Introduction to PCB Cutting
Printed Circuit Boards (PCBs) are essential components in modern electronics. They provide a platform for mounting and connecting electronic components, allowing for the creation of complex circuits. One crucial aspect of PCB fabrication is cutting the boards to the desired shape and size. In this comprehensive guide, we will explore various methods and techniques for cutting PCBs effectively.
Understanding PCB Materials and Thickness
Before delving into PCB cutting techniques, it’s important to understand the materials and thicknesses commonly used in PCB fabrication.
PCB Materials
PCBs are typically made from the following materials:
- FR-4: A flame-retardant composite material made of woven fiberglass cloth with an epoxy resin binder. It is the most widely used PCB material.
- Aluminum: Used for high-power applications that require efficient heat dissipation.
- Flexible PCBs: Made from flexible materials like polyimide or polyester, allowing for bending and folding.
PCB Thickness
PCB thickness is measured in thousandths of an inch (mils) or millimeters (mm). Common PCB thicknesses include:
Thickness (mils) | Thickness (mm) | Application |
---|---|---|
31.5 | 0.8 | Single-sided and double-sided PCBs |
39.4 | 1.0 | Double-sided and multilayer PCBs |
62.9 | 1.6 | Multilayer PCBs |
93.9 | 2.4 | High-power and Heavy Copper PCBs |
Understanding the material and thickness of your PCB is crucial for selecting the appropriate cutting method and tools.
PCB Cutting Methods
There are several methods for cutting PCBs, each with its own advantages and limitations. Let’s explore the most common PCB cutting techniques.
1. Manual Cutting
Manual cutting is suitable for small-scale production or prototyping. It involves using hand tools like saws, cutters, or shears to cut the PCB.
Tools for Manual PCB Cutting
- Hacksaw: A fine-toothed hacksaw can be used to cut PCBs along straight lines.
- Nibbling Tool: A nibbling tool removes small bits of material at a time, allowing for more intricate cuts.
- Shears: PCB shears are designed to cut through PCBs cleanly and precisely.
Advantages of Manual PCB Cutting
- Low cost and readily available tools
- Suitable for small-scale production or prototyping
- Allows for quick and simple cuts
Disadvantages of Manual PCB Cutting
- Time-consuming for larger quantities
- Limited precision and accuracy
- Risk of damaging the PCB or components
2. Mechanical Cutting
Mechanical cutting involves using powered machines to cut PCBs with high precision and speed. It is suitable for high-volume production and complex PCB designs.
Types of Mechanical PCB Cutting Machines
- PCB Depaneling Machine: Automated machines that use cutting blades or routers to separate individual PCBs from a panel.
- CNC Router: Computer-controlled routers that use high-speed spindles and cutting bits to cut PCBs along programmed paths.
- PCB Punch Machine: Uses a die and punch to create precise holes or cutouts in PCBs.
Advantages of Mechanical PCB Cutting
- High precision and accuracy
- Faster than manual cutting methods
- Suitable for high-volume production
- Consistent and repeatable results
Disadvantages of Mechanical PCB Cutting
- Higher initial investment in equipment
- Requires skilled operators and programming
- Limited flexibility for design changes
3. Laser Cutting
Laser cutting uses a high-powered laser beam to vaporize or melt the PCB material along a programmed path. It offers high precision and is suitable for intricate designs.
Types of Lasers Used for PCB Cutting
- CO2 Laser: Commonly used for cutting non-metallic materials like FR-4 PCBs.
- Fiber Laser: Suitable for cutting metallic materials like Aluminum PCBs.
- UV Laser: Offers high precision and minimal thermal damage, ideal for sensitive components.
