What is PCB insulation?
PCB insulation refers to the material used to separate and protect the conductive layers of a printed circuit board (PCB). The insulation material acts as a barrier, preventing short circuits and ensuring the proper functioning of the electronic components on the board. PCB insulation is a crucial aspect of PCB manufacturing, as it directly impacts the reliability, durability, and performance of the final product.
Types of PCB Insulation Materials
There are several types of insulation materials used in PCB manufacturing, each with its own unique properties and benefits. Some of the most common PCB insulation materials include:
- FR-4: A glass-reinforced epoxy laminate, FR-4 is the most widely used PCB insulation material due to its excellent mechanical and electrical properties.
- Polyimide: Known for its high heat resistance and flexibility, polyimide is often used in flexible PCBs and high-temperature applications.
- Teflon: Teflon, or PTFE (polytetrafluoroethylene), is a low-dielectric constant material that offers excellent high-frequency performance and is used in high-speed applications.
- Ceramic: Ceramic substrates are used in high-power and high-frequency applications due to their excellent thermal conductivity and low dielectric loss.
Material | Dielectric Constant | Thermal Conductivity (W/mK) | Max. Operating Temperature (°C) |
---|---|---|---|
FR-4 | 4.5 | 0.3 | 130 |
Polyimide | 3.5 | 0.2 | 260 |
Teflon | 2.1 | 0.3 | 260 |
Ceramic | 9.0 | 20.0 | 1000 |
The Role of PCB Insulation in PCB Manufacturing
Preventing Short Circuits
One of the primary functions of PCB insulation is to prevent short circuits between the conductive layers of the board. Short circuits can occur when two or more conductive paths come into contact with each other, causing an unintended flow of electrical current. This can lead to component failure, overheating, and even fire hazards. By separating the conductive layers with insulation material, PCB manufacturers can minimize the risk of short circuits and ensure the proper functioning of the electronic components.
Maintaining Signal Integrity
PCB insulation also plays a crucial role in maintaining signal integrity, especially in high-speed and high-frequency applications. The dielectric constant and dissipation factor of the insulation material can significantly impact the propagation of electrical signals through the board. A low dielectric constant material, such as Teflon, can help reduce signal loss and improve signal speed, while a high dielectric constant material, such as ceramic, can provide better signal stability and reduce crosstalk between adjacent traces.
Enhancing Mechanical Strength
In addition to its electrical properties, PCB insulation also contributes to the mechanical strength and durability of the board. The insulation material acts as a support structure, holding the conductive layers together and providing a stable base for the electronic components. This is particularly important in applications where the PCB is subjected to vibration, shock, or other mechanical stresses.
Thermal Management
PCB insulation can also play a role in thermal management, helping to dissipate heat generated by the electronic components. Some insulation materials, such as ceramic, have excellent thermal conductivity, allowing heat to be efficiently transferred away from the components and into the surrounding environment. This can help prevent overheating and improve the overall reliability of the PCB.
Factors to Consider When Choosing PCB Insulation
When selecting a PCB insulation material, there are several factors that PCB manufacturers must consider, including:
-
Dielectric Constant: The dielectric constant of the insulation material determines its ability to store electrical energy and affects the speed and integrity of signals propagating through the board. A lower dielectric constant is generally preferred for high-speed applications.
-
Thermal Conductivity: The thermal conductivity of the insulation material determines its ability to dissipate heat generated by the electronic components. Higher thermal conductivity is desirable for applications with high power dissipation requirements.
-
Mechanical Strength: The mechanical strength of the insulation material determines its ability to withstand physical stresses, such as bending, twisting, and vibration. Higher mechanical strength is important for applications where the PCB is subjected to harsh environmental conditions.
-
Cost: The cost of the insulation material is an important consideration for PCB manufacturers, as it directly impacts the overall cost of the final product. While some high-performance insulation materials may offer superior electrical and mechanical properties, they may also come with a higher price tag.
