What Are High Tg PCBs?
A printed circuit board’s glass transition temperature (Tg) is the point at which the board transitions from a rigid, glassy state to a more flexible, rubbery state as temperature increases. Standard FR-4 PCBs made of woven fiberglass cloth with epoxy resin have a Tg around 130-140°C. Above this temperature, the epoxy softens and the board’s structural integrity degrades.
In contrast, high TG PCBs utilize alternative materials that can maintain mechanical strength and stable electrical properties at much higher temperatures. The most common high TG laminates and solder masks have glass transition points ranging from 170°C to over 250°C.
High TG PCB materials include:
Material | Tg (°C) | Td (°C) | Dielectric Constant | Dissipation Factor | CTE (ppm/°C) |
---|---|---|---|---|---|
Polyimide | 250 | 425 | 3.5 | 0.002 | 60 |
High Tg Multifunctional Epoxy | 180-210 | 325-400 | 3.8-4.0 | 0.010-0.020 | 60-80 |
Blended Cyanate Ester | 220-250 | 350-410 | 3.5-3.8 | 0.004-0.009 | 30-60 |
PTFE (Teflon) | 327 | 400 | 2.1 | 0.001 | 140 |
- Tg = Glass Transition Temperature
- Td = Decomposition Temperature
- CTE = Coefficient of Thermal Expansion
These high-performance materials offer several advantages over standard FR-4:
- Stability at extreme temperatures up to 250°C+
- Low CTE for improved thermal stress resistance
- Low moisture absorption and outgassing
- Excellent dielectric properties and low losses at high frequencies
- Inherent flame retardancy and low smoke generation
However, high TG laminates are also more expensive and challenging to process than FR-4. Polyimide, for example, requires higher drilling speeds, more frequent drill bit changes, and specialized desmear chemistries. The brittle nature of some high Tg materials like cyanate ester can lead to lower yields. Careful PCB Manufacturing process control is necessary to fabricate reliable high TG circuit boards.
Applications for High Temperature PCBs
High TG PCBs are used in numerous industries where electronic devices must survive harsh environments:
Automotive Electronics
Advanced driver assistance systems (ADAS), engine control units (ECUs), infotainment systems, and power electronics for electric vehicles require PCBs that can handle temperatures up to 150°C or more. High TG materials ensure these mission-critical components remain functional despite thermal stresses from the engine compartment, exhaust heat, and power switching.
Aerospace and Defense
Avionics, radar systems, engine controls, and other aerospace electronics must withstand temperature extremes from -55°C to 200°C+. Military-grade PCBs also need to resist shock, vibration, humidity, and corrosive fluids. High TG laminates like polyimide offer the durability and reliability necessary for these demanding applications.
Oil and Gas Exploration
Downhole drilling tools and sensors used in oil and gas wells are subject to temperatures up to 200°C and pressures over 30,000 psi. The electronics controlling these devices must survive in these hostile conditions for extended periods without failure. High TG PCBs with polyimide or cyanate ester materials are essential for this industry.
Industrial Controls and Power Electronics
Factory automation systems, motor drives, IGBT modules, and other industrial electronics operate in environments with high ambient temperatures, vibration, and contaminants. High TG circuit boards provide the thermal stability and mechanical strength required for reliable operation over the equipment’s lifespan.
LED Lighting
High-power LED luminaires generate significant heat that can degrade or damage standard PCBs. Aluminum-backed circuit boards with high TG dielectrics are often used to dissipate heat and maintain LED performance and longevity in demanding solid-state lighting applications.
High TG PCB Manufacturing Process Considerations
Fabricating high-temperature circuit boards requires specialized equipment, processes, and expertise compared to standard PCB manufacturing. Key process considerations include:
Material Preparation and Handling
High Tg laminates are more expensive and often more delicate than FR-4. Careful material cutting, cleaning, and baking processes are necessary to remove moisture and prevent damage. Polyimide film, for example, requires clean room conditions to avoid contamination that could lead to delamination or adhesion issues.
