1. Component Placement
1.1 Grouping Components
When placing components on your PCB, it’s essential to group them based on their functionality and interconnectivity. This approach helps minimize the length of traces and reduces the risk of signal interference. For example, keep analog and digital components separated to avoid noise coupling.
1.2 Orientat ion and Spacing
Consider the orientation and spacing of components to ensure proper heat dissipation and ease of assembly. Align components in the same direction whenever possible to simplify the assembly process. Maintain adequate spacing between components to allow for proper soldering and to prevent short circuits.
Component Type | Minimum Spacing |
---|---|
Resistors | 0.5 mm |
Capacitors | 0.8 mm |
ICs | 1.0 mm |
1.3 Placement for Manufacturability
When placing components, keep in mind the manufacturability of your PCB. Avoid placing components too close to the board edges or in areas that are difficult to access during the assembly process. Consider the size and shape of the components to ensure they fit properly on the board.
2. Routing and Trace Width
2.1 Signal Integrity
Proper routing is crucial for maintaining signal integrity. Keep trace lengths as short as possible to minimize signal distortion and attenuation. Use appropriate trace widths based on the current carrying capacity and the desired impedance of the signal.
Signal Type | Recommended Trace Width |
---|---|
Power traces | 0.5 mm – 1.0 mm |
Signal traces | 0.2 mm – 0.4 mm |
High-speed traces | 0.1 mm – 0.2 mm |
2.2 Crosstalk and EMI
To minimize crosstalk and electromagnetic interference (EMI), route sensitive traces away from noisy traces and components. Use ground planes and proper shielding techniques to reduce EMI. Consider using differential pairs for high-speed signals to cancel out electromagnetic fields.
2.3 Trace Corners and Angles
When routing traces, avoid sharp corners and acute angles. Use 45-degree angles or rounded corners to prevent signal reflections and improve manufacturability. Sharp corners can cause Acid Traps during the etching process, leading to open circuits or signal integrity issues.
3. Grounding and Power Distribution
3.1 Ground Planes
Use solid ground planes whenever possible to provide a low-impedance return path for signals and to reduce EMI. In multi-layer boards, dedicate one or more layers to ground planes. Connect components to the ground plane using short traces or vias to minimize ground loops and improve signal integrity.
3.2 Power Distribution
Design a robust power distribution network to ensure stable and clean power supply to all components. Use wide traces or power planes to minimize voltage drops and power supply noise. Decouple power supplies using appropriate capacitors near the power pins of ICs to suppress high-frequency noise.
Component | Recommended Decoupling Capacitor |
---|---|
Digital ICs | 0.1 μF ceramic capacitor |
Analog ICs | 1 μF – 10 μF tantalum capacitor |
Power modules | 100 μF – 1000 μF electrolytic capacitor |
3.3 Analog and Digital Grounding
Separate analog and digital ground planes to prevent noise coupling between the two domains. Use a single point ground connection or a star grounding technique to connect the analog and digital grounds. This approach helps minimize ground loops and ensures a clean reference for both analog and digital signals.
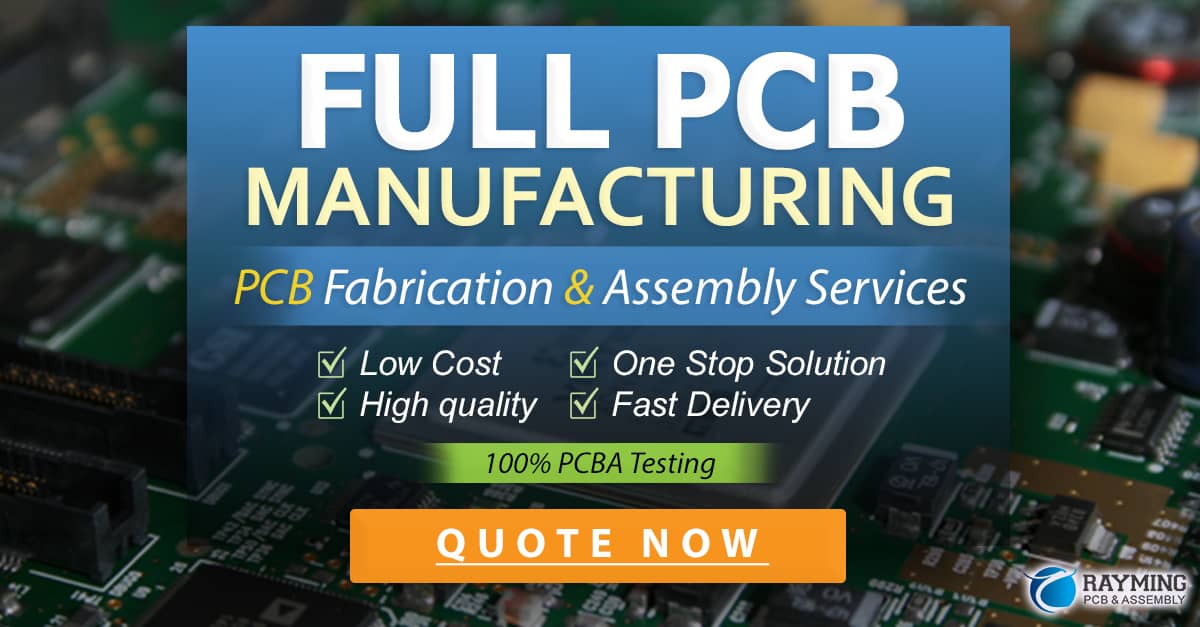
4. Thermal Management
4.1 Heat Dissipation
Consider the thermal requirements of your components and design the PCB Layout accordingly. Provide adequate copper area for heat dissipation, especially for power-hungry components like voltage regulators and power transistors. Use thermal vias to transfer heat from components to the ground plane or dedicated thermal layers.
