The Importance of PCB Cleanliness
Printed Circuit Boards (PCBs) are the backbone of modern electronic devices. They are responsible for connecting and supporting various components that make up a system. The performance and reliability of these systems heavily depend on the cleanliness of the PCBs. Contaminants on the surface of a PCB can lead to various issues, such as short circuits, corrosion, and signal interference, which can ultimately affect the overall system performance.
Types of Contaminants
There are various types of contaminants that can accumulate on a PCB surface:
-
Flux residues: Flux is used during the soldering process to prevent oxidation and improve solder joint quality. However, if not properly cleaned, flux residues can attract moisture and cause corrosion.
-
Dust and debris: Dust particles and other debris can settle on the PCB surface during manufacturing, assembly, or storage. These contaminants can cause short circuits and interfere with signal transmission.
-
Oils and greases: Fingerprints, lubricants, and other oils can contaminate the PCB surface during handling. These contaminants can degrade the adhesion of conformal coatings and affect the performance of high-frequency circuits.
-
Ionic contamination: Ionic contamination refers to the presence of charged particles on the PCB surface. These particles can come from various sources, such as plating solutions, human sweat, and environmental pollutants. Ionic contamination can lead to electrochemical migration and dendrite growth, which can cause short circuits and system failures.
Measuring PCB Cleanliness
To ensure the cleanliness of PCBs, it is essential to measure the level of contamination. There are several methods for measuring PCB cleanliness:
-
Visual inspection: Visual inspection is the most basic method for assessing PCB cleanliness. It involves examining the PCB surface under magnification for visible contaminants, such as flux residues, dust, and debris.
-
Resistivity of Solvent Extract (ROSE) testing: ROSE testing is a widely used method for measuring ionic contamination on PCBs. It involves washing the PCB with a solvent and measuring the resistivity of the resulting solution. The resistivity value indicates the level of ionic contamination on the PCB surface.
-
Ion chromatography: Ion chromatography is a more accurate method for measuring ionic contamination. It involves extracting the ions from the PCB surface and separating them based on their charge and size. This method can identify specific ionic species and their concentrations.
-
Fourier Transform Infrared (FTIR) spectroscopy: FTIR spectroscopy is used to identify organic contaminants, such as oils and greases, on the PCB surface. It works by measuring the absorption of infrared light by the contaminants and comparing the resulting spectrum with known reference spectra.
Method | Contaminants Detected | Advantages | Disadvantages |
---|---|---|---|
Visual Inspection | Visible contaminants | Quick and easy | Limited to visible contaminants |
ROSE Testing | Ionic contamination | Widely used, relatively simple | Does not identify specific ionic species |
Ion Chromatography | Ionic contamination | Identifies specific ionic species and concentrations | Requires specialized equipment and expertise |
FTIR Spectroscopy | Organic contaminants | Identifies specific organic compounds | Requires specialized equipment and expertise |
Cleaning Methods
Once the level and type of contamination have been determined, appropriate cleaning methods can be selected. The choice of cleaning method depends on various factors, such as the type of contaminant, the PCB material, and the components on the board.
-
Solvent cleaning: Solvent cleaning involves using organic solvents, such as isopropyl alcohol (IPA) or acetone, to dissolve and remove contaminants from the PCB surface. This method is effective for removing flux residues, oils, and greases. However, it is important to ensure that the solvents used are compatible with the PCB material and components.
-
Aqueous cleaning: Aqueous cleaning uses water-based solutions to remove contaminants from the PCB surface. This method is effective for removing ionic contamination and is more environmentally friendly than solvent cleaning. Aqueous cleaning solutions often contain surfactants and other additives to improve their cleaning performance.
-
Plasma cleaning: Plasma cleaning uses ionized gas to remove contaminants from the PCB surface. This method is effective for removing organic contaminants and is particularly useful for cleaning high-density PCBs with tight spaces between components. Plasma cleaning is a dry process and does not require the use of solvents or water.
