Introduction to PCB Through-Holes
Printed Circuit Boards (PCBs) are essential components in modern electronics, providing a platform for interconnecting various electronic components. One crucial aspect of PCB design is the use of through-holes, which are small holes drilled through the board to allow for the insertion of component leads or the creation of electrical connections between different layers of the board. Among the different types of through-holes, plated through-holes (PTHs) stand out for their ability to significantly enhance the performance and reliability of PCBs.
What are Plated Through-Holes?
Plated through-holes are a specific type of through-hole in which the inner walls of the hole are coated with a conductive material, typically copper. This plating process creates an electrical connection between the top and bottom layers of the PCB, as well as any inner layers that the hole passes through. The plating is applied using an electroplating process, which ensures a uniform and reliable coating throughout the hole.
Advantages of Plated Through-Holes
Plated through-holes offer several key advantages over non-plated through-holes:
-
Electrical Connectivity: The conductive plating in PTHs allows for reliable electrical connections between different layers of the PCB, enabling more complex and compact circuit designs.
-
Mechanical Strength: The plating process reinforces the structure of the through-hole, making it more resistant to mechanical stress and vibration.
-
Thermal Conductivity: The copper plating in PTHs helps to dissipate heat more efficiently, which is particularly important for high-power components.
-
Solderability: Plated through-holes provide a superior surface for soldering components, ensuring a strong and reliable connection.
How Plated Through-Holes Enhance PCB Performance
Improved Signal Integrity
One of the primary benefits of using plated through-holes in PCB design is the improvement in signal integrity. Signal integrity refers to the quality and reliability of the electrical signals transmitted through the PCB. By providing a consistent and low-resistance electrical path between layers, PTHs help to minimize signal loss, distortion, and interference.
Reduction in Impedance Mismatch
Impedance mismatch occurs when there is a difference in the characteristic impedance between two points in a signal path, leading to signal reflections and degradation. Plated through-holes help to maintain a consistent impedance throughout the signal path, reducing the occurrence of impedance mismatches and ensuring cleaner signal transmission.
Minimizing Cross-talk
Cross-talk is the unwanted coupling of signals between adjacent traces or components on a PCB. By using plated through-holes to route signals between layers, designers can effectively shield sensitive signals from the influence of neighboring traces, minimizing cross-talk and improving overall signal integrity.
Enhanced Power Delivery
Plated through-holes also play a crucial role in optimizing power delivery on PCBs. In modern electronics, the demand for stable and efficient power distribution is ever-increasing, and PTHs help to meet this challenge.
Low-Resistance Power Distribution
The copper plating in PTHs provides a low-resistance path for power distribution, allowing for efficient and uniform power delivery to components across the PCB. This is particularly important for high-current applications, where minimizing power losses is critical.
Improved Voltage Regulation
By utilizing plated through-holes for power distribution, designers can achieve better voltage regulation across the PCB. The low-resistance paths created by PTHs help to maintain a stable voltage level, minimizing voltage drops and ensuring that components receive the required power supply for optimal performance.
Thermal Management
Effective thermal management is essential for maintaining the reliability and longevity of electronic components on a PCB. Plated through-holes contribute to improved thermal management by providing an efficient path for heat dissipation.
Heat Dissipation through PTHs
The copper plating in PTHs acts as a thermal conductor, allowing heat generated by components to be efficiently transferred through the board and dissipated into the environment. This helps to prevent localized hot spots and reduces the risk of component failure due to thermal stress.
Thermal Vias
In addition to their use for electrical connectivity, plated through-holes can also be used as thermal vias. Thermal vias are strategically placed PTHs that are designed to transfer heat away from high-power components, such as processors or power regulators. By creating a low-resistance thermal path, these vias help to maintain acceptable operating temperatures and improve overall system reliability.
Mechanical Robustness
Plated through-holes contribute to the mechanical robustness of PCBs, making them more resistant to physical stress and vibration. This is particularly important in applications where the PCB is subject to harsh environmental conditions or frequent handling.
Reinforced Hole Structure
The electroplating process used to create PTHs results in a reinforced hole structure, with the copper plating adding strength and rigidity to the hole walls. This reinforcement helps to prevent hole deformation or collapse, even under significant mechanical stress.
