What is an HDI PCB?
An HDI PCB is a printed circuit board that features higher wiring density per unit area compared to traditional PCBs. This is achieved through the use of smaller vias, finer traces, and advanced manufacturing techniques. HDI PCBs enable the miniaturization of electronic devices while maintaining or improving their functionality and performance.
Advantages of HDI PCBs
- Reduced board size and weight
- Improved signal integrity
- Higher component density
- Enhanced thermal management
- Lower power consumption
- Increased reliability
HDI PCB Design Considerations
Layer Stack-up
The layer stack-up is a critical aspect of HDI PCB design. It determines the number of layers, their arrangement, and the materials used. A typical HDI PCB stack-up may include:
- Core layers
- Prepreg layers
- Copper foil
- Solder mask
- Silkscreen
When designing the layer stack-up, consider the following factors:
- Signal integrity
- Impedance control
- Manufacturability
- Cost
Via Types and Sizes
HDI PCBs utilize various types of vias to achieve high-density routing. The most common via types include:
- Through-hole vias
- Blind vias
- Buried vias
- Microvias
The choice of via type depends on the design requirements, layer stack-up, and manufacturing capabilities. Smaller via sizes, such as microvias, allow for higher routing density and improved signal integrity.
Trace Width and Spacing
To achieve high-density routing in HDI PCBs, designers must use finer traces and smaller spacing between them. The trace width and spacing are determined by factors such as:
- Signal integrity requirements
- Current carrying capacity
- Manufacturing capabilities
- IPC standards
Designers should work closely with the PCB manufacturer to ensure that the chosen trace width and spacing are achievable and reliable.
Component Placement and Routing
Component placement and routing are critical aspects of HDI PCB design. Proper component placement helps minimize the board size, improve signal integrity, and enhance manufacturability. When placing components, consider the following:
- Component size and shape
- Pin pitch and pad size
- Thermal management
- Mechanical constraints
Routing in HDI PCBs requires careful planning and execution. Use the following techniques to achieve optimal routing:
- Shortest path routing
- Differential pair routing
- Matched length routing
- Via stitching
- Teardrops and fillets
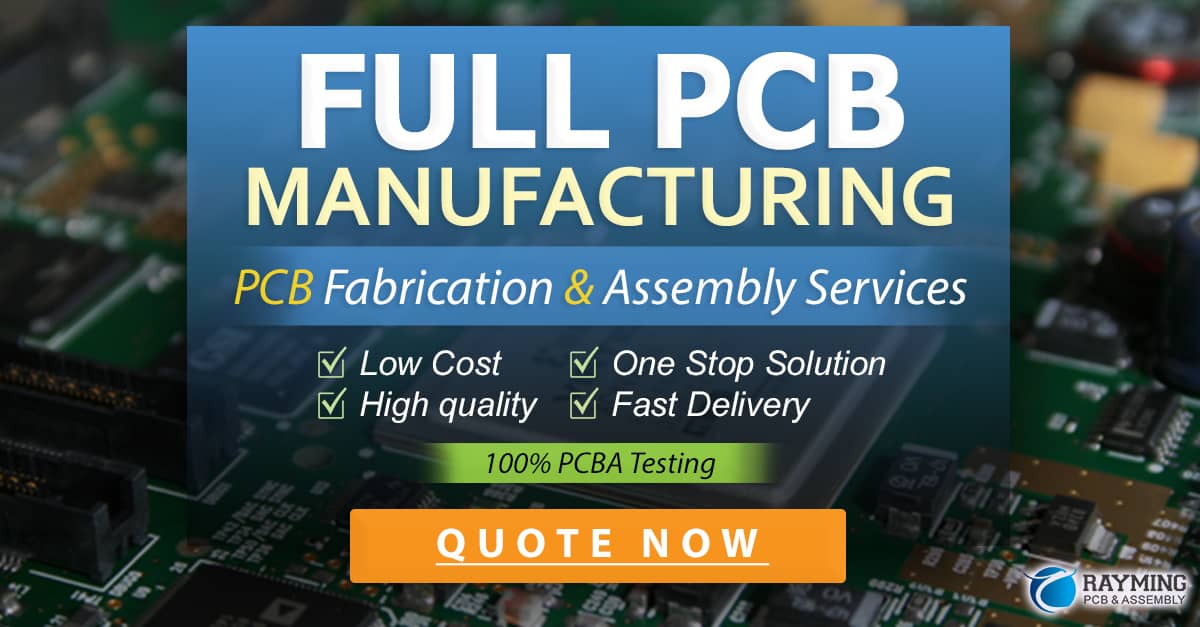
HDI PCB Manufacturing Process
The manufacturing process for HDI PCBs involves several steps that differ from traditional PCB fabrication. The key steps include:
- Material selection
- Drilling
- Plating
- Patterning
- Lamination
- Solder mask application
- Surface finish
- Electrical testing
- Inspection
Each step requires precise control and adherence to strict quality standards to ensure the reliability and performance of the final product.
