Introduction to PCB insulation
Printed Circuit Boards (PCBs) are essential components in modern electronics, providing a platform for interconnecting electrical components. To ensure proper functionality and prevent short circuits, PCBs require insulation between the conductive layers and traces. PCB insulation refers to the non-conductive materials used to separate and protect the electrical pathways on the board.
In this comprehensive article, we will explore the various aspects of PCB insulation, including the types of insulating materials, their properties, and their applications in different PCB designs. We will also discuss the importance of proper insulation and the factors to consider when selecting insulating materials for your PCB projects.
The Importance of PCB Insulation
PCB insulation plays a crucial role in the overall performance and reliability of electronic devices. Here are some key reasons why proper insulation is essential:
-
Preventing Short Circuits: Insulating materials prevent unintended electrical connections between conductive traces, components, and layers. This helps avoid short circuits that can damage components or cause system failures.
-
Electrical Isolation: PCB insulation provides electrical isolation between different sections of the board, allowing for the separation of high and low voltage areas, as well as the isolation of sensitive circuits from sources of interference.
-
Signal Integrity: Proper insulation helps maintain signal integrity by reducing crosstalk and electromagnetic interference (EMI) between adjacent traces or layers. This is particularly important in high-speed and high-frequency applications.
-
Mechanical Support: Insulating materials not only provide electrical isolation but also offer mechanical support to the PCB structure. They help maintain the stability and durability of the board, especially in harsh environments or under physical stress.
-
Thermal Management: Some insulating materials possess thermal properties that aid in heat dissipation, preventing components from overheating and ensuring optimal performance.
Types of PCB Insulating Materials
Various insulating materials are used in PCB manufacturing, each with its own unique properties and advantages. Here are some commonly used PCB insulating materials:
FR-4 (Flame Retardant 4)
FR-4 is the most widely used PCB substrate material. It is a composite material made of woven fiberglass cloth impregnated with an epoxy resin. FR-4 offers excellent mechanical strength, dimensional stability, and good electrical insulation properties. It is also flame retardant, making it suitable for a wide range of applications.
Property | Value |
---|---|
Dielectric Constant (1 MHz) | 4.5 – 4.7 |
Dielectric Strength | 50 – 60 kV/mm |
Thermal Conductivity | 0.2 – 0.3 W/m·K |
Glass Transition Temperature | 130 – 140 °C |
Polyimide
Polyimide is a high-performance polymer known for its excellent thermal stability, chemical resistance, and mechanical properties. It is commonly used in flexible PCBs and applications that require high temperature resistance. Polyimide has a higher dielectric constant compared to FR-4 but offers superior insulation properties.
Property | Value |
---|---|
Dielectric Constant (1 MHz) | 3.2 – 3.5 |
Dielectric Strength | 200 – 300 kV/mm |
Thermal Conductivity | 0.1 – 0.2 W/m·K |
Glass Transition Temperature | 360 – 410 °C |
Teflon (PTFE)
Teflon, or polytetrafluoroethylene (PTFE), is a fluoropolymer known for its low dielectric constant, low dissipation factor, and excellent chemical resistance. It is commonly used in high-frequency applications, such as RF and microwave circuits, due to its superior electrical properties. Teflon is also known for its non-stick and hydrophobic properties.
Property | Value |
---|---|
Dielectric Constant (1 MHz) | 2.0 – 2.1 |
Dielectric Strength | 60 – 170 kV/mm |
Thermal Conductivity | 0.2 – 0.3 W/m·K |
Glass Transition Temperature | 117 – 130 °C |
Rogers Materials
Rogers Corporation offers a range of high-performance PCB insulating materials, such as RO4000 series, RO3000 series, and RT/duroid. These materials are known for their excellent high-frequency performance, low dielectric loss, and controlled dielectric constant. They are widely used in RF, microwave, and millimeter-wave applications.
