The Impact of Digitalization on Electronics Manufacturing
Digitalization is having a profound impact on all aspects of electronics manufacturing, from product design and development to production, supply chain management, and customer service. Here are some of the key ways digitalization is transforming the industry:
1. Smart Factories and Industry 4.0
One of the most significant impacts of digitalization on electronics manufacturing is the rise of smart factories and Industry 4.0. Smart factories use advanced technologies like IoT sensors, robotics, and AI to create a fully connected and automated production environment. This enables manufacturers to optimize their processes, reduce downtime, and improve quality control.
Technology | Description | Benefits |
---|---|---|
IoT Sensors | Sensors that collect real-time data on production processes and equipment | Enables predictive maintenance, reduces downtime, and improves quality control |
Robotics | Automated machines that perform tasks like assembly, testing, and packaging | Increases efficiency, reduces labor costs, and improves consistency and accuracy |
AI | Advanced algorithms that analyze data and optimize processes | Enables predictive analytics, improves decision-making, and drives continuous improvement |
2. Digital Twin Technology
Another key impact of digitalization on electronics manufacturing is the use of digital twin technology. A digital twin is a virtual replica of a physical product or process that can be used for simulation, testing, and optimization. By creating a digital twin of their products and production processes, electronics manufacturers can identify potential issues and optimize designs before committing to physical prototypes or production runs.
Benefits of Digital Twin Technology |
---|
Reduces development time and costs |
Improves product quality and reliability |
Enables faster time-to-market |
Facilitates collaboration and innovation |
3. 3D Printing and Additive Manufacturing
3D printing and additive manufacturing are also transforming electronics manufacturing by enabling faster prototyping, customization, and production of complex parts. With 3D printing, manufacturers can create prototypes and low-volume production runs quickly and cost-effectively, without the need for expensive tooling or molds.
Advantages of 3D Printing in Electronics Manufacturing |
---|
Faster prototyping and iteration |
Customization and personalization of products |
Production of complex geometries and lightweight parts |
Reduced inventory and supply chain costs |
4. Supply Chain Digitalization
Digitalization is also transforming the electronics supply chain, enabling greater visibility, agility, and resilience. By leveraging technologies like IoT, blockchain, and AI, manufacturers can track products and materials in real-time, optimize inventory levels, and respond quickly to changes in demand or supply.
Benefits of Supply Chain Digitalization |
---|
Real-time visibility and tracking |
Improved forecasting and demand planning |
Reduced inventory costs and waste |
Faster response to disruptions and changes |
5. Customer-Centric Innovation
Finally, digitalization is enabling electronics manufacturers to become more customer-centric and innovative. By leveraging data analytics and digital platforms, manufacturers can gain deeper insights into customer needs and preferences, and develop new products and services that meet those needs.
Examples of Customer-Centric Innovation in Electronics Manufacturing |
---|
Personalized and customized products |
Subscription-based services and solutions |
Predictive maintenance and remote monitoring |
Co-creation and open innovation with customers and partners |
Challenges and Opportunities for Electronics Manufacturers
While digitalization offers many benefits for electronics manufacturers, it also presents some challenges and opportunities. Here are some of the key considerations for manufacturers looking to embrace digital transformation:
1. Investment and ROI
Implementing digital technologies requires significant investment in hardware, software, and talent. Manufacturers need to carefully evaluate the potential return on investment (ROI) and prioritize initiatives that will deliver the greatest value.
2. Skills and Talent
Digitalization also requires new skills and talent, particularly in areas like data science, AI, and robotics. Manufacturers need to invest in training and development programs to upskill their existing workforce, as well as recruit new talent with the necessary skills.
3. Cybersecurity and Data Privacy
As manufacturers become more connected and data-driven, they also become more vulnerable to cyber attacks and data breaches. Ensuring the security and privacy of sensitive data is critical to maintaining trust and compliance with regulations like GDPR.
4. Collaboration and Ecosystem
Digitalization also requires greater collaboration and partnership across the electronics manufacturing ecosystem. Manufacturers need to work closely with suppliers, customers, and technology providers to develop and implement digital solutions that create value for all stakeholders.
The Future of Electronics Manufacturing
Looking ahead, the future of electronics manufacturing is likely to be shaped by continued digitalization and innovation. Here are some of the key trends and predictions for the industry:
1. Increased Automation and Robotics
As the cost of robotics and automation continues to decline, more manufacturers will adopt these technologies to increase efficiency, reduce costs, and improve quality. This will lead to more fully automated factories and production lines, with humans working alongside robots in collaborative roles.
2. Growth of IoT and Connected Devices
The growth of the Internet of Things (IoT) and connected devices will continue to drive demand for electronics manufacturing. As more products become connected and intelligent, manufacturers will need to develop new capabilities in areas like wireless connectivity, sensor integration, and edge computing.
3. Sustainable and Circular Manufacturing
Sustainability and circularity will become increasingly important in electronics manufacturing, as consumers and regulators demand more environmentally friendly products and practices. Manufacturers will need to adopt sustainable materials, design for recyclability, and implement circular business models that minimize waste and extend product lifecycles.
