What to Look for in a PCB Automotive Assembly Partner
When selecting a PCB Assembly company for automotive applications, there are several key factors to consider:
1. Automotive-Specific Certifications and Standards
Look for a PCB assembly partner that holds relevant automotive certifications such as IATF 16949 (formerly TS 16949), which is the international standard for quality management systems in the automotive industry. Compliance with other standards like AEC-Q100 (Automotive Electronics Council – Qualification 100) for component reliability is also important.
2. Capability for High-Mix, Low-Volume Production
The automotive industry often requires smaller production runs of a wide variety of PCB designs, rather than mass production of a few standard boards. Choose a PCB assembler with the flexibility to handle high-mix, low-volume orders efficiently.
3. Experience with Automotive-Grade Components and Materials
Automotive PCBs must withstand harsh operating conditions including extreme temperatures, vibration, and exposure to moisture, chemicals, and electromagnetic interference (EMI). Partner with a PCB assembly company that has experience working with automotive-grade components and materials, such as high-temperature solder, conformal coatings, and underfill resins.
4. Robust Quality Control and Testing Procedures
Given the critical safety requirements of automotive electronics, it’s essential to work with a PCB assembler that has stringent quality control measures and comprehensive testing capabilities. These may include automated optical inspection (AOI), X-ray inspection, in-circuit testing (ICT), functional testing, and environmental stress screening (ESS).
5. Design for Manufacturing (DFM) Support
Look for a PCB assembly partner that offers design for manufacturing (DFM) analysis and feedback to optimize your PCB designs for manufacturability, reliability, and cost-effectiveness. DFM support can help catch potential issues early in the design process, before they lead to production delays or field failures.
Top PCB Assembly Companies for the Automotive Industry
Here are some of the leading PCB assembly companies serving the automotive industry:
Company | Headquarters | Key Automotive Capabilities |
---|---|---|
Jabil | St. Petersburg, FL, USA | IATF 16949 certified, high-volume production, global footprint |
Sanmina | San Jose, CA, USA | IATF 16949 certified, expertise in automotive sensors and ADAS |
Flex | Singapore | IATF 16949 certified, focus on connected car and autonomous driving |
Kimball Electronics | Jasper, IN, USA | IATF 16949 certified, experience with automotive infotainment and power systems |
Plexus | Neenah, WI, USA | IATF 16949 certified, rapid prototyping and NPI services for automotive |
Jabil
Jabil is one of the world’s largest contract manufacturers, with over 100 facilities in 29 countries. The company’s automotive division is IATF 16949 certified and specializes in high-volume production of PCBs for a wide range of automotive applications, including powertrain, lighting, safety systems, and infotainment. Jabil’s global footprint and scale make it a strong choice for large automotive OEMs and Tier 1 suppliers.
Sanmina
Sanmina is another global contract manufacturer with deep experience in the automotive industry. The company holds IATF 16949 certification and has particular expertise in assembling PCBs for automotive sensors, ADAS, and infotainment systems. Sanmina’s automotive customers benefit from its vertical integration capabilities, which include in-house PCB fabrication, cable and harness assembly, and enclosure manufacturing.
Flex
Flex (formerly Flextronics) is a Singapore-based contract manufacturer with a significant presence in the automotive industry. The company is IATF 16949 certified and focuses on PCB assembly for connected car technologies and autonomous driving systems. Flex has invested heavily in automotive-specific design and engineering services, including software development, to support its customers’ increasingly complex electronic requirements.
Kimball Electronics
Kimball Electronics is a mid-sized contract manufacturer based in Indiana, USA, with a strong focus on the automotive market. The company holds IATF 16949 certification and has extensive experience assembling PCBs for automotive infotainment systems, power management modules, and safety-critical applications. Kimball Electronics prides itself on its responsiveness and customer service, making it a good fit for automotive customers who value a more personalized approach.
Plexus
Plexus is a US-based contract manufacturer with a growing automotive business. The company is IATF 16949 certified and offers a range of services tailored to automotive customers, including rapid prototyping, new product introduction (NPI), and low-volume, high-mix production. Plexus has a global network of design and manufacturing facilities, with specialized automotive capabilities in the Americas, Europe, and Asia.
PCB Automotive Assembly Process Overview
The PCB assembly process for automotive applications typically involves the following steps:
-
Solder Paste Printing: A stencil is used to apply solder paste to the pads on the PCB where components will be placed.
-
Component Placement: Surface mount technology (SMT) components are placed onto the PCB using automated pick-and-place machines.
-
Reflow Soldering: The PCB is heated in a reflow oven to melt the solder paste and form electrical connections between the components and the board.
