Introduction to Medical PCB Prototype
In the rapidly advancing field of modern medicine, medical PCB (Printed Circuit Board) prototypes have emerged as a crucial component in the development and implementation of innovative medical devices and technologies. These specialized circuit boards are designed to meet the stringent requirements of the medical industry, ensuring reliable performance, accuracy, and patient safety. This article delves into the significance of medical PCB Prototypes in contemporary healthcare and explores their emergence as a game-changer in the medical landscape.
What is a Medical PCB Prototype?
A medical PCB prototype is a customized printed circuit board designed specifically for use in medical devices and equipment. These prototypes are created to meet the unique demands of the medical industry, such as high reliability, precision, and adherence to strict regulatory standards. Medical PCB prototypes serve as the foundation for various medical applications, ranging from diagnostic tools and monitoring systems to implantable devices and surgical instruments.
The Role of Medical PCB Prototypes in Modern Medicine
1. Enabling Innovative Medical Devices
Medical PCB prototypes play a pivotal role in the development of cutting-edge medical devices. These prototypes allow engineers and researchers to test and refine their designs, ensuring optimal functionality and performance before mass production. By leveraging the capabilities of medical PCB prototypes, medical device manufacturers can push the boundaries of innovation, creating more advanced and effective solutions for diagnosing, treating, and managing various health conditions.
2. Enhancing Diagnostic Accuracy
In the realm of medical diagnostics, PCB prototypes contribute to the development of highly accurate and reliable diagnostic tools. From portable ultrasound machines and digital X-ray systems to wearable health monitoring devices, medical PCB prototypes form the core of these technologies. By integrating sophisticated sensors, data processing units, and communication modules, these prototypes enable precise data acquisition, analysis, and transmission, ultimately leading to improved diagnostic accuracy and early detection of diseases.
3. Facilitating Minimally Invasive Procedures
Medical PCB prototypes have revolutionized the field of minimally invasive surgery. Miniaturized PCBs, equipped with advanced sensors and control systems, are integral to the development of laparoscopic instruments, endoscopes, and robotic surgical systems. These prototypes enable precise control, real-time image guidance, and seamless integration with other medical technologies, allowing surgeons to perform complex procedures with greater precision, reduced tissue trauma, and faster patient recovery.
4. Enabling Personalized Medicine
The advent of medical PCB prototypes has paved the way for personalized medicine, where treatments are tailored to individual patient needs. Customized PCB designs facilitate the development of wearable devices, implantable sensors, and drug delivery systems that can monitor and respond to a patient’s unique physiological parameters. By collecting and analyzing real-time patient data, these prototypes enable healthcare providers to optimize treatment plans, monitor treatment efficacy, and make informed decisions based on individual patient responses.
The Emergence of Medical PCB Prototypes
Advancements in PCB Manufacturing Technologies
The emergence of medical PCB prototypes can be attributed to the significant advancements in PCB manufacturing technologies over the past few decades. Innovations in materials science, such as the development of biocompatible substrates and conductive inks, have enabled the creation of PCBs that meet the stringent requirements of the medical industry. Additionally, improvements in PCB fabrication techniques, including high-density interconnect (HDI) technology and 3D printing, have allowed for the production of more complex and miniaturized PCB designs.
Regulatory Standards and Compliance
The medical device industry is subject to rigorous regulatory standards to ensure patient safety and device effectiveness. The emergence of medical PCB prototypes has been driven by the need to comply with these standards, such as the FDA’s Quality System Regulation (QSR) and the ISO 13485 standard for medical device quality management systems. Medical PCB manufacturers must adhere to strict guidelines for design, production, and testing to meet these regulatory requirements, ensuring the reliability and safety of the final product.
Collaborative Efforts between Medical and Engineering Disciplines
The emergence of medical PCB prototypes has been fueled by the growing collaboration between medical professionals and engineering experts. Interdisciplinary teams, consisting of physicians, biomedical engineers, and PCB designers, work together to identify clinical needs, develop innovative solutions, and translate them into functional prototypes. This collaborative approach has accelerated the development of medical PCB prototypes, bringing together the expertise of both domains to create more effective and patient-centric medical devices.
Challenges and Future Prospects
Challenges in Medical PCB Prototype Development
Despite the significant advancements in medical PCB prototypes, several challenges remain. One of the primary challenges is the need for miniaturization while maintaining high performance and reliability. As medical devices become smaller and more complex, PCB designers must find innovative ways to integrate multiple components and functionalities into compact form factors. Additionally, ensuring the long-term reliability of medical PCBs in the harsh environment of the human body poses another challenge, requiring the use of biocompatible materials and robust manufacturing processes.
Future Prospects and Trends
The future of medical PCB prototypes looks promising, with several exciting trends on the horizon. One of the key trends is the integration of artificial intelligence (AI) and machine learning algorithms into medical PCBs. By incorporating AI capabilities, medical devices can analyze vast amounts of patient data in real-time, enabling predictive diagnostics, personalized treatment recommendations, and early detection of potential health issues. Another trend is the development of flexible and stretchable PCBs that can conform to the contours of the human body, opening up new possibilities for wearable and implantable medical devices.
