Introduction to Automotive PCB Assembly
Automotive PCB (Printed Circuit Board) assembly is a crucial process in the manufacturing of electronic components for vehicles. As the automotive industry continues to evolve and incorporate more advanced technologies, the demand for high-quality, reliable, and efficient PCB assembly processes has never been greater. In this article, we will explore some of the top innovative strategies for automotive PCB assembly that are helping manufacturers stay ahead of the curve.
The Importance of Automotive PCB Assembly
Automotive PCBs are essential components in modern vehicles, powering everything from infotainment systems and advanced driver assistance systems (ADAS) to engine control units (ECUs) and sensors. These PCBs must be able to withstand harsh environmental conditions, including extreme temperatures, vibrations, and moisture, while maintaining optimal performance and reliability.
Effective automotive PCB assembly strategies not only ensure the quality and durability of these components but also help manufacturers streamline their production processes, reduce costs, and improve overall efficiency.
Innovative Strategies for Automotive PCB Assembly
1. Automated Assembly Processes
One of the most significant advancements in automotive PCB assembly is the increasing use of automated processes. Automated assembly lines, powered by robotics and advanced software, offer several benefits over traditional manual assembly methods:
- Increased speed and efficiency
- Improved accuracy and consistency
- Reduced human error and labor costs
- Enhanced scalability and flexibility
Automated assembly processes can handle a wide range of tasks, from component placement and soldering to inspection and testing. By leveraging these technologies, manufacturers can significantly reduce production times and improve overall product quality.
Examples of Automated Assembly Equipment
Equipment | Function |
---|---|
Pick-and-Place Machines | Accurately place components on PCBs at high speeds |
Reflow Ovens | Solder components to PCBs using precise temperature profiles |
Automated Optical Inspection (AOI) Systems | Detect assembly defects and ensure product quality |
2. Lean Manufacturing Principles
Lean manufacturing is a methodology that focuses on minimizing waste and maximizing value in production processes. By applying lean principles to automotive PCB assembly, manufacturers can:
- Reduce inventory and storage costs
- Improve process flow and efficiency
- Enhance product quality and customer satisfaction
- Foster a culture of continuous improvement
Key lean manufacturing techniques include:
- Just-in-Time (JIT) production
- Kanban systems for inventory management
- 5S workplace organization
- Kaizen continuous improvement
By implementing these techniques, automotive PCB assembly companies can streamline their operations, reduce lead times, and respond more quickly to changing market demands.
3. Design for Manufacturing (DFM)
Design for Manufacturing (DFM) is an approach that involves optimizing PCB designs to facilitate efficient and cost-effective assembly processes. By collaborating closely with PCB designers and incorporating DFM principles early in the design phase, manufacturers can:
- Reduce assembly complexity and costs
- Improve product reliability and performance
- Minimize the risk of assembly defects and rework
- Accelerate time-to-market
Some key DFM considerations for automotive PCB assembly include:
- Component selection and placement
- Pad and trace sizes
- Solder mask and silkscreen design
- Panelization and routing
By adopting a DFM mindset, automotive PCB assembly companies can ensure that their products are not only functionally superior but also easier and more cost-effective to manufacture.
4. Advanced Materials and Processes
As automotive electronics become more sophisticated, PCB assembly companies are exploring the use of advanced materials and processes to meet the demanding requirements of these applications. Some examples include:
-
High-Temperature Laminates: These materials can withstand the extreme temperatures encountered in automotive environments, ensuring the long-term reliability of PCBs.
-
Embedded Components: By embedding passive components within the PCB substrate, manufacturers can reduce assembly complexity, improve signal integrity, and minimize the overall size of the board.
-
Conformal Coatings: Applying specialized coatings to PCBs can protect them from moisture, dust, and other environmental hazards, enhancing their durability and performance in automotive applications.
-
Flexible and Rigid-Flex PCBs: These advanced PCB technologies offer greater design flexibility, improved reliability, and reduced assembly costs compared to traditional rigid PCBs.
By leveraging these advanced materials and processes, automotive PCB assembly companies can create products that are better suited to the unique challenges of the automotive industry.
5. Quality Control and Testing
Ensuring the highest levels of quality and reliability is critical in automotive PCB assembly. To achieve this, manufacturers must implement robust quality control and testing procedures throughout the production process. Some key strategies include:
-
In-Process Inspection: Conducting regular inspections at various stages of the assembly process helps identify and correct defects early, minimizing the risk of costly rework or product failures.
-
Automated Optical Inspection (AOI): Using advanced AOI systems to detect assembly defects, such as missing or misaligned components, can significantly improve product quality and reduce the need for manual inspection.
-
Functional Testing: Performing comprehensive functional tests on assembled PCBs ensures that they meet the required performance specifications and can withstand the rigors of automotive applications.
-
Traceability and Data Analysis: Implementing traceability systems and collecting data throughout the assembly process allows manufacturers to identify trends, optimize processes, and quickly respond to quality issues.
By prioritizing quality control and testing, automotive PCB assembly companies can deliver products that meet the stringent requirements of the automotive industry and maintain a competitive edge in the market.
The Future of Automotive PCB Assembly
As the automotive industry continues to evolve, PCB assembly companies must stay ahead of the curve by adopting new technologies and strategies. Some of the emerging trends and opportunities in automotive PCB assembly include:
-
Electric and Hybrid Vehicles: The growing demand for electric and hybrid vehicles is driving the development of advanced PCB technologies, such as high-voltage power electronics and battery management systems.