-
Through-Hole Assembly: Any through-hole components are inserted into the PCB and soldered in place, often using wave soldering or selective soldering techniques.
-
Inspection and Testing: The assembled PCB undergoes visual inspection, automated optical inspection (AOI), and electrical testing to ensure proper assembly and functionality.
-
Conformal Coating and Potting: For automotive applications, PCBs often receive a conformal coating or are potted in resin to protect against moisture, dust, and vibration.
-
Final Testing and Packaging: The finished PCB is subjected to additional functional testing and environmental stress screening (ESS) as needed, then packaged for shipment to the customer.
Throughout the process, strict quality control measures and traceability requirements must be followed to meet the demanding standards of the automotive industry.
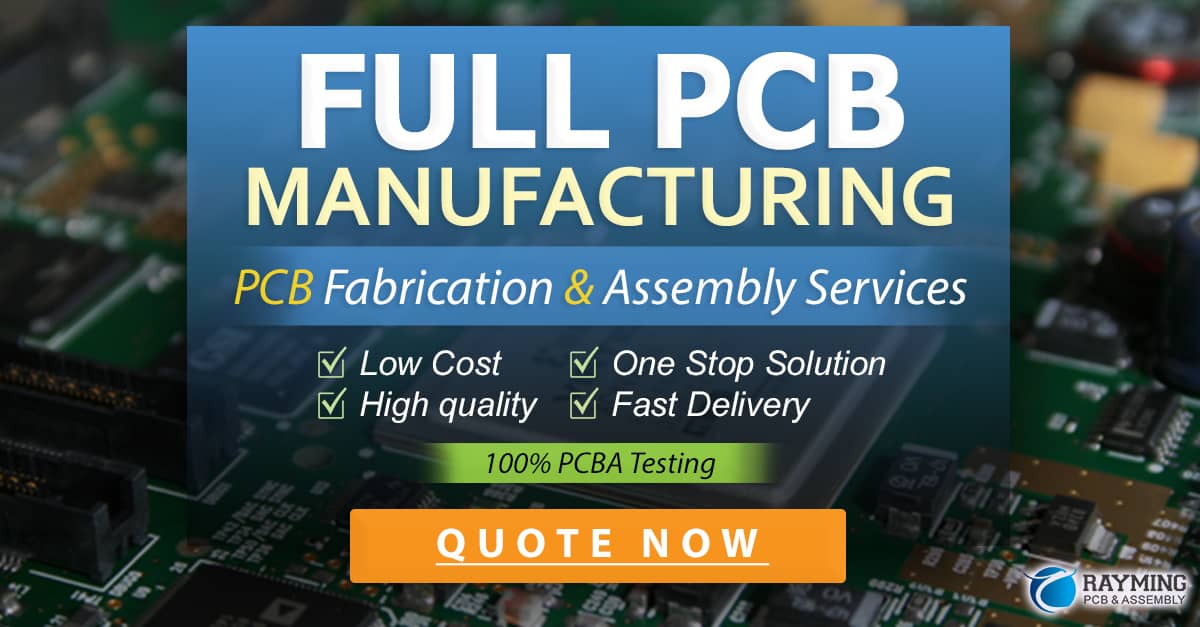
Common Automotive PCB Materials and Components
Automotive PCBs often use specialized materials and components to withstand the harsh operating environment inside a vehicle. Some common choices include:
-
High-Temperature FR-4 Substrate: Standard FR-4 PCB material may not be suitable for automotive applications due to its limited temperature range. High-temperature FR-4 variants, such as Isola’s TerraGreen or Panasonic’s R-1755V, offer better thermal stability and performance.
-
Ceramic Substrates: For high-power or high-frequency automotive applications, ceramic substrates like aluminum nitride (AlN) or alumina (Al2O3) may be used instead of FR-4. Ceramic PCBs offer superior thermal conductivity and dielectric properties.
-
High-Temperature Solder: Automotive PCBs often use lead-free solder alloys with higher melting points, such as SAC305 (96.5% tin, 3% silver, 0.5% copper) or SN100C (99.25% tin, 0.7% copper, 0.05% nickel), to withstand the elevated temperatures found in automotive environments.
-
Automotive-Grade Components: Electronic components used on automotive PCBs must be qualified to AEC-Q standards, which specify requirements for temperature range, reliability, and product change notifications. Common automotive-grade components include capacitors, resistors, connectors, and microcontrollers.
-
Shielding and EMI Protection: To protect against electromagnetic interference (EMI) from other vehicle systems or external sources, automotive PCBs may incorporate shielding measures such as metal shields, conductive gaskets, or EMI filters.
