff enables the provider to support challenging prototype boards:
- Fabrication engineers to identify optimizations for manufacturability
- CAM engineers to ensure accurate data processing from your CAD files
- Assembly engineers to create SMT programs, manage hand soldering, etc.
- Quality engineers to guarantee reliable PCB production and assembly
- Test engineers to validate board-level functionality thoroughly
Equally important is application knowledge for your specific industry and product type.
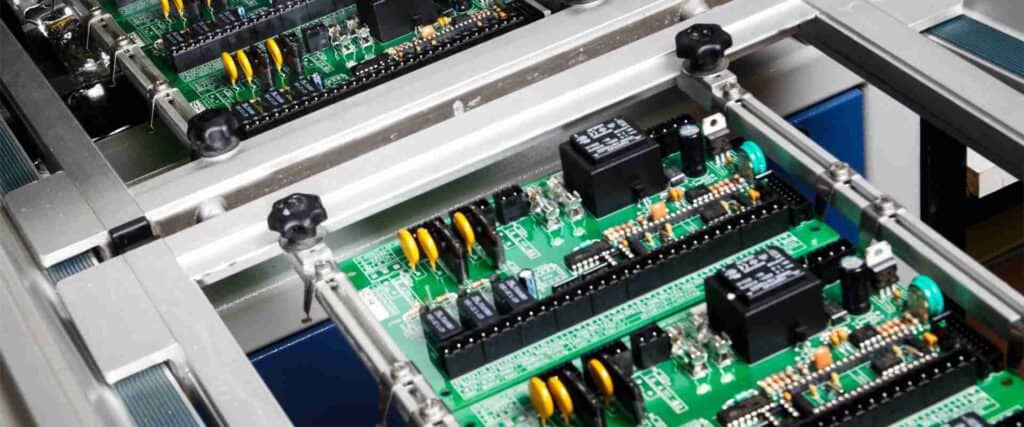
Quality Processes
Consistently producing high-quality prototype boards is crucial:
- PCB quality – demands robust fabrication process controls and inspection
- Assembly quality – requires strict component handling and soldering standards
- Outgoing quality – thorough finished board testing reduces field failures
Look for ISO 9001 or similar certified QMS processes. But also ask for specific quality metrics like fabrication yield and assembled board first-pass test yield.
Design Review and DFM Analysis
To maximize the likelihood of successful prototypes, leverage the provider’s design review services:
- Design rule checks – validate traces, spacing, hole sizes, etc. per fabrication capabilities
- DFM analysis – identify any issues with manufacturability of the layout
- Gerber review – check data integrity, layer alignment, omit/incorrect layers
- Library consistency – confirm CAD parts match vendor component libraries
Addressing flaws through redesign early prevents higher cost fixes later.
Supply Chain Management
Especially for advanced or long lead-time components, the provider should demonstrate supply chain expertise:
- Established distributor networks – enables competitive pricing on volume components
- Custom procurement – ability to source hard-to-find or obsolete parts
- Strategic stocking – inventory common high-value components to prevent delays
- ** lifecycle monitoring** – identify risk of component obsolescence or discontinuation
Having reliable access to required parts prevents component roadblocks.
Customer Service
As a services business, customer support is vital – assess their commitment to service:
- Technical experts – sales engineers to ensure the right solution
- Project management – single point of contact and schedule oversight
- Manufacturing transparency – production monitoring and status updates
- Issue resolution – clear escalation and support through problems
- Continuous improvement – incorporate customer feedback into better service
Getting your questions answered quickly eases the prototyping experience.
Security Considerations
For prototyping confidential designs, probe the partner’s data security provisions:
- Non-disclosure policies – mandatory for staff to protect customer data
- Secure data – encryption for transmitted and stored project files
- Physical security – restricted access to production facilities
- Digital security – protection against network threats, viruses, etc.
- Disaster recovery – data backups and contingency planning
Verify they treat your intellectual property with appropriate security.
Cost Optimization
While minimizing price is appealing, carefully balance cost vs:
- Quality – higher yields and reliability from a capable producer
- Turnaround time – faster market entry with accelerated fabrication
- Overheads – dedicated account reps and engineering support
- Long-term partnership – joint roadmap for future projects beyond initial prototypes
Leverage value-added services like DFM analysis to maximize bang-for-buck.
