Introduction to PCB Board Assembly
Printed circuit board (PCB) assembly is the process of soldering electronic components to a PCB to create a functional printed circuit assembly (PCA). Proper PCB assembly requires adherence to precise specifications and quality standards to ensure the reliability of the electronic devices being produced. This guide will provide a comprehensive overview of PCB assembly, including the key steps, equipment, materials, and best practices.
PCB Board Assembly Process Steps
The PCB assembly process consists of several main steps:
Solder Paste Printing
Solder paste is printed onto the PCB in a pattern that matches the footprint of the components. This provides the adhesive and conductive properties needed to mount and solder the components. Stencil printing and dispensing are two common solder paste application methods.
Component Placement
Electronic components are precisely placed onto the PCB according to the bill of materials (BOM) and assembly drawings. Automated pick-and-place machines populate most of the components rapidly and accurately.
Solder Reflow
The PCB passes through a reflow oven to heat the assembly above the melting point of the solder. This causes the solder particles in the paste to coalesce and solidify, forming both electrical and mechanical bonds between the components and board.
Inspection and Testing
Quality control steps like visual inspection and in-circuit testing verify that the PCB assembly meets specifications and identifies any defects. Automated optical inspection (AOI) systems can rapidly check for issues with component placement, solder joints, etc.
Conformal Coating
A protective plastic coating is often selectively applied to the assembled PCB to guard against moisture, contaminants, and electrical interference.
Final Testing
Additional functional testing ensures the PCB operates as intended before shipment to customers. Common tests include burn-in, where the board is stressed at high temperatures over an extended period.
PCB Assembly Equipment
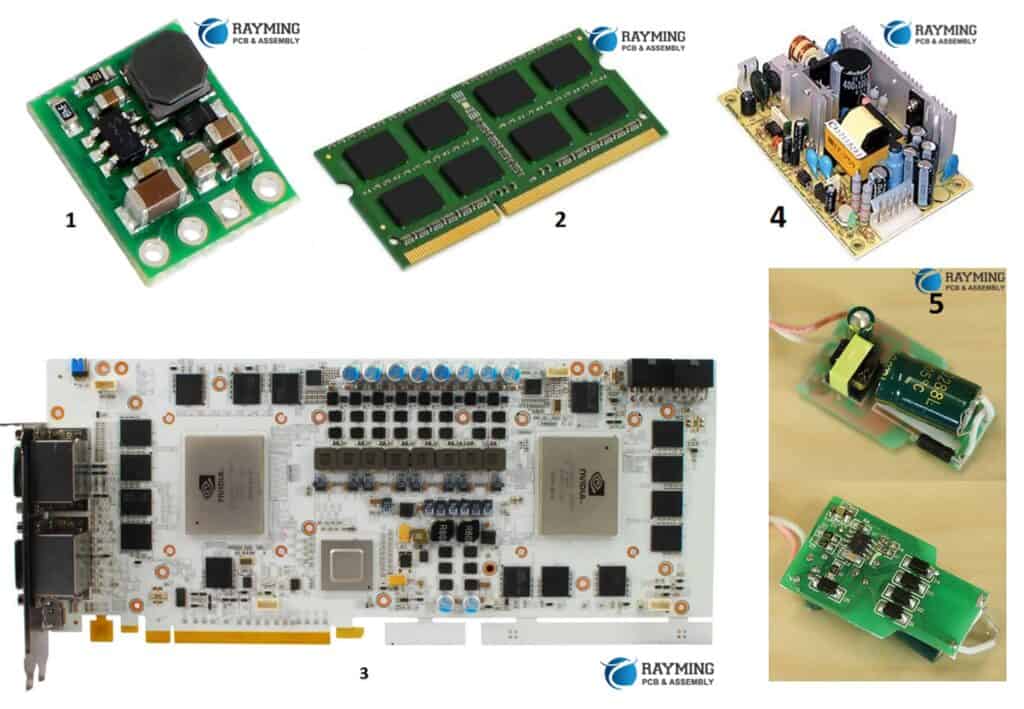
Specialized equipment is used at each stage of PCB assembly:
- Solder paste printers – Apply an even layer of solder paste through stencils onto the PCB.
- Pick-and-place machines – Use vacuum nozzles to rapidly and precisely pick components from reels or trays and place them on the board.
- Reflow ovens – Heat the PCB assembly to melt the solder paste and form solder joints. Convection, infrared, vapor phase, and other heating methods are used.