Factor | Importance |
---|---|
Dielectric Constant | Critical for high-speed and high-frequency applications |
Thermal Conductivity | Important for applications with high power dissipation |
Mechanical Strength | Crucial for applications subjected to physical stress |
Cost | Significant consideration for overall product cost |
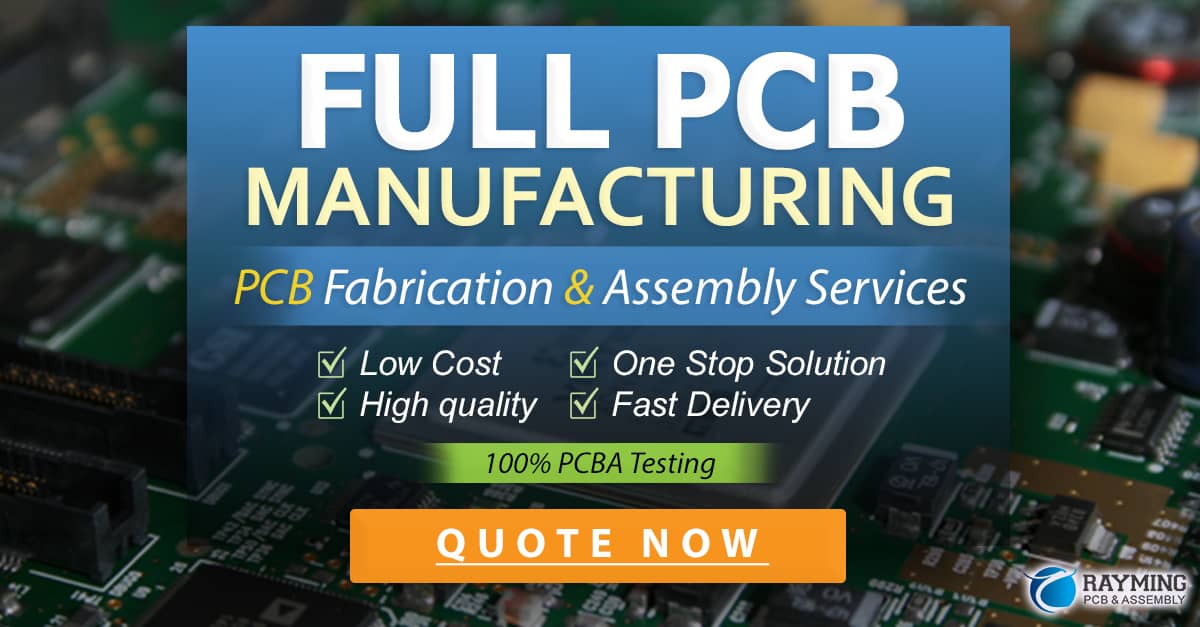
Best Practices for PCB Insulation in PCB Manufacturing
To ensure the optimal performance and reliability of PCBs, manufacturers should follow best practices when it comes to PCB insulation. Some of these best practices include:
-
Choosing the Right Insulation Material: Selecting the appropriate insulation material based on the specific requirements of the application, such as dielectric constant, thermal conductivity, and mechanical strength.
-
Proper Thickness Control: Maintaining consistent insulation thickness across the board to ensure uniform electrical and mechanical properties.
-
Minimizing Voids and Defects: Implementing strict quality control measures to minimize the presence of voids, inclusions, and other defects in the insulation material, which can negatively impact the performance and reliability of the PCB.
-
Adhering to Industry Standards: Following industry standards and guidelines, such as IPC-4101, which provide specifications for PCB insulation materials and their properties.
Frequently Asked Questions (FAQ)
- What is the most common PCB insulation material?
-
FR-4, a glass-reinforced epoxy laminate, is the most widely used PCB insulation material due to its excellent balance of electrical, mechanical, and thermal properties.
-
What is the difference between a low dielectric constant and a high dielectric constant material?
-
A low dielectric constant material, such as Teflon, has a lower capacity to store electrical energy and is preferred for high-speed applications, as it helps reduce signal loss and improve signal speed. A high dielectric constant material, such as ceramic, has a higher capacity to store electrical energy and is used in applications that require better signal stability and reduced crosstalk.
-
How does PCB insulation help with thermal management?
-
Some PCB insulation materials, such as ceramic, have high thermal conductivity, which allows heat generated by electronic components to be efficiently transferred away from the components and into the surrounding environment. This helps prevent overheating and improves the overall reliability of the PCB.
-
Why is mechanical strength an important factor when choosing PCB insulation?
-
The mechanical strength of the insulation material determines its ability to withstand physical stresses, such as bending, twisting, and vibration. In applications where the PCB is subjected to harsh environmental conditions, higher mechanical strength is crucial to ensure the integrity and reliability of the board.
-
What are some best practices for PCB insulation in PCB manufacturing?
- Best practices for PCB insulation include choosing the right insulation material based on application requirements, maintaining proper thickness control, minimizing voids and defects, and adhering to industry standards and guidelines. By following these best practices, PCB manufacturers can ensure the optimal performance and reliability of their products.
In conclusion, PCB insulation is a critical aspect of PCB manufacturing that directly impacts the reliability, durability, and performance of the final product. By understanding the types of insulation materials available, their properties, and the factors to consider when choosing an insulation material, PCB manufacturers can make informed decisions that lead to the production of high-quality PCBs. Additionally, by following best practices for PCB insulation, manufacturers can ensure the optimal performance and reliability of their products, ultimately contributing to the success of the electronic devices and systems that rely on these PCBs.
0 Comments