What is a High-Frequency PCB?
A high-frequency PCB is a specialized type of printed circuit board designed to handle high-speed signals with frequencies ranging from a few hundred megahertz (MHz) to several gigahertz (GHz). These PCBs are engineered to minimize signal loss, maintain signal integrity, and reduce electromagnetic interference (EMI) and radio frequency interference (RFI).
Key Characteristics of High-Frequency PCBs
-
Dielectric Materials: High-frequency PCBs utilize low-loss dielectric materials with stable dielectric constants over a wide frequency range. Common materials include Rogers, Teflon, and PTFE.
-
Controlled Impedance: The PCB traces are designed with controlled impedance to match the characteristic impedance of the connected components and minimize reflections.
-
Shielding and Grounding: Proper shielding and grounding techniques are employed to reduce EMI and RFI, ensuring signal integrity.
-
Multilayer Design: High-frequency PCBs often feature multilayer designs to accommodate complex routing and shielding requirements.
Design Considerations for High-Frequency PCBs
Designing a high-frequency PCB requires careful consideration of various factors to ensure optimal performance. Let’s explore some key design aspects:
Signal Integrity
Signal integrity is paramount in high-frequency PCB design. It involves maintaining the quality and consistency of the signal as it travels through the PCB traces. To achieve good signal integrity, designers must consider the following:
-
Impedance Matching: Ensuring proper impedance matching between the PCB traces and connected components minimizes reflections and signal distortions.
-
Trace Geometry: The width, thickness, and spacing of PCB traces impact signal integrity. Careful calculations are required to optimize trace geometry for the desired impedance and frequency.
-
Via Design: Vias, which are used to connect different layers of the PCB, must be designed to minimize discontinuities and reflections. Techniques like via stubs and backdrilling are employed to improve signal integrity.
EMI and RFI Mitigation
High-frequency signals are susceptible to electromagnetic interference (EMI) and radio frequency interference (RFI). To mitigate these issues, designers incorporate the following techniques:
-
Shielding: Metallic shielding layers or enclosures are used to contain electromagnetic radiation and prevent interference with nearby components.
-
Grounding: Proper grounding techniques, such as ground planes and stitching vias, help to create a low-impedance return path for high-frequency signals and reduce EMI.
-
Filtering: EMI filters, such as capacitors and ferrite beads, are used to suppress unwanted high-frequency noise and prevent it from entering or leaving the PCB.
Material Selection
The choice of materials plays a critical role in the performance of high-frequency PCBs. The key considerations for material selection include:
-
Dielectric Constant (Dk): A stable and low dielectric constant is desirable to minimize signal loss and maintain consistent impedance across the frequency range.
-
Dissipation Factor (Df): A low dissipation factor reduces signal attenuation and helps maintain signal integrity.
-
Thermal Stability: Materials with good thermal stability ensure consistent performance over a wide temperature range.
Multilayer PCB Design
High-frequency PCBs often require multilayer designs to accommodate complex routing and shielding requirements. Multilayer PCBs offer several advantages:
-
Increased Routing Density: Multiple layers allow for denser routing and more efficient use of PCB real estate.
-
Improved Signal Integrity: Dedicated signal layers and ground planes help maintain signal integrity by reducing crosstalk and providing a low-impedance return path.
-
Enhanced Shielding: Internal shielding layers can be incorporated to isolate sensitive signals and reduce EMI.
Manufacturing Processes for High-Frequency PCBs
The manufacturing process for high-frequency PCBs requires specialized techniques and stringent quality control measures. Let’s explore some key aspects of the manufacturing process:
Material Selection and Preparation
The first step in manufacturing high-frequency PCBs is selecting the appropriate dielectric materials based on the design requirements. The materials are carefully prepared, including cleaning, drying, and surface treatment, to ensure optimal bonding and adhesion.
Lamination and Drilling
The prepared dielectric materials are laminated together using high-pressure and temperature to form a solid PCB substrate. Precision drilling is then performed to create the necessary holes for vias and component mounting.
