What is PCB Legend Print?
PCB (Printed Circuit Board) legend print, also known as silkscreen or nomenclature, is the process of adding text, symbols, and graphics onto the surface of a PCB. The legend print provides important information about the board, such as component placement, orientation, and identification. It helps in the assembly, testing, and maintenance of the PCB by providing clear visual guidance.
Importance of PCB Legend Print
PCB legend print serves several crucial purposes:
-
Component Identification: Legend print labels components with their reference designators (e.g., R1, C2, U3) and values (e.g., 10K, 22uF, 74HC00). This helps in accurately placing components during assembly and troubleshooting.
-
Orientation Guidance: Legend print often includes polarity markers, pin numbers, and other orientation indicators. These help ensure correct component placement and prevent assembly errors.
-
User Information: Legend print can include user-facing information such as company logos, product names, version numbers, and warning labels. This enhances the professional appearance of the PCB and provides important details to the end-user.
-
Manufacturing and Testing: Legend print can include fiducial markers, test points, and other information that aids in the manufacturing, testing, and quality control processes.
PCB Legend Print Methods
There are several methods for applying legend print to PCBs, each with its own advantages and limitations. The choice of method depends on factors such as the desired durability, precision, and cost.
Silkscreen Printing
Silkscreen printing is the most common method for applying legend print to PCBs. It involves using a fine mesh screen with a stencil of the desired artwork. Ink is then forced through the screen onto the PCB surface using a squeegee. The process is as follows:
-
Create the artwork: Design the legend print artwork using PCB Design Software, ensuring that the text and graphics are clear and properly sized.
-
Prepare the screen: Create a stencil of the artwork on a fine mesh screen. The stencil allows ink to pass through only in the desired areas.
-
Apply the ink: Place the screen onto the PCB surface and apply ink using a squeegee. The ink is forced through the screen, transferring the artwork onto the PCB.
-
Cure the ink: The printed PCB is then dried and cured, typically using a conveyor oven. This ensures that the ink adheres properly to the surface and becomes durable.
Silkscreen printing is cost-effective for large volumes and provides good durability. However, it has limitations in terms of precision and minimum font sizes.
Direct Legend Printing
Direct legend printing, also known as direct legend inkjet printing, uses specialized inkjet printers to apply the legend artwork directly onto the PCB surface. This method offers several advantages over silkscreen printing:
-
Higher precision: Direct legend printing can achieve finer details and smaller font sizes compared to silkscreen printing.
-
Faster setup: Since no physical screens are required, direct legend printing has a faster setup time and is more suitable for low-volume or prototype runs.
-
Flexibility: Artwork changes can be made quickly without the need to create new screens.
However, direct legend printing may have higher equipment costs and slower printing speeds compared to silkscreen printing.
Laser Marking
Laser marking uses a focused laser beam to engrave the legend artwork onto the PCB surface. This method offers high precision and durability, as the artwork is permanently etched into the PCB material. Laser marking is suitable for applications that require high-quality, long-lasting legend print, such as military or aerospace products.
The main drawback of laser marking is the higher equipment cost and slower processing speed compared to other methods.
PCB Legend Print Design Considerations
To ensure the best results for PCB legend print, consider the following design guidelines:
-
Font selection: Choose clear, legible fonts that are appropriate for the PCB manufacturing process. Avoid overly decorative or small fonts that may be difficult to reproduce accurately.
-
Text size: Ensure that text is large enough to be easily readable. Minimum recommended text heights are typically 1.5mm for silkscreen printing and 0.8mm for direct legend printing.
-
Alignment and spacing: Maintain consistent alignment and spacing between text and components. Avoid placing text too close to components or other features that may interfere with assembly or soldering.
-
Polarity and orientation markers: Include clear polarity markers and orientation indicators for components such as diodes, electrolytic capacitors, and ICs.
-
Color selection: Choose legend print colors that provide good contrast against the PCB substrate. White and black are the most common colors, but others may be used for specific applications.
-
Artwork file format: Prepare the legend print artwork in a format that is compatible with the PCB manufacturing process, such as Gerber or vector files.