4. Personalization and Customization
Personalization and customization will become more prevalent in electronics manufacturing, as consumers demand products that are tailored to their individual needs and preferences. Manufacturers will need to leverage digital technologies like 3D printing, AI, and data analytics to enable mass customization and personalization at scale.
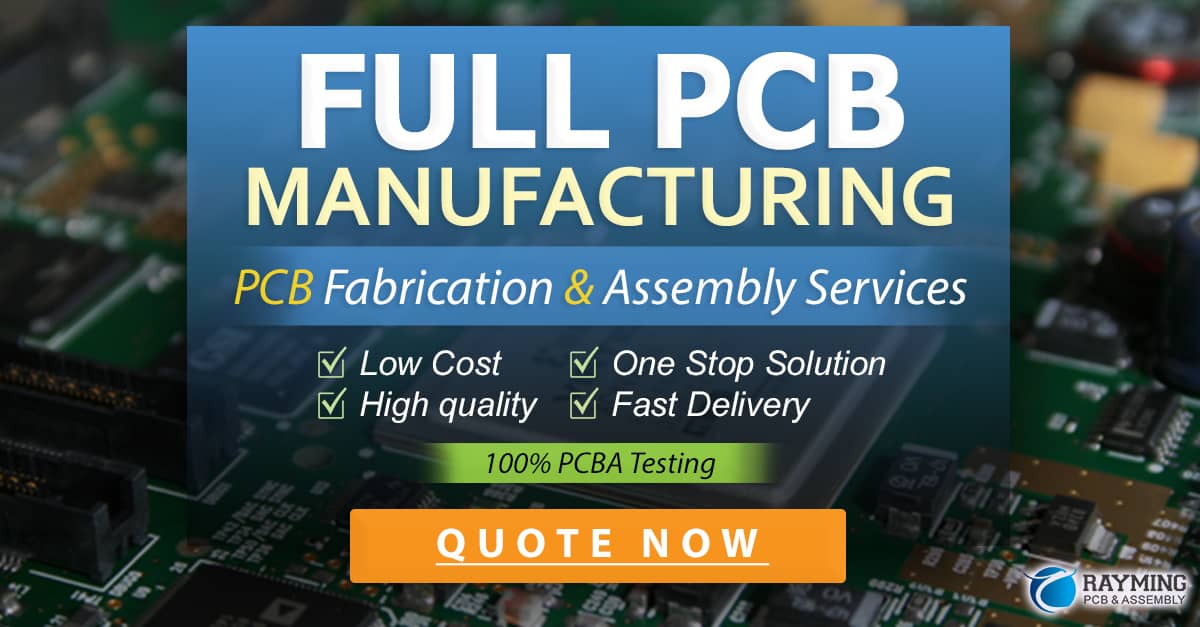
Frequently Asked Questions (FAQ)
1. What is digitalization in electronics manufacturing?
Digitalization in electronics manufacturing refers to the use of digital technologies like IoT, AI, robotics, and 3D printing to transform product design, production, and supply chain management. It involves the integration of physical and digital systems to create a fully connected and automated manufacturing environment.
2. What are the benefits of digitalization for electronics manufacturers?
The benefits of digitalization for electronics manufacturers include:
- Increased efficiency and productivity
- Reduced costs and waste
- Improved quality and consistency
- Faster time-to-market and innovation
- Greater flexibility and agility
- Enhanced customer experience and satisfaction
3. What are some of the key technologies driving digitalization in electronics manufacturing?
Some of the key technologies driving digitalization in electronics manufacturing include:
- Internet of Things (IoT) sensors and connectivity
- Artificial intelligence (AI) and machine learning
- Robotics and automation
- 3D printing and additive manufacturing
- Digital twin technology
- Blockchain and distributed ledger technology
4. What challenges do electronics manufacturers face in implementing digitalization?
Some of the challenges electronics manufacturers face in implementing digitalization include:
- High upfront investment costs and uncertain ROI
- Lack of skilled talent and expertise in digital technologies
- Cybersecurity and data privacy risks
- Integration and interoperability issues with legacy systems
- Change management and cultural resistance to new ways of working
5. What will the future of electronics manufacturing look like with continued digitalization?
The future of electronics manufacturing with continued digitalization is likely to be characterized by:
- Increased automation and human-robot collaboration
- Growth of IoT and connected devices
- Sustainable and circular manufacturing practices
- Personalization and customization of products and services
- Greater collaboration and partnership across the electronics manufacturing ecosystem
Conclusion
Digitalization is transforming the electronics manufacturing industry, enabling manufacturers to increase efficiency, flexibility, and innovation while reducing costs and time-to-market. By leveraging technologies like IoT, AI, robotics, and 3D printing, manufacturers can create smart factories, optimize production processes, and deliver personalized products and services to customers.
However, digitalization also presents challenges and opportunities for manufacturers, requiring significant investment, new skills and talent, and greater collaboration across the ecosystem. As the industry continues to evolve and innovate, manufacturers that embrace digitalization and adapt to the changing landscape will be well-positioned for success in the future.
0 Comments