What are IPC PCB Standards?
IPC, formerly known as the Institute for Printed Circuits, is a global trade association that develops and publishes standards for the electronic manufacturing industry. IPC PCB standards are a set of guidelines and specifications that define the requirements for the design, fabrication, assembly, and testing of printed circuit boards.
These standards cover various aspects of PCB manufacturing, including:
– Material selection
– Board design and layout
– Fabrication processes
– Assembly techniques
– Quality control and testing methods
By adhering to IPC PCB standards, manufacturers can ensure that their PCBs meet the necessary quality, reliability, and performance criteria.
The Importance of IPC PCB Standards
1. Consistency and Reliability
One of the primary reasons for implementing IPC PCB standards is to achieve consistency and reliability in PCB manufacturing. By following a set of standardized guidelines, manufacturers can produce PCBs that consistently meet the required specifications, regardless of the production location or the specific manufacturer.
This consistency is crucial for several reasons:
– It ensures that PCBs from different manufacturers are compatible and interchangeable.
– It reduces the risk of defects and failures, as the manufacturing process follows established best practices.
– It facilitates easier troubleshooting and maintenance, as technicians can rely on a common set of standards.
2. Cost Reduction and Efficiency
Adhering to IPC PCB standards can also lead to cost savings and improved efficiency in the manufacturing process. By following standardized procedures and using recommended materials and techniques, manufacturers can:
– Reduce the likelihood of errors and rework, minimizing waste and saving time and resources.
– Optimize the manufacturing process, leading to faster production times and increased throughput.
– Leverage the collective knowledge and best practices of the industry, avoiding the need to reinvent the wheel.
3. Enhanced Communication and Collaboration
IPC PCB standards provide a common language and framework for communication between different stakeholders in the electronics industry. This includes:
– PCB designers and engineers
– Manufacturers and suppliers
– Quality control and testing personnel
– End-users and customers
By using a standardized terminology and set of specifications, all parties involved can communicate effectively, avoiding misunderstandings and ensuring that everyone is on the same page.
4. Improved Product Quality and Performance
Ultimately, the goal of IPC PCB standards is to ensure the highest level of product quality and performance. By following these standards, manufacturers can produce PCBs that:
– Meet the required electrical and mechanical specifications
– Demonstrate excellent reliability and durability
– Function as intended in the final electronic product
This translates to better-performing electronic devices, reduced field failures, and enhanced customer satisfaction.
Key IPC PCB Standards
There are several key IPC PCB standards that cover different aspects of PCB manufacturing. Some of the most widely used standards include:
Standard | Description |
---|---|
IPC-2221 | Generic Standard on Printed Board Design |
IPC-6012 | Qualification and Performance Specification for Rigid Printed Boards |
IPC-A-600 | Acceptability of Printed Boards |
IPC-A-610 | Acceptability of Electronic Assemblies |
IPC-7711/7721 | Rework, Modification, and Repair of Electronic Assemblies |
These standards provide detailed specifications and guidelines for various aspects of PCB manufacturing, ensuring that the resulting PCBs meet the necessary quality and performance criteria.