Advantages of Laser PCB Cutting
- Extremely high precision and accuracy
- Minimal thermal damage to surrounding areas
- Suitable for intricate designs and small features
- No physical contact with the PCB, reducing the risk of damage
Disadvantages of Laser PCB Cutting
- High initial investment in equipment
- Requires specialized knowledge and training
- Limited material thickness capabilities compared to mechanical cutting
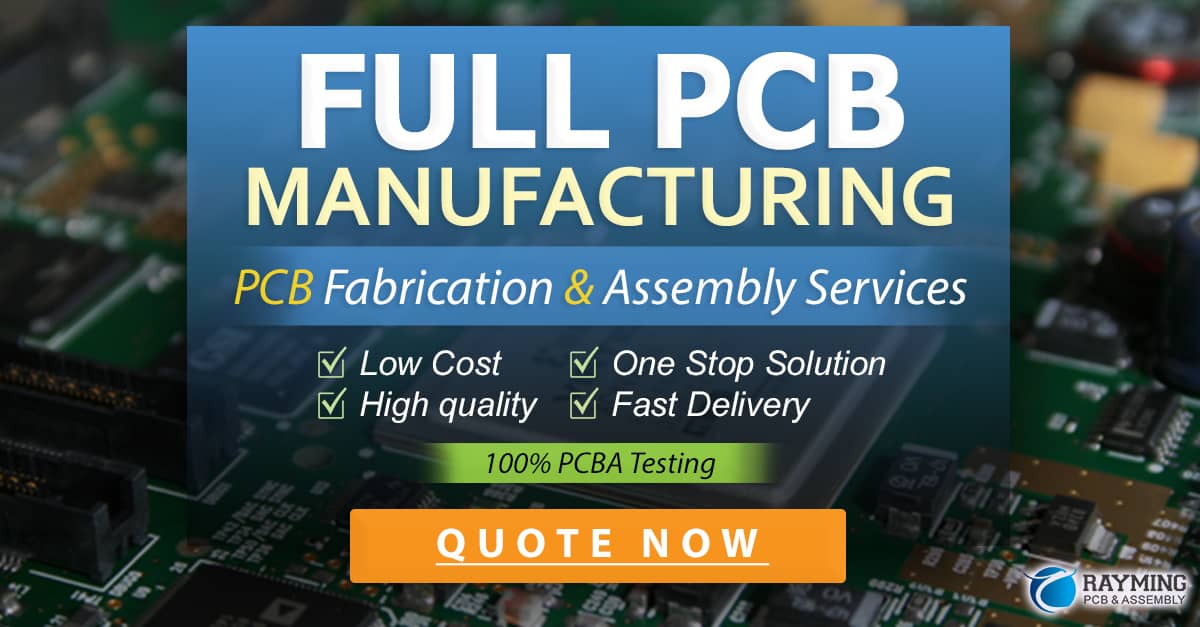
PCB Cutting Techniques
To achieve clean and precise cuts, consider the following techniques when cutting PCBs:
Scoring and Snapping
For straight cuts, scoring the PCB along the desired line using a sharp knife or scoring tool can make it easier to snap the board cleanly. This technique works well for thin PCBs and can be done manually.
Tabbed Designs
Incorporating tabs into the PCB design allows for easier separation of individual boards from a panel. The tabs can be cut or snapped off after the depaneling process, leaving smooth edges.
V-Groove Cutting
V-groove cutting involves creating a V-shaped groove along the cutting line on the PCB. This weakens the board, making it easier to snap along the groove. V-groove cutting can be done using a specialized V-groove router bit or a Laser Cutter.
Perforated Designs
Similar to tabbed designs, perforated designs incorporate small holes or slots along the cutting line. These perforations make it easier to separate the individual boards by breaking along the perforations.
Safety Considerations
When cutting PCBs, it’s essential to prioritize safety. Follow these guidelines to ensure a safe working environment:
- Wear protective eyewear to shield your eyes from debris or laser reflections.
- Use appropriate respiratory protection, especially when cutting materials that may release harmful particles.
- Ensure proper ventilation to remove any fumes or dust generated during the cutting process.
- Follow the manufacturer’s instructions and safety guidelines for the cutting equipment you are using.
- Properly dispose of any PCB waste, as it may contain hazardous materials.
Frequently Asked Questions (FAQ)
-
What is the best method for cutting PCBs in small quantities?
For small quantities or prototyping, manual cutting methods like using a hacksaw or nibbling tool are often sufficient. They are low-cost and require minimal setup. -
Can I use a regular saw to cut PCBs?
While a regular saw can be used to cut PCBs, it is recommended to use a fine-toothed saw designed for cutting metal or plastic. This will help achieve cleaner and more precise cuts. -
How do I choose between mechanical cutting and laser cutting for PCB fabrication?
The choice between mechanical cutting and laser cutting depends on factors like production volume, PCB design complexity, material thickness, and budget. Mechanical cutting is suitable for high-volume production and thicker materials, while laser cutting offers high precision and is ideal for intricate designs and sensitive components. -
What safety precautions should I take when cutting PCBs?
Always wear protective eyewear and respiratory protection when cutting PCBs. Ensure proper ventilation to remove any fumes or dust, and follow the manufacturer’s safety guidelines for the cutting equipment. Properly dispose of PCB waste, as it may contain hazardous materials. -
Can I cut PCBs with a laser cutter designed for other materials?
While it is possible to cut PCBs with a laser cutter designed for other materials, it is recommended to use a laser cutter specifically designed for PCB fabrication. PCB laser cutters are optimized for the specific materials and thicknesses used in PCBs, ensuring optimal results and minimizing the risk of damage to the board or components.
Conclusion
Cutting PCBs is a crucial step in the PCB fabrication process. By understanding the various methods, techniques, and safety considerations involved, you can achieve precise and clean cuts for your PCB projects. Whether you choose manual cutting, mechanical cutting, or laser cutting, the key is to select the method that best suits your needs, budget, and production scale. With the right tools and techniques, you can efficiently cut PCBs and bring your electronic designs to life.
0 Comments