Introduction
Soldering is a crucial process in electronics manufacturing that involves joining two or more metal surfaces together using a filler metal called solder. Traditionally, lead-based solders were widely used due to their excellent wetting properties, low melting points, and good electrical conductivity. However, with growing concerns about the environmental and health impacts of lead, the electronics industry has shifted towards lead-free solders.
In this comprehensive guide, we will delve into the differences between lead-free and lead solders, their compositions, properties, advantages, disadvantages, and applications. We will also discuss the transition from lead to lead-free solders, the challenges faced by the industry, and the future outlook for soldering technologies.
What is Solder?
Solder is a fusible metal alloy used to create a permanent bond between metal surfaces. It is typically composed of tin (Sn) and lead (Pb) in various proportions, along with small amounts of other elements such as silver (Ag), copper (Cu), or bismuth (Bi) to enhance its properties.
The most common types of solder are:
-
Tin-lead (SnPb) solder: This is the traditional solder alloy that contains 60% tin and 40% lead (Sn60Pb40). It has a melting point of 183°C (361°F) and is known for its excellent wetting properties and reliability.
-
Lead-free solder: These solders are composed of various combinations of tin, silver, copper, and other elements, without the use of lead. The most popular lead-free solder is SAC305, which contains 96.5% tin, 3% silver, and 0.5% copper (Sn96.5Ag3.0Cu0.5). Lead-free solders typically have higher melting points compared to tin-lead solders, ranging from 217°C to 227°C (423°F to 441°F).
Why the Shift to Lead-free Solder?
The transition from lead to lead-free solders was primarily driven by environmental and health concerns associated with lead exposure. Lead is a toxic substance that can accumulate in the body and cause various health problems, such as neurological disorders, reproductive issues, and developmental delays in children.
In response to these concerns, several countries and regions have implemented regulations restricting the use of lead in electronic products. The most notable of these regulations is the Restriction of Hazardous Substances (RoHS) Directive, which was first introduced by the European Union in 2003. The RoHS Directive limits the use of six hazardous materials, including lead, in the manufacture of various types of electronic and electrical equipment.
Other countries, such as the United States, China, and Japan, have also adopted similar regulations or voluntary standards to reduce the use of lead in electronics. As a result, the electronics industry has been forced to develop and adopt lead-free soldering technologies to comply with these regulations and meet consumer demands for eco-friendly products.
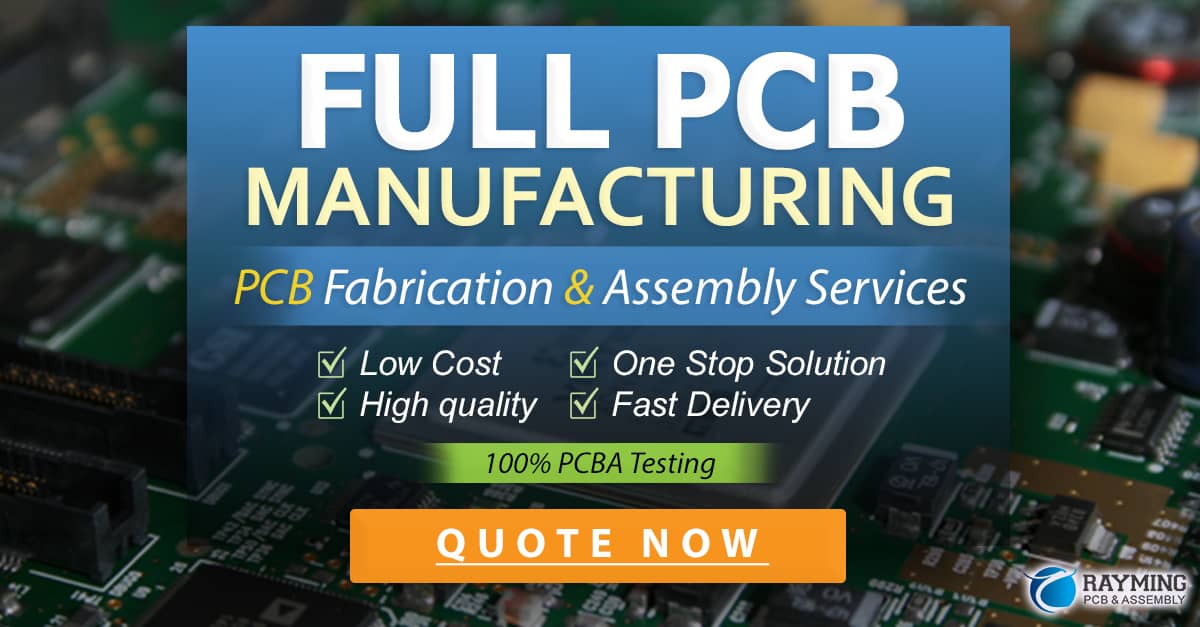
Composition and Properties of Lead-free vs. Lead Solders
To understand the differences between lead-free and lead solders, it is essential to examine their compositions and properties. The following table compares the most common lead-free solder (SAC305) with the traditional tin-lead solder (Sn60Pb40):
Property | SAC305 (Lead-free) | Sn60Pb40 (Lead) |
---|---|---|
Composition | Sn96.5Ag3.0Cu0.5 | Sn60Pb40 |
Melting Point | 217-220°C | 183°C |
Tensile Strength | 50-60 MPa | 40-50 MPa |
Electrical Conductivity | 12-15% IACS | 11.5% IACS |
Wetting Properties | Good | Excellent |
Fatigue Resistance | Better | Good |
Creep Resistance | Better | Good |
Cost | Higher | Lower |
As seen in the table, lead-free solders have higher melting points, better tensile strength, and improved fatigue and creep resistance compared to lead solders. However, lead solders have excellent wetting properties and are less expensive.