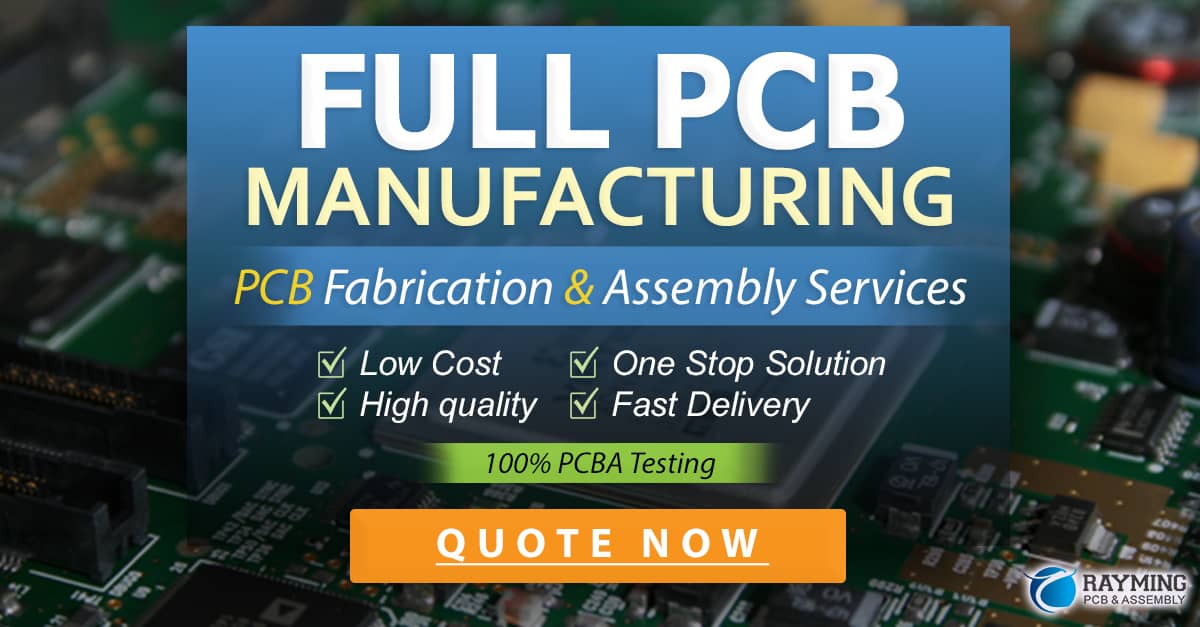
Legend Print Placement and Coverage
When designing the legend print layout, consider the following placement and coverage guidelines:
-
Component identifiers: Place component reference designators and values close to the corresponding component, typically on the same side of the PCB.
-
User information: Place user-facing information, such as company logos and product names, in a prominent location on the PCB, typically on the top side.
-
Fiducial markers: Include fiducial markers in the legend print artwork to aid in automated assembly and inspection processes.
-
Test points: Clearly label test points and other diagnostic features in the legend print to facilitate testing and troubleshooting.
-
Keep-out areas: Avoid placing legend print in areas that may interfere with component placement, soldering, or other manufacturing processes.
Legend Print Quality Control
To ensure the quality of the PCB legend print, consider the following quality control measures:
-
Visual inspection: Visually inspect the printed PCBs for legibility, alignment, and completeness of the legend print. Check for any smudging, fading, or inconsistencies.
-
Adhesion testing: Perform adhesion tests to ensure that the legend print is properly bonded to the PCB surface. This can be done using a simple tape test or more advanced methods such as cross-hatch testing.
-
Durability testing: Assess the durability of the legend print by subjecting the PCBs to environmental stress tests, such as temperature cycling, humidity exposure, or abrasion tests, depending on the intended application.
-
Process control: Implement process control measures to ensure consistent legend print quality across production runs. This may include regular calibration of printing equipment, ink viscosity monitoring, and operator training.
Frequently Asked Questions (FAQ)
- What is the minimum text size for PCB legend print?
-
For silkscreen printing, the minimum recommended text height is typically 1.5mm. For direct legend printing, smaller text sizes down to 0.8mm can be achieved.
-
Can PCB legend print be applied to both sides of the board?
-
Yes, legend print can be applied to both the top and bottom sides of the PCB, depending on the design requirements and manufacturing process.
-
What colors are available for PCB legend print?
-
The most common colors for PCB legend print are white and black, as they provide good contrast against the PCB substrate. However, other colors such as yellow, red, or blue may be used for specific applications or to distinguish between different types of information.
-
How durable is PCB legend print?
-
The durability of PCB legend print depends on the printing method and the ink used. Silkscreen printing and direct legend printing provide good durability for most applications, while laser marking offers the highest durability. Proper curing and handling of the printed PCBs also contribute to the long-term durability of the legend print.
-
Can legend print be customized with logos or graphics?
- Yes, PCB legend print can include custom logos, graphics, and other artwork elements. These should be designed in accordance with the PCB manufacturing process requirements and the legend print method being used. Vector-based artwork is typically preferred for the best results.
Conclusion
PCB legend print is a crucial aspect of PCB design and manufacturing, providing essential information for assembly, testing, and end-use. By understanding the different legend print methods, design considerations, and quality control measures, you can ensure that your PCBs have clear, durable, and informative legend print that enhances the overall quality and functionality of your products.
When designing PCB legend print, remember to choose appropriate fonts, sizes, and colors, and to consider the placement and coverage of the artwork. Work closely with your PCB manufacturer to ensure that the legend print artwork is compatible with their processes and meets their requirements.
By following best practices and implementing proper quality control measures, you can achieve high-quality PCB legend print that contributes to the success of your PCB projects.
0 Comments