Material | Dielectric Constant (10 GHz) | Dissipation Factor (10 GHz) |
---|---|---|
RO4350B | 3.48 | 0.0037 |
RO3006 | 6.15 | 0.0020 |
RT/duroid 5880 | 2.20 | 0.0009 |
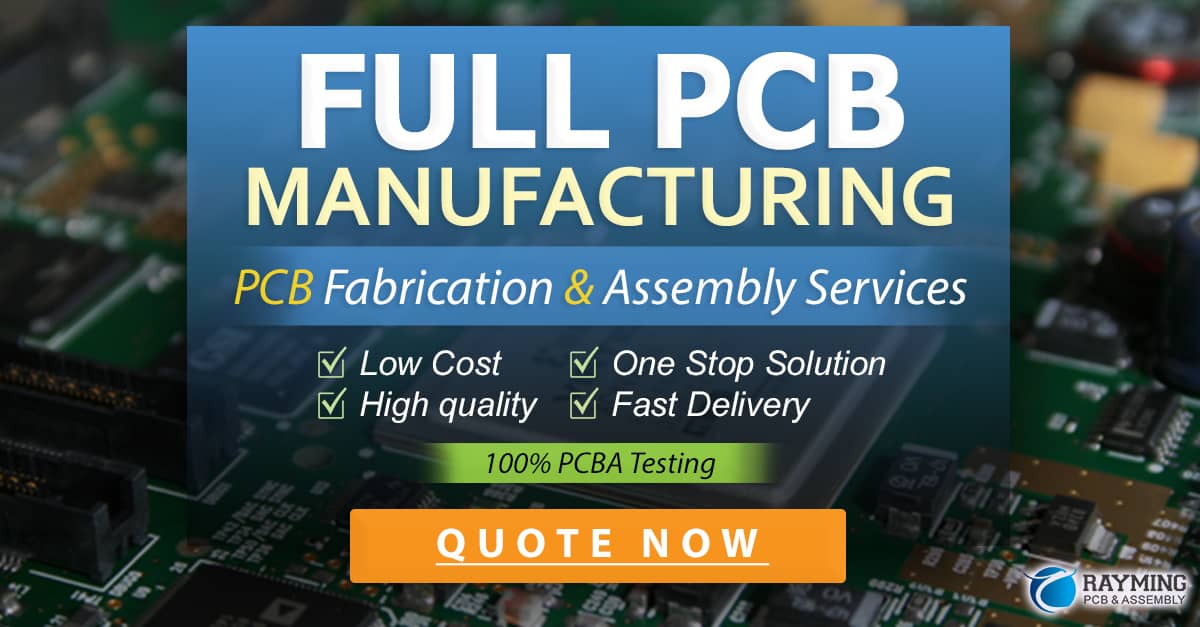
Factors to Consider When Selecting PCB Insulating Materials
When choosing insulating materials for your PCB design, several factors should be taken into account:
-
Dielectric Constant: The dielectric constant (Dk) of a material determines its ability to store electrical energy. A lower Dk is preferred for high-speed and high-frequency applications to minimize signal propagation delay and reduce capacitive coupling between traces.
-
Dissipation Factor: The dissipation factor (Df) represents the amount of energy lost as heat in the insulating material. A lower Df is desirable to minimize signal loss and maintain signal integrity, especially at high frequencies.
-
Thermal Properties: Consider the thermal conductivity and glass transition temperature (Tg) of the insulating material. Higher thermal conductivity helps in heat dissipation, while a higher Tg indicates better thermal stability and resistance to deformation at elevated temperatures.
-
Mechanical Strength: The insulating material should provide adequate mechanical support to the PCB structure. Factors such as tensile strength, flexural strength, and dimensional stability should be considered based on the specific application requirements.
-
Chemical Resistance: In certain environments, the PCB may be exposed to chemicals, solvents, or moisture. Select an insulating material that offers good chemical resistance to ensure long-term reliability.
-
Cost and Availability: The cost and availability of the insulating material should be taken into account, especially for large-scale production. Some high-performance materials may have higher costs or limited availability compared to standard materials like FR-4.
