The Importance of Annular Rings in PCB Design
Mechanical Stability
Annular rings provide mechanical stability to the components mounted on a PCB. They help to distribute the stress and strain caused by the insertion and removal of components, as well as the thermal expansion and contraction during operation. Without adequate annular rings, components may become loose or detach from the board, leading to device failure.
Electrical Connectivity
Annular rings serve as the primary connection point between the component leads and the copper traces on the PCB. They ensure a reliable electrical connection by providing a sufficient surface area for soldering. Larger annular rings allow for better current carrying capacity and improved heat dissipation, which is particularly important for high-power components.
Manufacturing Tolerances
Annular rings help to accommodate manufacturing tolerances during the PCB fabrication process. Drilling holes in a PCB is not always a perfect process, and there may be slight variations in hole size and position. By designing annular rings with appropriate sizes, engineers can ensure that there is enough copper area around the hole to maintain a reliable connection, even if the hole is slightly misaligned.
Annular Ring Design Considerations
Size and Shape
The size and shape of annular rings depend on several factors, such as the component package, the PCB manufacturing capabilities, and the design requirements. Generally, annular rings should be as large as possible to provide maximum mechanical stability and electrical connectivity. However, the size may be limited by the available space on the PCB and the proximity of other components.
Annular rings are typically circular, but they can also be oval or rectangular in shape to accommodate specific component packages or design constraints.
Minimum Annular Ring
The minimum annular ring is the smallest allowable copper area around a drilled hole. It is determined by the PCB manufacturer’s capabilities and the design standards followed by the industry. The IPC (Association Connecting Electronics Industries) provides guidelines for minimum annular ring sizes based on the hole diameter and the PCB class.
Hole Diameter (mm) | Minimum Annular Ring (mm) |
---|---|
0.2 – 0.4 | 0.05 |
0.4 – 0.8 | 0.1 |
0.8 – 1.2 | 0.15 |
1.2 – 2.0 | 0.2 |
2.0 – 3.0 | 0.25 |
Table 1: Minimum Annular Ring Sizes (IPC-6012 Class 2)
Annular Ring Breakout
Annular ring breakout occurs when the copper area around a hole is not sufficient to maintain a reliable connection. This can happen due to various reasons, such as:
- Hole misalignment during drilling
- Excessive copper etching during PCB fabrication
- Mechanical stress during component insertion or removal
To prevent annular ring breakout, designers should follow the minimum annular ring guidelines and consider additional factors such as the component package, the PCB material, and the expected operating conditions.
Annular Rings and Component Packages
Different component packages have specific requirements for annular ring sizes and shapes. Some common examples include:
Through-Hole Components
Through-hole components, such as resistors, capacitors, and connectors, have leads that are inserted into drilled holes on the PCB. The annular rings for through-hole components should be large enough to provide a secure connection and allow for easy soldering. The hole diameter and lead size determine the appropriate annular ring size.
Surface Mount Components
Surface mount components, such as chip resistors, capacitors, and integrated circuits, are mounted directly on the surface of the PCB. The annular rings for surface mount components are typically smaller than those for through-hole components, as they do not need to accommodate the leads. The pad size and shape are determined by the component package and the soldering method (e.g., reflow or wave soldering).
Ball Grid Array (BGA) Packages
BGA packages have an array of solder balls underneath the component, which are connected to corresponding pads on the PCB. The annular rings for BGA packages are critical for ensuring a reliable connection between the solder balls and the PCB. The pad size and pitch (distance between pads) are determined by the BGA package specifications and the PCB manufacturing capabilities.
