Printed circuit boards (PCBs) are essential components in almost all electronic devices today. From computers and smartphones to appliances and vehicles, PCBs provide the foundation for integrating and connecting electronic components. As critical elements enabling functionality, quality, and reliability in electronics, PCB assembly must meet high standards.
The IPC, formerly known as the Institute for Printed Circuits, is the leading industry association dedicated to the design, manufacture, and assembly of electronics. For over 60 years, the IPC has developed standards and specifications for PCB fabrication, assembly, soldering, repair, and related processes. Adherence to these widely adopted standards ensures quality, consistency, and best practices across the electronics industry supply chain.
IPC Standards for PCB Assembly
The IPC provides hundreds of standards related to the PCB assembly process. Some of the most important and commonly used standards include:
IPC-A-610 Acceptability of Electronic Assemblies
This visual quality standard provides acceptance criteria for the most common assembly defects like poor solder joints, damage, or contamination. It has photos and illustrations of defect examples at different acceptance levels. IPC-A-610 helps reduce subjective interpretations and disputes between assemblers and customers regarding assembly quality.
IPC J-STD-001 Requirements for Soldered Electrical and Electronic Assemblies
This is one of the most crucial standards for developing soldering processes. It provides criteria for materials, methods, inspection testing, process control, and training to produce quality soldered interconnections. The standard covers topics like solderability, surface finishes, solder paste printing, reflow soldering, hand soldering, rework, and more.
IPC-A-620 Requirements and Acceptance for Cable and Wire Harness Assemblies
As the name suggests, this standard sets quality requirements for cable and wire harness assemblies. It has acceptance criteria for materials, wire wrapping, terminations, markings, soldering, adhesives, insulation, shielding, and other harness features. IPC-A-620 is complemented by IPC/WHMA-A-620 for assemblies used in telecommunications devices and equipment.
IPC-6012 Qualification and Performance Specification for Rigid Printed Circuit Boards
While not directly about assembly, IPC-6012 sets reliability expectations for PCBs used in assembly. It defines qualification and conformance tests to ensure PCBs meet mechanical, environmental, and electrical needs for assembly and service life. Parameters like adhesion, resistance to chemicals, flammability, flexure, and more are covered.
IPC-6013 Qualification and Performance Specification for Flexible Printed Circuit Boards
This standard complements IPC-6012 for flexible PCBs or flex circuits. It provides similar conformance tests tailored for the unique features and applications of flex PCBs. IPC-6013 tests parameters like flexure endurance, dynamic bend stress, dielectric withstanding voltage, and more.
Benefits of Using IPC Standards
Adopting and following IPC standards offers many benefits for PCB assemblers and electronics companies:
- Quality and reliability – IPC standards help ensure consistent quality, reduce defects, and improve reliability in assembled electronics. This leads to lower failure rates in service.
- Interoperability – Common standards make it easier to integrate components from different manufacturers into an assembly. Standards aid compatibility.
- Process control – The standards provide well-defined assembly and soldering procedures that can be standardized across production lines and facilities. This enables process control and stability.
- Inspection methods – Acceptability criteria and inspection methods in IPC standards empower consistent defect detection. This facilitates quality control and oversight of assembly houses.
- Risk mitigation – Compliance with industry standards reduces risks of field failures and liabilities associated with poor quality or workmanship. It demonstrates due diligence and best practices.
- Qualified personnel – Standards for certification programs ensure assemblers are trained competently. IPC credentials like CIT and CIS demonstrate personnel qualification.
- Customer confidence – Adherence to IPC standards provides credibility to customers that assemblies meet quality benchmarks. This inspires confidence.
In summary, utilizing IPC assembly standards enables PCB assemblers and electronics manufacturers to produce reliable, quality products following industry best practices. The standards foster process and quality control while mitigating risks of defects. They provide a framework for managing complex assembly operations and supply chains efficiently. With electronics becoming more sophisticated and safety-critical, conformance to IPC standards is increasingly valued and expected.
Key Elements of IPC PCB Assembly Standards

IPC assembly standards provide comprehensive criteria, controls, and procedures across the assembly process. Here are some of the key elements covered within the standards:
Materials
- PCB acceptability requirements
- Solderability of component leads and terminations
- Solder paste properties (alloy, particle size, flux, etc.)
