What is PCB Assembly?
PCB assembly is the process of soldering or mounting electronic components onto a printed circuit board (PCB). It is a crucial step in the manufacturing of electronic devices, as it involves attaching various components such as resistors, capacitors, integrated circuits (ICs), and connectors to the PCB. The assembled PCB then undergoes testing and quality control before being integrated into the final electronic product.
Types of PCB Assembly
There are two primary types of PCB assembly:
-
Through-hole assembly (THA): In this method, component leads are inserted through drilled holes in the PCB and soldered onto the opposite side of the board. Through-hole assembly is generally more robust and reliable, making it suitable for applications that require high mechanical stress or exposure to harsh environments.
-
Surface mount assembly (SMA): Surface mount technology (SMT) involves placing components directly onto the surface of the PCB and soldering them in place. SMT components are smaller and have shorter leads, allowing for higher component density and smaller board sizes. Surface mount assembly is faster and more cost-effective than through-hole assembly, making it the preferred choice for most modern electronic devices.
The PCB Assembly Process
The PCB assembly process typically involves the following steps:
1. Solder Paste Application
Solder paste, a mixture of tiny solder particles suspended in flux, is applied to the PCB’s contact pads using a stencil or solder paste printer. The stencil ensures that the solder paste is deposited accurately and consistently on the pads.
2. Component Placement
Surface mount components are placed onto the solder paste-covered pads using pick-and-place machines. These machines use computer-controlled nozzles or grippers to accurately position the components on the board at high speeds.
3. Reflow Soldering
The PCB with the placed components is then passed through a reflow oven. The oven heats the board to a specific temperature profile, causing the solder paste to melt and form a permanent electrical and mechanical connection between the components and the PCB.
4. Inspection and Testing
After the reflow soldering process, the assembled PCB undergoes visual inspection and automated optical inspection (AOI) to detect any defects or misaligned components. Electrical testing, such as in-circuit testing (ICT) or functional testing, may also be performed to ensure that the board functions as intended.
5. Through-hole Component Insertion and Wave Soldering (if required)
If the PCB design includes through-hole components, these components are inserted into the designated holes on the board. The board then passes through a wave soldering machine, which applies molten solder to the underside of the board, creating a connection between the component leads and the PCB.
6. Final Inspection and Packaging
The assembled PCB undergoes a final visual inspection and may be subjected to additional testing, such as boundary scan or functional testing. Once the board passes all quality control checks, it is cleaned, conformal coated (if required), and packaged for shipment.
Benefits of One-stop PCB Assembly Services
One-stop PCB assembly services offer numerous advantages for businesses and individuals looking to manufacture electronic devices. These benefits include:
-
Time and Cost Savings: By outsourcing PCB assembly to a one-stop service provider, companies can save time and money associated with setting up and maintaining an in-house assembly line. One-stop services eliminate the need for investing in expensive equipment, training staff, and managing inventory.
-
Expertise and Quality: One-stop PCB assembly providers have the necessary expertise, experience, and equipment to ensure high-quality assembly. They employ skilled technicians and use state-of-the-art machinery to produce reliable and consistent results.
-
Scalability and Flexibility: One-stop services can accommodate a wide range of production volumes, from small prototype runs to large-scale production. They can also handle various PCB designs and component types, allowing for greater flexibility in product development.
-
Access to Advanced Technologies: One-stop PCB assembly providers often invest in the latest technologies and equipment to stay competitive. By partnering with these providers, companies can access advanced assembly techniques and capabilities without the need for capital investment.
-
Streamlined Communication and Support: Working with a single service provider simplifies communication and project management. One-stop services often assign dedicated project managers to ensure smooth coordination and provide technical support throughout the assembly process.
