What is a PCB?
A printed circuit board (PCB) is a flat board made of insulating material with electrical connections printed or etched onto its surface. PCBs provide mechanical support and electrical interconnection for electronic components using conductive tracks, pads and other features.
PCBs are used in nearly all electronic products today, from simple devices like digital clocks to complex computer systems and telecommunications equipment. They enable the miniaturization and automation of electronic circuits.
Types of PCBs
There are several different types of printed circuit boards:
Single-Layer PCBs
Single-layer or single-sided PCBs have conductive copper traces printed on one side of the board. The components are soldered onto the same side as the copper layer. Single-layer boards are the simplest and least expensive type of PCB.
Double-Layer PCBs
Double-layer or double-sided PCBs have conductive copper traces printed on both sides of the insulating substrate. The two sides are connected with vias. Double-layer PCBs allow for a higher component density than single-layer.
Multi-Layer PCBs
Multi-layer PCBs have three or more conductive copper layers with insulating layers in between. The different layers are interconnected with vias. Multi-layer PCBs enable very high component density and complex circuits. They are used in advanced electronic devices.
Flexible PCBs
Flexible or flex PCBs are made with flexible insulating material like polyimide. This allows the PCB to bend and fold to fit into tight spaces or moving parts. Flex PCBs are often used in automotive electronics, medical devices, and consumer products.
Rigid-Flex PCBs
Rigid-flex PCBs combine rigid and flexible substrates into a single circuit. The rigid parts of the board contain most of the components while the flexible parts act as connectors between rigid sections. Rigid-flex PCBs are used when both high component density and flexibility are required.
PCB Composition
PCBs are composed of several layers:
Substrate
The substrate is the base insulating layer of the PCB. It provides mechanical support and electrical insulation. The most common PCB substrate material is FR4, a glass-reinforced epoxy laminate. Other substrates include paper, polyimide, and Teflon.
Copper
Copper foil is laminated onto the substrate to create the conductive layer for circuit traces, pads, and planes. The thickness of the copper layer is typically expressed in ounces per square foot, such as 1 oz, 2 oz, or 0.5 oz copper.
Solder Mask
The solder mask is a polymer layer applied over the outer copper layers. It protects the copper from oxidation and prevents solder bridges from forming. The solder mask gives PCBs their characteristic green color, although other colors like red, yellow, blue, and black are available.
Silkscreen
The silkscreen is the white text and symbols printed onto the PCB. It is used to label components, test points, and other features. The silkscreen helps with PCB assembly and troubleshooting.
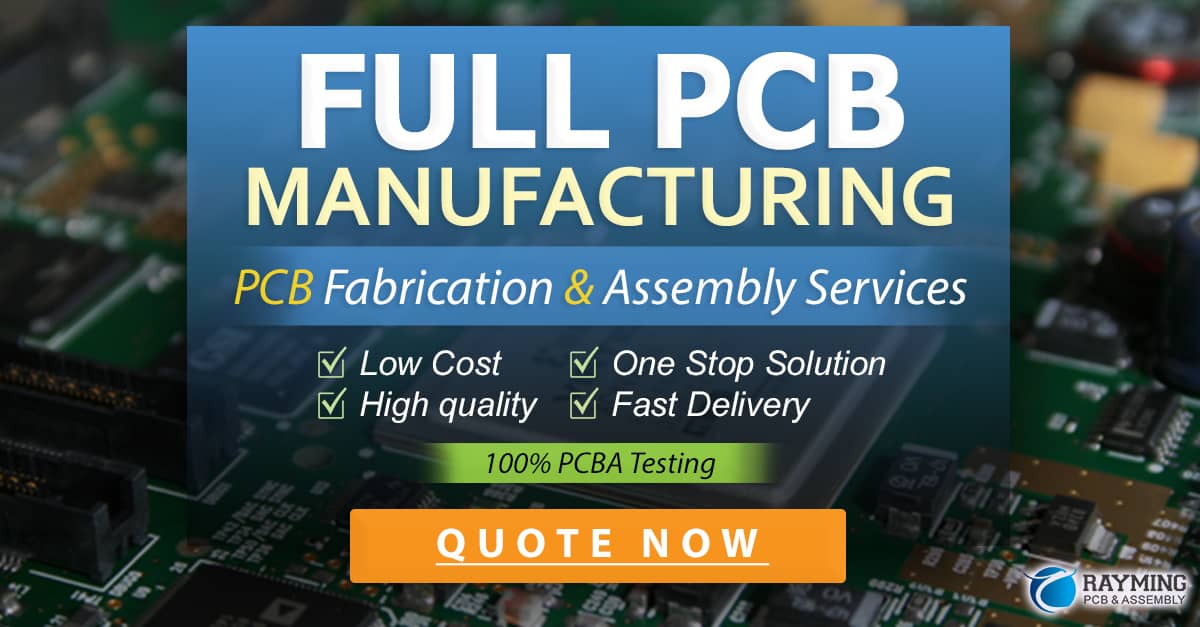
PCB Design
Designing a PCB involves several steps:
Schematic Capture
The first step is to create a schematic diagram of the electronic circuit. The schematic shows the components and their interconnections using standard symbols. It does not show the physical layout of the PCB.
Component Selection
The electronic components for the circuit are selected based on their specifications and availability. The component footprints and landing patterns must match the PCB layout.
PCB Layout
The PCB layout is created using electronic design automation (EDA) software. The software allows the designer to place components, route traces, and define manufacturing parameters. The layout must follow design rules for minimum trace width, spacing, hole size, etc.
Design Rule Check
The PCB layout undergoes a design rule check (DRC) to verify that it meets the manufacturing specifications. The DRC checks for errors like open circuits, short circuits, and acid traps.
