Introduction to Aerospace PCBs
Printed Circuit Boards (PCBs) are the backbone of modern electronics, and this is especially true in the aerospace industry. Aerospace PCBs are designed to withstand extreme conditions such as high temperatures, vibrations, and radiation while maintaining reliable performance. These PCBs are critical components in various aerospace applications, including satellites, aircraft, and spacecraft.
In this comprehensive guide, we will delve into the world of aerospace PCB assembly and design, covering essential aspects such as materials, manufacturing processes, testing, and best practices.
Key Characteristics of Aerospace PCBs
Aerospace PCBs have unique characteristics that set them apart from standard PCBs used in consumer electronics. These characteristics ensure that the PCBs can function reliably in the harsh environments encountered in aerospace applications.
1. High Reliability
Aerospace PCBs must maintain high reliability to ensure the safety and success of missions. Failure of these PCBs can lead to catastrophic consequences, making reliability a top priority in their design and manufacturing.
2. Resistance to Extreme Conditions
Aerospace PCBs are exposed to various extreme conditions, including:
- Wide temperature ranges (-55°C to +125°C)
- High levels of vibration and shock
- Exposure to radiation and cosmic rays
- Low atmospheric pressure
The PCBs must be designed and manufactured to withstand these conditions without compromising performance.
3. Lightweight and Compact Design
Weight and space are critical factors in aerospace applications. Aerospace PCBs are designed to be lightweight and compact to minimize the overall weight of the aircraft or spacecraft while maximizing functionality within limited space.
4. Long Lifespan
Aerospace PCBs are expected to have a long lifespan, often exceeding 15-20 years. This requirement calls for robust design, high-quality materials, and thorough testing to ensure long-term reliability.
Materials Used in Aerospace PCBs
The choice of materials is crucial in the design and manufacturing of aerospace PCBs. These materials must offer excellent electrical and mechanical properties while withstanding the harsh environmental conditions encountered in aerospace applications.
1. Substrate Materials
Common substrate materials used in aerospace PCBs include:
- Polyimide (PI): Known for its high heat resistance, flexibility, and excellent electrical properties.
- FR-4: A cost-effective and widely used substrate material with good mechanical and electrical properties.
- Polytetrafluoroethylene (PTFE): Offers low dielectric constant, low loss, and high temperature resistance.
2. Conductor Materials
Copper is the most common conductor material used in aerospace PCBs due to its excellent electrical conductivity and thermal properties. However, other materials such as silver, gold, and copper alloys may be used for specific applications or to enhance corrosion resistance.
3. Solder Mask and Silkscreen
Solder mask and silkscreen materials used in aerospace PCBs must be able to withstand high temperatures and provide clear markings for easy identification and assembly.
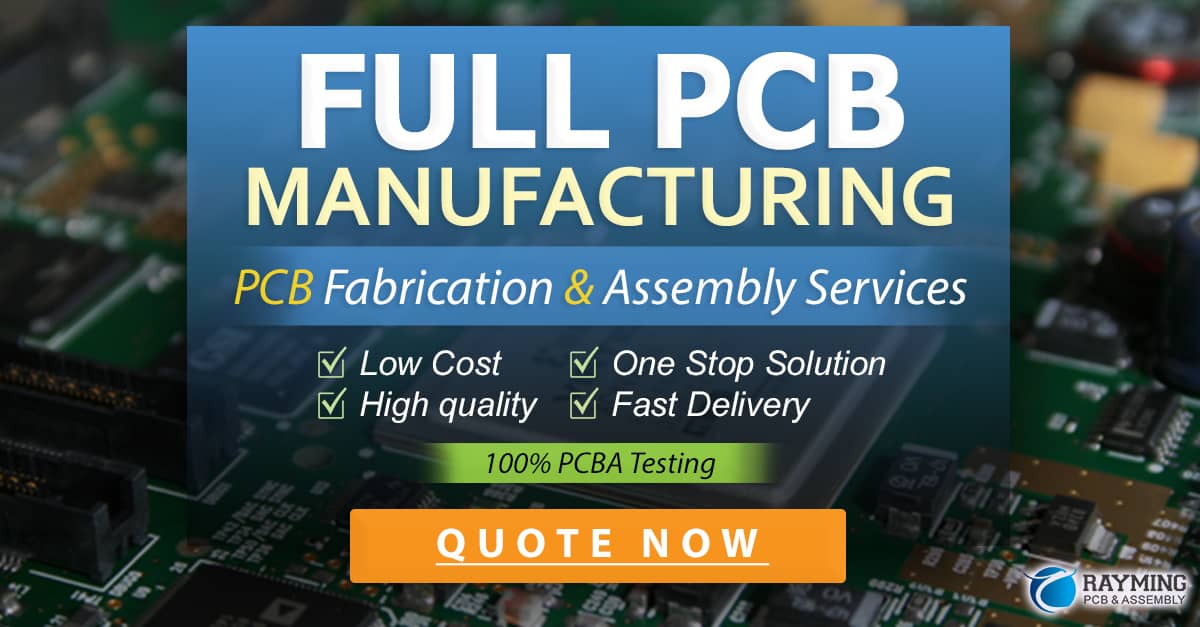
Aerospace PCB Manufacturing Processes
The manufacturing processes for aerospace PCBs are more stringent than those for standard PCBs to ensure the highest level of quality and reliability.
