What is a PCB Shield?
A PCB shield, or protective coating, is a layer of material applied to the surface of a printed circuit board to protect it from environmental factors such as moisture, dust, chemicals, and extreme temperatures. These coatings act as a barrier between the sensitive electronic components and the external environment, preventing damage and ensuring the proper functioning of the circuit.
PCB shields come in various forms, each with its own unique properties and advantages. Some common types of PCB protective coatings include:
- Conformal coatings
- Potting compounds
- Parylene coatings
- Silicone gels
- Acrylic coatings
The Importance of PCB Protection
PCBs are exposed to a wide range of environmental factors that can cause damage and lead to system failures. Some of the most common threats to PCBs include:
-
Moisture: Humidity and condensation can cause corrosion, short circuits, and dendrite growth on PCBs, leading to decreased performance and potential failure.
-
Dust and debris: Airborne particles can settle on PCBs, causing short circuits and interfering with the proper functioning of electronic components.
-
Chemical exposure: PCBs used in industrial settings may be exposed to harsh chemicals, such as solvents, acids, and oils, which can degrade the circuit materials and cause failures.
-
Extreme temperatures: High temperatures can cause thermal stress on PCBs, leading to component failure and reduced lifespan. Low temperatures can cause condensation and freezing, which may damage the circuit.
-
Mechanical stress: Vibrations, shocks, and physical impacts can cause PCB Components to become loose or damaged, resulting in system failures.
By applying a PCB shield, manufacturers can effectively mitigate these threats and ensure the long-term reliability and performance of their electronic devices.
Types of PCB Protective Coatings
1. Conformal Coatings
Conformal coatings are thin, protective layers applied to the surface of a PCB, conforming to its contours and providing a barrier against environmental factors. These coatings are typically applied by dipping, spraying, or brushing, and they can be easily removed for repairs or modifications.
There are several types of conformal coatings, each with its own unique properties:
-
Acrylic: Acrylic coatings offer good moisture and abrasion resistance, as well as easy application and removal. They are commonly used in consumer electronics and general-purpose applications.
-
Silicone: Silicone coatings provide excellent high-temperature resistance and flexibility, making them suitable for applications exposed to thermal cycling and vibrations.
-
Polyurethane: Polyurethane coatings offer superior chemical and abrasion resistance, as well as good dielectric properties. They are often used in automotive and industrial applications.
-
Epoxy: Epoxy coatings provide excellent moisture and chemical resistance, as well as high dielectric strength. They are commonly used in harsh industrial environments and aerospace applications.
Conformal Coating | Advantages | Disadvantages |
---|---|---|
Acrylic | Easy application and removal, good moisture and abrasion resistance | Limited chemical and high-temperature resistance |
Silicone | Excellent high-temperature resistance and flexibility | Difficult to remove, limited chemical resistance |
Polyurethane | Superior chemical and abrasion resistance, good dielectric properties | Requires specialized equipment for application |
Epoxy | Excellent moisture and chemical resistance, high dielectric strength | Difficult to remove, limited flexibility |
2. Potting Compounds
Potting compounds are thick, encapsulating materials that completely surround and protect PCBs and their components. These compounds are typically two-part epoxy or polyurethane resins that are mixed and poured over the circuit, filling all voids and creating a solid, protective layer.
Potting compounds offer several advantages over conformal coatings:
-
Enhanced mechanical protection: Potting compounds provide superior protection against vibrations, shocks, and physical impacts, making them ideal for applications in harsh environments.
-
Improved thermal management: The encapsulating nature of potting compounds helps to dissipate heat more effectively, reducing thermal stress on components and extending the lifespan of the PCB.
-
Increased moisture and chemical resistance: Potting compounds create a complete seal around the PCB, offering excellent protection against moisture, chemicals, and other contaminants.
However, potting compounds also have some disadvantages:
-
Difficult to remove: Once applied, potting compounds are challenging to remove without damaging the PCB, making repairs and modifications more difficult.
-
Increased weight and size: The thick, encapsulating nature of potting compounds can add significant weight and bulk to the PCB Assembly, which may be a concern for some applications.
3. Parylene Coatings
Parylene is a unique, vapor-deposited polymer coating that offers exceptional protection for PCBs. The coating process involves vaporizing a powdered precursor, which then undergoes polymerization and deposits as a thin, conformal film on the surface of the PCB.
Parylene coatings offer several advantages:
-
Uniform coverage: The vapor deposition process ensures that Parylene coatings conform precisely to the contours of the PCB, providing uniform coverage and protection.
-
Excellent dielectric properties: Parylene has a high dielectric strength and low dielectric constant, making it an ideal insulator for electronic applications.
-
Superior chemical and moisture resistance: Parylene coatings are highly resistant to chemicals, solvents, and moisture, providing long-term protection for PCBs in harsh environments.