Improved Component Retention
Plated through-holes provide a secure and reliable mounting point for through-hole components. The plating process creates a strong bond between the component leads and the hole walls, reducing the risk of component loosening or falling out due to vibration or physical shock.
PCB Through-Hole Plating Process
To achieve the benefits of plated through-holes, PCB manufacturers follow a specific plating process. This process ensures a uniform and reliable conductive coating is applied to the hole walls.
Drilling
The first step in the through-hole plating process is drilling the holes into the PCB substrate. This is typically done using a computer-controlled drilling machine, which ensures precise hole placement and consistent hole diameters.
Deburring and Cleaning
After drilling, the holes are deburred to remove any rough edges or debris that may have been created during the drilling process. The board is then thoroughly cleaned to remove any contaminants that could interfere with the plating process.
Electroless Copper Deposition
The next step is to apply an initial layer of copper to the hole walls using an electroless deposition process. This process involves immersing the board in a copper plating solution, which deposits a thin layer of copper onto the hole walls through a chemical reaction.
Electrolytic Copper Plating
Once the initial copper layer is in place, the board undergoes an electrolytic copper plating process. In this process, an electrical current is applied to the board while it is immersed in a copper plating solution. This current causes the copper ions in the solution to be attracted to the hole walls, building up a thicker layer of copper plating.
Final Finishing
After the electrolytic copper plating, the board may undergo additional finishing processes, such as solder mask application or surface finish plating, depending on the specific requirements of the PCB design.
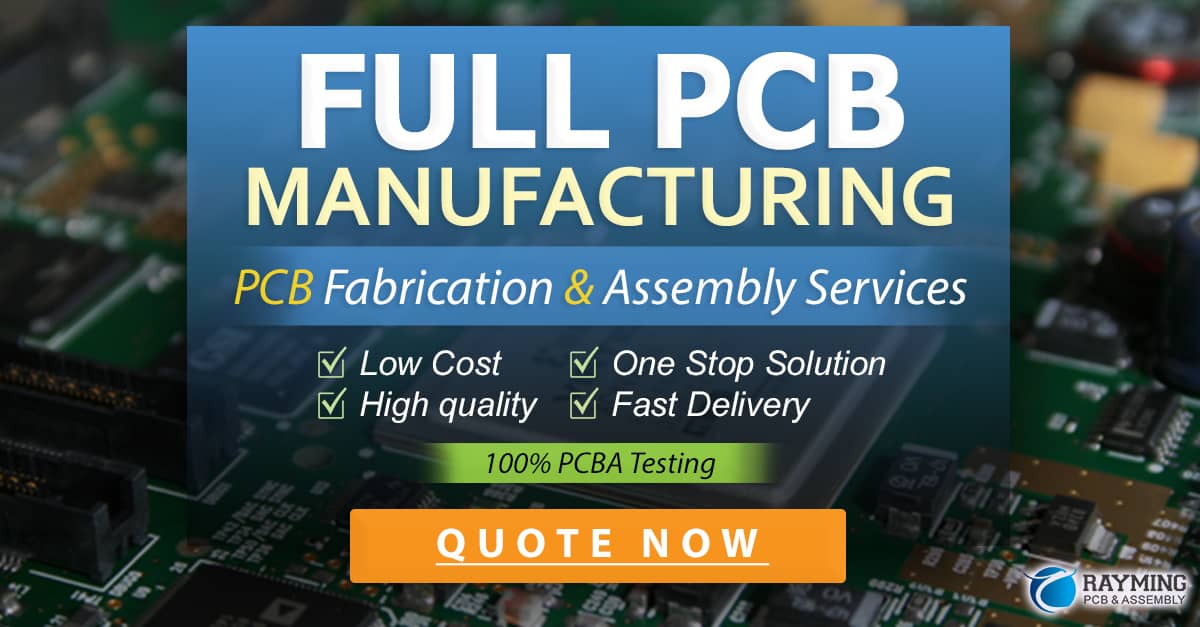
Design Considerations for Plated Through-Holes
When incorporating plated through-holes into a PCB design, there are several key factors to consider to ensure optimal performance and manufacturability.