Material Selection
The choice of materials for HDI PCBs is crucial for achieving the desired performance and reliability. The most common materials used in HDI PCBs include:
- FR-4
- High-Tg FR-4
- Polyimide
- Teflon
- Rogers materials
The material selection depends on factors such as:
- Dielectric constant
- Dissipation factor
- Thermal stability
- Mechanical strength
- Cost
Drilling and Plating
Drilling and plating are critical steps in the HDI PCB manufacturing process. The drilling process creates the vias that connect the different layers of the PCB. The most common drilling methods for HDI PCBs include:
- Mechanical drilling
- Laser drilling
After drilling, the vias are plated with copper to establish electrical connections between the layers. The plating process involves:
- Electroless copper plating
- Electrolytic copper plating
The quality of the drilling and plating processes directly impacts the reliability and performance of the HDI PCB.
Patterning and Lamination
Patterning and lamination are the processes that create the copper traces and bond the layers of the HDI PCB together. The patterning process involves:
- Applying a photoresist
- Exposing the photoresist to UV light through a photomask
- Developing the photoresist
- Etching the copper
- Stripping the remaining photoresist
The lamination process involves:
- Aligning the layers
- Applying pressure and heat
- Curing the bonding material
Proper patterning and lamination ensure the integrity and reliability of the HDI PCB.
HDI PCB Testing and Inspection
Testing and inspection are essential for ensuring the quality and reliability of HDI PCBs. The most common testing and inspection methods include:
- Automatic Optical Inspection (AOI)
- X-ray Inspection
- Electrical Testing
- Flying probe test
- In-circuit test (ICT)
- Boundary scan test (BST)
- Microsectioning
- Thermal Cycling
Each testing and inspection method focuses on different aspects of the HDI PCB, such as:
- Solder joint quality
- Via integrity
- Trace continuity
- Dielectric strength
- Thermal stability
By implementing a comprehensive testing and inspection plan, manufacturers can identify and address any issues before the HDI PCBs are shipped to customers.
Design for Manufacturing (DFM) Considerations
Design for Manufacturing (DFM) is a crucial aspect of HDI PCB design that ensures the manufacturability and reliability of the final product. Some key DFM considerations include:
- Adhering to manufacturer’s design rules
- Using standard via sizes and spacing
- Avoiding acute angles in traces
- Providing adequate clearance for tooling holes
- Balancing copper distribution
- Minimizing the number of unique parts
- Using standard component sizes and pitches
By incorporating DFM principles into the HDI PCB design process, designers can reduce manufacturing costs, improve yield, and enhance the overall quality of the final product.
Common Pitfalls in HDI PCB Design and Manufacturing
Despite the many benefits of HDI PCBs, there are several common pitfalls that designers and manufacturers should be aware of:
- Inadequate communication between design and manufacturing teams
- Insufficient documentation and version control
- Failing to account for material and process tolerances
- Neglecting signal integrity and thermal management
- Overlooking testing and inspection requirements
- Rushing the design or manufacturing process
To avoid these pitfalls, it is essential to foster open communication, maintain detailed documentation, and allow sufficient time for each stage of the HDI PCB design and manufacturing process.
Future Trends in HDI PCB Technology
As electronic devices continue to become smaller, faster, and more complex, HDI PCB technology must evolve to keep pace. Some of the future trends in HDI PCB technology include:
- Increasing use of embedded components
- Adoption of advanced materials, such as low-loss dielectrics
- Implementation of 3D printing for rapid prototyping
- Integration of active and passive components into the PCB substrate
- Development of advanced testing and inspection techniques
- Emphasis on environmental sustainability and recyclability
By staying abreast of these trends, designers and manufacturers can ensure that their HDI PCB solutions remain competitive and meet the evolving needs of the electronics industry.
Frequently Asked Questions (FAQ)
- What is the minimum via size achievable in HDI PCBs?
-
The minimum via size depends on the manufacturing capabilities of the PCB fabricator. Currently, most HDI PCB manufacturers can achieve via sizes as small as 0.1 mm (4 mil) in diameter.
-
How does the choice of material affect the performance of HDI PCBs?
-
The choice of material significantly impacts the electrical, thermal, and mechanical properties of HDI PCBs. For example, low-loss materials like Teflon and Rogers can improve signal integrity, while high-Tg FR-4 can enhance thermal stability.
-
What is the difference between blind and buried vias in HDI PCBs?
-
Blind vias connect an outer layer to an inner layer, but do not pass through the entire board. Buried vias connect two or more inner layers, but do not reach the outer layers of the PCB.
-
How can designers ensure the manufacturability of their HDI PCB designs?
-
Designers can ensure manufacturability by adhering to the manufacturer’s design rules, incorporating DFM principles, and maintaining open communication with the manufacturing team throughout the design process.
-
What are the main challenges in testing and inspecting HDI PCBs?
- The main challenges in testing and inspecting HDI PCBs include the small size of features, the complexity of the designs, and the need for specialized equipment and expertise. Overcoming these challenges requires a comprehensive testing and inspection plan that leverages advanced techniques like AOI, X-ray, and microsectioning.
Conclusion
HDI PCBs offer numerous benefits for the miniaturization and performance enhancement of electronic devices. However, achieving a perfect HDI PCB requires careful consideration of design, manufacturing, and testing aspects. By understanding the key principles and best practices outlined in this guide, designers and manufacturers can optimize their HDI PCB solutions and stay ahead of the curve in this rapidly evolving field.
0 Comments