-
Biocompatibility: Some Parylene variants are biocompatible, making them suitable for use in medical devices and implantable electronics.
Despite these advantages, Parylene coatings also have some drawbacks:
-
High cost: The specialized equipment and materials required for Parylene coating make it one of the most expensive PCB protection methods.
-
Limited reworkability: While Parylene coatings can be removed using specialized techniques, the process is more challenging than with other coating types, making repairs and modifications more difficult.
4. Silicone Gels
Silicone gels are soft, flexible materials that provide a protective cushion for PCBs and their components. These gels are typically two-part, room-temperature vulcanizing (RTV) silicones that are mixed and dispensed over the circuit, forming a compliant, self-healing layer.
Silicone gels offer several benefits:
-
Shock and vibration damping: The soft, compliant nature of silicone gels helps to absorb shocks and vibrations, protecting components from mechanical stress.
-
Thermal cycling resistance: Silicone gels maintain their flexibility over a wide temperature range, making them suitable for applications exposed to thermal cycling.
-
Self-healing properties: If the gel is punctured or torn, it can flow back together and re-seal, maintaining its protective properties.
However, silicone gels also have some limitations:
-
Limited chemical resistance: While silicone gels offer some protection against moisture and mild chemicals, they may degrade when exposed to harsh solvents or acids.
-
Reduced heat dissipation: The insulating nature of silicone gels can inhibit heat transfer from components, which may be a concern for high-power applications.
5. Acrylic Coatings
Acrylic coatings are widely used for PCB protection due to their ease of application, good moisture resistance, and low cost. These coatings are typically applied by spraying or dipping and can be easily removed for repairs or modifications.
Acrylic coatings offer several advantages:
-
Easy application and removal: Acrylic coatings can be applied using simple spraying or dipping techniques and can be easily removed using solvents.
-
Good moisture and abrasion resistance: Acrylic coatings provide effective protection against humidity, condensation, and light abrasion.
-
Cost-effective: Compared to other PCB protection methods, acrylic coatings are relatively inexpensive, making them a popular choice for general-purpose applications.
However, acrylic coatings also have some limitations:
-
Limited chemical resistance: Acrylic coatings may degrade when exposed to harsh chemicals or solvents, reducing their protective properties.
-
Reduced high-temperature performance: Acrylic coatings may soften or degrade at elevated temperatures, making them less suitable for high-temperature applications.
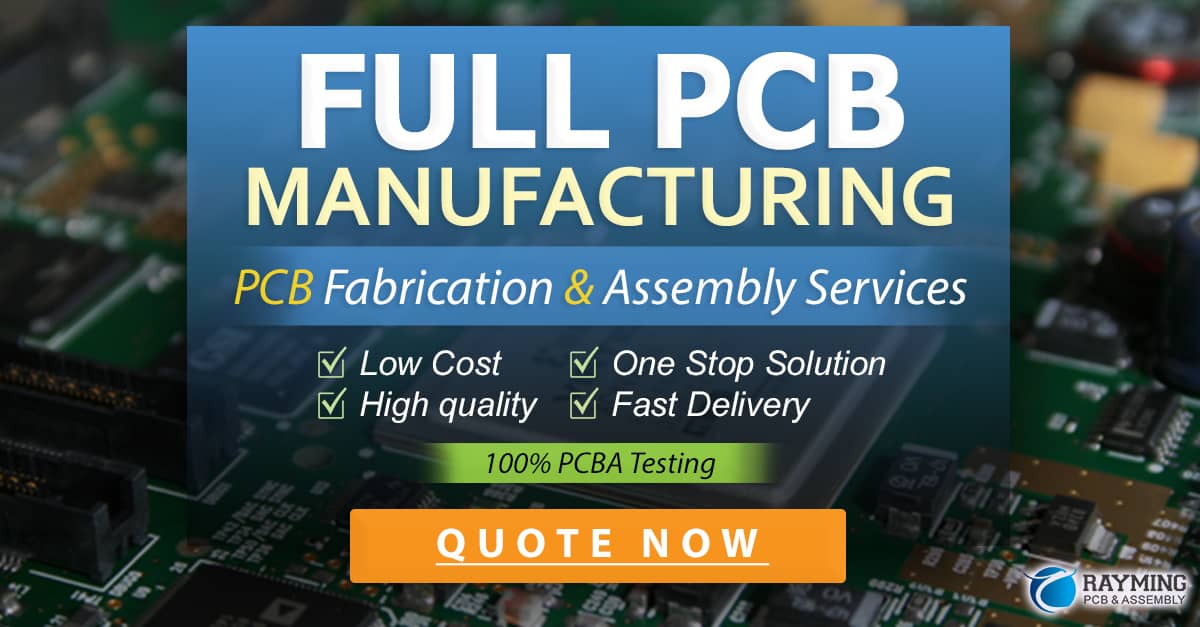
Choosing the Right PCB Shield
When selecting a PCB protective coating, it is essential to consider the specific requirements of your application. Factors to consider include:
-
Environmental conditions: Consider the temperature range, humidity levels, and chemical exposure that your PCB will be subjected to, and choose a coating that offers appropriate protection.
