Types of PCB Manufacturing Equipment
1. PCB Fabrication Equipment
1.1 PCB Printing Equipment
PCB printing equipment is used to transfer the circuit design onto the copper-clad board. There are several types of PCB printing equipment, including:
- Screen Printing Machines
- Inkjet Printers
- Laser Printers
Printing Equipment | Advantages | Disadvantages |
---|---|---|
Screen Printing Machines | – High precision – Cost-effective for large production runs |
– Requires stencils – Not suitable for complex designs |
Inkjet Printers | – Versatile – Suitable for small production runs |
– Lower resolution compared to other methods – Ink can be expensive |
Laser Printers | – High resolution – Suitable for complex designs |
– Expensive – Not cost-effective for large production runs |
1.2 PCB Etching Equipment
PCB etching equipment is used to remove the unwanted copper from the board, leaving only the desired circuit pattern. The most common types of PCB etching equipment are:
- Spray Etchers
- Bubble Etchers
- Conveyorized Etchers
Etching Equipment | Advantages | Disadvantages |
---|---|---|
Spray Etchers | – Uniform etching – Suitable for double-sided boards |
– Higher equipment cost – Requires regular maintenance |
Bubble Etchers | – Low equipment cost – Easy to maintain |
– Non-uniform etching – Not suitable for double-sided boards |
Conveyorized Etchers | – High throughput – Uniform etching |
– Expensive – Requires more floor space |
1.3 PCB Drilling Equipment
PCB drilling equipment is used to create holes in the board for component leads and vias. The most common types of PCB drilling equipment are:
- Manual Drill Presses
- CNC Drilling Machines
- Laser Drilling Machines
Drilling Equipment | Advantages | Disadvantages |
---|---|---|
Manual Drill Presses | – Low equipment cost – Suitable for small production runs |
– Slower than automated methods – Requires skilled operators |
CNC Drilling Machines | – High precision – High throughput |
– Expensive – Requires programming skills |
Laser Drilling Machines | – Suitable for micro-vias – No wear on tools |
– Very expensive – Limited to certain materials |
2. PCB Assembly Equipment
2.1 Pick and Place Machines
Pick and place machines are used to automatically place electronic components onto the PCB. They come in various types, such as:
- Chip Shooters
- Fine Pitch Placement Machines
- Multi-Function Placement Machines
Pick and Place Machines | Advantages | Disadvantages |
---|---|---|
Chip Shooters | – High speed – Suitable for simple components |
– Limited component range – Not suitable for fine-pitch components |
Fine Pitch Placement Machines | – High precision – Suitable for fine-pitch components |
– Slower than chip shooters – More expensive |
Multi-Function Placement Machines | – Versatile – Can handle a wide range of components |
– Higher equipment cost – Requires more setup time |
2.2 Soldering Equipment
Soldering equipment is used to create permanent electrical connections between components and the PCB. The most common types of soldering equipment are:
- Wave Soldering Machines
- Reflow Ovens
- Selective Soldering Machines
Soldering Equipment | Advantages | Disadvantages |
---|---|---|
Wave Soldering Machines | – High throughput – Suitable for through-hole components |
– Not suitable for SMD components – Can cause thermal stress on components |
Reflow Ovens | – Suitable for SMD components – Uniform heating |
– Not suitable for through-hole components – Requires precise temperature control |
Selective Soldering Machines | – Suitable for mixed-technology boards – Localized heating |
– Slower than other methods – More expensive |
2.3 Inspection Equipment
Inspection equipment is used to ensure the quality and reliability of the assembLED PCBs. The most common types of inspection equipment are:
- Automated Optical Inspection (AOI) Machines
- X-Ray Inspection Machines
- In-Circuit Testing (ICT) Equipment
Inspection Equipment | Advantages | Disadvantages |
---|---|---|
AOI Machines | – High-speed inspection – Detects surface defects |
– Cannot detect hidden defects – Requires programming |
X-Ray Inspection Machines | – Detects hidden defects – Suitable for complex assemblies |
– Expensive – Requires skilled operators |
ICT Equipment | – Tests functionality of components – Detects shorts and opens |
– Requires test fixture development – Can be time-consuming |
Importance of PCB Manufacturing Equipment
PCB manufacturing equipment plays a crucial role in the production of high-quality, reliable PCBs. The right equipment ensures:
-
Consistency: Automated equipment helps maintain consistent quality across production runs, reducing the risk of human error.
-
Efficiency: Advanced PCB manufacturing equipment enables faster production times, increasing overall throughput and reducing lead times.
-
Precision: High-precision equipment allows for the fabrication of complex, high-density PCBs with tight tolerances.
-
Cost-effectiveness: Investing in the right PCB manufacturing equipment can reduce labor costs, minimize waste, and improve overall production efficiency, resulting in lower production costs.