- Conformal coating properties
Processes
- Solder paste stencil design
- Solder paste printing and inspection
- Component placement and inspection
- Reflow soldering profiles and requirements
- Conformal coating application methods
- Marking and identification of assemblies
Inspection & Testing
- Visual inspection criteria and acceptability levels
- Dimensional measurement methods
- Solder joint inspection (e.g. IPC-A-610)
- Component damage evaluation
- Electrical testing approaches
- Environmental stress testing
- Qualification and conformance testing
Workmanship
- Soldering methods, terminations, and limits
- Cleanliness requirements
- Repair and rework instructions
- ESD control
- Handling and storage guidelines
Documentation
- Assembly drawings
- Bill of materials
- Acceptance and inspection reports
- Process change notices
- Certificates of conformance
- Qualification reports
IPC PCB Assembly Techniques
PCB assembly integrates many techniques, each with design, materials, process, inspection, and workmanship considerations. Here are some of the key assembly techniques guided by IPC standards:
Soldering
Soldering makes both electrical and mechanical connections between components and PCBs. IPC J-STD-001 establishes criteria for soldering materials, procedures, and acceptability across various methods like:
- Reflow soldering – Surface mount components are soldered by heating entire boards in a convection reflow oven. Solder paste reflows when heated above its melting point.
- Wave soldering – Through-hole component leads are soldered as the PCB passes over a wave of molten solder. The wave wets and solders the exposed leads.
- Hand soldering – Manual soldering of larger components, wires, and hardware (e.g. connectors) is done with irons and solder.
- Selective soldering – Targeted soldering of specific joints is done using mini-wave, iron, or jetting methods. Useful for repairs and rework.
- Ball grid array (BGA) soldering – Reflow methods solder BGA packages with solder balls under the package connecting to PCB pads.
Conformal Coating
Conformal coatings are thin protective layers applied over PCB assemblies. IPC-CC-830 provides guidance on materials, application, cure, inspection, and repair of conformal coatings. Common coating methods include:
- Spraying – Liquid coatings sprayed and air dried. Provides uniform thin layers.
- Brushing – Manual brushing for selective coating or rework.
- Dipping – Dipping boards in a coating bath.
- Dispenser/jetting – Precision, automated dispensing of dots or beads of coating.
Cleaning
Cleaning removes unwanted contaminants and residues from assembly processes. IPC-CH-65 covers cleaning agents, procedures, and cleanliness testing. Some methods include:
- Aqueous cleaning – Using water-based cleaners to remove fluxes and other water-soluble residues.
- Solvent cleaning – Applying solvents to dissolve and rinse away organic contaminants.
- Mechanical scrubbing – Brushing or agitating assemblies in cleaning solutions.
- Ultrasonic cleaning – Using ultrasonic frequency vibrations to remove tightly adhered particles.
- Vacuum cleaning – Dry vacuum cleaning removes loose particles and dust.
- Plasma/ionized gas cleaning – Plasma energy breaks down and removes organic residues.
In-Circuit Testing (ICT)
ICT using benchtop fixtures verifies proper assembly by electrically testing boards before further integration. IPC-9191 outlines test fixture design, test coverage, and test limits for ICT.
Box Build Assembly
Larger sub-assemblies that integrate PCBs, cables, and other components are called box builds. IPC-610, J-STD-001, and IPC/WHMA-A-620 apply to box build soldering and wiring.
IPC Workmanship Standards by Class
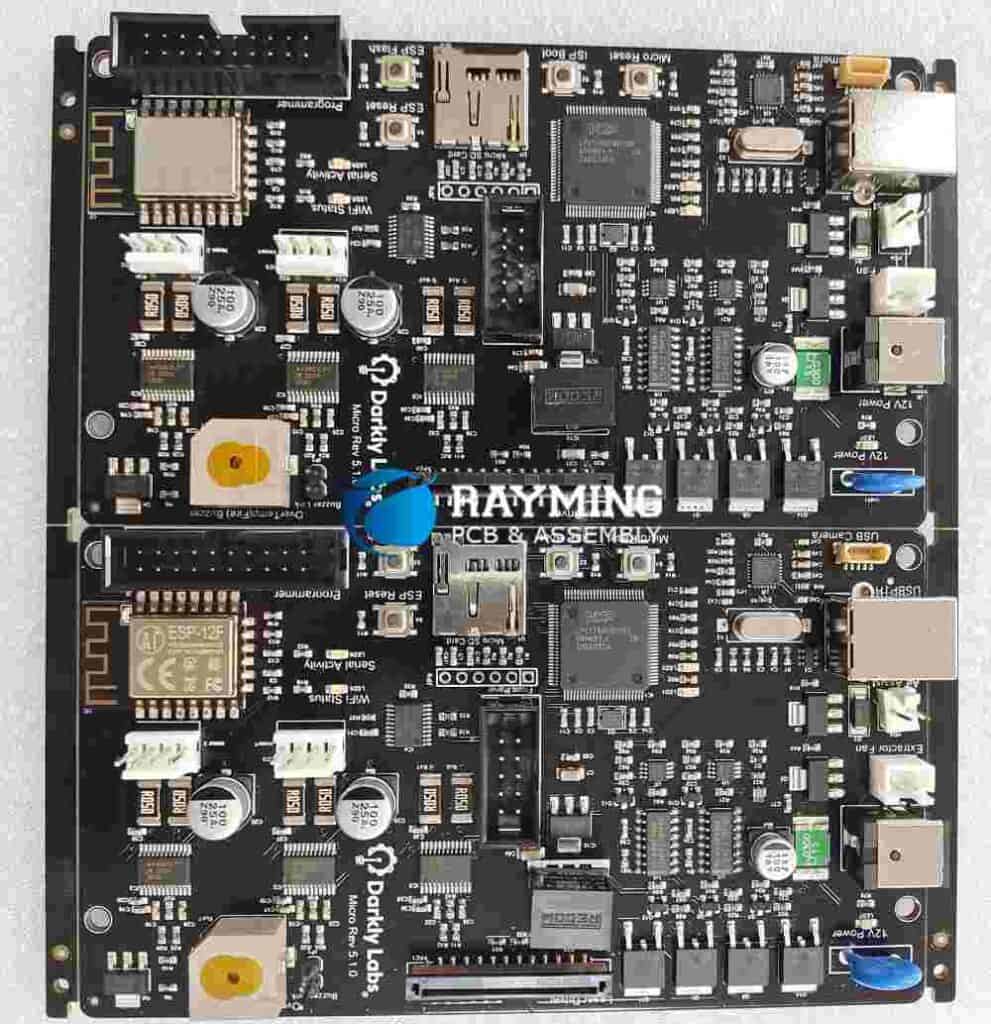
To allow flexibility for different applications, IPC assembly standards define acceptance criteria under three workmanship classes:
Class | Description | Example Applications |
---|---|---|
