What is an Acid Trap?
An acid trap is a small, intentionally designed feature on a PCB that serves as a reservoir for excess acid during the etching process. It is typically located in areas where traces or copper planes are more likely to trap or hold onto acid, such as in corners, narrow spaces, or around densely populated components.
Purpose of Acid Traps
The primary purpose of an acid trap is to prevent the accumulation of acid in specific areas of the PCB during the etching process. When a PCB is exposed to the etching solution, the acid removes the unwanted copper, leaving behind the desired traces and components. However, if the acid is not properly removed or if it gets trapped in certain areas, it can lead to several issues:
-
Over-etching: Trapped acid can continue to etch the copper, resulting in the thinning or complete removal of traces, potentially causing open circuits or reduced current-carrying capacity.
-
Undercutting: Acid that is not effectively removed can etch the sides of the traces, leading to a phenomenon called undercutting. This can weaken the mechanical strength of the traces and affect the overall reliability of the PCB.
-
Contamination: Residual acid left on the PCB can cause contamination, leading to corrosion, reduced solderability, and other quality issues.
By incorporating acid traps into the PCB design, manufacturers can mitigate these problems and ensure a higher-quality end product.
Designing Acid Traps
Designing effective acid traps requires careful consideration of various factors, such as the PCB layout, etching process, and manufacturing capabilities. Here are some key aspects to consider when designing acid traps:
Location
Acid traps should be strategically placed in areas where acid is most likely to accumulate. These locations include:
- Corners and intersections of traces
- Narrow spaces between traces or components
- Areas with high component density
- Regions with large copper planes
By identifying these critical areas and incorporating acid traps, designers can minimize the risk of acid entrapment and its associated issues.
Size and Shape
The size and shape of acid traps can vary depending on the specific requirements of the PCB design and the manufacturing process. However, there are some general guidelines to follow:
- Acid traps should be large enough to accommodate the expected amount of excess acid without causing interference with nearby traces or components.
- The shape of the acid trap should promote easy drainage of the acid during the etching process. Common shapes include circles, teardrops, and triangles.
- The dimensions of the acid trap should be consistent with the manufacturing capabilities and tolerances of the PCB fabrication facility.
Shape | Advantage | Disadvantage |
---|---|---|
Circle | Easy to manufacture, promotes uniform acid drainage | May require more space compared to other shapes |
Teardrop | Facilitates smooth acid flow, reduces stress concentration | More complex to design and manufacture |
Triangle | Space-efficient, promotes acid drainage in corners | May create sharp edges that can concentrate stress |
Connection to Traces
Acid traps should be connected to the adjacent traces or copper planes to ensure proper acid drainage. The connection can be made through a narrow neck or a small trace, depending on the design requirements. It is important to ensure that the connection does not create any additional acid entrapment points or compromise the integrity of the traces.
Spacing and Clearance
When placing acid traps, designers must consider the spacing and clearance requirements between the traps and other features on the PCB. Adequate spacing helps prevent unintended connections or short circuits, while sufficient clearance ensures that the acid traps do not interfere with the placement of components or the routing of traces.
Impact on PCB Manufacturing
The inclusion of acid traps in a PCB design has several implications for the manufacturing process:
Etching Process
Acid traps play a crucial role during the etching stage of PCB fabrication. As the PCB is exposed to the etching solution, the acid traps collect and drain away the excess acid, preventing it from accumulating in unwanted areas. This helps ensure a more uniform and controlled etching process, resulting in better trace definition and reduced risk of over-etching or undercutting.
Quality Control
The presence of well-designed acid traps contributes to the overall quality of the manufactured PCB. By minimizing the occurrence of acid entrapment-related issues, such as open circuits, weakened traces, and contamination, acid traps help maintain the integrity and reliability of the final product. This, in turn, reduces the need for rework or scrap, ultimately saving time and costs in the manufacturing process.
Design for Manufacturing (DFM)
Incorporating acid traps is an essential aspect of Design for Manufacturing (DFM) principles in PCB design. DFM aims to optimize the design to ensure efficient and cost-effective manufacturing. By considering the placement, size, shape, and connection of acid traps early in the design phase, designers can create PCBs that are more easily manufacturable, reducing the likelihood of production issues and delays.
