What is a PCB Board?
A Printed Circuit Board (PCB) is a fundamental component in modern electronics. It is a flat board made of insulating materials, such as fiberglass or composite epoxy, with conductive copper traces printed onto its surface. These traces connect various electronic components, such as resistors, capacitors, and integrated circuits, to form a complete electrical circuit.
PCBs have revolutionized the electronics industry by providing a reliable and efficient means of connecting electronic components. They have replaced the old method of point-to-point wiring, which was time-consuming, error-prone, and resulted in bulky and unreliable devices.
Types of PCB Boards
There are several types of PCB boards, each with its own unique characteristics and applications. The most common types include:
-
Single-Sided PCB: These boards have copper traces on only one side of the insulating substrate. They are the simplest and most cost-effective type of PCB, suitable for basic electronic projects.
-
Double-Sided PCB: These boards have copper traces on both sides of the insulating substrate, allowing for more complex circuit designs and higher component density. The two sides are connected through plated holes called vias.
-
Multi-Layer PCB: These boards consist of multiple layers of insulating substrate with copper traces on each layer. They can have anywhere from four to twelve or more layers, depending on the complexity of the circuit. Multi-layer PCBs are used in advanced electronic devices, such as smartphones, computers, and medical equipment.
-
Flexible PCB: These boards are made of flexible insulating materials, such as polyimide or PEEK, allowing them to bend and conform to various shapes. They are commonly used in wearable electronics, aerospace applications, and medical devices.
-
Rigid-Flex PCB: These boards combine the benefits of both rigid and flexible PCBs. They consist of rigid PCB sections connected by flexible PCB sections, providing the best of both worlds in terms of reliability and flexibility.
PCB Type | Layers | Applications | Cost |
---|---|---|---|
Single-Sided | 1 | Basic electronic projects | Low |
Double-Sided | 2 | More complex circuits | Medium |
Multi-Layer | 4-12+ | Advanced electronic devices | High |
Flexible | 1-2 | Wearable electronics, aerospace | Medium-High |
Rigid-Flex | 2+ | High-reliability applications | High |
PCB Board Materials
The choice of materials for a PCB board is crucial, as it affects the board’s performance, durability, and cost. The most common materials used in PCB manufacturing are:
Substrate Materials
-
FR-4: This is the most widely used substrate material for PCBs. It is a composite material made of woven fiberglass cloth with an epoxy resin binder. FR-4 offers excellent mechanical and electrical properties, making it suitable for a wide range of applications.
-
High-Tg FR-4: This is a variant of FR-4 with improved thermal properties. It has a higher glass transition temperature (Tg), which allows it to withstand higher operating temperatures without deforming.
-
Polyimide: This is a high-performance substrate material used in flexible PCBs. It offers excellent thermal stability, chemical resistance, and mechanical strength.
Copper Foil
Copper foil is the conductive material used to create the traces on a PCB. The thickness of the copper foil is measured in ounces per square foot (oz/ft²). The most common thicknesses are:
- 0.5 oz/ft² (17.5 µm)
- 1 oz/ft² (35 µm)
- 2 oz/ft² (70 µm)
Thicker copper foil allows for higher current-carrying capacity but may increase the cost and complexity of manufacturing.
Solder Mask
Solder mask is a thin layer of polymer applied over the copper traces on a PCB. It serves several purposes:
- Protects the copper traces from oxidation and corrosion
- Prevents accidental short circuits during soldering
- Provides a visual contrast for easier component placement and inspection
Solder mask is typically green in color, but other colors, such as red, blue, and black, are also available.
Silkscreen
Silkscreen is a layer of text and symbols printed onto the PCB surface. It provides useful information, such as component designators, polarity markers, and logos. Silkscreen is typically white in color, but other colors are also available.
PCB Board Design Considerations
Designing a PCB board requires careful consideration of several factors to ensure optimal performance, reliability, and manufacturability. Some of the key design considerations include:
Schematic Design
The first step in PCB design is to create a schematic diagram of the circuit. This involves selecting the appropriate components, defining their interconnections, and ensuring that the circuit functions as intended. Schematic design software, such as Eagle or KiCad, is commonly used for this purpose.
