Introduction to PCB PCBA
PCB PCBA stands for Printed Circuit board assembly and refers to the process of assembling electronic components onto a printed circuit board (PCB) to create a functional electronic device or product. The PCB provides the physical structure and electrical connections between the various components.
PCBA involves several key steps:
- Solder paste application
- Component placement
- Reflow soldering
- Inspection and testing
Once the PCB PCBA process is complete, the assembled board is ready to be integrated into an electronic device or product.
Applications and Devices that Use PCB PCBA
PCB PCBA is used in a wide range of electronic devices and products across various industries. Some common applications include:
Consumer Electronics
- Smartphones
- Tablets
- Laptops
- Televisions
- Gaming consoles
- Wearable devices
Automotive Electronics
- Infotainment systems
- Engine control units (ECUs)
- Advanced driver assistance systems (ADAS)
- Electric vehicle battery management systems
Medical Devices
- Patient monitoring systems
- Diagnostic equipment
- Implantable devices
- Wearable health trackers
Industrial Automation and Control
- Programmable logic controllers (PLCs)
- Human-machine interfaces (HMIs)
- Sensors and transducers
- Motor drives
Aerospace and Defense
- Avionics systems
- Radar and surveillance equipment
- Satellite communications devices
- Military-grade computers and displays
Benefits of PCB PCBA in Electronic Devices
Using PCB PCBA in electronic devices offers several advantages:
-
Miniaturization: PCBs allow for high-density component placement, enabling smaller and more compact devices.
-
Reliability: Properly designed and assembled PCBs provide reliable electrical connections and can withstand harsh environments.
-
Cost-effectiveness: PCB PCBA enables mass production of electronic devices, reducing manufacturing costs.
-
Complexity management: PCBs simplify complex circuits by providing a structured platform for component interconnections.
-
Scalability: PCB designs can be easily modified or scaled up to accommodate new features or increased production volumes.
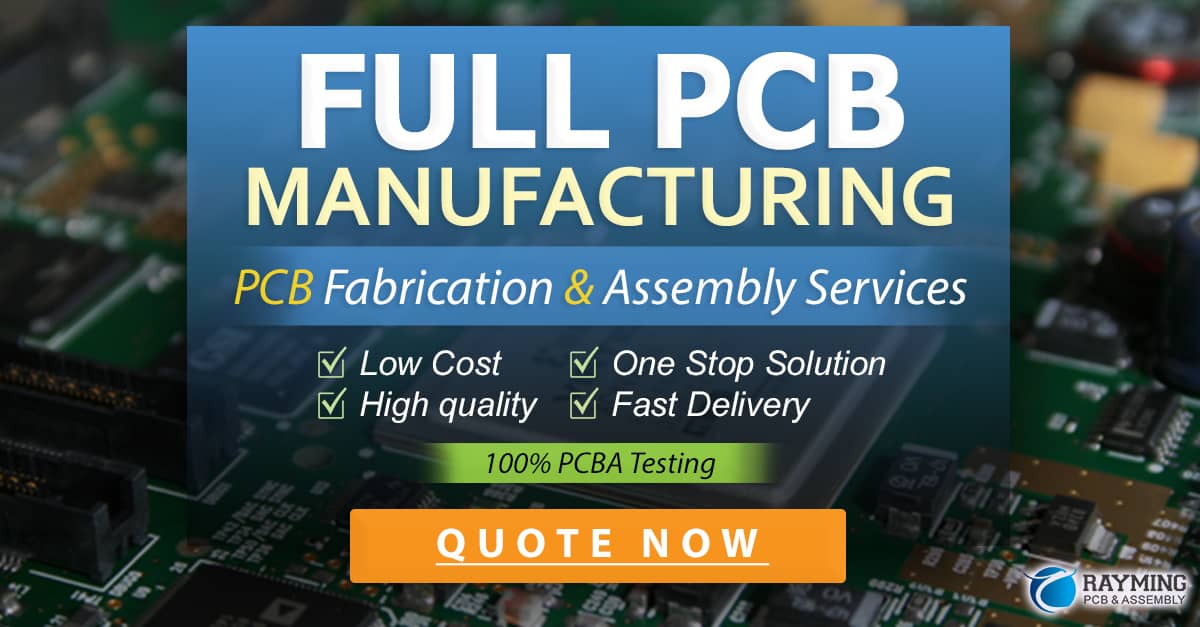
Key Considerations for PCB PCBA Design
When designing a PCB for PCBA, several factors must be considered to ensure optimal performance and manufacturability:
Component Selection
Choose components that are compatible with the PCB fabrication and assembly processes. Consider factors such as package type, size, and thermal requirements.
Layout and Routing
Design the PCB layout to minimize signal interference, ensure proper power distribution, and facilitate efficient assembly. Follow best practices for component placement, trace routing, and grounding.
Manufacturing Constraints
Consider the capabilities and limitations of the PCB fabrication and assembly processes. Adhere to design rules for minimum trace widths, clearances, and drill sizes.
Testability
Incorporate test points and other features that enable efficient testing and debugging of the assembled PCB.
Thermal Management
Ensure proper thermal dissipation to prevent overheating of components. Consider the use of thermal vias, heatsinks, or other cooling methods.