Drilling
The hard, brittle nature of high Tg materials necessitates high-speed drilling with hard tool steel or carbide drill bits. Dwell times must be minimized to prevent heat damage, and bits should be changed frequently to ensure hole quality. Laser drilling is an alternative for small, high-aspect-ratio holes in challenging substrates.
Desmear and Metallization
Plasma or permanganate desmear processes are typically required to remove drill smear and prepare high Tg hole walls for copper plating. The specific desmear chemistry and parameters must be tailored to the material to avoid damaging or roughening the hole walls excessively. Electroless copper or direct metallization can then be used to provide a conductive seed layer for pattern plating.
Imaging and Etching
High Tg laminates often have darker colors and lower light sensitivity than FR-4, which can affect photoresist imaging. Higher exposure energies or specialized photoresists may be necessary to achieve adequate feature resolution. The different etch rates of high Tg materials must also be accounted for in the etching process to prevent over-or under-etching of fine traces.
Solder Mask and Finish
High-temperature solder masks are required for HT PCBs to protect the base laminate and prevent solder bridging. These solder masks must have high Tg values, good adhesion to the substrate, and resistance to thermal shocks during assembly. ENIG (Electroless Nickel Immersion Gold) is a common surface finish for high TG boards due to its flat surface, durability, and aluminum wire bonding compatibility.
Controlled Impedance
Many high-speed or RF applications require controlled impedance transmission lines to manage signal integrity. However, the dielectric constant (Dk) of high Tg materials can vary significantly with frequency and temperature compared to FR-4. Careful characterization of the laminate’s Dk and dissipation factor (Df) is necessary to design and fabricate controlled impedance structures that will perform consistently in the end-use environment.
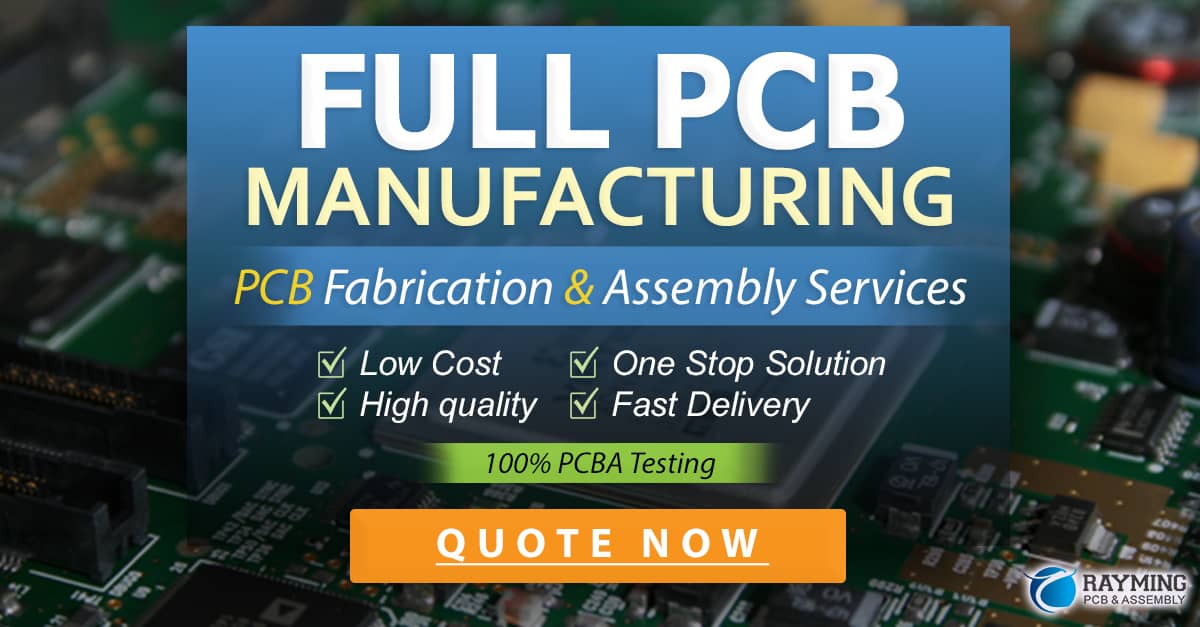
High TG PCB Design Guidelines
Designing reliable high-temperature circuit boards requires attention to several key factors:
Material Selection
Choose a high Tg laminate and solder mask system that meets the application’s temperature, mechanical, and electrical requirements. Consider the material’s CTE, Dk, Df, thermal conductivity, and processability when making a selection. Consult with the PCB manufacturer early in the design process to ensure the material is compatible with their capabilities.