Applications of PCB Insulation
PCB insulation finds applications in various industries and electronic products. Here are some common applications:
-
Consumer Electronics: PCB insulation is essential in consumer electronics, such as smartphones, tablets, laptops, and home appliances. Proper insulation ensures reliable operation and prevents short circuits in these devices.
-
Automotive Electronics: In the automotive industry, PCBs are used in various systems, including engine control units, infotainment systems, and advanced driver assistance systems (ADAS). PCB insulation plays a critical role in ensuring the reliable functioning of these systems in harsh automotive environments.
-
Industrial Electronics: Industrial applications often require PCBs to operate in challenging conditions, such as high temperatures, vibrations, and exposure to chemicals. Selecting appropriate insulating materials is crucial for the durability and reliability of industrial electronic systems.
-
Medical Devices: PCBs are used in medical devices, such as patient monitors, diagnostic equipment, and implantable devices. Insulation is critical in these applications to ensure patient safety and prevent electrical hazards.
-
Aerospace and Defense: In aerospace and defense applications, PCBs are subjected to extreme environmental conditions, including high altitudes, temperature fluctuations, and vibrations. High-performance insulating materials, such as polyimide or PTFE, are often used to meet the stringent requirements of these applications.
FAQ
1. What is the most commonly used PCB insulating material?
The most commonly used PCB insulating material is FR-4 (Flame Retardant 4). It is a composite material made of woven fiberglass cloth impregnated with an epoxy resin. FR-4 offers a good balance of electrical, mechanical, and thermal properties, making it suitable for a wide range of applications.
2. Can PCB insulation materials affect signal integrity?
Yes, PCB insulation materials can affect signal integrity. The dielectric constant and dissipation factor of the insulating material influence signal propagation and loss. Materials with lower dielectric constant and dissipation factor are preferred for high-speed and high-frequency applications to minimize signal distortion and maintain signal integrity.
3. How does the glass transition temperature (Tg) of an insulating material impact PCB performance?
The glass transition temperature (Tg) is the temperature at which the insulating material transitions from a rigid, glassy state to a softer, rubbery state. A higher Tg indicates better thermal stability and resistance to deformation at elevated temperatures. PCBs with insulating materials having a higher Tg are less likely to experience issues like warping or delamination when exposed to high temperatures during operation or manufacturing processes.
4. Are there any special considerations for insulating materials in flexible PCBs?
Flexible PCBs require insulating materials that can withstand repeated bending and flexing without cracking or losing their insulating properties. Polyimide is a common choice for flexible PCBs due to its excellent mechanical flexibility, high temperature resistance, and good electrical insulation properties. Other flexible insulating materials, such as polyester or polyethylene naphthalate (PEN), may also be used depending on the specific requirements of the application.
5. How can I select the right insulating material for my PCB design?
When selecting an insulating material for your PCB design, consider the following factors:
- Electrical properties: Dielectric constant, dissipation factor, and dielectric strength
- Thermal properties: Thermal conductivity and glass transition temperature
- Mechanical properties: Tensile strength, flexural strength, and dimensional stability
- Environmental factors: Chemical resistance, moisture absorption, and operating temperature range
- Cost and availability: Material cost and lead times for procurement
Evaluate your specific application requirements and consult with PCB manufacturers or material suppliers to choose the most suitable insulating material for your design.
Conclusion
PCB insulation plays a vital role in ensuring the proper functioning, reliability, and safety of electronic devices. By understanding the different types of insulating materials, their properties, and their applications, you can make informed decisions when designing and manufacturing PCBs.
From the commonly used FR-4 to high-performance materials like polyimide and Teflon, each insulating material has its own strengths and limitations. Selecting the right insulating material involves considering factors such as dielectric properties, thermal stability, mechanical strength, and environmental resistance.
By choosing the appropriate PCB insulation for your specific application, you can enhance signal integrity, prevent short circuits, and ensure the long-term reliability of your electronic products. As technology continues to advance, new insulating materials and techniques may emerge, offering even better performance and reliability for future PCB designs.
0 Comments