RAYPCB’s PCB PCBA Services
RAYPCB is a leading provider of PCB PCBA services, offering end-to-end solutions for electronic product development and manufacturing. Our services include:
- PCB design and layout
- Component sourcing and procurement
- PCB fabrication
- PCB Assembly (PCBA)
- Testing and quality control
- Box build and final assembly
We work with clients across various industries, including consumer electronics, automotive, medical, industrial, and aerospace. Our state-of-the-art facilities and experienced team ensure high-quality PCB PCBA services with quick turnaround times.
PCB PCBA Industry Trends
The PCB PCBA industry is constantly evolving to keep pace with advancements in electronic devices and technologies. Some notable trends include:
Miniaturization and High-Density Interconnect (HDI)
As electronic devices become smaller and more compact, PCBs must accommodate higher component densities. HDI technologies, such as micro-vias and fine-pitch components, enable the creation of highly miniaturized PCBs.
Flexible and Rigid-Flex PCBs
Flexible and Rigid-Flex PCBs are gaining popularity in applications that require flexibility, durability, or complex form factors. These PCBs can bend, fold, or conform to specific shapes, making them ideal for wearable devices, automotive electronics, and aerospace applications.
Advanced Materials
New PCB materials with improved thermal, electrical, and mechanical properties are being developed to meet the demands of high-performance applications. These materials include low-loss dielectrics, high-temperature laminates, and metal core substrates.
Internet of Things (IoT) and Wireless Connectivity
The proliferation of IoT devices is driving demand for PCBs with integrated wireless connectivity, such as Wi-Fi, Bluetooth, and cellular modules. PCB PCBA plays a crucial role in enabling the development of IoT products.
Sustainable and Eco-Friendly Practices
There is a growing emphasis on sustainable and eco-friendly practices in the PCB PCBA industry. This includes the use of lead-free solders, halogen-free materials, and recycling of electronic waste.
Frequently Asked Questions (FAQ)
1. What is the difference between PCB and PCBA?
PCB refers to the printed circuit board itself, which is the bare board without any components. PCBA, on the other hand, refers to the assembled PCB with all the electronic components soldered onto it.
2. How long does the PCB PCBA process typically take?
The duration of the PCB PCBA process depends on factors such as the complexity of the design, the number of components, and the production volume. Typical lead times can range from a few days to several weeks.
3. What types of components can be used in PCB PCBA?
A wide variety of electronic components can be used in PCB PCBA, including resistors, capacitors, inductors, diodes, transistors, integrated circuits (ICs), connectors, and more. The specific components used depend on the functionality and requirements of the electronic device or product.
4. What are some common challenges in PCB PCBA?
Some common challenges in PCB PCBA include:
- Ensuring proper component placement and orientation
- Managing thermal issues and preventing overheating
- Dealing with electrostatic discharge (ESD) and electromagnetic interference (EMI)
- Achieving high yields and minimizing defects
- Keeping up with rapid technological advancements and changing industry standards
5. How can I ensure the quality and reliability of my PCB PCBA?
To ensure the quality and reliability of your PCB PCBA, consider the following:
- Work with experienced and reputable PCB PCBA service providers like RAYPCB
- Follow best practices for PCB design and layout
- Use high-quality components from trusted suppliers
- Implement strict quality control measures and testing procedures
- Conduct thorough inspections and testing at various stages of the PCBA process
- Continuously monitor and improve your manufacturing processes based on data and feedback
Conclusion
PCB PCBA is a crucial process in the development and manufacturing of electronic devices and products. It enables the creation of highly functional, reliable, and cost-effective electronics across a wide range of industries and applications.
As the demand for more advanced and miniaturized electronic devices continues to grow, the PCB PCBA industry must adapt and innovate to keep pace with these evolving requirements. This involves adopting new technologies, materials, and manufacturing processes to deliver high-quality PCB PCBA services.
RAYPCB is at the forefront of these developments, providing comprehensive PCB PCBA solutions to clients worldwide. With our state-of-the-art facilities, experienced team, and commitment to quality, we are well-positioned to support the growing needs of the electronics industry.
Tables
Common PCB Materials
Material | Description | Applications |
---|---|---|
FR-4 | Glass-reinforced epoxy laminate | General-purpose PCBs |
Rogers | High-frequency laminates | RF and microwave applications |
Polyimide | Flexible polymer film | Flexible and rigid-flex PCBs |
Aluminum | Metal core substrate | High-power LED lighting |
PCB PCBA Defects and Causes
Defect | Cause | Prevention |
---|---|---|
Solder bridge | Excessive solder, incorrect component placement | Proper solder paste application, accurate component placement |
Cold solder joint | Insufficient heat, poor solder wetting | Optimized reflow soldering profile, clean PCB surfaces |
Component misalignment | Inaccurate pick-and-place machine setup | Regular machine calibration, visual inspection |
Tombstoning | Uneven heating, component imbalance | Balanced component placement, controlled reflow process |
I hope this article provides a comprehensive overview of PCB PCBA-Devices and their applications. If you have any further questions or require assistance with your PCB PCBA needs, please don’t hesitate to contact RAYPCB.
0 Comments