What is Flexible PCB Prototyping?
Flexible PCB prototyping is the process of creating initial samples of flexible printed circuit boards for testing and validation purposes. Unlike traditional rigid PCBs, flexible PCBs are designed to bend, twist, and conform to various shapes and configurations. This unique characteristic allows for the development of electronic devices that are more compact, lightweight, and adaptable to different form factors.
The prototyping phase is crucial in the flexible PCB manufacturing process as it enables designers and engineers to assess the feasibility, functionality, and reliability of their designs before proceeding to mass production. By creating prototypes, potential issues can be identified and addressed early on, saving time and resources in the long run.
Types of Flexible PCBs
Flexible PCBs come in various types, each with its own distinct characteristics and applications. The three main categories of flexible PCBs are:
- Single-sided Flexible PCBs
- Consist of a single conductive layer on a flexible substrate
- Ideal for simple, low-density circuit designs
-
Commonly used in keypads, sensors, and displays
-
Double-sided Flexible PCBs
- Feature conductive layers on both sides of the flexible substrate
- Offer higher circuit density compared to single-sided PCBs
-
Suitable for more complex designs and applications
-
Multi-layer Flexible PCBs
- Comprise multiple conductive layers sandwiched between flexible insulating layers
- Provide the highest circuit density and complexity
- Used in advanced applications such as medical devices, aerospace systems, and high-end consumer electronics
Type | Conductive Layers | Circuit Density | Common Applications |
---|---|---|---|
Single-sided Flexible PCB | 1 | Low | Keypads, sensors, displays |
Double-sided Flexible PCB | 2 | Medium | More complex designs and applications |
Multi-layer Flexible PCB | 3 or more | High | Medical devices, aerospace systems, high-end consumer electronics |
Benefits of Flexible PCB Prototyping
Engaging in flexible PCB prototyping offers numerous advantages for businesses and product developers. Some of the key benefits include:
1. Design Validation
Prototyping allows designers to test and validate their flexible PCB designs in real-world scenarios. By creating physical prototypes, potential design flaws, compatibility issues, and performance bottlenecks can be identified and rectified before committing to mass production. This iterative process ensures that the final product meets the desired specifications and functions as intended.
2. Cost Savings
Investing in flexible PCB prototyping can lead to significant cost savings in the long run. By identifying and addressing design issues early on, businesses can avoid costly mistakes and rework during the mass production phase. Prototyping also enables designers to optimize their designs for manufacturability, reducing material waste and production time, ultimately resulting in lower overall costs.
3. Accelerated Time-to-Market
Flexible PCB prototyping streamlines the product development process, allowing businesses to bring their products to market faster. By validating designs through prototyping, the need for extensive revisions and modifications during the later stages of development is minimized. This accelerated timeline provides a competitive edge, enabling businesses to capitalize on market opportunities and stay ahead of the competition.
4. Enhanced Product Quality
Prototyping plays a vital role in ensuring the quality and reliability of the final product. Through rigorous testing and validation, potential weaknesses and failure points can be identified and addressed. By refining the design based on prototype feedback, businesses can deliver high-quality flexible PCBs that meet customer expectations and industry standards.
5. Customization and Flexibility
Flexible PCB prototyping allows for greater customization and flexibility in product design. Designers can experiment with different materials, layouts, and form factors to create PCBs that precisely fit the requirements of their specific applications. This level of customization enables the development of innovative and unique electronic devices that stand out in the market.
Flexible PCB Prototype Manufacturing Process
The flexible PCB prototype manufacturing process involves several key steps to ensure the creation of high-quality and functional prototypes. Let’s take a closer look at each stage of the process:
1. Design and Layout
The first step in flexible PCB prototyping is creating the circuit design and layout. Designers use specialized software tools to develop the schematic diagram and physical layout of the PCB. They consider factors such as component placement, signal routing, and mechanical constraints to optimize the design for flexibility and functionality.
2. Material Selection
Choosing the right materials is crucial for the performance and reliability of flexible PCBs. The most commonly used substrate materials for flexible PCBs include polyimide, polyester, and flexibles. Conductive materials, such as copper, are selected based on their electrical properties and compatibility with the substrate. The thickness and properties of the materials are carefully considered to ensure the desired flexibility and durability of the PCB.
3. Fabrication
Once the design is finalized and the materials are selected, the fabrication process begins. The flexible PCB prototype manufacturing process typically involves the following sub-steps:
a. Substrate Preparation: The flexible substrate material is cleaned and treated to ensure proper adhesion of the conductive layers.
b. Lamination: The conductive material, usually copper foil, is laminated onto the flexible substrate using heat and pressure.
c. Patterning: The desired circuit pattern is transferred onto the copper layer using photolithography or laser direct imaging techniques.
d. Etching: The unwanted copper is removed using chemical etching, leaving behind the desired circuit traces.
e. Drilling: Holes are drilled through the PCB to accommodate component leads and vias.
f. Surface Finishing: The exposed copper traces are coated with a protective finish, such as solder mask or gold plating, to prevent oxidation and enhance solderability.
