Introduction
Printed circuit board (PCB) assembly is a crucial process in electronics manufacturing. It involves soldering and assembling various electronic components like resistors, capacitors, integrated circuits, etc. onto a PCB to create a functional electronic product.
Choosing the right PCB assembly service provider is critical for ensuring quality products delivered on time and within budget. A key factor in selecting an assembly partner is understanding PCB assembly pricing and how various factors affect the overall cost.
This comprehensive guide examines key considerations for PCB assembly pricing in detail to help electronics OEMs make informed sourcing decisions.
Factors That Determine PCB Assembly Cost
PCB assembly pricing depends on various factors, including:
1. Board Complexity
The complexity of the PCB design significantly impacts assembly costs. Simple single-sided and double-sided boards are cheaper to assemble than complex multilayer boards.
Here are some parameters that determine PCB complexity:
- Number of layers – More layers mean higher costs
- Component density – Boards with higher component density take more time to assemble
- Component types – Complex components like BGAs, connectors add to assembly costs
- Board size – Larger boards occupy more assembly time and resources
- Fine pitch components – Components with finer pitch require more precision to assemble
- Routed holes – Boards with several routed holes and cutouts increase assembly costs
2. Component Factors
The type, quantity, and size of components used impact PCB assembly pricing.
- Component types – Complex ICs like FPGAs are more expensive than simple resistors or capacitors
- Component size – Smaller components (SMD 0201 vs 0805) require more precision and add to cost
- Component counts – Higher number of component placements means longer assembly time
- Component sourcing – Providing vs procuring components affects pricing
3. Production Volume
Higher quantities bring economies of scale, reducing the per-unit assembly costs. On the other hand, low-volume or prototype builds often have high setup charges, increasing per unit costs.
4. Lead Time
Rushed turnaround times often command a premium over standard assembly lead times. Normal lead times range from 3 days to 2 weeks, with rush orders completed in 1-3 days for an additional fee.
5. Testing and Inspection
The extent of testing (in-circuit, functional, burn-in) and inspection (AOI, X-ray) adds to assembly costs but results in higher quality boards.
6. Location
PCB assembly pricing varies by geographic location. In general, costs are lower in China compared to the US or Europe. Shipping and logistics costs also factor in.
7. Certifications
Special certifications like ITAR, UL, RoHS, ISO, etc. add overhead costs due to stringent processes required to achieve compliance.
8. Value-added Services
Services like custom packaging, supply chain management, drop shipping to end customers, etc. add to the overall costs.
PCB Assembly Pricing Models
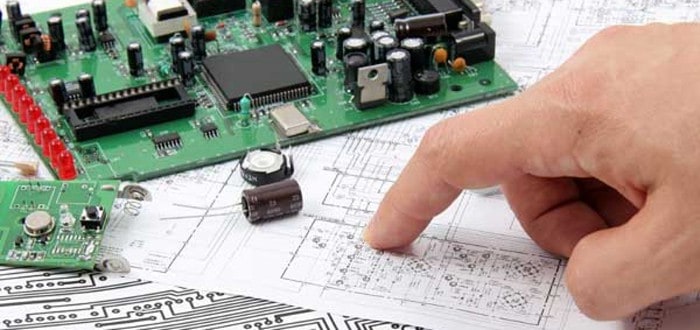
There are three primary pricing models used by assembly providers:
1. Per part pricing
This model is based on the total component count on the assembled PCB. The provider charges a fixed cost per component placed, which scales with the total number of parts.
Simple and straightforward, but does not account for complexity, layer count, special parts, etc. Suited for simple, high-volume boards.
2. Time & Materials pricing
The assembly time and material costs incurred are billed to the customer. Labor charges are based on IPC-A-610 assembly standards. Material charges include components, solder, stencils, etc.
Offers complete transparency of costs but the final price is not known upfront. Best suited for new customers with low volumes.
3. All-inclusive pricing
A fixed price is quoted upfront for the complete assembly job, including components. The most common model, offering cost predictability. Involves higher profit margins to account for unknowns.
Suited for medium to high volume production. Large orders can negotiate discounted pricing.
PCB Assembly Cost Breakdown
A typical PCB assembly price quote contains individual line items with cost breakdowns for:
- Engineering/NRE Charges – For Gerber review, BOM setup, tooling prep, test fixture design, etc. Charged only once.