1. PCB Fabrication
Aerospace PCB fabrication involves the following key steps:
- Designing the PCB layout using specialized software
- Preparing the substrate material
- Applying the conductor pattern using photolithography or etching
- Laminating multiple layers (for multilayer PCBs)
- Drilling and plating through-holes
- Applying solder mask and silkscreen
2. PCB Assembly
After fabrication, the PCB undergoes the assembly process, which includes:
- Solder paste application using stencils or screen printing
- Component placement using pick-and-place machines or manual assembly
- Reflow soldering to establish electrical connections
- Inspection and testing to ensure proper assembly
3. Quality Control and Inspection
Strict quality control measures are implemented throughout the manufacturing process to ensure that aerospace PCBs meet the required specifications. This includes:
- Visual inspection
- Automated Optical Inspection (AOI)
- X-ray inspection
- Electrical testing
- Environmental testing (thermal cycling, vibration, etc.)
Aerospace PCB Design Considerations
Designing aerospace PCBs requires careful consideration of various factors to ensure optimal performance and reliability.
1. Signal Integrity
Maintaining signal integrity is crucial in aerospace PCBs to ensure accurate data transmission and prevent signal degradation. This involves:
- Proper impedance matching
- Minimizing crosstalk and electromagnetic interference (EMI)
- Careful routing and layer stackup design
2. Thermal Management
Aerospace PCBs must be designed to dissipate heat efficiently to prevent overheating and ensure reliable operation. This can be achieved through:
- Proper component placement
- Use of thermal vias and heat sinks
- Selection of materials with good thermal conductivity
3. Vibration and Shock Resistance
To withstand high levels of vibration and shock, aerospace PCBs must incorporate:
- Robust mechanical design
- Proper component mounting and securing
- Use of vibration-dampening materials
4. Electromagnetic Compatibility (EMC)
Aerospace PCBs must be designed to minimize electromagnetic interference (EMI) and ensure electromagnetic compatibility (EMC) with other electronic systems. This involves:
- Proper grounding and shielding
- Filtering of power supplies
- Careful routing of high-speed signals
Testing and Certification of Aerospace PCBs
Aerospace PCBs undergo rigorous testing and certification processes to ensure they meet the stringent requirements for reliability and performance.
1. Environmental Testing
Environmental testing simulates the harsh conditions aerospace PCBs will encounter during operation. This includes:
- Thermal cycling
- Vibration and shock testing
- Altitude testing
- Humidity testing
2. Functional Testing
Functional testing verifies that the PCB performs as intended and meets the specified requirements. This includes:
- In-circuit testing (ICT)
- Boundary scan testing
- Functional testing under various environmental conditions
3. Certification and Compliance
Aerospace PCBs must comply with various industry standards and certifications, such as:
- IPC (Association Connecting Electronics Industries) standards
- MIL-PRF-31032 (Performance Specification for Printed Circuit Board Assemblies)
- DO-160 (Environmental Conditions and Test Procedures for Airborne Equipment)
- AS9100 (Quality Management Systems – Requirements for Aviation, Space, and Defense Organizations)
Best Practices for Aerospace PCB Assembly and Design
To ensure the success of aerospace PCB projects, follow these best practices:
- Collaborate closely with experienced aerospace PCB manufacturers and assembly partners
- Use high-quality, aerospace-grade materials and components
- Implement strict quality control measures throughout the manufacturing process
- Conduct thorough testing and certification to validate reliability and performance
- Stay up-to-date with the latest industry standards and guidelines
- Continuously monitor and improve processes to enhance quality and efficiency
FAQ
1. What is the main difference between aerospace PCBs and standard PCBs?
Aerospace PCBs are designed to withstand extreme environmental conditions, such as wide temperature ranges, high levels of vibration, and exposure to radiation. They also have more stringent requirements for reliability, long lifespan, and lightweight design compared to standard PCBs.
2. What are the most common substrate materials used in aerospace PCBs?
The most common substrate materials used in aerospace PCBs are polyimide (PI), FR-4, and polytetrafluoroethylene (PTFE). These materials offer excellent electrical and mechanical properties while withstanding the harsh environmental conditions encountered in aerospace applications.
3. Why is signal integrity important in aerospace PCB design?
Signal integrity is crucial in aerospace PCB design to ensure accurate data transmission and prevent signal degradation. This is achieved through proper impedance matching, minimizing crosstalk and electromagnetic interference (EMI), and careful routing and layer stackup design.
4. What types of environmental testing do aerospace PCBs undergo?
Aerospace PCBs undergo various environmental tests to simulate the harsh conditions they will encounter during operation. These tests include thermal cycling, vibration and shock testing, altitude testing, and humidity testing.
5. What are some key industry standards and certifications for aerospace PCBs?
Some key industry standards and certifications for aerospace PCBs include IPC standards, MIL-PRF-31032 (Performance Specification for Printed Circuit Board Assemblies), DO-160 (Environmental Conditions and Test Procedures for Airborne Equipment), and AS9100 (Quality Management Systems – Requirements for Aviation, Space, and Defense Organizations).
Conclusion
Aerospace PCBs are critical components in the success and safety of aerospace applications. By understanding the unique characteristics, materials, manufacturing processes, design considerations, and testing requirements of aerospace PCBs, engineers and manufacturers can ensure the development of reliable, high-performance electronic systems for the aerospace industry.
Collaborating with experienced aerospace PCB manufacturers, implementing strict quality control measures, and staying up-to-date with industry standards and best practices are essential for the success of aerospace PCB projects. As technology continues to advance, the aerospace industry will continue to push the boundaries of PCB design and manufacturing to enable more ambitious and innovative projects in the future.
0 Comments