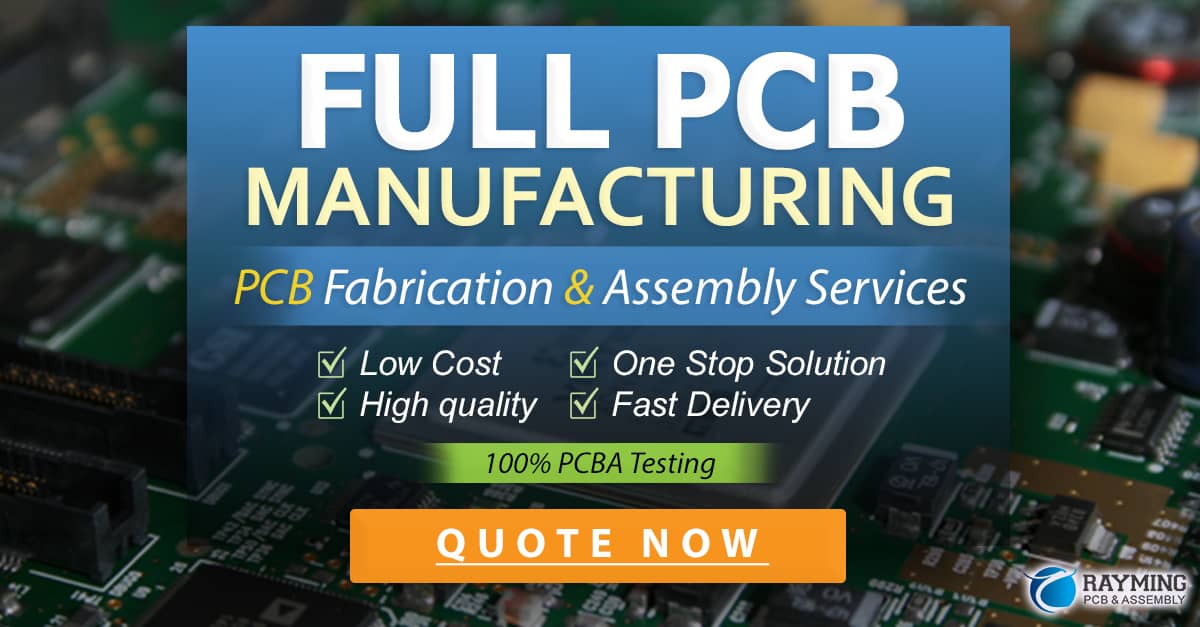
Choosing the Right One-stop PCB Assembly Service Provider
When selecting a one-stop PCB assembly service provider, consider the following factors:
-
Technical Capabilities: Ensure that the provider has the necessary equipment, expertise, and experience to handle your specific PCB assembly requirements. Consider their ability to work with different PCB types, component packages, and assembly techniques.
-
Quality Control and Certifications: Look for providers with robust quality control processes and relevant industry certifications, such as ISO 9001, IPC, or UL. These certifications demonstrate the provider’s commitment to quality and adherence to industry standards.
-
Production Capacity and Lead Times: Assess the provider’s production capacity and their ability to meet your desired lead times. Consider their flexibility in accommodating changes in production volume or schedule.
-
Customer Support and Communication: Choose a provider that offers reliable customer support and clear communication channels. Responsive and knowledgeable support teams can help address any issues or concerns promptly.
-
Pricing and Value-added Services: Compare pricing among different providers, but also consider the value-added services they offer, such as design support, testing, or logistics management. Strike a balance between cost and the overall value provided by the service provider.
PCB Assembly Techniques and Technologies
One-stop PCB assembly service providers employ various techniques and technologies to ensure efficient and high-quality assembly. Some of these include:
Surface Mount Technology (SMT)
Surface mount technology is the most common PCB assembly method, involving the placement of components directly onto the surface of the board. SMT offers several advantages, including:
- Smaller component sizes and higher component density
- Faster assembly speeds and lower production costs
- Improved electrical performance due to shorter lead lengths
Through-hole Technology (THT)
Through-hole technology involves inserting component leads through drilled holes in the PCB and soldering them on the opposite side. While THT is less common than SMT, it is still used for certain components that require greater mechanical strength or heat dissipation, such as:
- Connectors and sockets
- Power transformers and large capacitors
- High-power resistors and diodes
Mixed Technology (SMT and THT)
Some PCB designs require a combination of surface mount and through-hole components. One-stop PCB assembly providers are equipped to handle mixed technology assembly, ensuring the proper integration of both SMT and THT components on a single board.
Automated Optical Inspection (AOI)
Automated optical inspection systems use high-resolution cameras and advanced image processing algorithms to detect assembly defects, such as:
- Solder bridges or insufficient solder
- Misaligned or missing components
- Reversed or incorrect component polarities
AOI ensures consistent quality control and helps identify issues early in the assembly process, reducing the risk of defective products reaching the market.