- Solder Paste Stencils – Based on number of stencils, size, and complexity. Some vendors include stencil costs in assembly charges.
- PCB Depanelization – Removing singulated PCBs from the panel from the PCB manufacturer. Optional cost.
- SMT Pick & Place – Charges for SMT assembly based on pricing model. Influenced by complexity, volume and lead time.
- SMT Programming – One time charge for creating assembly program files. Based on number of unique boards.
- Component Costs – Bill of Materials cost. Vastly varies based on component types and quantities.
- Through Hole Assembly – For inserting and soldering PTH components. Based on number of holes.
- Inspection & Testing – Charges for inspection, in-circuit test, functional testing selected by customer.
- Inventory and Kitting – Optional service to kit components for production. May reduce handling overhead.
- Packaging & Shipment – Custom packaging and drop ship costs if required.
Here is an example high-level BOM with typical assembly cost breakdown for a mid-complexity board:
PCB Assembly Cost Breakdown | Price |
---|---|
Engineering/NRE Charges | $250 |
Solder Paste Stencils | $200 |
SMT Assembly – 2500 components | $4000 |
SMT Programming | $50 |
Component Costs – BOM | $1500 |
Testing and Inspection | $800 |
Inventory/Kitting | $100 |
Total Cost | $6900 |
This basic breakdown shows the major cost segments in a PCB assembly quote. The component costs and SMT assembly charges typically dominate overall costs.
Estimating PCB Assembly Costs
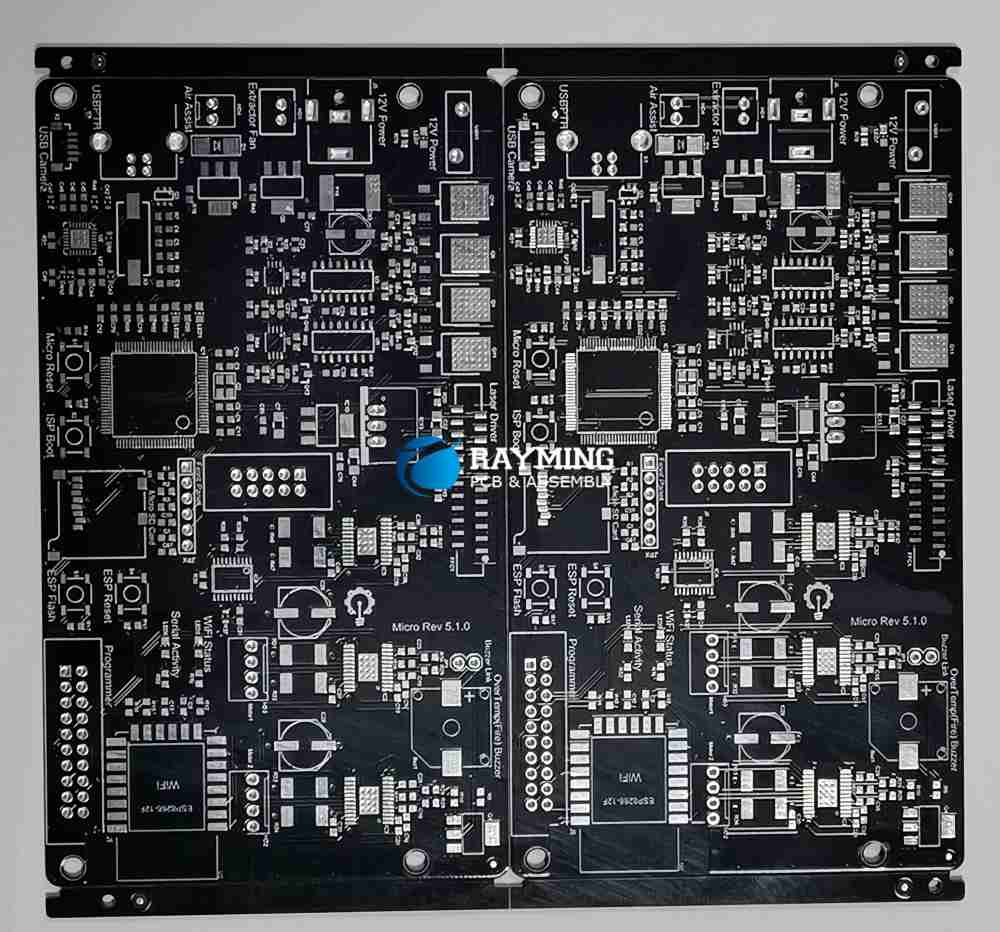
You can estimate rough assembly costs even without a detailed quote, using these thumb rules:
- Simple 2-layer PCB – $2 to $5 per component
- Medium complexity PCB – $5 to $10 per component
- High-complexity multilayer PCB – $10 to $25 per component
- High-density HDI PCB – $25+ per component
Apply suitable cost based on your board complexity and multiply by total component count to estimate overall costs.
