Printed circuit boards (PCBs) serve as the foundation of electronics, providing the interconnects between components to bring products to life. While PCB fabrication has traditionally been complex, new technologies are making in-house PCB production increasingly accessible. This guide covers everything you need to know about fabricating your own PCBs.
Overview of PCB Fabrication
PCB fabrication involves taking the design file and physically creating the board. The key steps include:
- Design – Creating the board layout in CAD software.
- Gerber generation – Converting the design into Gerber files used for fabrication.
- Panelization – Arranging multiple PCB designs onto panels for mass production.
- Imaging – Using photolithography to pattern the copper layer onto the base laminate.
- Etching – Chemically etching away unwanted copper to leave the desired traces.
- Drilling – Drilling holes for component leads and vias.
- Plating and coating – Electroplating contacts and applying solder mask and silkscreen.
- Assembly – Stenciling solder paste and placing components onto the board.
- Testing and inspection – Electrically and visually inspecting the boards for defects.
For complex multilayer boards, additional steps like lamination and via formation are also involved. We’ll explore these fabrication processes in more detail throughout this guide.
In-House PCB Fabrication Options
Thanks to new equipment and processes, it’s now possible to fabricate PCBs in-house without the need for a full production facility. Here are some options for DIY PCB fabrication:
Milling PCBs
CNC milling uses a small endmill to carve copper traces directly onto a substrate. No chemicals are required, making it suitable for office or home use. Limitations include lower resolution and inability to create vias.
Laser Ablation
A laser can selectively ablate away copper on a laminate to leave just the desired conductive pattern. Allows high-resolution trace fabrication without chemicals.
Photochemical Etching
Using photoresist, UV light, and etchant chemicals allows accurate transfer of a PCB design onto a copper clad laminate through etching.
Direct Metallization
Technologies like conductive ink printing allow depositing copper traces directly without any etching. Resolution is improving with newer processes.
Flatbed Printing
Special inks and processes can print conductive traces from inkjet or other flatbed printers. Only suitable for simple single layer boards.
Each method has tradeoffs between cost, capability, and complexity. Selecting the right DIY fabrication process depends on your specific boards and volume needs.
Design Considerations for DIY PCB Production
When planning to fabricate your own PCBs, keep these design considerations in mind:
- Single-sided boards – Double layer boards are much more complex to produce in-house.
- Larger features and spacing – Account for lower feature resolution compared to commercial production.
- Avoid small vias – Minimum via sizes are larger, so space them accordingly.
- Use design for manufacturability guidelines – Follow industry PCB design rules to avoid issues.
- Panel utilization – Careful layout arrangement when panelizing maximizes board quantity.
- Breakout tabs – Add tabs to facilitate individual board removal after panelization.
- Tooling holes – Include fiducials and tooling holes for alignment during fabrication.
- Include test points – Helpful for validating continuity or detecting defects.
- Go bigger – Larger boards maximize productivity for each setup.
By keeping DIY process limitations in mind during design, you can ensure your boards translate successfully from layout into reality.
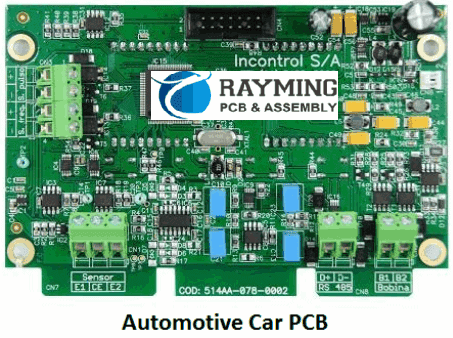
Step-by-Step PCB Fabrication Process
Here is an overview of the typical workflow required to go from design to finished boards using DIY methods:
1. Design the PCB
Complete your schematic and PCB layout in EDA software like Eagle, KiCad, Altium or others. Include design specifications optimized for DIY fabrication.
2. Export Gerber Files
Generate and check Gerber files for all layers needed to fabricate the boards. This includes copper layers, solder mask, silkscreen, drill files, etc.
3. Panelize the Design
Using Gerber viewer software, arrange multiple PCB designs onto panels for mass production. Add breakout tabs, isolation routing, and tooling holes.
4. Prepare the Substrate
Cut copper clad laminate sheets to match the panel size. Clean the material and treat the surface if needed by the process.
5. Apply Photoresist (Photochemical Etching)
For photochemical etching, apply liquid or dry film photoresist onto the copper surface, and soft bake to set.
6. Expose the Photoresist
Use the Gerber files to pattern UV light onto the photoresist, transferring the trace layout. Hard bake to finalize.
7. Etch the Board
Submerge boards in etchant chemicals to dissolve away unwanted copper, leaving just the desired conductive traces.
8. Strip Photoresist
For photochemical etching, soak boards in remover solution to strip off all photoresist, leaving bare copper.
9. Drill Holes
Using the NC drill files, drill all component and via holes using a small CNC drill machine.
10. Plate and Coat
Apply coatings and platings like immersion tin, ENIG, or liquid solder mask. Repeat for double sided boards.