The higher melting points of lead-free solders can pose challenges during the soldering process, as they require higher processing temperatures and longer dwell times. This can lead to increased thermal stress on components and printed circuit boards (PCBs), potentially affecting their reliability and performance.
On the other hand, the improved mechanical properties of lead-free solders, such as higher tensile strength and better fatigue resistance, can enhance the durability and reliability of solder joints, particularly in applications subject to vibration, thermal cycling, or mechanical stress.
Advantages and Disadvantages of Lead-free Solder
Lead-free solders offer several advantages over traditional lead solders, but they also have some disadvantages that need to be considered. Let’s examine the pros and cons of using lead-free solders:
Advantages
-
Environmental and health benefits: The primary advantage of lead-free solders is the reduction of lead exposure and its associated environmental and health risks. By eliminating lead from the soldering process, the electronics industry can contribute to a safer and more sustainable future.
-
Compliance with regulations: Using lead-free solders enables manufacturers to comply with international regulations, such as the RoHS Directive, and access markets that have strict lead restrictions.
-
Improved mechanical properties: Lead-free solders exhibit better tensile strength, fatigue resistance, and creep resistance compared to lead solders, which can enhance the reliability and durability of solder joints in demanding applications.
-
Higher temperature stability: The higher melting points of lead-free solders can provide better thermal stability and resistance to high-temperature environments.
Disadvantages
-
Higher processing temperatures: Lead-free solders require higher reflow and wave soldering temperatures, which can increase energy consumption, generate more thermal stress on components and PCBs, and potentially affect their reliability.
-
Longer process times: Due to their higher melting points, lead-free solders may require longer preheat and dwell times during the soldering process, which can impact production throughput and efficiency.
-
Increased costs: Lead-free solders and the associated process changes can result in higher material, equipment, and training costs for manufacturers.
-
Tin whisker formation: Some lead-free solders, particularly those with high tin content, are more susceptible to tin whisker growth, which can cause short circuits and reliability issues in electronic devices.
-
Compatibility issues: Transitioning to lead-free solders may require changes in component finishes, PCB materials, and soldering equipment, which can create compatibility challenges and require significant investments.
Applications of Lead-free Solder
Lead-free solders are used in a wide range of electronic applications, including:
-
Consumer electronics: Smartphones, tablets, laptops, televisions, and home appliances.
-
Automotive electronics: Engine control units, sensors, infotainment systems, and advanced driver assistance systems (ADAS).
-
Aerospace and defense: Avionics, satellite communications, and military equipment.
-
Medical devices: Implantable devices, diagnostic equipment, and patient monitoring systems.
-
Industrial electronics: Process control systems, automation equipment, and power electronics.
-
Telecommunications: Network equipment, routers, switches, and 5G infrastructure.
-
Renewable energy: Solar panels, wind turbines, and energy storage systems.
As the electronics industry continues to embrace lead-free soldering, the use of these solders will expand across various sectors, driven by the need for compliance with regulations, environmental stewardship, and technological advancements.