-
Ultrasonic cleaning: Ultrasonic cleaning uses high-frequency sound waves to agitate a cleaning solution and remove contaminants from the PCB surface. This method is effective for removing particles and debris that are trapped in tight spaces or under components. Ultrasonic cleaning can be used with both solvent and aqueous cleaning solutions.
Cleaning Method | Contaminants Removed | Advantages | Disadvantages |
---|---|---|---|
Solvent Cleaning | Flux residues, oils, greases | Effective for removing organic contaminants | May not be compatible with certain PCB materials |
Aqueous Cleaning | Ionic contamination | Environmentally friendly, effective for ionic contamination | May not be effective for certain organic contaminants |
Plasma Cleaning | Organic contaminants | Dry process, effective for high-density PCBs | Requires specialized equipment |
Ultrasonic Cleaning | Particles, debris | Effective for removing trapped contaminants | May damage delicate components |
Effects of PCB Contamination on System Performance
PCB contamination can have various effects on system performance, depending on the type and level of contamination. Some of the most common effects include:
-
Short circuits: Contaminants, such as dust particles and debris, can bridge the gap between adjacent conductors on the PCB, causing short circuits. Short circuits can lead to system malfunctions, overheating, and even fires.
-
Signal interference: Contaminants on the PCB surface can interfere with signal transmission, particularly in high-frequency circuits. This can result in signal distortion, crosstalk, and reduced system performance.
-
Corrosion: Ionic contamination and moisture can lead to corrosion of the PCB conductors and components. Corrosion can cause open circuits, increased resistance, and reduced system reliability.
-
Degraded adhesion: Oils and greases on the PCB surface can degrade the adhesion of conformal coatings and other protective layers. This can lead to delamination and reduced protection against environmental factors, such as moisture and temperature changes.
-
Dendrite growth: Ionic contamination can cause the growth of conductive metal filaments, known as dendrites, between adjacent conductors on the PCB. Dendrite growth can lead to short circuits and system failures.
Case Studies
-
Automotive Electronics: In a study conducted by the National Physical Laboratory (NPL) in the UK, researchers found that ionic contamination on PCBs used in automotive electronics can lead to reduced reliability and premature failures. The study highlighted the importance of proper cleaning and contamination control in the manufacturing process to ensure the long-term reliability of automotive electronics.
-
Medical Devices: PCB cleanliness is particularly critical in medical devices, where system failures can have serious consequences for patient safety. In a case study published by the Association Connecting Electronics Industries (IPC), a medical device manufacturer experienced intermittent failures in a critical component. Investigation revealed that the failures were caused by ionic contamination on the PCB surface, which led to dendrite growth and short circuits. The manufacturer implemented a more stringent cleaning process and contamination monitoring program to prevent future failures.
-
Aerospace Applications: In the aerospace industry, PCBs are subjected to harsh environmental conditions, such as extreme temperatures, vibration, and radiation. Contamination on PCBs can exacerbate these effects and lead to system failures. In a study conducted by NASA, researchers found that ionic contamination on PCBs used in spacecraft can lead to dendrite growth and short circuits, particularly in the presence of moisture. The study emphasized the importance of thorough cleaning and contamination control to ensure the reliability of aerospace electronics.
Frequently Asked Questions (FAQ)
-
What are the most common sources of PCB contamination?
The most common sources of PCB contamination include flux residues from the soldering process, dust and debris from the manufacturing environment, oils and greases from handling, and ionic contamination from various sources, such as plating solutions and environmental pollutants. -
How can I determine the level of contamination on a PCB?
There are several methods for measuring PCB cleanliness, including visual inspection, Resistivity of Solvent Extract (ROSE) testing, ion chromatography, and Fourier Transform Infrared (FTIR) spectroscopy. The choice of method depends on the type of contaminant and the required level of accuracy. -
What are the most effective cleaning methods for removing PCB contamination?