Class 1 | General electronics assemblies | Consumer electronics, appliances |
Class 2 | Dedicated service electronics | Communications infrastructure |
Class 3 | High performance/critical electronics | Aerospace, defense, medical |
Higher classes call for more stringent requirements and tighter acceptability levels. Workmanship standards are tailored for an assembly’s end-use environmental conditions, product life cycles, and reliability needs.
Certifications for IPC Standards
To help educate the industry workforce and demonstrate competency working to IPC standards, IPC offers various personnel certification programs including:
- IPC Specialist (CIS) – Covers soldering, inspection, repair/rework, and wire harness assembly standards.
- Certified IPC Trainer (CIT) – For instructors teaching IPC curriculum and standards.
- IPC Master Instructor (MIT) – Senior-level program for experienced instructors.
- IPC Trainer Development (TD) – Provides apprentice instructional training.
Certified assemblers, inspectors, trainers, and facilities indicate expertise in properly applying IPC methods and requirements. Many electronics manufacturers require IPC certifications.
IPC Validation Services
In addition to standards and education, IPC provides auditing, testing, inspection, and certification services to validate conformance for:
- PCB fabrication per IPC-6010 and IPC-6012/6013
- PCB assembly per IPC-A-610, J-STD-001, and IPC/WHMA-A-620
- Wire and cable harnesses per IPC/WHMA-A-620
- EMS companies per IPC-J-STD-001 and IPC-A-610
IPC validation provides independent oversight to verify that facilities meet applicable quality standards. It supplements required internal procedures and quality management systems.
Frequently Asked Questions
What are the main differences between IPC-A-610 and J-STD-001 for assembly?
- IPC-A-610 focuses on visual acceptance criteria for solder joints and component conditions. J-STD-001 covers soldering materials, processes, inspection testing, and personnel training in more depth. IPC-A-610 is driven by final inspection while J-STD-001 guides building quality into the process.
How often are IPC standards updated?
- IPC reviews and updates standards every 5-7 years on average. Updates incorporate feedback from industry users and account for changing technologies, materials, and best practices. Users should adopt the latest version of standards.
Is implementing IPC standards expensive?
- While there are costs related to new equipment, training, inspections, and process changes, this is offset by reduced defects, rework, failures, and reputation damage. High quality ultimately saves money. IPC’s ROI calculators help estimate costs vs. benefits.
What is the difference between IPC workmanship Classes 1, 2, and 3?
- The classes designate progressively tighter acceptability levels. Class 1 suits general commercial electronics, Class 2 for long-life dedicated service products, and Class 3 for high performance, critical systems with the tightest reliability needs.
How can we demonstrate compliance with IPC standards?
- Certification and training for staff, documented processes referencing IPC standards, validation audits, inspection reports, quality records, IPC marking and labeling, and obtaining certification from IPC Validation Services.
Conclusion
IPC standards play a critical role in enabling electronics manufacturers to produce high-quality, reliable PCB assemblies at scale across the industry. They encapsulate best practices refined over decades into accessible requirements and procedures. By adopting up-to-date IPC standards and integrating them into product designs, assembly processes, inspections, qualifications, and workforce training, companies can confidently deliver assemblies that function correctly over intended lifetimes. With electronics increasing in complexity and criticality, maintaining competency in applying IPC standards provides tremendous value for both PCB assembly businesses and their customers.
0 Comments