Keyword: Aerospace PCB
Miniaturization and High-Density Interconnect (HDI) PCBs
One of the most significant trends in aerospace PCBs is miniaturization and the adoption of high-density interconnect (HDI) technology. As aerospace systems become more compact and sophisticated, there is a growing need for smaller, lighter, and more efficient PCBs. HDI PCBs feature finer traces, smaller vias, and higher layer counts, enabling the integration of more components and functionality into a smaller footprint.
Benefits of HDI PCBs in aerospace applications:
– Reduced weight and size
– Improved signal integrity and speed
– Enhanced thermal management
– Increased reliability and durability
Advanced Materials for Aerospace PCBs
The aerospace industry requires PCBs that can withstand extreme temperatures, vibrations, and exposure to harsh chemicals and radiation. To meet these challenges, manufacturers are developing advanced materials specifically designed for aerospace applications.
Some of the advanced materials used in aerospace PCBs include:
Material | Properties | Applications |
---|---|---|
Polyimide | High temperature resistance, excellent mechanical strength | High-temperature environments, flexible PCBs |
Teflon (PTFE) | Low dielectric constant, high thermal stability | High-frequency applications, radar systems |
Ceramic | Excellent thermal conductivity, high dielectric strength | High-power applications, RF and microwave circuits |
Metal-core | Enhanced thermal dissipation, improved mechanical stability | Power electronics, LED lighting systems |
Embedded Components and 3D PCB Design
Embedded components and 3D PCB design techniques are gaining traction in the aerospace industry as a means to further reduce PCB size and improve performance. By embedding components within the PCB substrate, designers can create more compact and integrated solutions.
Advantages of embedded components and 3D PCB design:
– Reduced PCB footprint and overall system size
– Improved signal integrity and reduced noise
– Enhanced thermal management and heat dissipation
– Increased reliability and protection against environmental factors
Flexible and Rigid-Flex PCBs
Flexible and rigid-flex PCBs are becoming increasingly popular in aerospace applications due to their ability to conform to complex shapes and withstand repeated flexing and bending. These PCBs offer several advantages over traditional rigid PCBs, including:
- Reduced weight and increased flexibility
- Improved shock and vibration resistance
- Enhanced durability and reliability
- Simplified assembly and reduced interconnections
Flexible and rigid-flex PCBs find applications in various aerospace systems, such as:
– Avionics displays and control panels
– Satellite solar arrays and deployable structures
– In-flight entertainment systems
– Wearable devices for pilots and crew members
Additive Manufacturing and 3D Printed Electronics
Additive manufacturing, also known as 3D printing, is emerging as a promising technology for the fabrication of aerospace PCBs. 3D printing allows for the creation of complex geometries and customized designs that are difficult or impossible to achieve with traditional manufacturing methods.
Benefits of additive manufacturing in aerospace PCB production:
– Rapid prototyping and iterative design
– Customization and on-demand manufacturing
– Reduced waste and material consumption
– Potential for embedded electronics and multi-functional structures
Aerospace PCBs for Harsh Environments
Aerospace PCBs must be designed to withstand the unique challenges posed by the extreme conditions encountered in aircraft and spacecraft operations. These harsh environments include:
- Wide temperature ranges (from -55°C to +125°C or higher)
- High altitude and low atmospheric pressure
- Exposure to radiation and cosmic rays
- Vibration and mechanical stress
- Exposure to chemicals and fluids (e.g., fuel, hydraulic fluid)
To ensure reliable performance in these conditions, aerospace PCBs employ various techniques, such as:
- Conformal coating and encapsulation for environmental protection
- Ruggedized connectors and high-reliability components
- Thermal management solutions (e.g., heat sinks, thermal vias)
- Redundant circuits and fault-tolerant design
Testing and Qualification of Aerospace PCBs
Given the critical nature of aerospace applications, PCBs used in this industry must undergo rigorous testing and qualification processes to ensure their reliability and performance. Some of the key testing and qualification standards for aerospace PCBs include:
- IPC-6012 (Qualification and Performance Specification for Rigid Printed Boards)
- IPC-6013 (Qualification and Performance Specification for Flexible Printed Boards)
- IPC-6018 (Qualification and Performance Specification for High-Frequency (Microwave) Printed Boards)
- MIL-PRF-31032 (Performance Specification for Printed Circuit Board Assemblies)
These standards cover various aspects of PCB design, fabrication, and assembly, including:
– Material selection and characterization
– Dimensional tolerances and layer registration
– Hole quality and plating requirements
– Surface finish and soldermask requirements
– Electrical testing and continuity
– Environmental testing (e.g., thermal cycling, vibration, humidity)
Compliance with these standards ensures that aerospace PCBs meet the necessary quality, reliability, and performance criteria for their intended applications.
Frequently Asked Questions (FAQs)
-
What are the main differences between aerospace PCBs and standard commercial PCBs?
Aerospace PCBs are designed to withstand harsher environments and more demanding conditions compared to standard commercial PCBs. They often require specialized materials, advanced manufacturing techniques, and rigorous testing to ensure reliable performance in extreme temperatures, high altitudes, and under exposure to radiation and mechanical stress. -
What are the benefits of using HDI PCBs in aerospace applications?