Plating and Etching
The drilled PCB undergoes a plating process to deposit conductive material, typically copper, onto the hole walls and surface. This is followed by a photolithography and etching process to create the desired circuit patterns on the PCB Layers.
Solder Mask and Silkscreen
A solder mask layer is applied to the PCB to protect the circuitry from damage and prevent short circuits during soldering. Silkscreen printing is used to add component labels, text, and other markings for easier assembly and identification.
Inspection and Testing
Rigorous inspection and testing procedures are conducted throughout the manufacturing process to ensure the quality and reliability of the high-frequency PCBs. This includes visual inspections, electrical testing, and signal integrity analysis.
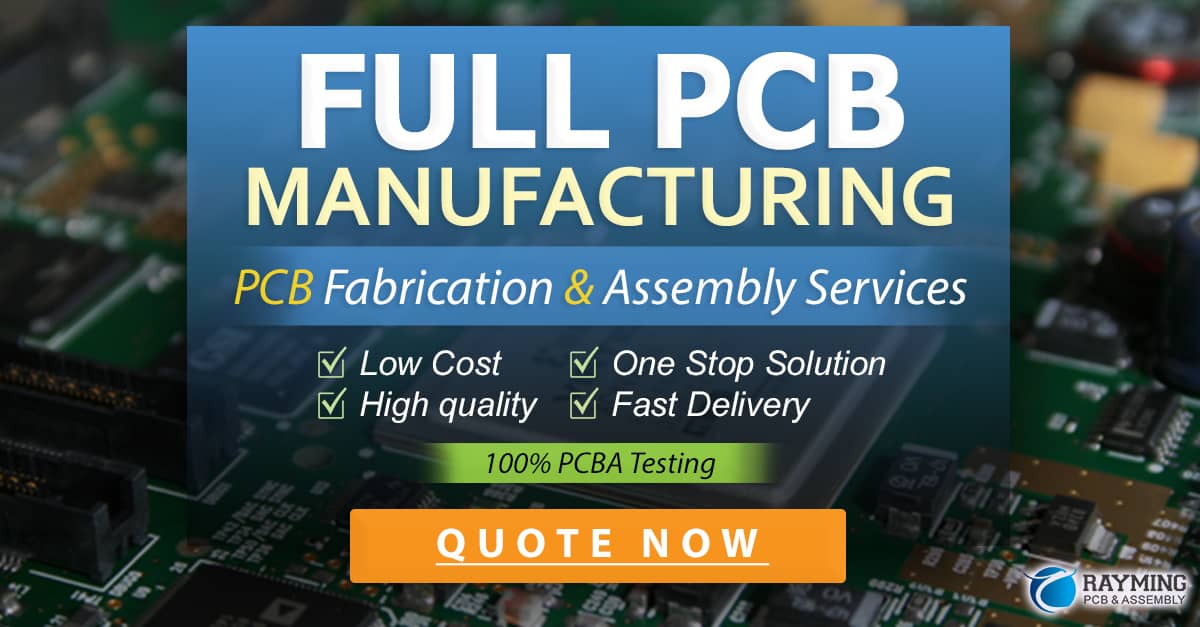
Applications of High-Frequency PCBs
High-frequency PCBs find applications in various industries and domains where high-speed signal transmission is critical. Some notable applications include:
-
Telecommunications: High-frequency PCBs are used in wireless communication systems, such as 5G networks, satellite communication, and radar systems.
-
Networking: High-speed networking equipment, including routers, switches, and modems, rely on high-frequency PCBs for efficient data transmission.
-
Aerospace and Defense: Avionics systems, missile guidance, and radar applications utilize high-frequency PCBs for reliable and secure communication.
-
Medical Devices: Advanced medical imaging systems, such as MRI and CT scanners, employ high-frequency PCBs for precise signal processing.
-
Automotive: Modern vehicles incorporate high-frequency PCBs in advanced driver assistance systems (ADAS), infotainment systems, and vehicle-to-vehicle communication.