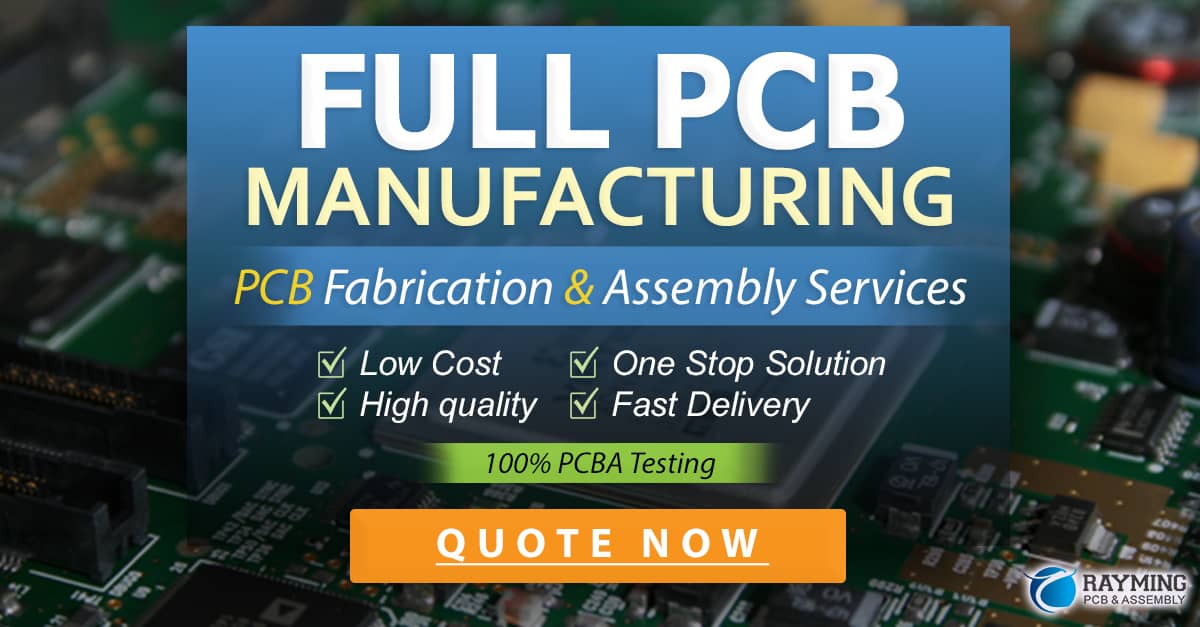
FAQs
-
Q: What is the difference between a medical PCB prototype and a regular PCB?
A: Medical PCB prototypes are designed to meet the specific requirements of the medical industry, such as biocompatibility, high reliability, and adherence to strict regulatory standards. They often incorporate specialized materials, components, and manufacturing processes to ensure optimal performance and patient safety. -
Q: How long does it take to develop a medical PCB prototype?
A: The development timeline for a medical PCB prototype varies depending on the complexity of the design, the regulatory requirements, and the collaboration between medical and engineering teams. It can range from several weeks to several months, including the design, fabrication, testing, and validation phases. -
Q: What are the key considerations when designing a medical PCB prototype?
A: When designing a medical PCB prototype, key considerations include biocompatibility, miniaturization, signal integrity, power management, and reliability. Designers must also take into account the specific clinical application, user requirements, and regulatory standards to ensure the prototype meets the desired functionality and safety criteria. -
Q: How do medical PCB prototypes contribute to personalized medicine?
A: Medical PCB prototypes enable the development of wearable devices, implantable sensors, and drug delivery systems that can monitor and respond to individual patient needs. By collecting and analyzing real-time patient data, these prototypes facilitate personalized treatment plans, optimize treatment efficacy, and allow for informed decision-making based on individual patient responses. -
Q: What are the future prospects for medical PCB prototypes?
A: The future of medical PCB prototypes is expected to witness the integration of artificial intelligence and machine learning algorithms, enabling predictive diagnostics and personalized treatment recommendations. Additionally, the development of flexible and stretchable PCBs will open up new possibilities for wearable and implantable medical devices that can conform to the contours of the human body.
Conclusion
Medical PCB prototypes have emerged as a critical component in the advancement of modern medicine. By enabling innovative medical devices, enhancing diagnostic accuracy, facilitating minimally invasive procedures, and paving the way for personalized medicine, these prototypes have revolutionized the healthcare landscape. The emergence of medical PCB prototypes can be attributed to advancements in PCB manufacturing technologies, adherence to regulatory standards, and collaborative efforts between medical and engineering disciplines.
As the medical industry continues to evolve, medical PCB prototypes will play an increasingly important role in shaping the future of healthcare. With ongoing advancements in miniaturization, integration of AI capabilities, and the development of flexible and stretchable PCBs, the possibilities for medical PCB prototypes are vast. By leveraging these innovations, healthcare providers can deliver more accurate diagnoses, personalized treatments, and improved patient outcomes, ultimately transforming the way we approach healthcare in the years to come.
0 Comments