HDI (High-Density Interconnect) PCBs offer several benefits for aerospace applications, including reduced weight and size, improved signal integrity and speed, enhanced thermal management, and increased reliability and durability. By enabling the integration of more components and functionality into a smaller footprint, HDI PCBs contribute to the miniaturization and performance optimization of aerospace systems. -
How do flexible and rigid-flex PCBs improve the design of aerospace systems?
Flexible and rigid-flex PCBs offer improved design flexibility, allowing them to conform to complex shapes and withstand repeated flexing and bending. They provide advantages such as reduced weight, increased flexibility, improved shock and vibration resistance, and enhanced durability and reliability. These characteristics make them well-suited for applications like avionics displays, satellite solar arrays, and in-flight entertainment systems. -
What role does additive manufacturing play in the production of aerospace PCBs?
Additive manufacturing, or 3D printing, is emerging as a promising technology for the fabrication of aerospace PCBs. It enables rapid prototyping, customization, and on-demand manufacturing of complex geometries and customized designs that are difficult to achieve with traditional manufacturing methods. Additive manufacturing also offers the potential for embedded electronics and multi-functional structures, further expanding the design possibilities for aerospace PCBs. -
What are the key testing and qualification standards for aerospace PCBs?
Aerospace PCBs must undergo rigorous testing and qualification processes to ensure their reliability and performance in the demanding conditions of aircraft and spacecraft operations. Key standards include IPC-6012 (rigid PCBs), IPC-6013 (flexible PCBs), IPC-6018 (high-frequency PCBs), and MIL-PRF-31032 (PCB assemblies). These standards cover various aspects of PCB design, fabrication, and assembly, including material selection, dimensional tolerances, hole quality, surface finish, electrical testing, and environmental testing.
Conclusion
The aerospace industry continues to push the boundaries of technology, and PCBs play a crucial role in enabling the development of advanced aircraft and spacecraft systems. From miniaturization and HDI technology to advanced materials and embedded components, the trends in aerospace PCBs are driven by the need for improved performance, reliability, and functionality in extreme environments.
As the industry evolves, we can expect to see further advancements in PCB design, manufacturing, and testing techniques. Flexible and rigid-flex PCBs, additive manufacturing, and the adoption of new materials will likely shape the future of aerospace PCBs. By staying at the forefront of these trends, PCB manufacturers and aerospace companies can collaborate to develop innovative solutions that meet the ever-increasing demands of the aerospace industry.
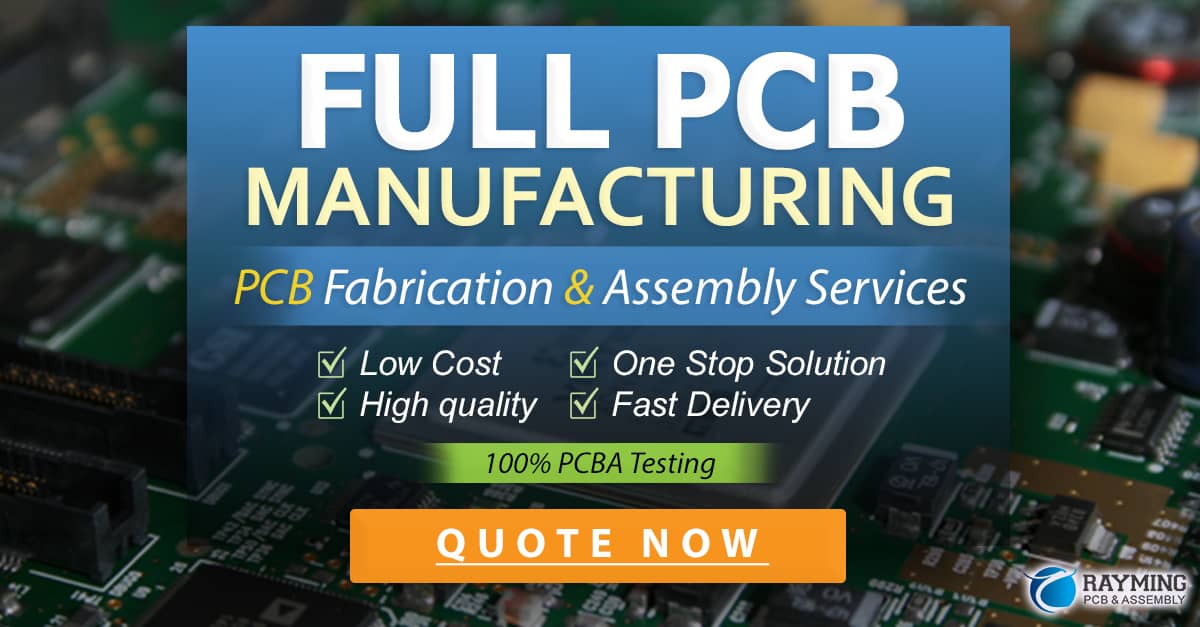
0 Comments