11. Rout Boards
Route around the perimeter of each board to provide breakout and isolation between them.
12. Finish and Test
Electrically test boards for shorts and opens. Touch up solder mask or finishes as needed. Your PCBs are complete!
While simplified, this overview covers the core fabrication processes required to produce your own printed circuit boards using DIY methods. Each step must be carefully tested and validated to hone the process prior to ramping up production. Patience and persistence is key to mastering PCB fabrication.
Equipping Your Own PCB Fabrication Lab
Here is some of the equipment you’ll need to set up your own PCB fabrication lab:
Item | Description |
---|---|
Laminate Shearing | For cutting substrate sheets to size |
Photoresist Laminator | Applies dry film resist evenly |
UV Exposure Unit | Selectively exposes resist per the PCB design |
Spray Etching Equipment | Sprays etchant to dissolve copper |
CNC Drill Machine | Drills precision holes for vias and leads |
Imaging and Developing Equipment | For applying and developing liquid photoresist |
Solder Mask Applicator | Applies solder mask coatings |
Electroless Plating Solution | Plates copper, nickel, or tin |
Electrical Testing | For validation and troubleshooting |
Additionally you’ll need a wide range of chemicals, materials, personal protective equipment, cleaning tools, and more. Set aside ample budget for acquiring all needed equipment, consumables, and supplies. Leverage detailed process guides to understand equipment requirements before purchasing.
Optimizing for Iterative PCB Prototyping
For quickly iterating PCB layouts, optical fabrication methods like CNC milling offer fast in-house turnaround. The key advantages of CNC milling for prototyping include:
- No chemicals – Safer and easier to operate and maintain.
- Quick fabrication – New designs can be milled in under an hour in many cases.
- Shorter learning curve – Easier to master than complex chemical processes.
- Design flexibility – New layouts can be milled on-demand with minimal preparation.
- Low startup cost – No need for an array of equipment and chemicals.
- Scalable – Small desktop mills are affordable up front. Later on, larger mills offer higher throughput.
The simplified process and low cost of entry make CNC milling a great choice for efficiently prototyping boards during development without relying on external PCB manufacturers.
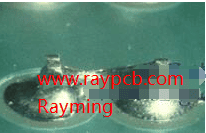
Key Benefits of In-House PCB Production
Here are some of the main advantages of bringing PCB fabrication in-house:
- Faster iteration – Tweak, fabricate, and test boards rapidly without waiting for manufacturing.
- Improved designs – More easily refine layouts to optimize performance and cost.
- IP protection – No need to share confidential schematics and designs.
- Flexibility – Produce new designs on-demand in very small or large volumes.
- Cost savings – Lower prototyping costs compared to using PCB manufacturers.
- Educational – Learn hands-on about the entire PCB production process.
- Customization – Tailor processes and materials to your specific needs.
While balancing higher effort levels, in-house fabrication enables much faster and cost-optimized development of new electronics products.
Key Considerations for In-House PCB Production
There are also some important factors to keep in mind:
- Higher startup costs – Equipment, materials, and supplies can be expensive up front.
- Facilities – Need adequate space as well as ventilation and utilities.
- Learning curve – Mastering fabrication processes takes diligent practice.
- ** Labor-intensive** – Very hands-on, slower, lower volumes than commercial production.
- Quality – More prone to defects; repetition develops skill and quality.
- Limitations – In-house processes have more restrictions than commercial.
- Consumables – Ongoing cost of materials, chemicals, utilities, etc.
Not a turnkey solution, bringing fabrication in-house requires significant effort. The benefits for prototyping and customization often outweigh the investments for the right applications.
Common Questions About In-House PCB Production
What are the minimum trace widths and spacing when milling PCBs?
The minimum trace is around 10 mil (0.254mm) width and space. resolutions under 5 mil are very challenging for milling.
What are some safety precautions for DIY PCB fabrication?
Use protective gear, avoid direct contact with chemicals, handle acids and etchants carefully, ventilate work areas, and follow safety guidelines rigorously.
What materials are needed to fabricate double layer PCBs?
Pre-clad copper laminate, drill bits, standoffs, alignment pins, photoresist or milling machine, plating solution, soldermask, and assorted chemicals, solutions, tapes, etc.
Can I fabricate complex multilayer boards at home?
High layer counts with blind and buried vias is extremely difficult without commercial lamination equipment. Optical processes like milling are limited to 2-4 layers maximum in DIY settings.
What resolution and line width can be achieved with photochemical etching?
With processes finely optimized, photochemical etching can achieve traces and spaces down to 2-3 mils. This is very challenging in DIY environments however.
Conclusion
Producing PCBs in-house puts board fabrication directly in the hands of hardware developers and engineers. Leveraging lower-cost equipment and simplified processes, it’s now possible to fabricate functional PCBs without a full-scale production facility. While requiring diligence to master, DIY PCB fabrication enables iterative prototyping and pilot production to be done completely internally. By understanding the processes, equipment, and limitations, you can set up a custom PCB fabrication capability tailored to your specific needs. The ability to quickly take designs from layout to prototype unlocks faster, lower-cost development of electronic products.
0 Comments