-
Dielectric properties: If your application involves high voltages or sensitive signals, select a coating with high dielectric strength and low dielectric constant to ensure proper insulation and signal integrity.
-
Reworkability: If your PCB may require repairs or modifications in the future, choose a coating that can be easily removed, such as an acrylic or silicone conformal coating.
-
Cost: Evaluate the cost of the coating method in relation to your budget and the expected production volume of your PCBs.
Application | Recommended PCB Shield |
---|---|
Consumer electronics | Acrylic conformal coating |
Automotive and industrial | Polyurethane conformal coating or potting compound |
Aerospace and defense | Epoxy conformal coating or Parylene coating |
Medical devices | Parylene coating or silicone gel |
High-temperature environments | Silicone conformal coating or potting compound |
Applying PCB Protective Coatings
The application process for PCB protective coatings varies depending on the type of coating and the specific requirements of the application. Some general steps include:
-
PCB Cleaning: Before applying any coating, the PCB must be thoroughly cleaned to remove dirt, debris, and contaminants that could interfere with adhesion.
-
Masking: Areas of the PCB that should not be coated, such as connectors or test points, must be masked off using tape or specialized masking materials.
-
Coating application: The chosen coating is applied to the PCB using the appropriate method, such as spraying, dipping, or dispensing.
-
Curing: After application, the coating must be cured to achieve its final properties. Curing methods can include room-temperature curing, heat curing, or UV curing, depending on the coating type.
-
Inspection: Once the coating has cured, the PCB should be inspected for proper coverage, thickness, and any defects that may require rework.
Benefits of PCB Protective Coatings
Applying a PCB shield offers numerous benefits for electronic devices, including:
-
Enhanced reliability: By protecting PCBs from environmental factors that can cause damage, protective coatings help to ensure the long-term reliability and performance of electronic systems.
-
Extended lifespan: PCB shields can significantly extend the lifespan of electronic devices by preventing premature failure due to moisture, chemical exposure, or mechanical stress.
-
Improved signal integrity: Coatings with high dielectric strength and low dielectric constant help to maintain signal integrity and reduce interference in high-frequency applications.
-
Reduced maintenance costs: By preventing damage and extending the lifespan of PCBs, protective coatings can help to reduce maintenance and repair costs over the life of the electronic device.
-
Compliance with industry standards: Many industries, such as automotive, aerospace, and medical, have specific standards for PCB protection. Using appropriate protective coatings can help ensure compliance with these standards and regulations.
FAQ
- What is the difference between a conformal coating and a potting compound?
-
Conformal coatings are thin, protective layers that conform to the contours of the PCB, while potting compounds are thick, encapsulating materials that completely surround and protect the PCB and its components.
-
Can PCB protective coatings be removed for repairs or modifications?
-
Some coatings, such as acrylic and silicone conformal coatings, can be easily removed using solvents. Others, like potting compounds and Parylene coatings, are more difficult to remove and may require specialized techniques.
-
How do I choose the right PCB protective coating for my application?
-
When selecting a PCB protective coating, consider factors such as the environmental conditions, dielectric properties, reworkability, and cost. Consult the table in the “Choosing the Right PCB Shield” section for recommendations based on specific applications.
-
What are the advantages of using Parylene coatings for PCB protection?
-
Parylene coatings offer uniform coverage, excellent dielectric properties, superior chemical and moisture resistance, and biocompatibility. However, they are also more expensive and less reworkable than other coating types.
-
Can PCB protective coatings help with thermal management?
- Some coatings, such as potting compounds, can help with thermal management by dissipating heat more effectively. However, others, like silicone gels, may act as insulators and inhibit heat transfer from components.
Conclusion
PCB protective coatings, or PCB shields, are essential for ensuring the reliability, performance, and longevity of electronic devices. By providing a barrier against environmental factors such as moisture, dust, chemicals, and mechanical stress, these coatings help to prevent damage and extend the lifespan of PCBs.
With a variety of coating types available, including conformal coatings, potting compounds, Parylene, silicone gels, and acrylic coatings, manufacturers can select the most appropriate protection method for their specific application. By considering factors such as environmental conditions, dielectric properties, reworkability, and cost, engineers can design and produce electronic devices that are well-protected and capable of withstanding the challenges of their intended environment.
As electronic systems continue to advance and find new applications in demanding industries, the importance of PCB protective coatings will only continue to grow. By staying informed about the latest developments in PCB shield technology and best practices for application, manufacturers can ensure that their products are reliable, durable, and capable of meeting the evolving needs of their customers.
0 Comments