4. Assembly
After the fabrication process, the flexible PCB prototype undergoes assembly. Surface mount technology (SMT) or through-hole technology (THT) is used to mount electronic components onto the PCB. Specialized equipment, such as pick-and-place machines and reflow ovens, is employed to ensure precise and reliable component placement.
5. Testing and Validation
Once the prototype is assembled, it undergoes rigorous testing and validation to ensure its functionality, reliability, and compliance with design specifications. Various tests, including electrical continuity, insulation resistance, and flexibility tests, are performed to identify any potential issues or defects. Visual inspection and functional testing are also conducted to verify the overall quality of the prototype.
6. Iteration and Refinement
Based on the results of testing and validation, designers may need to make iterative changes and refinements to the prototype. This process involves analyzing the feedback, identifying areas for improvement, and implementing necessary modifications. The prototype is then re-fabricated and re-tested until it meets the desired performance and quality standards.
Step | Description |
---|---|
Design and Layout | Create circuit design and layout using specialized software |
Material Selection | Choose suitable substrate and conductive materials |
Fabrication | Prepare substrate, laminate, pattern, etch, drill, and surface finish |
Assembly | Mount components using SMT or THT techniques |
Testing and Validation | Perform electrical, visual, and functional tests to ensure quality |
Iteration and Refinement | Make necessary changes based on testing feedback and refine prototype |
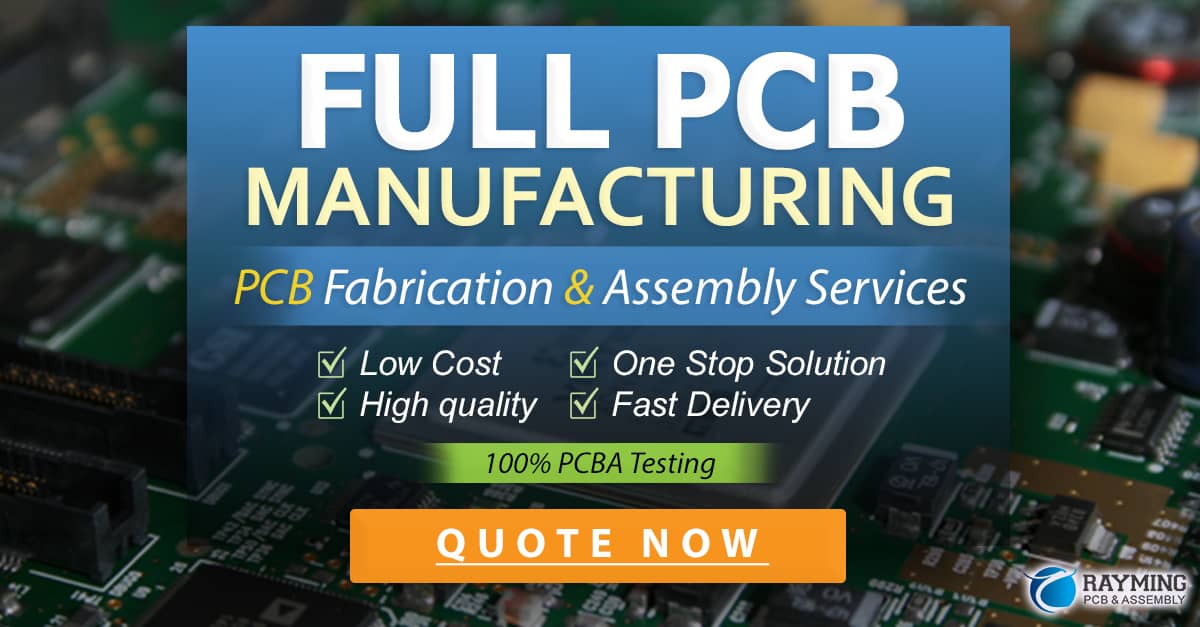
Choosing a Flexible PCB Prototype Manufacturing Service
When selecting a flexible PCB prototype manufacturing service, several factors should be considered to ensure the best results. Here are some key points to keep in mind:
1. Experience and Expertise
Look for a manufacturer with extensive experience in flexible PCB prototyping. They should have a proven track record of successfully delivering high-quality prototypes for a wide range of applications. Experienced manufacturers possess the knowledge and expertise to navigate the complexities of flexible PCB design and fabrication, ensuring optimal results.
