What is Automated X-Ray Inspection (AXI)?
Automated X-Ray Inspection (AXI) is an advanced non-destructive testing method used to examine the internal structure of PCBs. It utilizes X-rays to create high-resolution images of the PCB, allowing for the detection of various defects and anomalies. AXI systems are equipped with state-of-the-art software that analyzes these images and identifies potential issues, such as:
- Solder joint defects (e.g., voids, bridges, insufficient solder)
- Component placement errors
- Broken or missing components
- Shorts and opens in the circuit
- Foreign object debris (FOD)
By detecting these issues early in the manufacturing process, AXI helps PCB assembly companies improve the quality and reliability of their products while reducing costs associated with rework and repairs.
Benefits of AXI in PCB Assembly
The implementation of AXI in PCB assembly offers several significant benefits, including:
-
Improved Quality: AXI systems can detect defects that may be missed by manual inspection or other automated inspection methods, such as automated optical inspection (AOI). This leads to higher quality PCBs with fewer defects and improved reliability.
-
Increased Efficiency: AXI systems can inspect PCBs at a much faster rate than manual inspection, allowing for higher throughput and reduced production times. This increased efficiency translates to lower costs and faster time-to-market for PCB assembly companies.
-
Non-Destructive Testing: Unlike some other testing methods, AXI does not damage or alter the PCB during the inspection process. This non-destructive nature allows for 100% inspection of all PCBs without the risk of rendering them unusable.
-
Detailed Failure Analysis: AXI systems generate detailed images and data that can be used for failure analysis and process improvement. By analyzing the root causes of defects, PCB assembly companies can make necessary adjustments to their processes to prevent future occurrences.
-
Compliance with Industry Standards: Many industries, such as aerospace, defense, and medical, have strict quality requirements for PCBs. AXI helps PCB assembly companies meet these standards by providing a reliable and comprehensive inspection method.
Leading PCB Assembly Companies with AXI Capabilities
Several PCB assembly companies have recognized the benefits of AXI and have incorporated this technology into their manufacturing processes. Some of the leading companies in this field include:
1. Jabil Circuit
Jabil Circuit is a global manufacturing services company that offers a wide range of services, including PCB assembly. The company has invested heavily in AXI Technology to ensure the highest quality standards for its customers. Jabil’s AXI systems are integrated into its manufacturing lines, providing real-time feedback and allowing for quick identification and correction of defects.
2. Flex Ltd.
Flex Ltd. is a multinational electronics manufacturing company that specializes in PCB assembly and other electronic manufacturing services. The company has implemented AXI technology in its facilities worldwide, ensuring consistent quality and reliability across its global operations. Flex’s AXI systems are complemented by a team of experienced engineers who analyze the data and make necessary process improvements.
3. Sanmina Corporation
Sanmina Corporation is a leading electronics manufacturing services company that offers PCB assembly services to a wide range of industries, including medical, automotive, and aerospace. The company has adopted AXI technology to meet the stringent quality requirements of these industries. Sanmina’s AXI systems are fully integrated with its manufacturing execution system (MES), allowing for seamless data collection and analysis.
4. Celestica Inc.
Celestica Inc. is a global electronics manufacturing services company that provides PCB assembly services to customers in various industries, such as aerospace, defense, and telecommunications. The company has invested in AXI technology to enhance its quality control processes and meet the high reliability standards demanded by its customers. Celestica’s AXI systems are supported by a team of skilled technicians and engineers who ensure optimal performance and results.
5. Plexus Corp.
Plexus Corp. is a leading electronics manufacturing services company that offers PCB assembly services to customers in the healthcare, industrial, and communications sectors. The company has integrated AXI technology into its manufacturing processes to provide the highest levels of quality and reliability. Plexus’s AXI systems are complemented by a comprehensive quality management system that includes regular audits and continuous improvement initiatives.
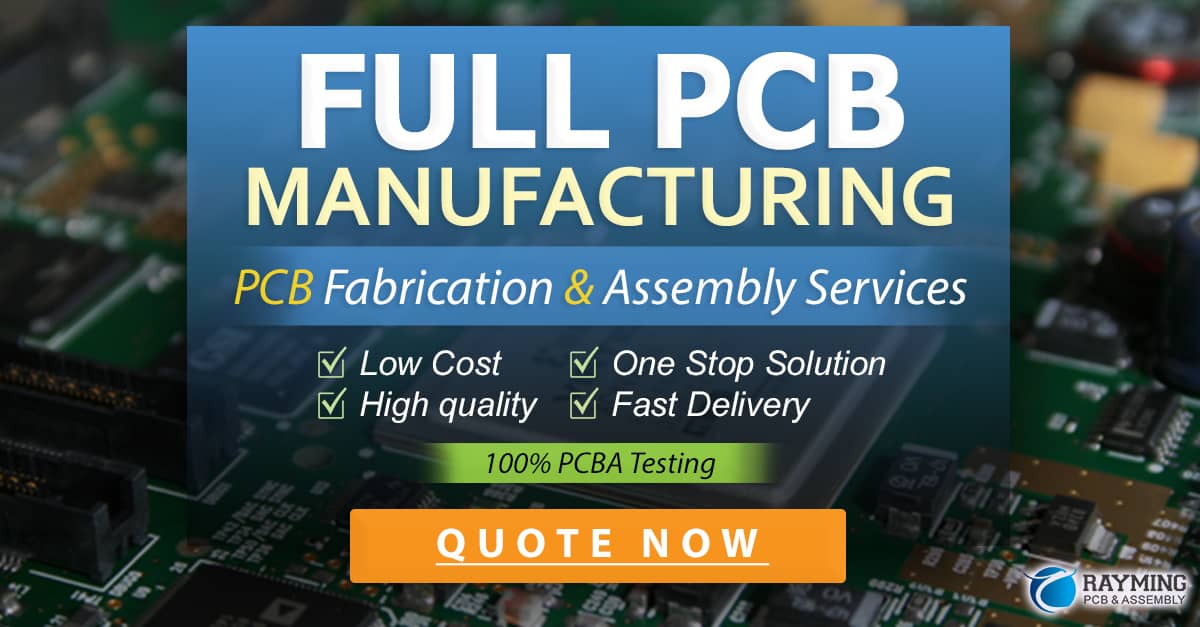
Case Studies
To further illustrate the benefits of AXI in PCB assembly, let’s take a look at a few case studies from companies that have successfully implemented this technology:
Case Study 1: Aerospace PCB Assembly
An aerospace company partnered with a PCB assembly company that utilizes AXI technology to manufacture high-reliability PCBs for aircraft systems. The AXI system detected a small void in a critical solder joint that had been missed by manual inspection. By identifying and correcting this defect early in the manufacturing process, the PCB assembly company prevented a potential failure in the field, which could have had serious consequences for the aircraft and its passengers.