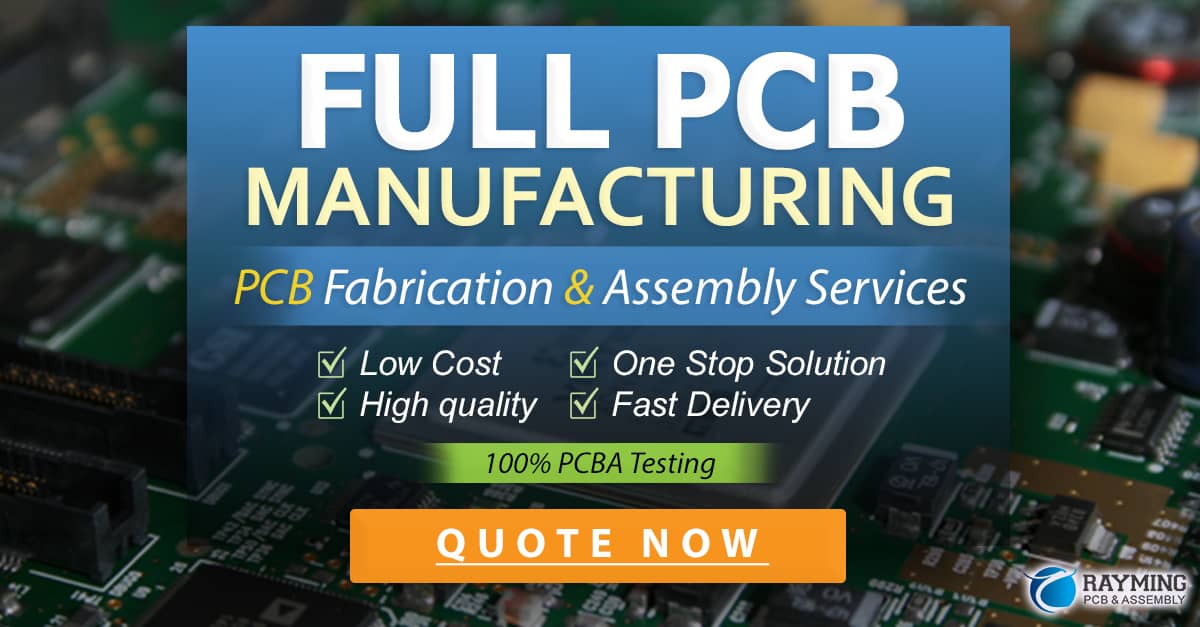
Frequently Asked Questions (FAQ)
-
What happens if acid traps are not included in a PCB design?
If acid traps are not included in a PCB design, there is a higher risk of acid accumulation in certain areas during the etching process. This can lead to over-etching, undercutting, and contamination, which can compromise the quality and reliability of the final product. -
Are acid traps necessary for all PCB designs?
While acid traps are generally recommended for most PCB designs, their necessity may vary depending on factors such as the complexity of the layout, the etching process used, and the specific manufacturing requirements. In some cases, simpler designs with wider trace spacing and fewer dense areas may not require acid traps. However, it is always advisable to consult with the PCB manufacturer and follow their guidelines. -
Can acid traps be added after the initial PCB design is complete?
It is possible to add acid traps after the initial PCB design is complete, but it may require significant modifications to the layout. Adding acid traps retrospectively can be time-consuming and may impact other aspects of the design, such as trace routing and component placement. It is best to incorporate acid traps early in the design process to avoid potential issues and delays. -
How do I determine the appropriate size and shape of acid traps for my PCB design?
The size and shape of acid traps depend on various factors, including the PCB layout, etching process, and manufacturing capabilities. As a general guideline, acid traps should be large enough to accommodate the expected amount of excess acid without interfering with nearby traces or components. The shape should promote easy acid drainage, with common options being circles, teardrops, and triangles. It is recommended to consult with the PCB manufacturer and adhere to their specific guidelines and requirements. -
Are there any drawbacks to using acid traps in PCB design?
While acid traps offer significant benefits in terms of quality and reliability, there are a few potential drawbacks to consider. Firstly, incorporating acid traps may slightly increase the overall size of the PCB, as they require additional space. Secondly, designing and placing acid traps adds complexity to the PCB layout process, which may increase design time and effort. However, the advantages of using acid traps often outweigh these minor drawbacks, particularly for designs with high reliability requirements.
Conclusion
Acid traps are a critical feature in the design and fabrication of printed circuit boards. By providing a reservoir for excess acid during the etching process, acid traps help prevent issues such as over-etching, undercutting, and contamination, ultimately ensuring the quality and reliability of the final product.
Designing effective acid traps requires careful consideration of factors such as location, size, shape, and connection to traces. By incorporating acid traps into the PCB design and following Design for Manufacturing principles, designers can create PCBs that are more easily manufacturable and less prone to production issues.
As PCB designs continue to evolve and become more complex, the importance of acid traps in ensuring the integrity and reliability of these essential components will only continue to grow. By understanding the role of acid traps and implementing them effectively in PCB designs, manufacturers can deliver high-quality products that meet the ever-increasing demands of today’s electronics industry.
0 Comments