Introduction to PCB Assembly
Printed circuit board (PCB) assembly is the process of soldering electronic components onto a PCB. This involves placing components such as resistors, capacitors, integrated circuits (ICs), transistors etc. in their designated locations on the PCB and then soldering them into place. PCB assembly requires great precision and is usually done by automated assembly machines, although manual assembly is also possible for low volume production.
The end product of PCB assembly is called a printed circuit assembly (PCA) which forms an integral part of most electronic devices. From consumer devices like smartphones and laptops to industrial equipment, automotive electronics and aerospace avionics, PCB assemblies are ubiquitous across all sectors. As electronic products become more complex and miniaturized, the demand for high-quality PCB assembly services continues to grow globally.
Why Outsource PCB Assembly?
For most companies involved in electronics manufacturing, outsourcing PCB assembly to a specialized provider makes strategic and economic sense. Here are some of the benefits of outsourced PCB assembly services:
Focus on Core Competencies: Electronics companies can stay focused on their core product development and innovation activities while leveraging the expertise of PCB assembly service providers.
Cost Savings: Outsourced assembly is often cheaper compared to maintaining in-house SMT production lines due to economies of scale and specialization of service providers.
Greater Flexibility: Usage spikes, production ramp-ups, prototyping needs etc. can be easily managed by utilizing extra production capacity of assembly partners.
Improved Quality: Reputed PCB assembly companies invest heavily in advanced machinery, processes and quality control to deliver high-precision assembly.
Accelerated Time-to-Market: Outsourcing assembly parallelizes production activities and helps bring new products faster to the market.
Access to Advanced Technologies: Partnering with industry leaders allows leveraging cutting-edge assembly equipment and processes.
Reduced Capital Investment: In-house SMT lines require huge upfront investment and continuous upgrade expenditure which is avoided in outsourced assembly.
Clearly, there are significant merits in partnering with an experienced PCB assembly company, especially for high-mix, low to medium volume production needs.、
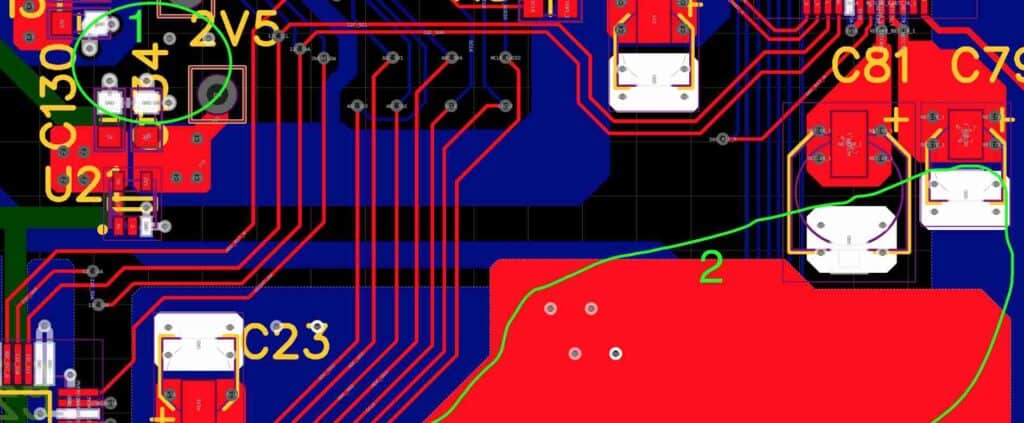
Key Considerations for PCB Assembly Services
Selecting the right PCB assembly partner involves evaluating several parameters and asking the right questions. Here are some key considerations:
Technical Capabilities
- What assembly technologies (SMT, THT, mixed) are supported?
- What is the maximum PCB size that can be assembled?
- What component types and packaging can be handled (QFP, BGA, 01005, etc)?
- What is the minimum achievable component pitch?
- Are advanced processes like vapour phase soldering, press-fit connectors etc. available?
- What inspection and test capabilities are implemented?
Quality & Reliability
- Is the company certified for QMS/ESD/green standards?
- What process controls and SPC techniques are implemented?
- How is counterfeit component mitigation ensured?
- What testing and inspection methods are utilized?
- What are the current defect rates and Cpk levels?
- Is reliability testing (HALT, HASS, burn-in etc.) offered?