2. Manufacturing Capabilities
Assess the manufacturing capabilities of the service provider. They should have state-of-the-art equipment and facilities to handle the specific requirements of flexible PCB prototyping. This includes advanced fabrication processes, such as high-resolution patterning, precise drilling, and reliable lamination. Additionally, they should have the capacity to accommodate various material options and PCB configurations.
3. Quality Control and Certifications
Quality is paramount in flexible PCB prototyping. Choose a manufacturer that adheres to strict quality control standards and holds relevant certifications, such as ISO 9001 and IPC standards. They should have robust quality assurance processes in place, including thorough inspections, testing, and documentation. Certifications demonstrate the manufacturer’s commitment to delivering consistently high-quality products.
4. Turnaround Time and Flexibility
Rapid prototyping is essential for accelerating product development timelines. Look for a manufacturer that offers quick turnaround times without compromising on quality. They should have streamlined processes and efficient workflows to deliver prototypes within the agreed-upon timeframe. Additionally, they should be flexible in accommodating design changes and iterations during the prototyping phase.
5. Customer Support and Communication
Effective communication and responsive customer support are crucial throughout the prototyping process. Choose a manufacturer that values open and transparent communication. They should have dedicated support teams available to address your queries, provide technical guidance, and keep you informed about the progress of your project. Clear communication channels and proactive problem-solving approaches ensure a smooth and collaborative prototyping experience.
6. Cost-Effectiveness
While cost is an important consideration, it should not be the sole determining factor when selecting a flexible PCB prototype manufacturing service. Strike a balance between cost and quality. Look for a manufacturer that offers competitive pricing without compromising on the quality of materials, workmanship, and overall prototype performance. Consider the long-term value and benefits of working with a reliable and experienced manufacturer.
Frequently Asked Questions (FAQ)
-
What is the typical turnaround time for flexible PCB Prototypes?
The turnaround time for flexible PCB prototypes varies depending on the complexity of the design, the selected materials, and the manufacturer’s capacity. Generally, Prototyping Services offer turnaround times ranging from a few days to a couple of weeks. Express or expedited options may be available for time-critical projects, but they may come at a higher cost. -
Can flexible PCBs be used in harsh environmental conditions?
Yes, flexible PCBs can be designed to withstand harsh environmental conditions. By selecting appropriate materials and applying specialized coatings or encapsulation techniques, flexible PCBs can be made resistant to moisture, extreme temperatures, vibrations, and chemical exposure. It is important to communicate the specific environmental requirements to the manufacturer during the prototyping phase to ensure the PCB is designed and fabricated accordingly. -
What is the minimum bend radius for flexible PCBs?
The minimum bend radius for flexible PCBs depends on factors such as the substrate material, copper thickness, and the number of layers. As a general rule of thumb, the minimum bend radius is typically 6 times the total thickness of the PCB. However, it is recommended to consult with the manufacturer and adhere to their specific guidelines to ensure the long-term reliability and performance of the flexible PCB. -
Can flexible PCBs be used for high-frequency applications?
Yes, flexible PCBs can be designed for high-frequency applications. However, special considerations must be taken into account to ensure optimal signal integrity and minimize signal loss. This includes careful material selection, controlled impedance design, and proper shielding techniques. Manufacturers with experience in High-Frequency PCB design can provide guidance and recommendations to optimize the performance of flexible PCBs in high-frequency applications. -
How do I ensure the manufacturability of my flexible PCB design?
To ensure the manufacturability of your flexible PCB design, it is essential to adhere to the manufacturer’s design guidelines and best practices. This includes considerations such as minimum trace width and spacing, hole sizes, copper thickness, and bend radius limitations. Engaging in early collaboration with the manufacturer and seeking their feedback during the design phase can help identify and address any potential manufacturability issues before proceeding to prototyping.
Conclusion
Flexible PCB prototype manufacturing is a critical step in the development of innovative and compact electronic devices. By leveraging the expertise of experienced prototyping services, businesses can validate their designs, optimize performance, and accelerate time-to-market. When selecting a flexible PCB prototype manufacturing service, it is crucial to consider factors such as experience, manufacturing capabilities, quality control, turnaround time, customer support, and cost-effectiveness.
By partnering with a reliable and skilled manufacturer, businesses can unlock the full potential of flexible PCBs and create products that push the boundaries of electronic design. As the demand for flexible electronics continues to grow across various industries, investing in flexible PCB prototyping becomes a strategic imperative for staying competitive and delivering cutting-edge solutions to customers.
Embrace the power of flexible PCB prototype manufacturing and embark on a journey of innovation, reliability, and success in the ever-evolving world of electronics.
0 Comments