Future Trends in High-Frequency PCBs
As technology continues to advance, the demand for higher data rates and faster signal transmission is driving innovations in high-frequency PCB design and manufacturing. Some notable trends include:
-
Higher Frequencies: PCBs are being designed to handle even higher frequencies, reaching into the millimeter-wave range (30 GHz and above) for applications like 5G and beyond.
-
Advanced Materials: Ongoing research is focused on developing new dielectric materials with improved electrical and thermal properties to meet the demands of higher frequencies and power densities.
-
3D Printing: Additive manufacturing techniques, such as 3D printing, are being explored for the fabrication of high-frequency PCBs, enabling more complex geometries and faster prototyping.
-
Integration of Active Components: The integration of active components, such as amplifiers and filters, directly onto the PCB substrate is gaining traction to reduce interconnect losses and improve overall system performance.
Frequently Asked Questions (FAQ)
-
What is the difference between a high-frequency PCB and a regular PCB?
A high-frequency PCB is specifically designed to handle high-speed signals with frequencies ranging from a few hundred megahertz to several gigahertz. It utilizes specialized materials, controlled impedance, and advanced design techniques to maintain signal integrity and minimize interference. Regular PCBs, on the other hand, are designed for lower frequency applications and may not have the same stringent requirements. -
What materials are commonly used for high-frequency PCBs?
High-frequency PCBs commonly use low-loss dielectric materials with stable dielectric constants over a wide frequency range. Some popular materials include Rogers, Teflon, and PTFE. These materials offer excellent electrical properties, such as low dielectric constant and low dissipation factor, which are crucial for maintaining signal integrity at high frequencies. -
Why is impedance matching important in high-frequency PCB design?
Impedance matching is critical in high-frequency PCB design to ensure proper signal transmission and minimize reflections. When the impedance of the PCB traces matches the characteristic impedance of the connected components, it prevents signal reflections and distortions. Mismatched impedances can lead to signal degradation, reduced signal quality, and potential system malfunctions. -
How can EMI and RFI be mitigated in high-frequency PCBs?
EMI and RFI can be mitigated in high-frequency PCBs through various techniques. Shielding, such as metallic layers or enclosures, helps contain electromagnetic radiation and prevent interference. Proper grounding techniques, including ground planes and stitching vias, provide a low-impedance return path for high-frequency signals. Additionally, EMI filters, such as capacitors and ferrite beads, can be used to suppress unwanted high-frequency noise. -
What are the advantages of multilayer PCB design for high-frequency applications?
Multilayer PCB design offers several advantages for high-frequency applications. It allows for increased routing density, enabling more efficient use of PCB real estate. Dedicated signal layers and ground planes help maintain signal integrity by reducing crosstalk and providing a low-impedance return path. Moreover, internal shielding layers can be incorporated to isolate sensitive signals and reduce EMI.
Conclusion
High-frequency PCBs are essential components in today’s fast-paced electronic landscape, enabling high-speed signal transmission across various industries and applications. Designing and manufacturing high-frequency PCBs requires careful consideration of signal integrity, EMI mitigation, material selection, and advanced manufacturing processes.
As technology continues to advance, the demand for higher data rates and faster signal transmission will drive further innovations in high-frequency PCB design and manufacturing. From advanced materials to 3D printing and the integration of active components, the future of high-frequency PCBs looks promising.
By understanding the principles and techniques behind high-frequency PCBs, engineers and designers can create robust and reliable electronic systems that meet the ever-increasing demands for high-speed signal transmission in our connected world.
Parameter | Description |
---|---|
Frequency Range | Few hundred MHz to several GHz |
Dielectric Materials | Rogers, Teflon, PTFE |
Impedance Matching | Critical for signal integrity |
EMI/RFI Mitigation | Shielding, grounding, filtering |
Multilayer Design | Increased routing density, improved signal integrity, enhanced shielding |
0 Comments