Challenges in Adopting Lead-free Solder
The transition from lead to lead-free solders has not been without challenges. Some of the key issues faced by the electronics industry include:
-
Process optimization: Adapting soldering processes to accommodate the higher melting points and different wetting characteristics of lead-free solders requires extensive process optimization and validation.
-
Equipment upgrades: Manufacturers may need to invest in new soldering equipment or modify existing machines to handle the higher processing temperatures and ensure compatibility with lead-free solders.
-
Training and skill development: Technicians and engineers must be trained on the proper handling, processing, and inspection techniques for lead-free solders to ensure high-quality solder joints and minimize defects.
-
Supply chain management: Ensuring a consistent and reliable supply of lead-free solders, components, and PCBs can be challenging, particularly during the transition period when both lead and lead-free materials are in use.
-
Reliability concerns: The long-term reliability of lead-free solder joints, especially in harsh environments or under high stress conditions, is still a topic of ongoing research and debate in the industry.
Addressing these challenges requires collaboration among solder manufacturers, equipment suppliers, component vendors, and electronics manufacturers to develop innovative solutions, share best practices, and establish industry standards for lead-free soldering.
Future Outlook for Lead-free Soldering
As the electronics industry continues to evolve, so will the development and adoption of lead-free soldering technologies. Some of the key trends and opportunities in the future of lead-free soldering include:
-
Advanced solder alloys: Researchers are developing new lead-free solder alloys with improved properties, such as lower melting points, better wetting characteristics, and enhanced mechanical performance, to address the limitations of current lead-free solders.
-
Nanoparticle-reinforced solders: The incorporation of nanoparticles, such as silver, copper, or ceramic nanoparticles, into lead-free solders can potentially enhance their mechanical strength, thermal conductivity, and electromigration resistance.
-
Innovative soldering techniques: Novel Soldering Methods, such as laser soldering, ultrasonic soldering, and microwave soldering, are being explored to improve the efficiency, precision, and reliability of lead-free soldering processes.
-
Environmentally friendly materials: The development of bio-based, recyclable, or biodegradable soldering materials and fluxes can further reduce the environmental impact of electronics manufacturing.
-
Automation and process control: The integration of advanced automation, sensor technologies, and data analytics can help optimize lead-free soldering processes, ensure consistent quality, and minimize defects.
As the electronics industry strives for greater sustainability, performance, and reliability, the adoption of lead-free soldering will continue to grow, driven by technological advancements, regulatory requirements, and consumer demands.
Frequently Asked Questions (FAQ)
-
Q: Are lead-free solders as reliable as lead solders?
A: Lead-free solders can be as reliable as lead solders when properly processed and used in appropriate applications. However, the long-term reliability of lead-free solders in harsh environments or under high stress conditions is still a topic of ongoing research and debate in the industry. -
Q: Can lead and lead-free solders be mixed?
A: Mixing lead and lead-free solders is not recommended, as it can result in inconsistent melting points, poor wetting, and reduced joint reliability. It is best to use either lead or lead-free solders consistently throughout a project or product. -
Q: What is the most common lead-free solder alloy?
A: The most common lead-free solder alloy is SAC305, which contains 96.5% tin, 3% silver, and 0.5% copper (Sn96.5Ag3.0Cu0.5). This alloy is widely used in the electronics industry due to its good balance of properties and compatibility with various components and PCB finishes. -
Q: Do lead-free solders require special handling or storage?
A: Lead-free solders do not typically require special handling or storage compared to lead solders. However, it is essential to follow the manufacturer’s recommendations for storage conditions, shelf life, and handling to ensure optimal performance and prevent contamination. -
Q: Can lead-free solders be used for hand soldering?
A: Yes, lead-free solders can be used for hand soldering, but they may require higher soldering iron temperatures and slightly different techniques compared to lead solders. It is essential to use the appropriate soldering iron tip, temperature, and dwell time to ensure good wetting and joint formation with lead-free solders.
Conclusion
The transition from lead to lead-free solders in the electronics industry has been driven by environmental and health concerns, as well as regulatory requirements. While lead-free solders offer several advantages, such as reduced lead exposure and improved mechanical properties, they also present challenges in terms of processing temperatures, costs, and compatibility.
As the industry continues to adapt and innovate, the development of advanced lead-free solder alloys, innovative soldering techniques, and environmentally friendly materials will shape the future of soldering technologies. By embracing lead-free soldering and addressing the associated challenges, the electronics industry can contribute to a more sustainable and responsible future while delivering high-quality, reliable products to consumers.
0 Comments