- Inspection systems – Automated optical inspection (AOI) and x-ray systems identify defects in solder joints, component placement, etc.
- Conformal coating machines – Selectively apply protective coatings to the assembled PCB via spraying, brushing, or dipping methods.
- Test systems – Conduct electrical tests to verify function and identify faults on the completed boards.
Equipment | Purpose |
---|---|
Solder Paste Printer | Prints solder paste onto PCB |
Pick-and-Place Machine | Places components onto solder paste-coated PCB |
Reflow Oven | Melts solder paste to form solder joints |
AOI System | Optically inspects solder joints and component placement |
Conformal Coating Machine | Applies protective coating to assembled PCB |
Electrical Test System | Functionally tests the completed PCB assembly |
PCB Assembly Materials
In addition to the PCB itself, key materials used in the assembly process include:
- Solder paste – A mixture of solder powder, flux, and viscosity modifiers, used to adhere components before soldering.
- Components – The electronic components that will be mounted to the PCB – ICs, resistors, capacitors, connectors, etc.
- Stencils – Metal templates used to apply solder paste onto the PCB in the desired pattern.
- Conformal coatings – Protective plastic coatings applied to prevent damage from moisture, dust, chemicals, etc.
PCB Assembly Best Practices
Follow these best practices to achieve high-quality PCB assemblies:
- Maintain tight process controls and adhere to specifications – for solder paste printing, component placement accuracy, reflow profile, etc.
- Use inspection systems like AOI to catch defects early.
- Validate processes upfront using test assemblies.
- Use solder paste and other materials from trusted suppliers.
- Closely monitor oven reflow temperature profiles.
- Implement ESD control procedures.
- Use no-clean solder paste to avoid post-solder cleaning.
- Apply conformal coatings selectively to avoid interfering with component function.
- Conduct comprehensive functional testing on finished boards.
Benefits of Outsourcing PCB Assembly
Many companies outsource PCB assembly to contract manufacturers (CMs) or electronics manufacturing services (EMS) providers. Benefits include:
- Faster time-to-market – No need to purchase expensive assembly equipment and establish in-house capabilities.
- Quality – CMs have the expertise, facilities, and capital for high-quality, reliable assemblies.
- Cost savings – Economies of scale allow CMs to offer competitive assembly pricing.
- Supply chain simplification – CMs source components, manage suppliers, and integrate assembly into a streamlined workflow.
Partnering with an experienced, trusted CM enables companies to focus on core competencies and accelerate new product introductions while still meeting budget goals.
Conclusion
In summary, PCB assembly is a complex, multi-step manufacturing process requiring specialized equipment, trained operators, and disciplined procedures to produce electronic assemblies efficiently and with minimal defects. Solder paste printing, component placement, soldering, inspection and conformal coating are the key stages. By leveraging the expertise and capabilities of contract manufacturers, companies can cost-effectively introduce high-quality, reliable PCB assemblies to market faster.
Frequently Asked Questions
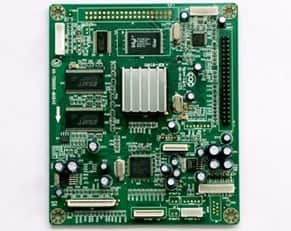
What is the most critical stage in PCB assembly?
The soldering process, where components are permanently attached to the board through reflow soldering, is arguably the most critical PCB assembly stage. Defective solder joints can lead to electrical faults and product failures down the line.
How are very small surface mount components handled in assembly?
Smaller components like 0201 and 01005 chip components are handled by specialized pick-and-place machines designed for micro-scale placement. High magnification cameras precisely locate and position the tiny components.
What kind of testing is performed on completed boards?
Electrical testing like in-circuit testing and flying probe testing verify connectivity and function. Other common production tests include burn-in testing, where boards are stressed at high temperatures, as well as vibration, drop, and environmental testing.
What is the benefit of selective coating in conformal coating?
Selectively applying conformal coating avoids covering components like test points, switches, or connectors that need to be accessed or exposed for the board to function properly. It provides protection while minimizing impact on board operation.
How are PCB assembly line workers trained and qualified?
Formal training programs, certification standards such as IPC-A-610 for acceptability of electronics assemblies, and on-the-job experience under the guidance of veteran assemblers help workers gain the skills needed to meet quality and productivity objectives.
0 Comments