Case Study 2: Medical Device PCB Assembly
A medical device manufacturer required PCBs with extremely high reliability for use in a life-supporting system. The PCB assembly company chosen for this project employed AXI technology to ensure the highest quality standards were met. The AXI system identified a component placement error that would have caused the device to malfunction. By detecting and correcting this issue, the PCB assembly company ensured the medical device would perform as intended, potentially saving lives.
Case Study 3: Automotive PCB Assembly
An automotive electronics supplier needed PCBs for a critical safety system in a new vehicle model. The PCB assembly company selected for this project utilized AXI technology to inspect the boards for defects. The AXI system discovered a small foreign object debris (FOD) lodged between two components, which could have caused a short circuit. By removing the FOD and verifying the integrity of the PCB, the assembly company prevented a potential safety hazard and ensured the reliable operation of the vehicle’s safety system.
FAQs
-
Q: How does AXI compare to other inspection methods, such as automated optical inspection (AOI)?
A: AXI and AOI are complementary inspection methods. AOI is effective at detecting surface-level defects, while AXI excels at identifying internal defects and anomalies that may not be visible to AOI systems. Using both methods together provides a comprehensive inspection solution for PCB assembly. -
Q: Can AXI be used for both single-sided and double-sided PCBs?
A: Yes, AXI systems can inspect both single-sided and double-sided PCBs. The X-rays penetrate through the entire board, allowing for the examination of solder joints, components, and other features on both sides of the PCB. -
Q: How long does an AXI inspection take?
A: The duration of an AXI inspection depends on factors such as the size and complexity of the PCB, the resolution of the X-ray images, and the specific AXI system being used. However, AXI inspections are generally much faster than manual inspection, with some systems capable of inspecting up to 80 PCBs per hour. -
Q: Are there any limitations to AXI technology?
A: While AXI is a powerful inspection method, it does have some limitations. For example, AXI may have difficulty detecting certain types of defects, such as hairline cracks in components or solder joints. Additionally, the initial investment in AXI equipment can be substantial, which may be a barrier for some smaller PCB assembly companies. -
Q: How do PCB assembly companies ensure their AXI systems are operating correctly?
A: PCB assembly companies typically have quality control procedures in place to ensure their AXI systems are functioning properly. This may include regular calibration and maintenance of the equipment, as well as the use of reference PCBs with known defects to validate the system’s performance. Many companies also employ skilled technicians and engineers who are trained to operate and maintain the AXI systems.
Conclusion
Automated X-Ray Inspection (AXI) has revolutionized the PCB assembly industry, providing a powerful tool for ensuring the quality and reliability of PCBs. By detecting internal defects and anomalies that may not be visible to other inspection methods, AXI helps PCB assembly companies improve their products, reduce costs, and meet the stringent requirements of various industries. As technology continues to advance, it is likely that more and more PCB assembly companies will adopt AXI to stay competitive and deliver the highest quality products to their customers.
Company | AXI Implementation | Industries Served | Key Benefits |
---|---|---|---|
Jabil Circuit | Integrated into manufacturing lines | Various | Real-time feedback, quick defect identification and correction |
Flex Ltd. | Implemented in facilities worldwide | Various | Consistent quality and reliability across global operations |
Sanmina Corporation | Integrated with manufacturing execution system (MES) | Medical, automotive, aerospace | Seamless data collection and analysis |
Celestica Inc. | Supported by skilled technicians and engineers | Aerospace, defense, telecommunications | Optimal performance and results |
Plexus Corp. | Complemented by comprehensive quality management system | Healthcare, industrial, communications | Highest levels of quality and reliability |
In conclusion, the adoption of AXI technology by leading PCB assembly companies demonstrates the industry’s commitment to delivering high-quality, reliable products to customers across various sectors. As the demand for advanced electronics continues to grow, the role of AXI in PCB assembly will only become more critical, ensuring that PCBs meet the ever-increasing standards of performance and reliability.
0 Comments