-
Autonomous Driving: As self-driving cars become a reality, PCB assembly companies will need to support the development of advanced sensors, communication systems, and processing units that enable these technologies.
-
5G and Connected Vehicles: The rollout of 5G networks and the increasing connectivity of vehicles will create new opportunities for PCB assembly companies in areas such as telematics, infotainment, and vehicle-to-everything (V2X) communication.
-
Miniaturization and High-Density Packaging: The trend towards smaller, more compact automotive electronics will require PCB assembly companies to develop advanced packaging technologies, such as 3D packaging and system-in-package (SiP) solutions.
By staying attuned to these trends and investing in the necessary technologies and skills, automotive PCB assembly companies can position themselves for success in the rapidly evolving automotive industry.
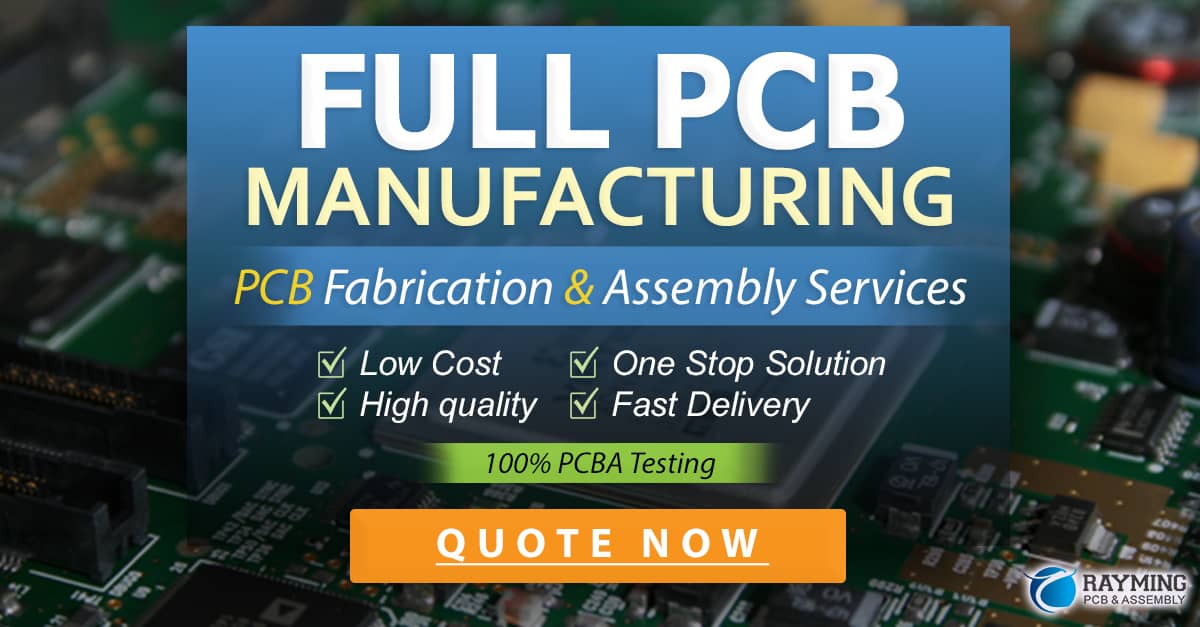
Conclusion
Automotive PCB assembly is a critical process that plays a vital role in the development of advanced vehicle technologies. By adopting innovative strategies such as automated assembly processes, lean manufacturing principles, design for manufacturing, advanced materials and processes, and robust quality control and testing procedures, PCB assembly companies can meet the demanding requirements of the automotive industry and stay ahead of the competition.
As the automotive landscape continues to evolve, PCB assembly companies must remain agile and adaptable, continuously seeking out new technologies and strategies to drive innovation and growth. By doing so, they can not only succeed in the present but also position themselves for long-term success in the exciting future of the automotive industry.
Frequently Asked Questions (FAQ)
- What are the key challenges in automotive PCB assembly?
-
Some of the main challenges include ensuring high reliability and durability in harsh automotive environments, managing complex supply chains and logistics, and keeping up with rapidly evolving technologies and customer requirements.
-
How can automated assembly processes benefit automotive PCB manufacturing?
-
Automated assembly processes can improve speed, accuracy, and consistency while reducing labor costs and human error. They also enable greater scalability and flexibility in production.
-
What is Design for Manufacturing (DFM), and why is it important in automotive PCB assembly?
-
DFM involves optimizing PCB designs to facilitate efficient and cost-effective assembly processes. By incorporating DFM principles early in the design phase, manufacturers can reduce assembly complexity, improve product reliability, and accelerate time-to-market.
-
What are some advanced materials and processes used in automotive PCB assembly?
-
Examples include high-temperature laminates, embedded components, conformal coatings, and flexible and rigid-flex PCBs. These technologies offer improved performance, reliability, and design flexibility for automotive applications.
-
How can quality control and testing procedures ensure the reliability of automotive PCBs?
- Implementing robust quality control and testing procedures, such as in-process inspection, automated optical inspection (AOI), functional testing, and traceability systems, can help identify and correct defects early, minimize product failures, and ensure that PCBs meet the stringent requirements of the automotive industry.
0 Comments