Add roughly 15% to 20% overhead charges for programming, testing, stencils etc. on top of base component placement costs.
These provide only a ballpark estimate but help budget and plan assemblies especially in early prototyping stages.
Always get quotes from multiple assembly shops to compare pricing. Check for hidden charges and minimum order fees.
Optimizing PCB Assembly Costs
Here are some tips to optimize PCB assembly costs:
- Consolidate components – Reduce unique component types to minimize inventory and kitting costs
- Increase volumes – Manufacture in bulk to lower per unit costs through scale
- Standardize designs – Minimize customization and reuse common PCBs across products
- Simplify board layout – Use less layers, looser spacing, avoid blind/buried vias
- Free DFM checks – Get design feedback to optimize manufacturability
- Compare BOM costs – Price components from different suppliers, including salvaged and excess parts
- Use DFM test boards – Validate assembly process before full production
- Qualify multiple vendors – Keep 2 to 3 providers in loop for competitive pricing
- Negotiate cost drivers – Focus on high-cost items like special components, testing needs etc.
With careful design choices and supplier selection, companies can reduce PCB assembly costs significantly.
Choosing the Right PCB Assembly Partner
In addition to pricing, choosing the right assembly partner involves evaluating multiple factors:
- Technical capabilities – Evaluate production capacity, certifications, expertise with complex boards, quality processes etc.
- Geographic location – Consider delivery timelines, logistics costs and production flexibility needs.
- Financial stability – Review company size, years in business, customer base to assess long-term viability.
- Customer service – How responsive and transparent is the vendor in resolving issues and communicating status.
- Quality – Review defect rates, quality certifications, inspection processes employed by the vendor.
- IP protection – Choose vendors who follow secure design transfer protocols and have NDAs in place.
Electronics OEMs must align PCB assembly partners with their specific technical needs, volumes, budgets and business goals for a successful long-term relationship.
FAQs on PCB Assembly Pricing
Here are some common questions around PCB assembly costs answered:
Q: How are PCB assembly costs estimated initially?
A: Vendors typically need the Gerber files, BOM and any special instructions to estimate costs. The Gerber files are reviewed to gauge complexity. The BOM provides component costs. Some key requirements like lead time, testing needs etc. also factor into the estimate.
Q: What are typical PCB assembly lead times?
A: Assembly lead times vary from 3 days to 2 weeks normally. Simpler boards can be assembled faster owing to lower complexity and easier component sourcing. High-mix boards take longer for programming and procuring parts.
Q: Does assembling in China reduce costs vs. USA or Europe?
A: Yes, typically costs in China are 30% to 50% lower for PCB assembly compared to the US or Europe. Other regions like Eastern Europe, Southeast Asia offer cost savings too. Lower labor costs are the primary driver though other overheads are also cheaper.
Q: How can I get accurate component pricing?
A: The PCB assembly vendor can provide current accurate component pricing by doing a live market check at time of quote. Alternatively, you can contact distributors like Digikey, Mouser, Arrow etc. to check latest part prices yourself.
Q: What are typical NRE charges for new PCB assembly projects?
A: NRE cost depends on complexity but often ranges from $250-$1000 for simple boards and up to $3000 or more for complex boards requiring extensive engineering review and test fixture creation.
Conclusion
PCB assembly pricing depends on a variety of factors. While it varies considerably based on complexity, volume, lead time and other requirements, having an understanding of the key cost drivers helps estimate budgets.
Ongoing engagement with assembly partners, right from design stage itself, is crucial as they can provide valuable DFM feedback and component recommendations to optimize manufacturability and cost.
With meticulous upfront planning and design choices, electronics OEMs can secure quality PCB assembly services at a favorable cost point and accelerate time to market.
0 Comments