Thermal Management
Proper thermal management is critical for HT PCBs to prevent overheating and ensure long-term reliability. Use thick copper traces and planes where possible to improve heat spreading. Incorporate thermal vias to conduct heat away from hot components and into heat sinks or metal substrates. Use thermal simulation tools to identify and eliminate hot spots in the layout.
Expansion and Contraction
Different materials in the PCB Stackup will expand and contract at different rates as temperature changes. This can lead to mechanical stress, warpage, or even delamination if not properly managed. Use balanced copper layups and symmetric stackups where possible. Allow for adequate expansion space around components, mounting holes, and vias. Consider using stress-relief patterns or flexible sections in the layout to accommodate expansion mismatches.
Via Design
High aspect ratio vias are more challenging to drill and plate in high Tg laminates. Minimize the number of vias and use larger via sizes where possible to improve manufacturability. Stagger via locations to prevent stacked or chain vias that can create weak points. Use teardrops or thicker Annular Rings to strengthen via-to-trace connections.
Component Selection
Use components rated for the expected operating temperature range and environmental conditions. High-temperature solder alloys, underfills, and adhesives may be necessary for reliable assembly. Pay attention to component packaging and lead styles to ensure compatibility with the PCB material and assembly process.
FAQ
What is the difference between high Tg and standard FR-4 PCBs?
High Tg PCBs use specialized laminates and solder masks that can maintain their mechanical and electrical properties at temperatures up to 250°C or higher. Standard FR-4 PCBs, in contrast, are only rated for temperatures up to about 130-140°C before the epoxy resin begins to soften and degrade.
What are some common high Tg PCB materials?
Polyimide, high Tg epoxy, cyanate ester, and PTFE (Teflon) are among the most common high Tg laminates used for HT PCBs. These materials offer different combinations of thermal stability, mechanical strength, dielectric properties, and processability to suit various application requirements.
How much do high TG PCBs cost compared to standard PCBs?
High Tg laminates and solder masks are typically several times more expensive than standard FR-4 materials. The specialized processing equipment and expertise required for HT PCB manufacturing also contribute to higher costs. In general, expect high Tg PCBs to cost 3-10 times more than comparable FR-4 boards, depending on the specific material, complexity, and volume.
Can high TG PCBs be assembled using standard soldering processes?
Many high Tg PCBs can be assembled using standard SAC (tin-silver-copper) solder alloys and reflow or wave soldering processes. However, for the most demanding high-temperature applications, specialized solder alloys with higher melting points may be necessary. These alloys may require different fluxes, reflow profiles, and cleaning processes to ensure reliable solder joints.
What design challenges are associated with high TG PCBs?
Designing high TG PCBs requires careful attention to thermal management, expansion mismatches, via design, and component selection. The different mechanical and electrical properties of high Tg laminates compared to FR-4 must be accounted for in the stackup, layout, and manufacturing process to ensure reliability and performance in harsh environments. Close collaboration between the design team and PCB manufacturer is essential for successful high TG PCB Development.
Conclusion
High temperature PCBs using high Tg laminates and solder masks are essential for electronics that must survive extreme thermal and environmental stresses. These specialized circuit boards find use in demanding applications across the automotive, aerospace, oil and gas, industrial, and LED lighting industries.
However, designing and manufacturing reliable high TG PCBs is not a trivial task. The unique mechanical, thermal, and electrical properties of high Tg materials require careful consideration in the PCB stackup, layout, and manufacturing process. From material selection and thermal management to via design and component choices, designers must work closely with experienced HT PCB Fabricators to ensure a successful product.
As electronic systems push the boundaries of temperature and performance, high TG PCBs will continue to play a critical role in enabling new technologies and applications. By understanding the materials, processes, and design principles behind these cutting-edge circuit boards, engineers can unlock new possibilities for electronics in the harshest environments.
0 Comments