-
Ruggedized Connectors: Automotive PCBs often use specialized connectors designed to withstand vibration, shock, and temperature cycling. These may include board-to-board, wire-to-board, or sealed connectors with locking mechanisms or high-retention contacts.
Automotive PCB Design Considerations
Designing PCBs for automotive applications involves several unique considerations compared to other industries:
-
Temperature Range: Automotive PCBs must be designed to operate reliably across a wide temperature range, typically -40°C to +125°C or higher, depending on the specific application and location within the vehicle.
-
Vibration and Shock: PCBs in automotive environments are subjected to constant vibration and occasional shock loads. Proper component selection, mounting, and support strategies must be used to prevent solder joint failures or component detachment.
-
EMI and ESD Protection: Automotive PCBs must be designed with robust electromagnetic interference (EMI) and electrostatic discharge (ESD) protection measures to ensure reliable operation in the electrically noisy environment of a vehicle.
-
Signal Integrity: With the increasing data rates and frequencies used in modern automotive systems, maintaining signal integrity is critical. PCB designers must carefully manage impedance, crosstalk, and other signal integrity factors to ensure proper performance.
-
Size and Weight Constraints: Automotive PCBs are often designed for compact, lightweight packaging to minimize vehicle weight and fit within limited space. This may require the use of high-density interconnect (HDI) PCB technologies or flexible circuit boards.
-
Reliability and Lifecycle: Automotive PCBs are expected to operate reliably for the life of the vehicle, which may be 10-15 years or more. Designers must consider long-term reliability factors such as thermal cycling, corrosion resistance, and component obsolescence management.
-
Safety and Regulatory Compliance: PCBs used in safety-critical automotive systems must be designed and manufactured in compliance with relevant safety standards and regulations, such as ISO 26262 for functional safety or ECE R10 for electromagnetic compatibility (EMC).
By working closely with experienced automotive PCB assembly partners and following best practices for automotive PCB design, manufacturers can ensure that their electronic systems meet the demanding requirements of the automotive industry.
Frequently Asked Questions (FAQ)
1. What is the difference between IATF 16949 and ISO 9001 certification?
IATF 16949 is a quality management system standard specific to the automotive industry, while ISO 9001 is a general quality management standard applicable to any industry. IATF 16949 includes all the requirements of ISO 9001, plus additional automotive-specific requirements related to product safety, defect prevention, and continuous improvement. PCB assembly companies serving the automotive industry should hold IATF 16949 certification to demonstrate their commitment to meeting the strict quality standards of the automotive sector.
2. How do automotive PCBs differ from PCBs used in other industries?
Automotive PCBs are designed and manufactured to withstand the harsh operating conditions found in vehicles, including extreme temperatures, vibration, shock, and exposure to moisture, chemicals, and electromagnetic interference. They often use specialized materials, such as high-temperature FR-4 or ceramic substrates, and automotive-grade components that are qualified to AEC-Q standards. Automotive PCBs also must meet stringent reliability, safety, and regulatory requirements that may not apply to PCBs used in other industries.
3. What is the typical lead time for automotive PCB assembly?
Lead times for automotive PCB assembly can vary depending on factors such as the complexity of the design, the availability of materials and components, and the production schedule of the assembler. In general, automotive PCB assembly lead times may range from 4-12 weeks or more, with faster turnaround times possible for prototypes or small production runs. It’s important to work closely with your PCB assembly partner to plan for lead times and ensure that your production schedule is aligned with their capabilities.
4. How can I ensure the reliability of my automotive PCBs?
To ensure the reliability of automotive PCBs, it’s important to work with a PCB assembly partner that has experience in the automotive industry and follows best practices for design, manufacturing, and testing. This includes using automotive-grade materials and components, adhering to relevant quality and safety standards, and conducting thorough testing and inspection at every stage of the assembly process. Techniques such as design for manufacturability (DFM) analysis, reliability testing, and environmental stress screening (ESS) can help identify and mitigate potential reliability issues before they lead to field failures.
5. What should I look for in an automotive PCB assembly partner?
When choosing an automotive PCB assembly partner, look for a company that holds relevant certifications such as IATF 16949, has experience with automotive-specific materials and components, and offers a range of services tailored to the needs of automotive customers. These may include design for manufacturability (DFM) support, rapid prototyping, high-mix low-volume production, and comprehensive testing and inspection capabilities. It’s also important to consider factors such as the assembler’s quality control measures, technical expertise, customer service, and ability to meet your production schedule and cost targets. By selecting the right automotive PCB assembly partner, you can ensure the success of your electronic systems and stay competitive in the fast-moving automotive industry.
0 Comments