Assessing Potential Prototype Partners
Use this checklist when evaluating PCB prototype services:
- Full turn-key fabrication to assembly services
- Flexible and fast production capacities
- Skilled engineering teams for design review and DFM
- Quality management rigor for consistent results
- Leading-edge fabrication and assembly equipment
- Supply chain excellence for procuring parts
- Security provisions to protect sensitive designs
- Excellent customer service and communication
- Competitive pricing matched to overall value
PCB prototyping hinges on choosing the right partner – thoroughly qualify prospective services against these criteria.
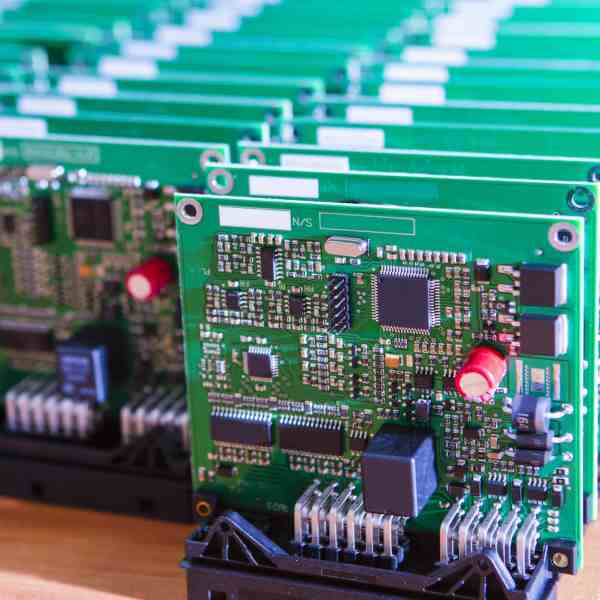
Onboarding a New Provider
When transitioning to a new PCB prototyping service, implement the following best practices:
- Start with a non-critical pilot project first before committing fully
- Review the first set of prototypes extensively to confirm acceptable quality
- Clearly communicate your specifications, expectations, and requirements
- Assign a primary point of contact for streamlined communication
- Utilize their capabilities beyond just fabrication such as design assistance
- Provide feedback to develop the relationship and improve future prototyping engagements
Closely monitoring initial projects builds confidence and alignment between your teams.
Maximizing Prototype Success
By selecting the best-fit service provider and implementing robust processes, you can ensure your prototypes live up to their full potential for accelerating development. Utilizing capabilities beyond fabrication enables creating reliable prototypes – the vital bridge from design concept to high-volume production.
Frequently Asked Questions
What are the main benefits of using a full-service PCB prototype provider?
Key advantages include:
- Faster development through integrated fabrication and assembly
- Leveraging the provider’s component sourcing expertise
- Avoiding hassle of managing multiple vendors
- Accessing engineering resources for design review
- Focusing your team on design rather than production logistics
- Building a partnership for long-term prototyping and low-volume needs
What risks or disadvantages should be considered when using a prototype service?
Potential downsides to weigh:
- Dependence on the provider’s production schedules and priorities
- Possible delays if the partner lacks needed capabilities
- Increased time for complex custom services like procurement
- Lack of control compared to in-house prototyping
- Information security vulnerabilities when sharing confidential data
- Higher cost versus large-scale offshore manufacturing
What aspects of a PCB prototype project should be kept confidential?
Recommended elements to protect:
- Details of proprietary technologies in your design
- Schematics showing key circuit architectures
- PCB layout artwork and layer stackup information
- Bill of materials with vendors and part numbers
- Component placement instructions
- Functional specifications for the product
- Performance parameters like frequency, speed, power levels, etc.
- Any test procedures used to validate the design
What steps can be taken to de-risk transitioning to a new prototype provider?
Useful de-risking strategies:
- Start with simpler, low-priority designs first
- Perform extensive first-article inspections on initial boards
- Pilot lower-quantity batch orders before full-scale commitments
- Verify quality processes and certifications are fully implemented
- Formalize the manufacturing plan including tolerances, test requirements, etc.
- Establish detailed handling procedures for your components and boards
- Stage intentional test failures to confirm robust containment systems
- Scale up from prototype-appropriate to high-volume production methods
What investments make the most sense when trying to optimize prototype cost?
Highest ROI options:
- Additional design reviews to reduce revisions later on
- More comprehensive assembly test coverage through ICT, fixture testing, etc.
- Higher-quality critical components that enable better performance validation
- More capable test equipment to fully exercise the prototypes’ capabilities
- Upgraded shipping/handling to reduce damage rates
- Additional units for field trials, destructive testing, etc. beyond minimal viable prototypes
0 Comments