The most effective cleaning methods for removing PCB contamination include solvent cleaning, aqueous cleaning, plasma cleaning, and ultrasonic cleaning. The choice of method depends on the type of contaminant, the PCB material, and the components on the board. -
Can PCB contamination cause long-term reliability issues?
Yes, PCB contamination can lead to long-term reliability issues, such as corrosion, dendrite growth, and delamination of protective coatings. These issues can cause system failures and reduced product lifetime. -
How can I prevent PCB contamination in my manufacturing process?
To prevent PCB contamination in your manufacturing process, you should implement strict contamination control measures, such as using clean room environments, wearing protective gear, and following proper handling procedures. Regular cleaning and monitoring of PCBs can also help identify and address contamination issues before they cause system failures.
Conclusion
PCB cleanliness is a critical factor in ensuring the performance and reliability of electronic systems. Contaminants on the PCB surface can lead to various issues, such as short circuits, signal interference, corrosion, and dendrite growth, which can ultimately affect the overall system performance. To prevent these issues, it is essential to implement proper cleaning and contamination control measures throughout the manufacturing process.
Regular monitoring of PCB cleanliness using appropriate measurement methods can help identify contamination issues early and prevent system failures. By selecting the most effective cleaning methods for the specific type of contamination and PCB material, manufacturers can ensure the long-term reliability and performance of their electronic products.
As electronic systems become more complex and miniaturized, the importance of PCB cleanliness will only continue to grow. By staying up to date with the latest cleaning technologies and best practices, manufacturers can stay ahead of the curve and deliver high-quality, reliable electronic products to their customers.
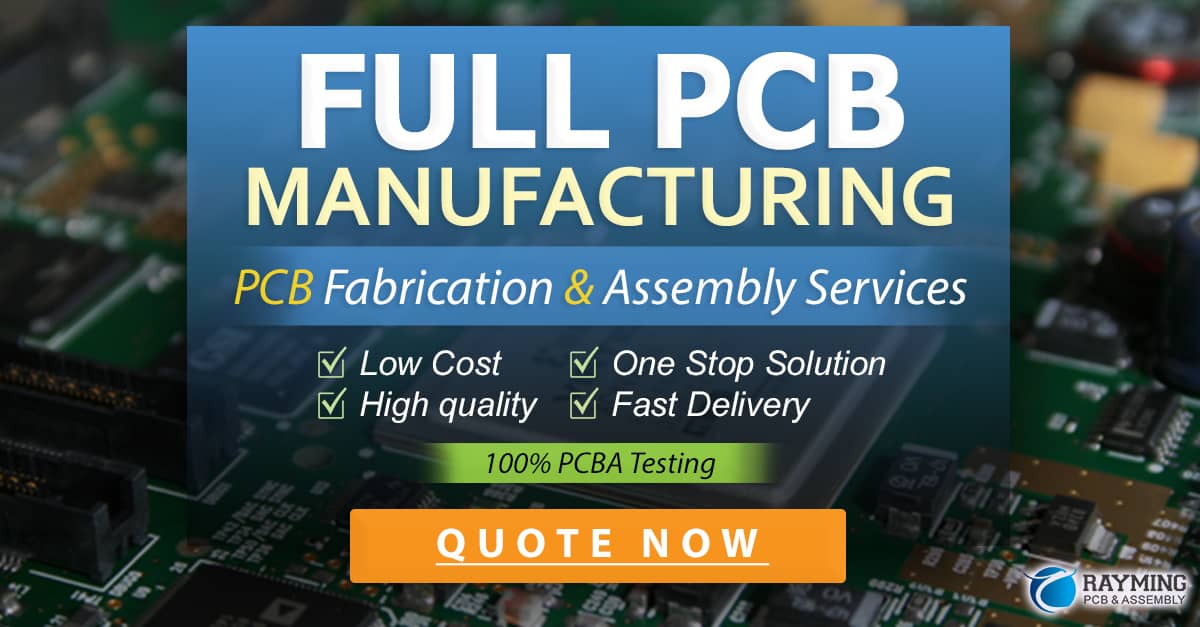
0 Comments