X-ray Inspection
X-ray inspection is used to detect defects that are not visible to the naked eye or AOI systems, such as:
- Voids or cracks in ball grid array (BGA) solder joints
- Solder joint defects under components with hidden leads (e.g., flip-chips or package-on-package)
- Insufficient solder fill in through-holes
X-ray inspection provides a non-destructive means of assessing the quality of solder joints and ensuring the reliability of the assembled PCB.
Industry Standards and Certifications
One-stop PCB assembly service providers adhere to various industry standards and certifications to ensure consistent quality and reliability. Some of the key standards and certifications include:
IPC Standards
The Association Connecting Electronics Industries (IPC) develops and maintains standards for PCB design, fabrication, and assembly. Key IPC standards include:
- IPC-A-610: Acceptability of Electronic Assemblies
- IPC J-STD-001: Requirements for Soldered Electrical and Electronic Assemblies
- IPC-A-600: Acceptability of Printed Boards
Compliance with IPC standards ensures that PCB assemblies meet industry-accepted quality criteria and can withstand the intended operating conditions.
ISO 9001
ISO 9001 is an international standard for quality management systems. PCB assembly providers with ISO 9001 certification demonstrate their commitment to continuous improvement, customer satisfaction, and the consistent delivery of high-quality products and services.
UL Certification
Underwriters Laboratories (UL) is a global safety certification company that tests and certifies products to ensure they meet specific safety standards. PCB assembly providers with UL certification have demonstrated their ability to manufacture products that comply with UL’s safety requirements, which is particularly important for electronic devices used in critical applications or harsh environments.
Frequently Asked Questions (FAQ)
-
What is the minimum order quantity (MOQ) for PCB assembly services?
MOQs vary among service providers, but many one-stop PCB assembly companies offer low MOQs, sometimes as low as a single unit for prototype runs. Larger production runs may have higher MOQs to ensure cost-effectiveness. -
How long does the PCB assembly process typically take?
Lead times for PCB assembly depend on factors such as the complexity of the design, the type of components used, and the production volume. One-stop service providers can often provide lead times ranging from a few days for prototype assemblies to several weeks for large-scale production runs. -
Can one-stop PCB assembly services handle complex PCB designs?
Yes, most one-stop PCB assembly providers are equipped to handle a wide range of PCB designs, including complex multi-layer boards, high-density interconnect (HDI) designs, and flexible or rigid-flex PCBs. However, it is essential to discuss your specific requirements with the service provider to ensure they have the necessary capabilities. -
What file formats are required for PCB assembly?
One-stop PCB assembly providers typically require a set of design files, including: - Gerber files for PCB fabrication
- Bill of Materials (BOM) listing all components and their quantities
- Pick-and-place files specifying component locations on the board
-
Assembly drawings or instructions, if necessary
The service provider will provide guidance on the specific file formats and requirements for your project. -
How can I ensure the quality of the assembled PCBs?
To ensure the quality of the assembled PCBs, choose a one-stop service provider with a robust quality management system, adherence to industry standards (e.g., IPC, ISO), and advanced inspection techniques (e.g., AOI, X-ray). Discuss your quality requirements with the provider and request documentation, such as inspection reports or certificates of conformity, to verify that the assembled PCBs meet your specifications.
PCB Assembly Service | Benefits | Typical Lead Time | MOQ |
---|---|---|---|
Prototype Assembly | Fast turnaround, design validation | 1-5 days | 1-10 units |
Low-volume Production | Cost-effective for small batches, quick iterations | 1-2 weeks | 10-500 units |
High-volume Production | Economies of scale, consistent quality | 2-8 weeks | 500+ units |
Table 1: Comparison of PCB Assembly Services
Conclusion
One-stop PCB assembly services provide a comprehensive solution for businesses and individuals looking to streamline their electronic product development and manufacturing processes. By offering expertise, advanced technologies, and a wide range of capabilities, these service providers help clients save time, reduce costs, and ensure high-quality PCB assemblies.
When choosing a one-stop PCB assembly service provider, consider factors such as technical capabilities, quality control processes, production capacity, customer support, and overall value. By partnering with the right provider, you can leverage their expertise and resources to bring your electronic products to market quickly and efficiently.
As the electronics industry continues to evolve, one-stop PCB assembly services will play an increasingly crucial role in enabling innovation and supporting the development of cutting-edge technologies. By staying informed about the latest advancements in PCB assembly techniques and technologies, you can make informed decisions and stay ahead of the competition in this dynamic and fast-paced industry.
0 Comments