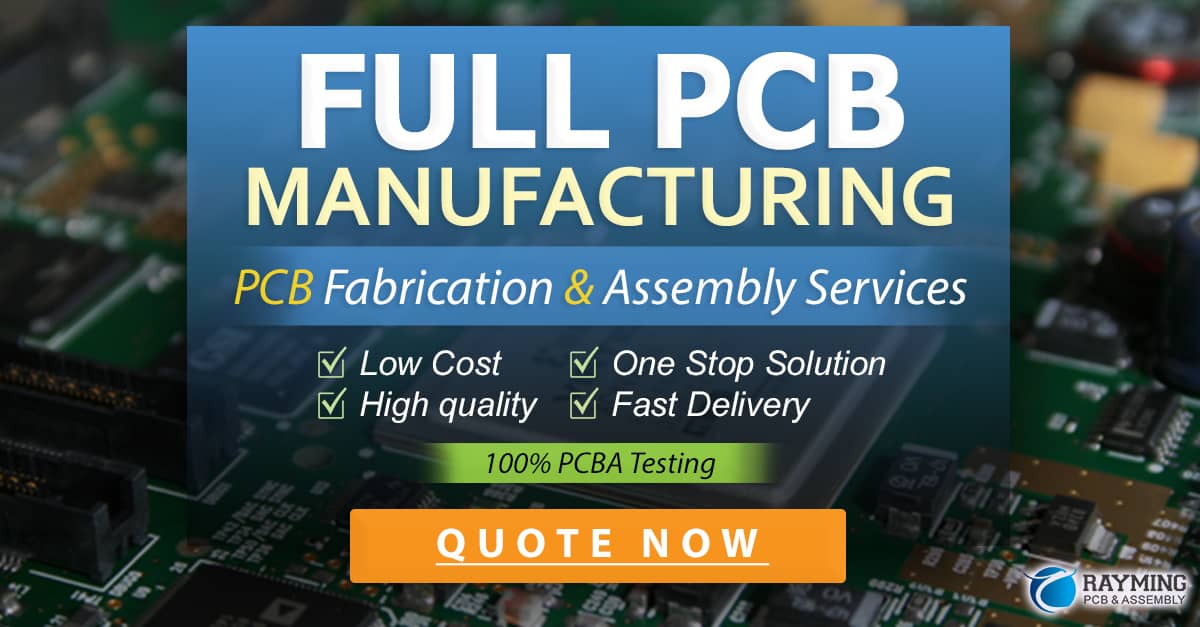
Annular Ring Inspection and Testing
To ensure the quality and reliability of PCBs, annular rings must be inspected and tested during the manufacturing process. Some common methods include:
Visual Inspection
Visual inspection is the most basic method for checking annular rings. It involves examining the PCB under a microscope or magnifying glass to look for any defects or anomalies, such as broken or missing annular rings, insufficient copper coverage, or contamination.
Automated Optical Inspection (AOI)
AOI is a computer-based system that uses cameras and image processing algorithms to inspect PCBs for defects. It can detect a wide range of annular ring issues, such as breakouts, insufficient size, and misalignment. AOI is faster and more consistent than visual inspection, making it suitable for high-volume production.
X-Ray Inspection
X-ray inspection is used to examine the internal structure of PCBs, particularly for components with hidden or obscured annular rings, such as BGA packages. X-ray machines can detect voids, cracks, and other defects in the solder joints and annular rings that are not visible from the surface.
Electrical Testing
Electrical testing involves applying a test signal to the PCB and measuring the response to verify the continuity and isolation of the annular rings and copper traces. Common electrical tests include:
- Continuity Test: Checks for open circuits or broken connections
- Isolation Test: Checks for short circuits or unintended connections
- Resistance Test: Measures the resistance of the annular rings and copper traces
- Capacitance Test: Measures the capacitance between adjacent annular rings or traces
Frequently Asked Questions (FAQ)
-
What is the purpose of an annular ring in PCB design?
Annular rings provide mechanical stability, electrical connectivity, and accommodate manufacturing tolerances in PCB design. They ensure a reliable connection between component leads and copper traces on the board. -
How are annular ring sizes determined?
Annular ring sizes are determined by several factors, including the component package, PCB manufacturing capabilities, and design requirements. The IPC provides guidelines for minimum annular ring sizes based on hole diameter and PCB class. -
What is annular ring breakout, and how can it be prevented?
Annular ring breakout occurs when the copper area around a hole is not sufficient to maintain a reliable connection. It can be prevented by following minimum annular ring guidelines, considering component packages, PCB material, and expected operating conditions. -
What are the common methods for inspecting and testing annular rings?
Common methods for inspecting and testing annular rings include visual inspection, automated optical inspection (AOI), X-ray inspection, and electrical testing (continuity, isolation, resistance, and capacitance tests). -
Why are annular rings important for different component packages?
Different component packages, such as through-hole, surface mount, and BGA, have specific requirements for annular ring sizes and shapes to ensure a secure connection and proper soldering. Annular rings must be designed according to the package specifications and PCB manufacturing capabilities.
In conclusion, annular rings are essential components in PCB design, providing mechanical stability, electrical connectivity, and accommodating manufacturing tolerances. Proper design, inspection, and testing of annular rings are crucial for ensuring the reliability and functionality of electronic devices. By understanding the importance of annular rings and following industry guidelines, PCB designers and manufacturers can create high-quality, robust electronic products.
0 Comments