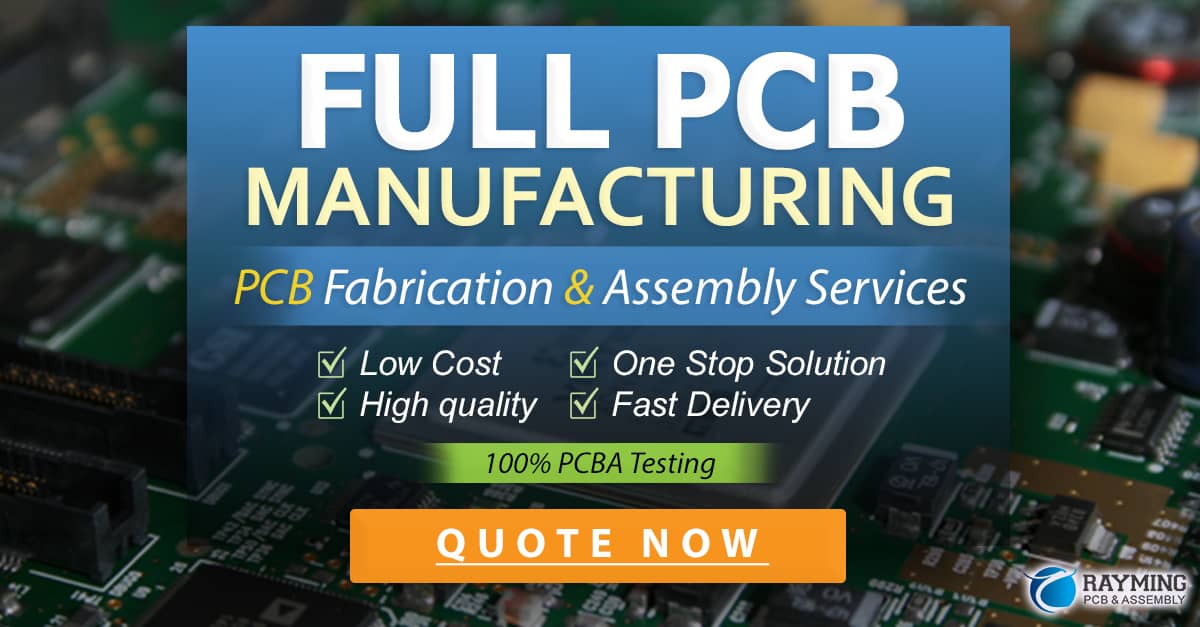
Implementing IPC PCB Standards
To effectively implement IPC PCB standards, manufacturers need to follow a systematic approach:
- Familiarize themselves with the relevant IPC standards and their requirements.
- Train their personnel on the proper application of these standards.
- Establish documented procedures and work instructions that align with the IPC standards.
- Implement appropriate quality control measures to ensure compliance with the standards.
- Regularly audit and review their processes to identify areas for improvement and ensure ongoing adherence to the standards.
By following this approach, manufacturers can successfully integrate IPC PCB standards into their operations and reap the benefits of consistent, reliable, and high-quality PCB production.
Frequently Asked Questions (FAQ)
1. Are IPC PCB standards mandatory?
While IPC PCB standards are not legally mandatory, they are widely recognized and adopted by the electronics industry. Many customers and end-users require their suppliers to adhere to these standards to ensure the quality and reliability of the PCBs they purchase.
2. How often are IPC PCB standards updated?
IPC regularly reviews and updates its standards to keep pace with technological advancements and industry needs. The frequency of updates varies depending on the specific standard and the rate of change in the relevant technology. Manufacturers should stay informed about the latest revisions of the standards they follow.
3. Can manufacturers deviate from IPC PCB standards?
In some cases, manufacturers may need to deviate from IPC PCB standards to meet specific customer requirements or to accommodate unique design features. However, any deviations should be carefully evaluated and documented, and their potential impact on the quality and reliability of the PCBs should be assessed.
4. How can manufacturers ensure compliance with IPC PCB standards?
Manufacturers can ensure compliance with IPC PCB standards by implementing a robust quality management system that includes:
– Documented procedures and work instructions aligned with the relevant standards
– Regular training and certification of personnel
– Appropriate quality control measures and testing procedures
– Ongoing audits and continuous improvement efforts
5. What are the consequences of not following IPC PCB standards?
Not following IPC PCB standards can lead to several negative consequences, including:
– Inconsistent and unreliable PCB Quality
– Increased risk of defects and failures
– Difficulty in troubleshooting and maintenance
– Potential loss of customer trust and business opportunities
– Higher costs due to rework and scrap
By adhering to IPC PCB standards, manufacturers can mitigate these risks and ensure the production of high-quality, reliable PCBs.
Conclusion
IPC PCB standards play a vital role in ensuring the consistency, reliability, and quality of printed circuit boards in the electronics industry. By providing a set of guidelines and specifications for the design, fabrication, assembly, and testing of PCBs, these standards help manufacturers to optimize their processes, reduce costs, and improve product performance.
Implementing IPC PCB standards requires a commitment to quality and a systematic approach to integrating these standards into the manufacturing process. By familiarizing themselves with the relevant standards, training their personnel, establishing documented procedures, and implementing appropriate quality control measures, manufacturers can successfully adopt and benefit from IPC PCB standards.
As the electronics industry continues to evolve and new technologies emerge, IPC PCB standards will remain an essential tool for ensuring the quality and reliability of PCBs. By staying up-to-date with the latest revisions of these standards and continuously improving their processes, manufacturers can position themselves for success in an increasingly competitive market.
0 Comments