4.2 Component Placement for Thermal Management
Place temperature-sensitive components away from heat-generating components to prevent thermal interference. Ensure proper airflow around components that require cooling. Consider using heatsinks or thermal pads for components with high heat dissipation requirements.
4.3 Thermal Relief
Use thermal relief pads for components with large copper areas to prevent solder joint issues during the reflow process. Thermal relief pads reduce the thermal mass connected to the component, allowing for proper solder joint formation and preventing component lifting or tombstoning.
5. Design for Manufacturing (DFM)
5.1 Board Dimensions and Panelization
Consider the standard board sizes and panelization requirements when designing your PCB. Choose board dimensions that optimize material usage and minimize waste. Use panelization techniques like tab routing or v-scoring to facilitate the separation of individual boards after fabrication.
5.2 Solder Mask and Silkscreen
Use solder mask to protect traces and prevent short circuits. Ensure adequate solder mask clearance around pads to allow for proper soldering. Include silkscreen labels for components and important information to aid in assembly and debugging.
5.3 Fiducial Marks and Assembly Points
Include fiducial marks on your PCB to assist in automated assembly processes. Fiducial marks provide reference points for pick-and-place machines to accurately position components. Use assembly points or tooling holes to secure the board during the assembly process.
6. Testing and Debugging
6.1 Test Points
Include test points on your PCB to facilitate testing and debugging. Place test points at critical nodes or signals that require probing or measurement. Use appropriate test point sizes and spacing to allow for easy access with test probes or connectors.
6.2 Debugging Features
Consider including debugging features like LED indicators, jumpers, or switches to aid in troubleshooting and system verification. These features can help isolate issues and provide visual feedback during the debugging process.
6.3 Boundary Scan and JTAG
For complex designs, consider implementing boundary scan or JTAG (Joint Test Action Group) testing capabilities. These techniques allow for automated testing and debugging of the PCB, reducing the time and effort required for manual probing and measurement.
Frequently Asked Questions (FAQ)
1. What is the importance of component placement in PCB layout?
Proper component placement is crucial for several reasons:
– It helps minimize trace lengths and reduces signal interference.
– It ensures proper heat dissipation and prevents thermal issues.
– It simplifies the assembly process and improves manufacturability.
2. How can I minimize crosstalk and EMI in my PCB layout?
To minimize crosstalk and EMI, consider the following techniques:
– Route sensitive traces away from noisy traces and components.
– Use ground planes and proper shielding techniques.
– Consider using differential pairs for high-speed signals.
3. What is the purpose of ground planes in PCB layout?
Ground planes serve several purposes in PCB layout:
– They provide a low-impedance return path for signals.
– They reduce electromagnetic interference (EMI).
– They help improve signal integrity and minimize ground loops.
4. How can I ensure proper thermal management in my PCB layout?
To ensure proper thermal management, consider the following:
– Provide adequate copper area for heat dissipation, especially for power-hungry components.
– Use thermal vias to transfer heat from components to the ground plane or dedicated thermal layers.
– Place temperature-sensitive components away from heat-generating components.
5. What are some important considerations for Design for Manufacturing (DFM)?
When designing for manufacturing, consider the following:
– Choose board dimensions that optimize material usage and minimize waste.
– Use panelization techniques like tab routing or v-scoring for easy separation of individual boards.
– Include solder mask and silkscreen labels for protection and assembly assistance.
– Use fiducial marks and assembly points to aid in automated assembly processes.
Conclusion
Designing a PCB layout requires careful consideration of various factors to ensure optimal performance, reliability, and manufacturability. By focusing on component placement, routing and trace width, grounding and power distribution, thermal management, Design for Manufacturing (DFM), and testing and debugging, you can create a well-designed PCB that meets your specific requirements.
Remember to keep signal integrity, crosstalk, and EMI in mind when routing traces, and use appropriate techniques like ground planes and shielding to mitigate these issues. Proper component placement and thermal management are essential for preventing thermal problems and ensuring reliable operation.
Incorporating DFM principles and including features for testing and debugging will streamline the manufacturing process and make it easier to identify and resolve any issues that may arise.
By following these guidelines and considering the six important things discussed in this article, you can create a PCB layout that not only functions as intended but also optimizes cost, reliability, and manufacturing efficiency.
0 Comments