Layout Design
Once the schematic is complete, the next step is to create a physical layout of the PCB. This involves placing the components on the board, routing the copper traces, and ensuring that the design meets the manufacturing constraints. Some important layout considerations include:
-
Component Placement: Components should be placed in a logical and efficient manner, minimizing the distance between related components and ensuring adequate spacing for heat dissipation and manufacturability.
-
Trace Routing: Copper traces should be routed in a way that minimizes crosstalk, signal integrity issues, and electromagnetic interference (EMI). Techniques such as ground planes, power planes, and shielding can be used to improve signal quality.
-
Design Rule Check (DRC): DRC is a software tool that checks the layout design against a set of predefined rules to ensure that it meets the manufacturing constraints. These rules include minimum trace width, minimum spacing between traces, and minimum drill size for vias.
Manufacturing Considerations
When designing a PCB, it is important to consider the manufacturing process and constraints. Some key manufacturing considerations include:
-
PCB Thickness: The thickness of the PCB affects its mechanical strength, thermal performance, and cost. Common thicknesses range from 0.031 inches (0.8 mm) to 0.125 inches (3.2 mm).
-
Minimum Feature Size: The minimum feature size refers to the smallest trace width and spacing that can be reliably manufactured. This depends on the PCB manufacturer’s capabilities and the chosen manufacturing process.
-
Panelization: Panelization is the process of arranging multiple PCB designs on a single panel for efficient manufacturing. It is important to consider the panelization layout and the spacing between individual boards to ensure proper fabrication and assembly.
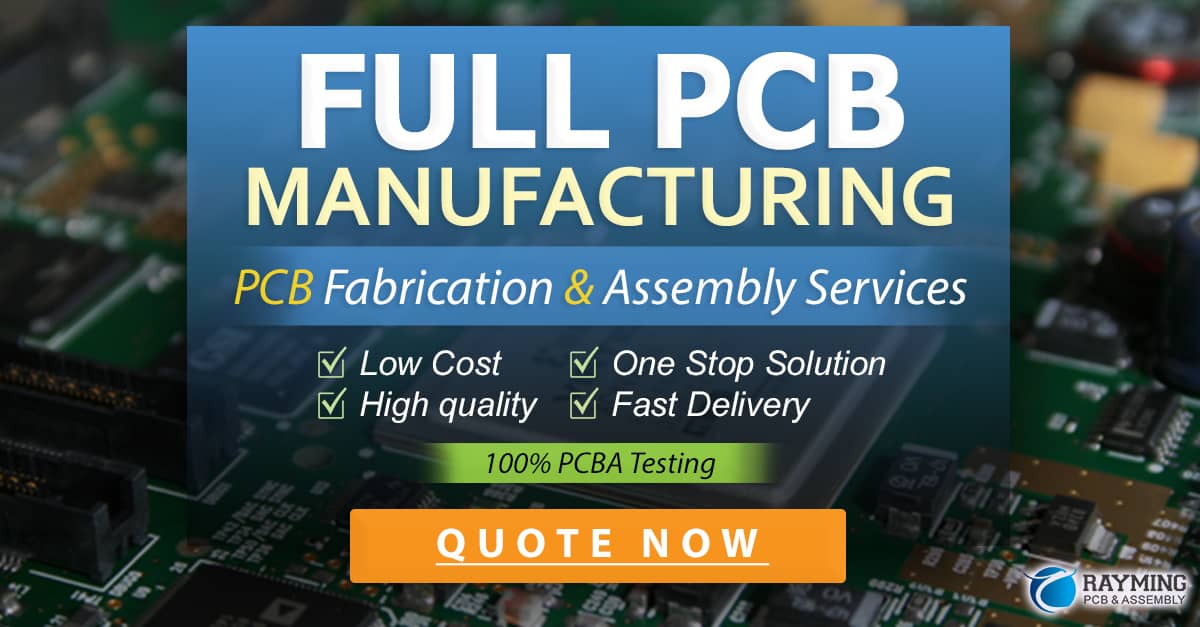
PCB Board Manufacturing Process
The PCB manufacturing process involves several steps, each requiring specialized equipment and expertise. The main steps in PCB manufacturing are:
-
PCB Design: The PCB design is created using specialized software, such as Altium Designer or Eagle. The design includes the schematic diagram, component placement, and trace routing.