Engineering Support
- Is DFM analysis offered to improve manufacturability?
- Does the assembler provide design review and assembly optimization recommendations?
- Will they build and supply extra samples for verification and testing?
- Can they handle quick-turn prototypes and low volume orders?
Supply Chain & Logistics
- What courier and shipping partners are utilized for transportation?
- How is BOM/component sourcing managed?
- What inventory management system is used?
- Are consignment stocking or VMI arrangements supported?
- How is ESD protection ensured during handling and shipment?
IT Infrastructure
- What ERP, MES and shop floor control systems are employed?
- How is manufacturing and test data collected and analyzed?
- What data/analytics are provided to the customer for each assembly batch?
- How is product configuration, version and change management handled?
- What online tools are provided for design, order and inventory management?
Carefully evaluating these parameters will help identify the right PCB assembly partner that is best aligned with your product needs and business priorities.
PCB Assembly Process Step-by-Step
The sequence of manufacturing steps in a typical PCB assembly process is outlined below:
1. Solder Paste Printing
The first step is to accurately print solder paste on all the pads where components need to be soldered. This is done using stencil masks and high precision solder paste printers.
2. Solder Paste Inspection (SPI)
The printed solder paste deposits are verified to ensure there are no missing prints or insufficient print volumes. Optical SPI machines capture high resolution images to detect any printing defects.
3. Component Placement
Electronic components are precisely placed on the PCB using automated SMT pick-and-place machines. These machines populate thousands of components per hour from reels or trays into their designated locations on the board.
4. Automated Optical Inspection (AOI)
Once component placement is completed, AOI machines verify all components for correct placement against the PCB CAD data. This detects any wrong or missing components.
5. Reflow Soldering
The populated boards pass through reflow ovens to melt the solder paste and metallurgically bond components to the PCB through controlled thermal profiles.
6. Post-Reflow AOI
AOI inspection is repeated after soldering to check for any soldering defects like shorts, opens, tombstoning etc.
7. Conformal Coating
A protective plastic coating may be selectively applied on the assembled boards to enhance product reliability.
8. End-of-Line Testing
Finished boards are put through a battery of electrical, functional and reliability tests for final verification and quality assurance.
9. Final Quality Inspection
Detailed workmanship inspection is done either manually or using automated optical inspection systems.
10. Packaging and Shipment
The finished PCB assemblies are packed with ESD shielding in customized trays, tubes or tapes and shipped to the customer.
Throughout the entire assembly process, detailed machine and process data is collected and analyzed to identify optimization areas using statistical process control techniques.
Key Factors Impacting PCB Assembly Cost
There are several elements that impact the overall cost of getting PCB assemblies produced. Being aware of these cost drivers helps optimize assembly expenses. The key factors affecting assembly costs are:
- PCB size – larger boards cost more to populate and process.
- Component count – more components means higher placement and soldering costs.
- Component types – odd-form factors, BGAs etc. require special tooling.
- Lead-free soldering – needs higher temperatures and is more expensive.
- Low volume batches – benefit from economies of scale in higher volumes.
- Testing and inspection – adds cost but improves quality assurance.
- High-mix complexity – frequent changeovers lead to production inefficiencies.
- Gold-plating – desirable for connectivity but adds cost over nickel plating.
- Certifications required – regulatory standards like ISO-9001 lead to more documentation.
- Rework rates – high defects increase rework costs and reduce throughput.
- Regional labor rates – lower labor costs in certain geographies helps reduce cost.