Gerber Files
The final PCB layout is exported as a set of Gerber files. Gerber is the standard file format for PCB manufacturing. The Gerber files contain the information needed to fabricate the PCB, including the copper layers, drill holes, and silkscreen.
PCB Manufacturing
PCBs are manufactured using a multi-step process:
Printing
The PCB layout is printed onto a photosensitive film or directly onto the copper-clad substrate using a laser printer or photoplotter.
Etching
The unexposed areas of the photoresist are removed, leaving behind a protective mask in the shape of the circuit traces. The exposed copper is etched away using an acidic solution, leaving only the desired copper traces.
Drilling
Holes are drilled through the PCB to accommodate through-hole components and vias. The holes are typically drilled using a computer numerical control (CNC) machine.
Plating
A thin layer of copper is electroplated onto the hole walls to provide electrical connection between layers. Additional metal layers like nickel and gold may be plated onto the copper for better durability and solderability.
Solder Mask
The solder mask is applied over the outer copper layers and cured using heat or ultraviolet light. Openings are left in the solder mask for component pads and test points.
Silkscreen
The silkscreen labels and symbols are printed onto the solder mask using ink or epoxy. The silkscreen is cured using heat or ultraviolet light.
Routing
The individual boards are routed out of the panel using a saw or router. V-score lines may be cut to allow the boards to be snapped apart by hand.
Testing
The finished PCBs are tested for continuity and short circuits using a flying probe or bed-of-nails tester. Functional testing may also be performed to verify that the board operates as intended.
LED PCBs
LED printed circuit boards are specialized PCBs designed to control and power light-emitting diodes (LEDs). LEDs are semiconductor devices that emit light when an electric current passes through them. They are used for a wide range of applications, including:
- Lighting
- Displays
- Indicators
- Automotive
- Signage
LED PCBs must be designed to provide the proper voltage and current to the LEDs while also dissipating heat. The PCB layout must also consider the optical properties of the LEDs and the desired light output.
LED Drivers
LEDs require a constant current source to operate properly. The current must be regulated to prevent the LED from burning out or flickering. LED drivers are electronic circuits that provide the constant current needed to power LEDs.
There are several types of LED drivers:
- Constant Current Drivers
- Constant Voltage Drivers
- Buck Converters
- Boost Converters
- Linear Regulators
The type of driver used depends on the number and type of LEDs, the input voltage, and the desired output current.
Thermal Management
LEDs generate a significant amount of heat during operation. If the heat is not properly dissipated, it can cause the LED to degrade or fail prematurely. LED PCBs must be designed with thermal management in mind.
There are several techniques for managing heat on LED PCBs:
- Heatsinks
- Thermal Vias
- Metal Core PCBs
- Thermally Conductive PCBs
- Fans and Blowers
The choice of thermal management technique depends on the power level of the LEDs and the operating environment.
Optical Design
The optical design of an LED PCB determines how the light is emitted and controlled. The PCB layout must consider the viewing angle, intensity, and color of the LEDs.
There are several techniques for controlling the light output of LEDs:
- Lenses
- Reflectors
- Diffusers
- Light Pipes
- Baffles
The choice of optical technique depends on the desired beam pattern, brightness, and uniformity.
FAQ
What is the difference between an LED and a traditional light bulb?
LEDs are solid-state devices that emit light through electroluminescence. Traditional light bulbs emit light through incandescence or fluorescence. LEDs are more energy-efficient, longer-lasting, and more durable than traditional bulbs.
Can I solder LEDs directly to a PCB?
Yes, LEDs can be soldered directly to a PCB using through-hole or surface-mount technology. However, it is important to use the correct solder temperature and duration to avoid damaging the LED.
How do I calculate the resistor value for an LED?
The resistor value for an LED depends on the forward voltage and current of the LED and the supply voltage. You can use Ohm’s law to calculate the resistor value:
R = (Vs – Vf) / If
Where:
* R is the resistor value in ohms
* Vs is the supply voltage in volts
* Vf is the forward voltage of the LED in volts
* If is the forward current of the LED in amps
What is the difference between a metal core PCB and a standard PCB?
A metal core PCB has a layer of metal, usually aluminum, as the base substrate instead of FR4. The metal layer acts as a heatsink to dissipate heat from the components. Metal core PCBs are often used for high-power LED applications.
Can I use a standard PCB for LED lighting?
Yes, standard PCBs can be used for LED lighting applications. However, they may not be able to dissipate heat as effectively as metal core or thermally conductive PCBs. It is important to consider the power level and operating environment when choosing a PCB for LED lighting.
Conclusion
LED printed circuit boards are an essential component of many modern electronic devices. They provide the power, control, and optical output needed to create efficient and effective LED lighting solutions.
When designing an LED PCB, it is important to consider factors like LED driver selection, thermal management, and optical design. By carefully selecting components and layout techniques, designers can create LED PCBs that meet the specific requirements of their application.
As LED technology continues to advance, we can expect to see even more innovative and efficient LED PCB designs in the future.
Here is a summary table of the key points covered in this article:
Topic | Key Points |
---|---|
PCB Types | Single-layer, double-layer, multi-layer, flexible, rigid-flex |
PCB Composition | Substrate, copper, solder mask, silkscreen |
PCB Design | Schematic capture, component selection, layout, DRC, Gerber files |
PCB Manufacturing | Printing, etching, drilling, plating, solder mask, silkscreen, routing, testing |
LED PCBs | Applications, drivers, thermal management, optical design |
FAQ | LED vs. traditional bulbs, soldering LEDs, resistor calculation, metal core vs. standard PCBs |
0 Comments