-
PCB Fabrication: The PCB design files are sent to a PCB manufacturer, who fabricates the board using a multi-step process:
a. Copper Cladding: A thin layer of copper is bonded to the insulating substrate material.
b. Patterning: The copper layer is patterned using a photolithography process to create the desired traces and pads.
c. Lamination: For multi-layer PCBs, the patterned layers are aligned and laminated together under high pressure and temperature.
d. Drilling: Holes are drilled through the board for component leads and vias.
e. Plating: The holes are plated with copper to create electrical connections between layers.
f. Solder Mask and Silkscreen: The solder mask and silkscreen layers are applied to the board. -
PCB Assembly: The fabricated PCB is populated with electronic components using one of two methods:
a. Through-Hole Assembly: Components with long leads are inserted through the holes in the board and soldered in place.
b. Surface-Mount Assembly: Components with small, flat contacts are placed directly onto the pads on the board and soldered in place. -
Testing and Inspection: The assembled PCB is tested and inspected to ensure proper functionality and quality. This may involve automated optical inspection (AOI), X-ray inspection, and electrical testing.
PCB Board Testing and Quality Control
Ensuring the quality and reliability of PCB boards is crucial for the success of any electronic product. Several testing and quality control methods are used throughout the manufacturing process:
-
Visual Inspection: PCBs are visually inspected for defects such as scratches, dents, and discoloration. This is typically done using automated optical inspection (AOI) machines.
-
Automated Optical Inspection (AOI): AOI machines use high-resolution cameras and image processing algorithms to detect defects such as missing components, incorrect component placement, and solder bridging.
-
X-Ray Inspection: X-ray machines are used to inspect the internal structure of PCBs, particularly for multi-layer boards and BGA (Ball Grid Array) components. They can detect defects such as voids in solder joints and misaligned vias.
-
Electrical Testing: PCBs are subjected to various electrical tests to ensure proper functionality. These tests include:
a. Continuity Test: Checks for open circuits and short circuits between pins and pads.
b. Insulation Resistance Test: Measures the resistance between isolated conductors to ensure adequate insulation.
c. Functional Test: Verifies that the PCB performs its intended function under normal operating conditions. -
Environmental Testing: PCBs are tested under various environmental conditions to ensure their reliability and durability. These tests include:
a. Temperature Cycling: PCBs are subjected to repeated cycles of high and low temperatures to simulate real-world operating conditions.
b. Humidity Testing: PCBs are exposed to high humidity levels to test their resistance to moisture.
c. Vibration and Shock Testing: PCBs are subjected to mechanical stress to ensure they can withstand the rigors of transportation and use.
By implementing a comprehensive testing and quality control process, manufacturers can ensure that their PCBs meet the highest standards of quality and reliability.
Frequently Asked Questions (FAQ)
-
What is the difference between a PCB and a PCBA?
A PCB (Printed Circuit Board) is the bare board without any components attached. A PCBA (Printed Circuit Board Assembly) is a PCB that has been populated with electronic components and is ready for use. -
What are the advantages of using a multi-layer PCB?
Multi-layer PCBs offer several advantages over single- and double-sided PCBs:
a. Higher component density, allowing for more complex circuits in a smaller space
b. Better signal integrity and reduced crosstalk due to the use of dedicated power and ground planes
c. Improved thermal management and heat dissipation -
What is the minimum feature size for a PCB?
The minimum feature size depends on the PCB manufacturer’s capabilities and the chosen manufacturing process. Typical minimum feature sizes range from 3 mil (0.075 mm) to 6 mil (0.15 mm) for trace width and spacing. -
How long does it take to manufacture a PCB?
The manufacturing time for a PCB depends on several factors, such as the complexity of the design, the chosen manufacturing process, and the PCB manufacturer’s workload. Typical lead times range from a few days to several weeks. -
What is the typical cost of a PCB?
The cost of a PCB depends on various factors, such as the board size, layer count, material choice, and order quantity. Small, simple PCBs can cost a few dollars each, while large, complex PCBs can cost hundreds of dollars each. Many PCB manufacturers offer online quoting tools to help estimate the cost of a specific design.
In conclusion, PCB boards are essential components in modern electronics, providing a reliable and efficient means of connecting electronic components. Understanding the different types of PCBs, materials, design considerations, manufacturing processes, and testing methods is crucial for anyone involved in the development of electronic products. By following best practices and working with experienced PCB manufacturers, designers can create high-quality, reliable PCBs that meet the demands of today’s increasingly complex electronic devices.
0 Comments