Here is a quick comparison of how some key parameters impact per unit PCB assembly cost:
PCB Assembly Parameter | Low-End | Medium | High-End |
---|---|---|---|
Board size | < 100 mm^2 | 100 – 600 mm^2 | > 600 mm^2 |
Component count | < 200 | 200 – 500 | > 500 |
Lead-free process | No | Optional | Default |
Monthly volume | > 10K units | 1K – 10K units | < 1K units |
Testing/inspection | Basic | Standard | Full AOI + functional test |
Certifications | None | ISO-9001 | IATF 16949 |
Choosing the Right PCB Assembly Partner
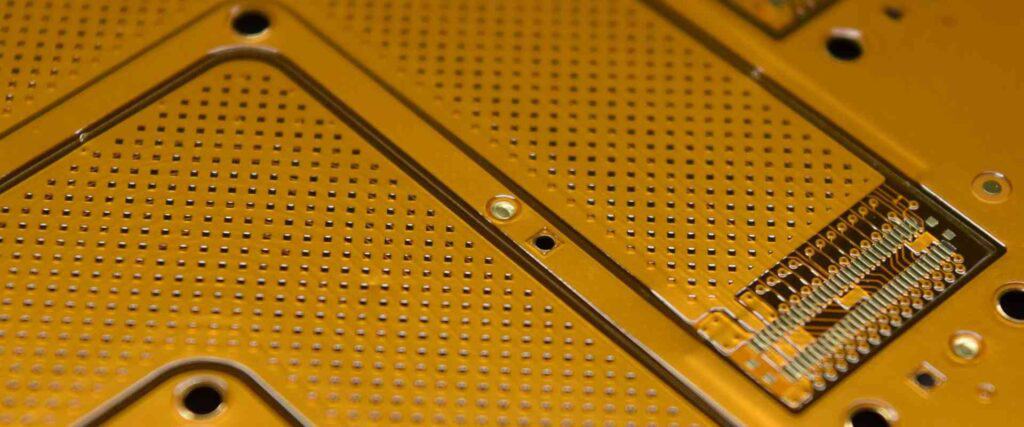
Here are some tips on selecting the best PCB assembly services partner for your specific requirements:
- Clearly detail your technical requirements, volume projections and quality expectations upfront.
- Evaluate capabilities across the range of assembly technologies needed.
- Validate quality system effectiveness through audits and visits.
- Review test, inspection and process data for reassurance.
- Check capabilities, cost and location advantages of global capacity.
- Opt for those providing comprehensive engineering support.
- Favor automated assembly over manual assembly for consistency.
- Partner with those offering supply chain services for turnkey support.
- Choose service providers that can scale capacity with your changing needs.
- Seek recommendations from industry peers on preferred partners.
- Leverage PCB assembly comparison sites to make data-driven decisions.
Mistakes to Avoid in PCB Assembly
Here are some common mistakes to avoid in order to prevent issues during PCB assembly and maximize yields:
- Inadequate component clearance leading to improper soldering.
- Using via-in-pad which creates weak solder joints.
- Specifying fine-pitch BGAs beyond assembler’s capabilities.
- Insufficient solder paste volume resulting in dry joints.
- Poor pad geometries causing tombstoning.
- Skipping reflow profile optimization.
- No spec control leading to counterfeit components.
- Inadequate test point access for end-of-line testing.
- Lack of fixture support for connectors/odd components.
- Not reviewing PCBA design with assembler early.
- Skipping functional testing of the assembled boards.
- Cheaping out on conformal coating for reliability.
- No ESD control during assembly handling steps.
Proactively avoiding such common errors in partnership with your PCB assembler will help maximize assembly quality and functional yield for your products.
Frequently Asked Questions
Here are some common FAQs regarding PCB assembly services:
Q: What are the typical deliverables when outsourcing PCB assembly?
A: The usual deliverables are – fully assembled PCBs, test/inspection reports, component placement files, solder paste stencils, assembly drawings, box/panel build instructions, and custom packaging as needed.
Q: How is prototyping different from production PCB assembly?
A: Prototyping involves more manual assembly, relaxed quality processes, smaller order sizes and faster lead times. Production focuses on automation, rigorous QC, higher volumes and leveraging economies of scale.
Q: Can PCB assemblers handle component sourcing as well?
A: Many PCB assembly service providers offer procurement and supply chain services to source components required for assembly BOMs. This provides a turnkey solution.
Q: How can assembled PCBs be tested by the service provider?
A: Assemblers can conduct basic power-on testing or comprehensive functional testing using fixture based or flying probe test systems for electrical and performance verification.
Q: What environmental standards do PCB assembly companies adhere to?
A: Most leading assemblers are ISO 14001 certified and use lead-free processes. Many also focus on reducing waste, energy/water use and carbon emissions in their facilities.
Conclusion
Partnering with a reliable PCB assembly company provides electronics manufacturers access to advanced assembly technologies, quality systems and supply chain capabilities. Carefully matching service provider strengths to your product and business needs is key to a successful outsourcing relationship. Leveraging the guidelines provided in this article will help you find the right PCB assembly partner to meet your requirements in a cost-effective and timely manner.
0 Comments