Value of PCB Manufacturing Equipment
The value of PCB manufacturing equipment extends beyond the production process itself. Investing in the right equipment can provide long-term benefits for electronics manufacturing businesses, such as:
-
Competitive advantage: High-quality PCB manufacturing equipment enables businesses to produce superior products, giving them an edge over competitors.
-
Expanded capabilities: Advanced equipment allows businesses to take on more complex projects and cater to a wider range of customer requirements.
-
Increased profitability: Efficient and precise PCB manufacturing equipment can help reduce production costs and increase profit margins.
-
Future-proofing: Investing in modern PCB manufacturing equipment ensures that businesses can adapt to evolving industry standards and customer demands.
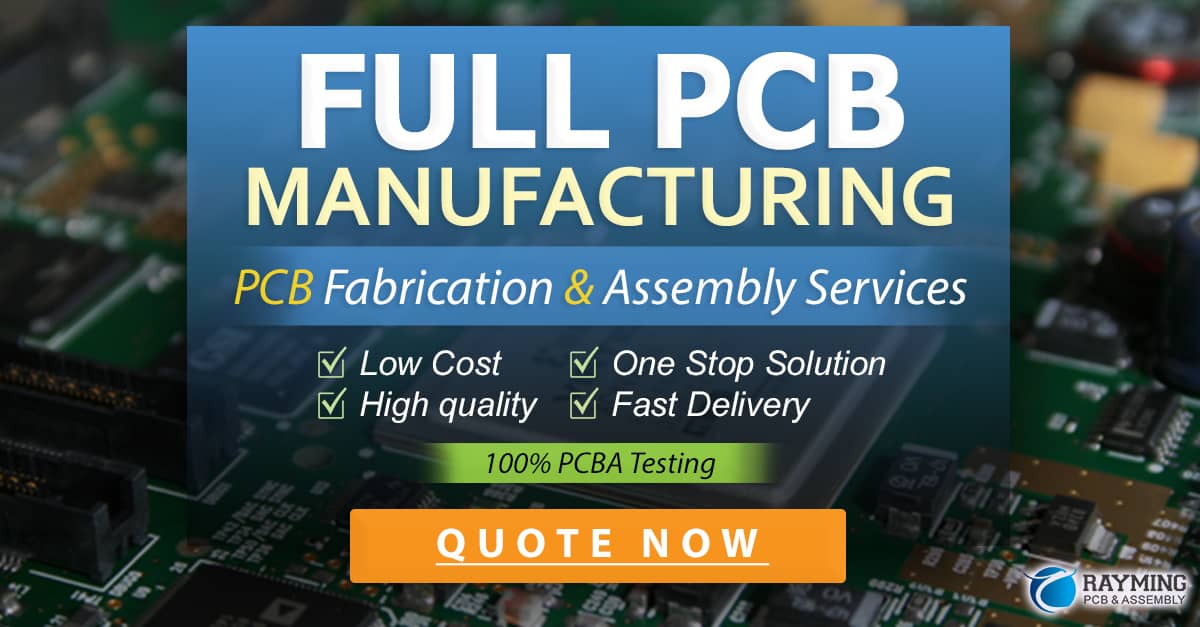
FAQ
- What is the most important factor to consider when selecting PCB manufacturing equipment?
-
The most important factor to consider is the specific requirements of your PCB production process, such as the complexity of the designs, the required throughput, and the target market for your products.
-
How often should PCB manufacturing equipment be maintained?
-
The maintenance frequency depends on the specific equipment and its usage. Generally, it is recommended to follow the manufacturer’s guidelines and establish a regular maintenance schedule to ensure optimal performance and longevity.
-
What are the benefits of investing in automated PCB manufacturing equipment?
-
Automated PCB manufacturing equipment offers several benefits, including increased consistency, higher throughput, improved precision, and reduced labor costs. It also enables businesses to take on more complex projects and remain competitive in the market.
-
Can small-scale electronics manufacturing businesses afford advanced PCB manufacturing equipment?
-
While advanced PCB manufacturing equipment can be expensive, there are options available for small-scale businesses, such as leasing or purchasing used equipment. It is essential to carefully evaluate the business’s needs and budget before making a decision.
-
How can businesses ensure they are getting the best value for their investment in PCB manufacturing equipment?
- To ensure the best value for their investment, businesses should research and compare different equipment options, consider the long-term benefits and potential return on investment, and choose reputable suppliers that offer comprehensive support and training.
In conclusion, PCB manufacturing equipment is an essential and valuable asset for any electronics manufacturing business. By understanding the various types of equipment available and their importance in the production process, businesses can make informed decisions when investing in PCB manufacturing equipment. The right equipment can provide a competitive edge, expand capabilities, increase profitability, and future-proof the business in an ever-evolving industry.
0 Comments