Hole Size and Aspect Ratio
The size of the plated through-holes and their aspect ratio (the ratio of hole depth to diameter) are critical design parameters. Smaller hole diameters and higher aspect ratios can pose challenges for the plating process, as it becomes more difficult to achieve uniform plating coverage. Designers must strike a balance between the electrical requirements of the circuit and the manufacturability of the PTHs.
Hole Diameter | Aspect Ratio | Plating Difficulty |
---|---|---|
> 0.5 mm | < 5:1 | Low |
0.3 – 0.5 mm | 5:1 – 8:1 | Moderate |
< 0.3 mm | > 8:1 | High |
Pad Size and Annular Ring
The pad size and annular ring around plated through-holes are also important considerations. The pad size must be sufficient to accommodate the component lead and provide a reliable soldering surface. The annular ring, which is the copper area surrounding the hole, must be wide enough to ensure a strong connection between the pad and the hole plating. Inadequate pad size or annular ring width can lead to soldering difficulties and reduced reliability.
Copper Thickness
The thickness of the copper plating in the through-holes is another critical factor. Thicker copper plating provides lower resistance and better thermal conductivity, but it also increases the cost and complexity of the manufacturing process. Designers must specify the appropriate copper thickness based on the electrical and thermal requirements of the circuit, while also considering the manufacturability and cost implications.
Copper Thickness | Electrical Performance | Thermal Performance | Manufacturing Complexity |
---|---|---|---|
1 oz (35 µm) | Good | Moderate | Low |
2 oz (70 µm) | Excellent | Good | Moderate |
3 oz (105 µm) | Excellent | Excellent | High |
Via Placement and Spacing
The placement and spacing of plated through-holes, particularly when used as vias, is another important design consideration. Vias should be placed strategically to minimize signal path lengths and reduce the risk of signal integrity issues. Adequate spacing between vias is necessary to ensure manufacturability and prevent shorts or other defects.
FAQs
1. What is the difference between plated and non-plated through-holes?
Plated through-holes have a conductive coating, typically copper, applied to the inner walls of the hole, creating an electrical connection between layers. Non-plated through-holes do not have this conductive coating and are used primarily for mechanical purposes or component mounting.
2. Can plated through-holes be used for both electrical and mechanical purposes?
Yes, plated through-holes can serve both electrical and mechanical functions. In addition to providing electrical connectivity between layers, the plating process reinforces the hole structure, making it more resistant to mechanical stress and vibration.
3. How does the aspect ratio of a plated through-hole affect its manufacturability?
Higher aspect ratios (hole depth to diameter) pose challenges for the plating process, as it becomes more difficult to achieve uniform plating coverage. Designers must consider the aspect ratio when specifying hole sizes to ensure manufacturability and reliability.
4. What is the role of copper thickness in plated through-holes?
The copper thickness in plated through-holes influences their electrical and thermal performance. Thicker copper plating provides lower resistance and better thermal conductivity, but it also increases manufacturing complexity and cost. Designers must strike a balance between performance requirements and manufacturability.
5. How do plated through-holes contribute to thermal management on a PCB?
Plated through-holes act as thermal conductors, allowing heat generated by components to be efficiently transferred through the board and dissipated into the environment. They can also be used as thermal vias, strategically placed to transfer heat away from high-power components and maintain acceptable operating temperatures.
Conclusion
Plated through-holes are a critical aspect of PCB design, offering numerous benefits that enhance the performance, reliability, and manufacturability of electronic circuits. By providing reliable electrical connectivity, improving signal integrity, enhancing power delivery, and contributing to thermal management and mechanical robustness, PTHs enable the development of more complex and efficient electronic systems.
When incorporating plated through-holes into a PCB design, it is essential to consider factors such as hole size, aspect ratio, pad size, annular ring, copper thickness, and via placement. By carefully balancing these design parameters, engineers can optimize the performance of their PCBs while ensuring cost-effective and reliable manufacturing.
As electronic devices continue to advance in complexity and functionality, the role of plated through-holes in PCB design will remain crucial. By understanding the benefits and design considerations associated with PTHs, engineers can create PCBs that meet the ever-increasing demands of modern electronics, driving innovation and technological progress across a wide range of industries.
0 Comments